Insulating basement walls with steel bracing

Good afternoon,
I really appreciate the advice offered on this forum. It’s been very helpful over the years. In 2010 and 2017, we insulated with rockwool comfortbatt in the wall cavities and comfortboard 80 on the exterior of our 60-year old bungalow. It really made a big difference not only in year-round inside temps but also noise levels. This year, we are re-tackling the basement.
One long wall of our house foundation cracked in 2022. It’s now repaired with waterproofing on the outside. We just had the other long wall braced as a preventative measure. This meant removing the framing and insulation installed in the basement in 2010. We’re starting over – and would like to re-use the comfortbatt R14.
My house is in Regina, Saskatchewan (climate zone 7a). The expansive clay soils here are hard on foundations, especially when soil conditions are extremely dry or wet. Radon levels can be high. I have an HRV and radon mitigation system. It would be good to reduce soil gas from entering the basement living space.
We’re trying to figure out a good approach for insulating, and a vapour retarder, but it seems complicated. Vertical steel braces are spaced every 4′ or so on the 2 long walls and are 5 1/2″ deep. One idea is 1″ of airspace directly against the foundation wall; 1″ of XPS or EPS, 4’x8′ sheets, between the steel braces (supported by a 1″ spacer); then rockwool comfortbatt R14 (3.5″ thick) on the horizontal. If XPS is used, we would seal it on all sides between the steel braces and use it as a vapour retarder. The local municipality requires vapour permeance <60 ng/pascal second m2. If EPS is used, same approach except no sealing the sides and instead would install a Smart vapour retarder on the front/interiour side of the braces. Securing the batts horizontally should be interesting. A Rockwool technical advisor suggested tape across the braces (or chicken wire but not keen on that). Admittedly, she said she has not heard of it being done before. The Smart vapour retarder may be able to keep the batts in place? Not an easy system to sort out. The wood framing (with no insulation) would be installed proud of the steel braces.
I’m keen on an air space against the foundation wall because I think it will help the cement breathe. All the main floor joists are embedded in the top of the foundation walls and no capillary break is evident. Given the heavy clay soils which can retain moisture under wet conditions, I’m reluctant to seal the foundation walls. This is from a post by Bill Wichers in 2022:
- The one issue you can have is “rising damp”, which means more moisture risk to the sill plate and rim joist area if you seal up the masonry. To address this, you want to be sure you have a capillary break between the top of the masonry wall and the sill plate. That’s the only real concern with sealing up the wall here.
I sure would appreciate any insights and advice others can offer! Apologies for this rather complicated predicament. I’m not sure I’m on the right track. Thank you.
GBA Detail Library
A collection of one thousand construction details organized by climate and house part
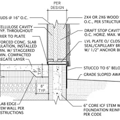
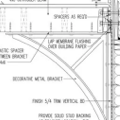
Replies
concrete walls do not need to breath. You do not want let any air exchange happen between your basement and your concrete walls. I would do spray foam if I were in your shoes. The biggest issue you need to overcome is that those steel posts are going to act as condensing surfaces for your interior air unless they are isolated from the interior be an impermeable insulation. Don't use xps, that stuff burns like wild and is not good for the environment. Spray would be a better option, as you could fully encapsulate your steel. If you are worried about water from exterior, you need to install a dimple mat against concrete and let it drain to an interior drainage system that is then sump pumped out. you would then spray foam over this. Do at least 2" of spray foam on wall and steel. this will put you at least two inches to the interior of the steel for your finished surface. frame your interior wall so that the interior is inline with the spray foam bumps on steel and then batt to fill remainder of space.
hope that makes sense. if not I could draw a quick section.
Thank you. Because of the unique dense clay soils here (only 2 cities in Canada have this kind of soil), I think it's important to be able to visually inspect the foundation walls (engineers, home buyers/owners) which is why I'm trying to avoid spraying them with insulation. The foundation situation (major shifting, cracking, differences in height) here has become rather extreme in the past 5 -10 years. Climate extremes may be part of the problem along with how houses were built 60 years ago for the soil type. If possible, I'd like to try to not spray the walls themselves. Spraying components of the wall system would be fine though (e.g., steel braces). The other concern is "rising damp" to the main floor joists (embedded in the concrete) if the walls are sealed by spray foam.
Well, the real fix to your issue is better site drainage around your basement wall. But water has to go somewhere, is doesn't just magically disappear. So what is your plan once your water is in that 1" space? just let it into your wall assembly? or drain it to sump pump? or not let the water through in the first place? You either need to seal that wall or drain it if you are finishing your basement. There are a number of articles on here discussing how to deal with moisture in finished basements. The only unique thing you need to think about is encapsulating those steel in the same way you encapsulate your concrete wall. This can be with spray foam or rigid board foam.
The exterior of the cracked long wall was excavated, new weeping tile installed, waterproofed with Blueskin, and backfilled with sand. The new weeping tile (exterior) is connected to a new second sump inside the basement. No water should come through that wall. The other 3 walls are currently in good shape. If a crack develops in the future (less likely since the good long wall is now braced; short walls less prone to fracture), detecting water leakage early would be good. I think spray foam on the walls makes it more difficult to monitor. Fortunately, the crack in the one long wall was caught early. Deflection <1". Not so keen on interior dimple board and weeping tile systems unless it's the only option.