Rigid Foam Strips for Thermal Break

Hey everyone, got a new build planned early 2024 in Lake Conroe Texas. We are doing 2×6 framing up and down with 5/8 OSB sheathing. I wanted zip R but the cost are just too high for our budget so I was looking for info about taking the Dow blue board rigid foam insulation ripping it down to 2” strips and installing over studs before the OSB sheathing. Then planning on going with open cell spray foam in the cavities. The foam board would be the 3/4 sheets.
Just looking for a cost effective solution to get the thermal break and getting a good insulation package. Before the spray foam was planning on the Areobarrier to get a tight seal and a fluid applied on the exterior.
GBA Detail Library
A collection of one thousand construction details organized by climate and house part
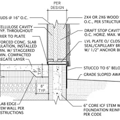
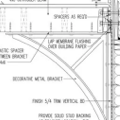
Replies
An engineer would need to approve this, specify fastener schedules, etc. because this is not a prescriptive design in the IRC, nor would I think any foam manufacturer would have pursued approval of such a design through an ICC recognized testing service.
Not sure if you are aware of what has been coined the "Bonfig wall" (https://www.finehomebuilding.com/project-guides/insulation/breaking-the-thermal-bridge), but you've described a reverse Bonfig wall. The Bonfig wall places the foam between the studs and the drywall. Unless the drywall happens to be a structural component of a shear wall, this interior foam doesn't affect the structural performance of the assembly (in contrast to foam between the studs and sheathing).
While I think the Bonfig wall has merits in retrofits (particularly if you have 2x4 walls and no plans to touch the exterior), you can consider other options for a new build.
One option is to frame the exterior walls with 2x8s. While it's extra labor because they're heavier, there's no extra steps. a 24" OC 2x8 wall with regular insulation has comparable performance to a 24" OC 2x6 wall with 1" of exterior insulation.
I never thought of that before. It definitely makes sense. I was just thinking about how the zip r sheathing places the foam between the studs and OSB and it’s widely accepted. The concept would technically be the same except that the foam doesn’t cover the entire wall assembly. I wanted to use the zip r 6 panels on the walls and zip r 9-12 on the roof deck. But the cost were significantly higher than I expected.
MyLifeinTexas,
It might have the same shear strength in practice, but what it lacks is the structural testing and fastener schedule that comes with Zip R.
Huber already did all the engineering for their Zip product line, which is why they can put the insulation between the sheathing and the framing. You MUST follow their fastener schedule though. What you end up with, using their products installed according to their procedures, is a "listed assembly", which means the *assembly* has been tested to perform in the application, and is KNOWN to be safe. It's that testing and engineering that you are paying for with their products, if you try to do it yourself, you don't have the "KNOWN to be safe", you have a "MIGHT be kinda sorta OK", and that's what won't pass muster with inspectors (and shouldn't -- it isn't safe!).
It's probably easier to just put your rigid foam on the EXTERIOR of the structural sheathing, which is commonly done, and which avoids all the potential structural issues with the fasteners. If you want to save more money, see if you can find some reclaimed or factory second polyiso to use here.
Bill
This. Just do exterior insulation. Also, I would highly recommend polyiso over XPS foam for environmental and R-value reasons. I live in Midland but I’m from Houston.
The "Bonfig wall" is similar to the SmartWall system that Pacific Homes (prefabs) on Vancouver Island here in BC has been using for about 20 years. (https://pacific-homes.com/pacific-smartwall-technology/)
Their walls have 2 x 6 top and bottom plates and 2 x 4 studs (proportionally thicker for colder climates), and custom cut 4" EPS with a 1/2" rabbetted (??) edge that overlaps 3/4" of each stud. You then put 1" of EPS over top, which results in a 1 1/2" thermal break over each stud. The 4" EPS is precision cut and very tightly fitted between the studs. I imagine that this also makes for a structurally very strong wall system.
This does require longer drywall screws and extra hassle in fitting electrical boxes, but putting rigid panels on the outside has its drawbacks as well.
There are ways to brace walls that don't require structural sheathing: https://codes.iccsafe.org/content/IRC2018/chapter-6-wall-construction#IRC2018_Pt03_Ch06_SecR602.10.4. You could use one of them with your proposed system.
Thanks for everyone’s input and advice. We will just use the foam sheathing on the exterior like originally planned and suggested. We are doing brick and hardie siding and that’s widely accepted. I just wanted something more than just the foam sheathing. I will talk to builder about doubling up and staggering the joints on the foam sheathing.
Thanks in advance.
Deleted
I actually found an article of the interior insulation/strapping idea in Fine Homebuilding. You can fur it out to a 2x8 wall which would give you an R30 if using 2x8 RockWool vs an R28 using exterior foam and 2x6 RockWool. It will also coast about $0.55 less per sq foot of wall space. I'm also a bit hesitant about putting foam board directly over sheathing (at least with Zip-R the sheathing can dry with an appropriate rain screen and good air flow). I feel like we are going to see a lot of houses with mold issues. There's a research group out of Alaska that shows the moisture retention in the various building assemblies. I'm surprised people don't reference this more.
I see some people making mini (or secondary) rainscreens between the sheathing and exterior insulation layer but feel like this negates a lot of the benefits of the insulation. Now you have cold airflow between your insulation and sheathing. Think of how well a winter jacket works when a gust of cold air goes up your back (between you and the jacket). Or...it would be like placing the fill in your jacket outside of the rain/wind resistant layer.
I would just glue some 1" XPS to 1" sheathing and rip it down to strips. Another benefit is that when you attach with screws the little bit of compression would allow you to correct for any bows in the studs.
https://www.finehomebuilding.com/project-guides/insulation/breaking-the-thermal-bridge
> I'm also a bit hesitant about putting foam board directly over sheathing
This is a common assembly with a good track record of success. The sheathing should not be getting wet. If it's getting wet to a degree that having foam over it is a problem, the wetting would likely be a problem without the foam, too.
> I see some people making mini (or secondary) rainscreens between the sheathing and exterior insulation layer but feel like this negates a lot of the benefits of the insulation. Now you have cold airflow between your insulation and sheathing.
If someone is doing this, they don't understand the purpose of exterior insulation in the first place and are throwing money away, both in materials and energy.
One would think that the sheathing shouldn't be getting wet; however, because of water absorption and diffusion of exterior foam it's ultimately inevitable; to some degree. Hence why people prefer foam (or Rockwool) that is more vapor permeable (to allow drying). The bigger issue (than water entering from the exterior) is that most people do not put enough of the insulation on the exterior wall and end up having moisture buildup on the sheathing d/t dew points. The exterior insulation will not allow for efficient drying to the exterior. There's a great research group out of Alaska that has demonstrated moisture retention on the sheathing of these various assemblies.
I agree! Unfortunately, I've seen a lot of 'famous' Youtube builders demonstrating (and praising) the idea of this secondary rainscreen to minimize moisture buildup between the sheathing and insulation.
One reason I prefer dense filled or batt cellulose in the stud cavities, over mineral wool or fiberglass, is that the insulation has more "hygric buffering" capacity. It still allows slightly damp sheathing to evaporate to the interior and also has some ability to hold water. It's my understanding that in colder climates you want this ability to dry towards the interior.
Deleted
I don't know if it's available in the USA but I've seen it here in France. You can buy the metric equivalent of 4'x8' gypsum board sheets but they come already bonded to standard thicknesses of EPS insulation. In France where walls are commonly built of CMU they are simply glued to the inside face of the block walls and you're ready to plaster the joints and paint. I see no reason you couldn't attach them to stud framing as well.
What do you do in France for electricals and plumbing in those walls? Are they set in conduit within the CMU prior to putting up the insulated gypsum board sheets?
Bill
Different solutions for plumbing and electrical.
Electrical is in conduits attached to the inside face of the CMU. Then the foam is routed as needed around the conduit.
Inside walls are typically framed with light gauge steel studs and so of course easily accommodate plumbing. At exterior walls they may again rout the foam or very often frame inside it with light gauge studs, often only going as high as needed, not the full wall height. For example vanities and toilets might have 4' (1.2m) walls creating a ledge above the sink and toilet.
If I can find any houses in the neighborhood where I can get some photos I'll post them in a future comment.
If you are seeking a thermal break, you can go a long way by using 2x6 top and bottom plates, then use 2x4 studs at 12" on center, alternating them between being flush with the inside and flush with the outside. Your only thermal bridges are then at top and bottom plates, and around doors/windows.
In my case this was almost the same as using 2x6 at 24" oc. While it uses more board feet of lumber, the board foot unit price for 2x4's was significantly less expensive than that of 2x6's, so that the lumber for 2x4's @ 12" oc was less expensive than 2x6's @ 24" oc. There was a bit for labor which roughly equal to the lumber savings.
The other benefit of this over your proposed method is that you wall depth will confirm to standard 2x6 framing, so you can order standard returns for your windows (if you are not using drywall returns) and standard exterior door frame throat dimensions.
For even more savings, use regular zip boards at the exterior, tape them tight using some of Scott True's methods (check YouTube), and insulate with damp applied cellulose.