Spray Foam vs. Mineral Wool for Roof Insulation in Cold Climate

The specified roof assembly for zone 5A has
(Sloping)
-EPDM Roofing Membrane
Tapered XPS insulation 2″ min R-10
Vapor control
Roof Decking SSD
WD Framing SSD
Mineral Wool Batt R-32
Poly Vapor barrier
WD Furring to finished ceiling height,
GWB
(nearly flat – small area)
Asphalt shingles
WRB
Roof Decking SSD
WD Framing SSD
Mineral Wool Batt R-32
Poly Vapor barrier
WD Furring to finished ceiling height,
GWB
Contractor claims Mineral wool R-32 is hard to find in Ontario and proposes using spray foam (Hunstman Heatlok SOYA HFO CCMC # 14078-L).
I loath the idea of spray foam – but before I push back, is there some benefit I am missing or some problem I am not anticipating?
(There is a similar issue with insulating a garage ceiling that is above ground but below the living space – again, mineral wool was specified, same complaint)
GBA Detail Library
A collection of one thousand construction details organized by climate and house part
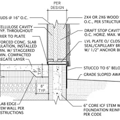
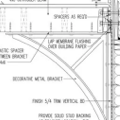
Replies
Lets break this up.
Your first one:
-EPDM Roofing Membrane
Tapered XPS insulation 2″ min R-10
Vapor control
Roof Decking SSD
WD Framing SSD
Mineral Wool Batt R-32
Poly Vapor barrier
WD Furring to finished ceiling height,
GWB
In zone 5, you want 40% of your overall R value as exterior rigid. So that R10 is good for about R15 of cavity insulation. This ratio can be pushed if you use a smart vapor retarder, so you can go up to R22 in the cavity to pass code. 6 mil poly can work on walls but it is trouble for unvented roofs, you want a variable per membrane here.
(nearly flat – small area)
Asphalt shingles
WRB
Roof Decking SSD
WD Framing SSD
Mineral Wool Batt R-32
Poly Vapor barrier
WD Furring to finished ceiling height,
GWB
You want this vented. For a small area like this, soffit intake vents only are fine if you can't vent the top. The only way to make this work unvented is with spray foam. With a vented roof, poly vapor barrier will work. If you go with spray foam, skip the poly. If going vented, the batts should be over the ceiling not the roof.
"There is a similar issue with insulating a garage ceiling that is above ground but below the living space – again, mineral wool was specified, same complaint"
This is a floor over unconditioned space. The good thing about floors is you don't need to vent it, so your batts only option is fine. You will need poly under the subfloor though. If you are doing spray foam, getting an inch or so under the subfloor to seal this up might be worth it for indoor air quality reason, there area also cheaper ways to air seal but are a bit more labor.
I would call one of the commercial drywall places, this is where I usually order this stuff from plus they carry brands other than Rockwool which can be cheaper sometimes. Mineral wool is standard in commercial construction and they can order you any standard size. The other option is to go for two layers, in a pinch I've used R14+R22 instead of the thicker batts.
Can someone with more knowledge of the manufacturing process explain why spray foam is worse than eps? The new spray foams, especially those with HFO have GWP of 1 or 2, while traditionally EPS is higher, around 6-7. Why do people hate it so much still? Is it a hold over from when the majority was using super high GWP blowing agents?
The new spray foams, especially those with HFO, have a smaller impact on the environment (like a GWP of 1 or 2), which is better than the older ones. But the dislike might come from the past when people used spray foams with not-so-environmentally-friendly stuff. So, it's kind of like old habits dying hard. Nowadays, there are more eco-friendly spray foam options, so maybe it's time to give them a second look for insulation.
This product seems to be in the ~2.5 kg CO2e range according to their EPD, page 14, which really isn’t that bad. Better than mineral wool for sure!
https://huntsmanbuildingsolutions.com/en-CA/sites/en_ca/files/2021-07/Final%20-%20Hunstman%20-%20EPD%20-%20Heatlok%20HFO%20and%20Heatlok%20Soya%20HFO%20-%20ENG.pdf
The BLOWING AGENT has a GWP of around 1, and foam companies have done an excellent job at marketing that portion of the total environmental impact. The remaining ingredients also have an environmental cost.
Yes I think this gets to the root of the question, are the other ingredients actually any worse than all of the other foams recommended, especially eps and poly? Because it seems like the main reason people don’t recommend XPS is based on the blowing agent.
This specific foam also claims 22%recycled or renewable ingredients ( I think they use soy in some capacity but have no idea in what capacity). I realize take this with a grain of salt as it from the manufacturer.
I feel like I am constantly seeing people on here going the cut and cobble route solely based on avoiding spray foam, when spray would be a better option, especially if the aversion is based on high GWP blowing agents that are being phased out.
As to the higher cost I think this is a bad holistic approach. We are constantly using higher costs materials for a better built structure, and often times it seems like ccSPF would result in a better built structure, particularly in retrofits and sometimes even in new construction. And I think in many instances if you factor in install cost (especially cut and cobble) of other foams they would not be that much cheaper.
For cost: 4x8 2” eps is $35 and has r 7.7. So $.142 per r/sf
I recently got quoted $1.5/ board foot of spray foam. The above spray foam has r7 ( I don’t know how accurate that is). So it works out to $.21 per r/sf.
So the eps for raw material is about 70% the cost of installed spray foam. It seems fair to say that install cost could easily overrun the spray foam.
to freyr comment #2,
I am not seeing any thing that would suggest the chemicals being blown by the new low GWP HFO are any different from before. While the previous blowing agents were especially bad for global health, badly mixed chemicals causing a home to become unlivable also played into why it was not recommended over EPS or Polyiso choices. The placed cost per R is high relative to other options. Foam has good value in certain places where other products simply won't perform. It is great to hear that the new blowing agents are rated as low as 1GWP when it makes sense to foam.