Rim joist condensation

My 1979 house is what I’ll call traditionally built; 2×10 floor joists & rim joist. The rim joist cavities are insulated with fiberglass and its causing condensation as it’s currently in the single digits here in Wisconsin. I plan to replace it with closed cell spray foam but dont have the means to do so in the very near future. My question is, would I be better off pulling all the fiberglass to allow the rim joist dry out and just accept the heat loss?
GBA Detail Library
A collection of one thousand construction details organized by climate and house part
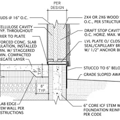
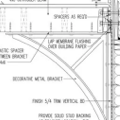
Replies
Bryan,
It would be good to let it dry out and then replace the insulation and seal it all up; you could air-seal that floor cavity on the inside to prevent humid air from reaching the cold rim joist.
It could also be as a result of a make-up air issue. Can you feel air coming in through spaces between the subfloor or sill plate and the rim joist when you turn on a range hood or bathroom fan? You might need to seal any cracks and look for a makeup air solution when turning on exhaust vents.
Closed cell spray foaming the cavity would create an air and moisture barrier that would keep the moisture from condensing and help seal it all up. You could try to do some air-sealing above and below the floor with acoustic sealant all around the perimeter of the cavity and some 6 mil poly or sheetrock to keep the inside humid air out of the floor... foam sheeting can also be spray foamed in place over the rim joist as a DIY alternative as long as you get a good seal all the way around.
Will
Thanks Will. As I mentioned, I dont really have the means to properly remediate the issue right now. My real question is what to do in the meantime? Leave the fiberglass or pull it?
Pulling the insulation out of the way near the rim board will warm up the cavity and might reduce the chance of condensation short-term. It all depends on if the rim board settles at a temperature that is warmer than the dewpoint temperature. If your house is 70 degrees and 40% relative humidity, then the dewpoint is about 45°F. If the board is colder then humidity will still condense there unless you can keep the humidity out. Condensation may still be an issue depending on how cold it is outside...
When you do get ready to apply spray foam, make sure the rim joist is up above about 50 degrees or so. If you try foaming it while it’s down in freezing temperatures the foam won’t expand and adhere correctly.
Bill
Bill, while that's true for one-part foam, professional installers can spray at much lower temperatures, albeit with more risk of failure, but it can be done.
Bryan, with fiberglass batts at your rim joists, the same amount (or less, if the batts are faced) of warm, moist air is reaching the rim joist as it would without the fiberglass. The only difference is the amount of heat (energy) available to push the moisture through to the exterior.
Assuming the exterior is somewhat vapor-open, you could remove the batts and let heat push the moisture through.
Or, with the batts in place, the surface of the rim joist will stay colder, probably below 50°F most of the time, so mold and fungus won't be able to grow until it warms up outside.
Removing the batts is somewhat safer, but I would probably leave them in place until the average outdoor temperature is well above freezing.
Hi Brian -
1. if you warm the inside surface of the rim joist above the dewpoint, you won't get condensation.
2. You could change the dewpoint by decreasing the amount of moisture in the air (dehumidify the basement or decrease sources of moisture the basement sees).
3. instead of spray foaming the rim joist, you could use decent-sized scraps of rigid insulation and rough-cut them to the rim joist cavity dimensions and foam the perimeter of the rough-cut insulation.
4. Professional spray foam installers need to follow the installation requirements of the spray foam manufacturer and they do differ. But if the spray foam reaction is exothermically-driven, then substrate temperature is critical to proper installation. See this article: https://www.buildinggreen.com/blog/foam-place-insulation-7-tips-getting-injection-and-spray-foam-right.
Peter