Remodeling a 1990’s straw bale home

Hi all!
I’m hoping I can get some advice on a remodel project I am doing in Plainfield, VT (zone 6A) to a 1990’s straw bale home. The original scope of work was to replace the worn out windows with new Kohltech triple pane units. I knew this was going to be a challenge as the house is covered in a cement based stucco on the exterior. There are few if any examples of stucco around here and seemingly no pool of talent to draw from, or at least that I have managed to access. My crew and I have been grinding out the stucco using angle grinders with diamond blades to free up the nailing flange. So far so good.
We’ve ground out 10 windows so far and two have advanced rot in the rough window bucks which are an inconsistent assemblage of plywood and 2x material. These two windows are inscrutably under the covered porch which appears to be sound and dry. The porch rafter ledger is let into the stucco a varying amount (wavy walls, after all) but didn’t ping my moisture meter above 14% moisture content (MC) at it’s worst. The rough bucks topped 50% which is when my inexpensive meter calls it quits. One window (the worst one) is within spitting distance of the upstairs bathroom, but we ran the water in the shower, sink, toilet, for a long time with no increase in wetting. We also have had some decent rains which didn’t worsen anything. Finally, we’ve attacked the sides of the house that we didn’t think had any moisture issues. The worrisome walls we have yet to grind into. There’s 26 windows all told.
The other window bucks have been okay thus far. Some rot primarily in the sills, but more easily repaired. The windows were installed to what I recall as being “best practice” for the time. Caulked flanged, felt paper wrapped into the rough opening. No tapes. No sill pan like we do nowadays.
So. Issue 1: I am not an experienced stucco plasterer. I know I need to grind a lot more stucco out to chase the moisture source and solve it as best I can – assuming I can pinpoint it.
Issue 1.1: There’s not a wealth of knowledge locally to repair or maintain a stucco structure around here, so overtime whenever these folks suffer from a maintenance issue they are going to bump up against this again – even if I gain some measure of competency in stucco repair after this I might be busy, injured, moved to wherever the Sam Hill… I don’t want them to be vulnerable to having only me to turn to if and when an issue creeps up; that’s not a sustainable situation for them or me.
Issue 2: The stucco was applied by volunteers and well-wishers, so has it’s share of hairline cracks and lacks for a weep screed, which certainly raises a flag for me. I think. I am no expert on this. The stucco was also gone over with some kind of elastomeric coating to, I think, bridge the cracks? It seems to have worked in some areas, but not very well overall.
Extreme fix proposal:
Remove the stucco, install vertical sleepers (maybe 2×4’s on edge?), insulate (cuz why not?) with dense packed cellulose or rockwool, sheath with air sealed 1/2 plywood & WRB or taped Zip System OSB, rainscreen, and reclad the house with something within the local talent pool (e.g. shiplap; clapboard; shingle; etc.).
This strikes me as an expensive fix. The clients are committed to the house and the land, and I wonder if this might actually save them money in the long term since repair and maintenance will be a cheaper proposition if folks know how to disassemble and reassemble the cladding system easily.
I would appreciate any and all thoughts you all have regarding this. I like taking on jobs that push my out of my depth so I can stay on my toes, and this one is certainly no exception! I want to guide these nice clients down a path that will make their life easier long term, but don’t want to bleed them dry doing it.
I would also welcome any stories anyone has about remodeling the exterior walls of straw bale homes in general.
Thanks!
GBA Detail Library
A collection of one thousand construction details organized by climate and house part
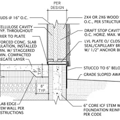
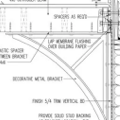
Replies
David,
That sounds like a good plan, and what I'd do in that situation. It's a lot of work, and a lot of finicky details, but so are all the other viable alternatives.
David,
It would be good if you can answer the question, "Where did the moisture come from?" If it turns out to be condensation of moisture piggybacking on exfiltrating air, it would be good to know that before you develop a solution.
Martin,
I completely agree. If I can't solve this moisture issue it's not going to make sense to go forward. Do you think it's reasonable to assume that I'm seeing exfiltration through the process of elimination? I see no evidence water intrusion from the outside, and haven't been able to make the bathroom fixtures leak. The next worst window buck is about 18' away and not near the bathroom at all. And there's another window in between these two that appears to be sound.
There are round pole floor joists that penetrate the interior plaster and presumably bear on a load bearing structure inside the wall (it's a two story house). These joists do have some checking in them.
I think what I'm struggling with is that lacking evidence for more obvious sources of moisture, is the de facto answer likely to be exfiltration? What else could it be, I wonder? My gut is telling me that the back side of the stucco is acting as a condensing surface for moisture laden air moving through the wall. I've seen this evidenced to varying degrees in other houses before - not straw bale houses per se - but usually this level of rot has had a clearer answer in the form of a leaky cladding/flashing system. The wood is complete chowder.
The clients have a bath fan on a timer that they run in the winter, but they have never had an energy audit done so they're not running the fan based on any recommendation from a professional.
I feel like I'm grasping at straws for an answer that sits right. No pun intended. Well... maybe a little.
Since there doesn't seem to be a pattern to the wood damage, you could have some leaking windows. Without a proper sill details, small leaks from the windows will take untreated wood apart in no time. All windows will leak eventually, that is why flashing details are important. The elastomeric coating on the stucco probably made things worse as it would reduce drying.
Proper flanged window install with stucco calls for a drainage plane/wrb behind the stucco. Sounds like there isn't anything there, leaks from the windows have nowhere to go. If you are installing new windows, I would figure out a way to have the sill in the rough opening drain to the outside above the stucco and install a separate sloped metal sill from the window over this.
Hi Akos,
Thanks for your reply. I don't know if I made it clear that the rot I'm seeing is primarily focused in the head of the window buck. The other windows we have removed have indeed had some minor sill rot related, no doubt, to the situation you have described. Also the worst window has been under a covered porch which doesn't show any tell-tales of having leaks.
Are you familiar with the elastomeric coating? Do you know what it might be - like a trade name or something? On the one hand I want to know what I'm grinding out and on the other I'm curious about it's perm rating (if any) and design intention.
I agree with you about the water having nowhere to go. There may be felt paper under the stucco - there is felt paper wrapping the window bucks. If there is a way to isolate the stucco from the felt to allow for a drainage plane I can't imagine how. The stucco wraps all the way down and over the foundation and isn't in such great shape. I don't see anything like weep holes or a weep screed to allow for water to drain away, which might explain some of the major cracks and loose chunks of stucco along the bottom.
I hope this helps create a more complete picture.
Thanks again for your input!
Being a two story house, it could be how the porch is attached the to the main structure specifically the roof/wall intersection details.
Flashing done wrong there could be channeling water down behind the stucco instead of out over the roof.
David,
A big part of my business is stucco consulting. I don't have any first-hand experience with straw bales, but I'll give you what help I can.
First, the stucco itself. It would be worth the effort to remove a few sections to figure out what the layers of materials are and whether there is even a WRB at all. I know that some guides to straw-bale show stucco simply being plastered right on the straw. As I recall, the belief is that the straw bales act somewhat like a mass masonry wall, absorbing and redistributing moisture and eventually allowing it to dry to either the interior or exterior. This could be why you see no drainage details. The cracking is likely related to simple movement of the straw bales. They are certainly not a very stable substrate for something rigid like stucco.
Elastomeric coatings are a very mixed bag. There are lots of them on the market with wildly different proprietary formulations, and you probably won't be able to tell what was used here unless someone comes out of the woodwork and admits to having installed it. Some have decent vapor permeability and some almost none. I have seen some outrageous failures with these coatings, including one mid-rise building that developed basketball-sized blisters full of water all over the building. Looked like it had warts. This did not make the owners happy. On the plus side, the right elastomeric can bridge and seal minor cracks and will reduce wetting from the exterior. So unless there is any good evidence that the coating is messing things up, I wouldn't worry too much about it.
I agree that the rotten window headers sounds like condensation of exfiltrating moisture, especially in your climate. What was the weather like when you measured 50% MC? How cold was it overnight? I know you're flirting with freezing weather these days, and that would be cold enough to condense typical interior moisture. I have no idea how to control 3D airflow through straw bales. Yikes. The air could be coming from anywhere. Your best bet might be to replace everything you can with treated lumber and maybe spray canned foam into any voids you find during the replacements.
I've attached a stucco repair specification that I've used for years in one form or another. It will help you figure out how to graft the new stucco onto the old.
Good luck.
Hi,
It looks like the elastomeric coating should be removed by sandblasting & a new finish coat applied. This will blend all the patching. They can maintain the finish coat by application of a colored fog coat that is sprayed on. The fog coat will keep the ability of the wall to dry outward. It is a lime, cement & pigment mix.
Full removal of the plaster from the bale walls my be impractical in that the plaster bonds with the straw and can be difficult to remove.
Hopefully the structure is a post and beam building with strawbale infill. If so the window framing is not structural to holding up the roof, and can be redone.
The current way to air seal & fill in gaps between wood framing & the bales is a light straw clay mix or a cob type mixture. The clay element take on the moisture rather than the wood.
It has been shown cement plasters direct to wood will rot the wood. Any new cement plaster patches should have a cement -lime plaster or lime plaster to provide vapor permeability to the plaster finish.
The windows need a good sill & path for moisture out of the wall just below the sill.
You might check with the California Straw Building Association (CASBA) website for professional help or if you contact them they could reference you to some one in your area with some expertise. CASBA has been involved with getting strawbale into the code as an appendix that can be adopted. The professionals Architects & engineers on the list have done work around the country. https://www.strawbuilding.org/straw-resources