Replacing siding and windows: should I remove the interior poly sheeting?

I am replacing my T1-11 siding with Hardie and replacing all my windows and I have a question on vapor control. My home was built in the mid 80s, and at the time in western PA it was common to use foam board on the exterior and poly sheeting on the inside of the studs.
The current structure of the wall is T1-11 siding, 3/4” poly-iso foil faced board (it’s actually slight over 3/4” thick), 2×4 studs with let-in bracing and r11 unfaced batts, poly sheeting, and 1/2” drywall. The t1-11 is in rough shape and needs to removed as it will not hold a nail or screw, and as far as I know when I a couple small areas of exterior wall open the framing looked in good shape.
While replacing the siding I will have the walls open as I anticipate most of the poly-iso to get damaged, there are holes from various pests over the years, plus the existing windows where attached through the poly-iso. While in there I plan to replace the R11 fiberglass with r15 Roxoul, then add 1/2” plywood sheathing with wood blocking for new windows, new 3/4” XPS (or R-Max poly iso) foam board, and wrap it with tyvek, and finally Hardie attached with 2-1/2 siding nails. The question I have is should I cut out the interior poly sheeting in the stud spaces? Or leave the poly sheeting and attempt to seal all interior penetrations through it?
For what it’s worth I have noticed a number of homes in my area which where built around the same time and probably by the same contractors with the same wall detail. They have been getting new siding, which they would remove the old siding, apply house wrap and the new siding and call it a day. Obviously these contractors that are doing the siding replacement are looking to just get in and out, not saying it’s right or wrong.
I am trying to take the correct approach here while I replace the siding, and address anything in the inside at this time. I have considered increasing the XPS to 1” (from proposed 3/4”) thick as that is the maximum non-nailable substrate allowed with the Hardie before requiring furring strips, which I am trying to avoid.
Thank you for reading and I appreciate your responses.
GBA Detail Library
A collection of one thousand construction details organized by climate and house part
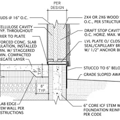
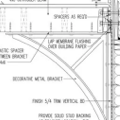
Replies
You have almost the same type of house construction as I do, except I have no poly and 1/2” polyiso. I’m also in the process of replacing the R11 fiberglass with R15 mineral wool, and I’m adding 3” of polyiso. I’m not doing it all at once though, and it was recently recommended to me on GBA to use a smart vapor retarded over the mineral wool since the 3” polyiso won’t be up for a while.
I think leaving the poly in there is taking a risk. I would use thicker exterior foam, probably polyiso. While you have the siding off is the time to do any exterior foam work.
Regardless of what you end up doing, be sure to do a good job of airsealing before putting the new mineral wool in the walls. Air sealing is always a good thing, and this is the only chance you get to do it right.
Bill
Hi Keilux,
If you are in Climate Zone 5, minimum R-value of exterior foam on 2x4 walls is R-5 (1 inch XPS or 3/4 inch polyiso), and you will not want to have a poly vapor barrier, so you can cut it out. Assuming you have painted drywall inside, that gives you a class three vapor retarder, which is recommended.
The key to making this wall work is air sealing. Since you will have the walls open, you have an opportunity to seal the perimeter of the wall cavities, electrical boxes, and other penetrations. You should also air seal the exterior, which you can do by detailing your sheathing (or the foam) as an air barrier .
You are planning a large project, and already planning to fur out the windows which includes interior trim work, so why not including a rain screen detail to allow you fiber cement siding (and your wall) some extra drying potential?
>"...minimum R-value of exterior foam on 2x4 walls is R-5 (1 inch XPS or 3/4 inch polyiso)..."
Derated for age the 1" XPS is at best R4.5 (the warranteed value), at worst R4.2 which is the fully depleted value, after the climate damaging HFCs that gave it the initial performance boost that allowed it to be legally labeled R5 are gone.
So with XPS you're really talking at least 1.25" to have any margin even on R13 cavity fill. With R15 rock wool in the cavities make that 1.5", and to be nice to the planet make it EPS, which is a stable ~R6 over time, and does less environmental damage than XPS. The performance of EPS is identical to the fully-depleted performance of XPS at a given foam density. Same polymer, different process.
Derated for temperature (important when looking at dew point control issues) most brand-X polyiso (and probably R-Max) would average about R4 @ 3/4" during the colder months that matter the most. Dow's Thermax polyiso would still meet spec at 3/4" though, according to their marketing fluff. If using R-Max make it 1" , not 3/4". If the shiny foil facer is next to a rainscreen gap (rather than housewrap) average performance of 1" generic foil faced polyiso would just barely make it for dew point control on R15 due to the performance boost of the low-E aluminum & air film, but even sandwiched to the housewrap it would be fine with R13.
Parts of western PA up in the mountains are zone 6, which would call for slightly higher R-values on the insulating sheathing.
Yes I am in climate zone 5, and I do have painted drywall, once back from 30 years ago and then a repaint about 3 years ago, which was at least 2 coats and touch up. The windows have the jambs built in, I did this to minimize the detail work on that end and have windows and jambs match, which is one of the reasons trying to mimic what is already on the house.
On the foam thickness and type isn’t the season in question the winter months, which XPS r-value increases as the temperature decreases, while Polyiso‘ se-value decreases.
Brian is expressing an opinion - code, research and experts also support the use of any amount of external foam as long as the interior and exterior perms are correct. See here and relevant code.
Don't use XPS (it's bad for the environment) and don't think that 3/4" polyiso will provide R5. Use 1" unfaced EPS along with a Class II vapor retarder on the interior side.
But with Hardie, I'd use furring strips to create a rain screen vent. Then you can use thicker EPS. If you can't use furring strips, put DrainWrap between the foam and plywood.
Use a blower door (or similar) to verify air sealing.
Hi Jon,
It's true that you can adjust materials and permeance on the inside and outside of a house to create many wall assemblies that work. But most builder and remodelers rely on rules of thumb, codes, building inspectors, etc. to determine how to detail a building envelope.
Concerned about giving confident recommendations for questions like this, which are among the most common here on GBA, I just spoke with Betsy Pettit at Building Science Corporation. Betsy confirmed that the chart in section R702.7.1 of the 2018 International Residential Code presents safe wall assemblies and good rules of thumb. In fact, she said that Joe Lstiburek helped to get that information into the IRC.
For Keilux, in zone 5, with 2x4 walls, the chart says that as long as the house has vented cladding over the plywood sheathing he plans to install or that it has continuous insulation with an R-value of R5 or greater, he can use a class III vapor retarder on the inside.
Betsy made a few points worth noting, some of which have already been mentioned, but I'll share them anyway:
1. R5 is a minimum amount of continuous insulation for this wall. Increase the R-value if possible.
2. Though the chart says you can have vented siding or continuous insulation to allow a class III vapor retarder to be used inside, it's best to have both.
3. Keeping bulk water out of the wall is super important. So a well-detailed WRB and flashings are worth fussing over.
4. These walls need to be able to dry towards the interior. Though the IRC simply says "Class III vapor retarders shall be permitted...," the reason they are permitted is to maximize inward drying potential.
Betsy and I were only discussing walls with wood, fiber cement, vinyl, composite siding, etc. Not walls with stucco or other masonry siding materials which may require different assemblies/materials.
> R702.7.1 of the 2018 International Residential Code presents safe wall assemblies
Agreed - but as you now say, so do lots of other designs. "minimum R-value of exterior foam on 2x4 walls is R-5" is simply false. It needs a qualifier along the lines of "if you want to use a Class III interior retarder..." or "a wall that works well is....".
Evidently Building Science said nothing along the lines of "BSD-106 is incorrect".
+1 on being conservative - don't build to code minimums on such an important issue.
Hi Jon,
Your point it taken; I will try to be more specific about the sources and reasons behind my suggestions.
I did not ask Betsy about the document you shared. Coming from BSC, I have no reason to think that that it is not perfectly good advice. I was curious about making suggestion based on the IRC.
I am curious why you would state that there are no code minimums (and I'm asking sincerely; if I'm misunderstanding something, I'd like to clear it up. I'm no code expert).
When I look at N1102.1.2 (R402.1.2) of the 2018 IRC (on building thermal envelope) it says "The building thermal envelope shall meet the requirements of [the table below]..." For wood framed walls in Climate Zone 5 the table requires an R-value of 20 or 13+5. The footnote says that means R13 cavity insulation and R5 continuous insulation.
I guess continuous insulation could be interior, or created in a double-stud wall, but most often, it's exterior rigid foam. I also understand that the code is not always best practice, but based only on the writing of the IRC, is that not a minimum? Am I missing something?
> the table requires an R-value of 20 or 13+5
Those are R-value minimums, so R20+0 satisfies code. So does R20+4(foam) or R13+R5(rockwool). I call that "no minimum" on external foam.
In the case of keilux's wall as planned, you (and more so Dana) may have a point wrt heat loss. I haven't done the U factor calculation with 1" of EPS (.060 is required). Maybe it requires graphite to meet total R value requirements (a very minor concern compared to the moisture risk of the other options).
keilux,
I'm afraid I have hijacked your thread. If you don't feel satisfied with the answers and suggestions offered, please ask more questions or for clarification.
I want to add one thing to the whole “rule of thumb vs. building science” discussion. I would warn that unless you are absolutely certain that your builder fully understands the science behind any particular building assembly that deviates from the norms and rules of thumb, then you’re better off going with the prescriptive assembly (the “rule of thumb”) and not the fancy assembly.
I work as a consulting engineer and often get called in after the fact to fix things that someone built without fully understanding the entire system. Usually people that don’t fully understand what they are doing will miss critical details that may not show up as problems until years later. I have many stories about things like that. Consulting engineers are expensive, and so are the contractors that implement the solutions we consultants come up with.
I tell all my clients the same thing: it is better to ask a thousand questions to BE SURE you get it right the first time than it is to try to fix it later. The often recommended wall assemblies are known to work, and while they may be on the conservative side, they are safe. Any other assembly requires everything to be done exactly right, and that is asking for trouble if anyone involved with the project doesn’t fully understand how everything works together as a system.
Bill
Leave the poly. If after almost 40 years there hasn't been a problem, why would there be one now. Millions of homes in the more northern climes have been constructed with an interior poly layer and most of them work. I have remodeled many similar wall assemblies in NY and have found no evidence of mold. Ever. If I was building new it would not be my first choice but then again I would have a much more robust wall. Leave it alone it will be fine.
That is kind of my thought as to my knowledge there is no known issue in the past 33years and reason I am asking the question. Now that all could change when I open the walls, obviously that is when something would need to be addressed, but if I all looks good why not keep it, and air seal all penetrations, right? Just trying to do it once and do it right.
Thank you all for the detailed responses, and no worries in the high jacking, more information the better as perhaps someone in the future might find this useful.
So to summarize I am on the right page with the wall detail, sure there are options, and what I have considered will work. *Remove the poly sheeting, with the paint from 30years ago and 3 years ago would give me the class III vapor retarder, air seal all penetrations, seams/edges. The R15 rockwool + R5 exterior foam meets the requirement.
-Painted drywall - Class III vapor retarder
-All penetrations, seams/edges sealed
-R15 Rockwool
-1/2” plywood sheathing
-1” or 3/4” Foam
-Tyvek house wrap
Do I want to tape both, one, or neither of the 1/2” plywood sheathing seams and the 1” or 3/4” foam(XPS or Polyiso)?
*Just a question out of curiosity and I might answer it myself here, the idea of vapor barriers is to keep the moisture out of the wall cavity, however in the event that vapor does enter the wall you need one side to dry from, which in today’s standards is inward drying. However in the case of Tyvek, which to my knowledge is vapor permeable, if I were to leave the poly sheeting wouldn’t it still dry to the outside with the tyvek?
Reread #8. 1" XPS and 3/4" polyiso are bad ideas. 1" polyiso (other than expensive Thermax) is marginal (and almost everyone believes in being conservative wrt moisture problems).
Yes, outward drying is an important factor in dry sheathing. The foam (not Tyvek) used effects how much can occur.
If I follow what you are saying Thermax is the best, however expensive? However for outward drying Thermax would provide the least drying effect to the outside, and therefore not ideal in this situation, correct?
IMO (based on reviewing lots of research), unfaced EPS (against DrainWrap WRB) and Class II on the interior will provide the driest wall matching your requirements. Unlike most other things you are considering, it is substantially safer than code limits in terms of moisture risk.
I would not violate the expert recommendations found here (just scroll down to Table 3).
Hi keilux
Your wall assembly looks good. Just a few thoughts, two of which have both been pointed out already (so, excuse the redundancy):
1) You're exterior insulation is at minimum recommended R-values for such an assembly. You should considering increasing the R-value some.
2) Where you locate the housewrap, either behind or over the exterior foam, may depend on how you choose to instal your windows. I recommend reading this, for options and details on installing windows in foam sheathed walls: Innie Windows or Outie Windows?
3) Ventilating your siding with a rainscreen detail is considered best practice by most experts for a wall assembly like this.
Also, yes. You should detail either the sheathing or rigid foam as an exterior air barrier. That means caulking the perimeter of the panels and taping the seams (or using a fluid-applied product).
Your curiosity question is a thorny subject. Here's an article that may help clarify the issue: Do I Need a Vapor Retarder?
I had ordered my windows based on them being “outties” so the Tyvek would in installed over the foam.
My thought was to caulk the edges of the plywood to the framing, then tape the foam insulation seams to air seal from exterior.
I found this article, what kind of merit does it hold? I am referring to the chart in figure 6, in regards to my situation with the existing interior vapor barrier.
https://cdn.ymaws.com/www.polyiso.org/resource/resmgr/news_articles/2018-01-ahrenholz.pdf
Given my wall detail is it preferred to have a faced or Unfaced ridgid foam for vapor permanence and outward drying?
I took alittle time to mull it over, which I have a habit of over doing on most things. I don’t think I want to go the route of adding more insulation and furring strips, based on added cost/time, how the windows and doors where ordered, and a few others.
Remove all existing material, inspect for any signs of moisture. If it all looks good leave poly sheeting, air seal stud spaces and penetrations in drywall with low expansion window and door foam.
R-15 rockwool
1/2” plywood caulk and tape seams
1” Dow Tuff-r tape seams (or current polyiso)
Tyvek house wrap
Windows tied into the house wrap
How much cause for concern is there by using the R-15 rockwool over R-13 fiberglass in regards to the R-13+5 code? The reason I ask and why was planning on using the rock wool as I got it for an extremely low price, $10 a bundle, at the time I was looking for unfaced R-13 and came across the rockwool that was being clearanced out and jumped on it.
To what extent does polyiso lose its r-value over the years? The reason I ask as there is a good chance I currently have Thermax under my siding, however I believe it’s 3/4” so I would be better off replacing it with the 1” Tuff-R.
I decided to open a wall up to see what I am dealing with, now this was a north facing wall where the T1-11 was in decent shape, aside from the bottoms for being weathered and rodent/insect infiltration. The wall cavities look clean and dry, the rim joist/back of T1-11 in that area had some signs of moisture around the infiltrated areas. The polyiso did seem to shrink a bit, all seams have atleast a 1/4”+ gap or more. If there were any condensation on the interior side of the polyiso from the winter it would have been very minimal as I did not notice much/if any signs at all. Plus the existing poly sheeting, back of drywall, fiberglass all looks in good shape, no signs of moisture in the few cavities I had opened. Proper air seating should tighten it all up nicely. So probably going to just use the current fiberglass, scarified the little r-value for extra warmth on the sheathing side, is that is more advisable and put the new 1/2” plywood and 1” foam overtop. I do need to address the double header to roof joist area as the header is not insulated, may end up using some of that rock wool since it semi ridgid and will hold into place well without blocking the baffle vents.