Running wiring into a crawlspace from a wall on a slab

I have designed a kitchen/garage addition that I am about to start work on. Because yard slopes toward the house the garage will sit slighter higher than the kitchen, with a step down into the kitchen. Because the garage is larger than the kitchen the common wall will sit on the garage slab. Also, a new electric panel will be in the garage on that common wall.
The questions is; how to you accommodate running wire down through the garage floor and into the crawlspace in this scenario? Is it as simple as drilling holes in the block foundation and running the wires down through the cavity of the concrete blocks, or is there a more elegant solution?
GBA Detail Library
A collection of one thousand construction details organized by climate and house part
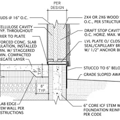
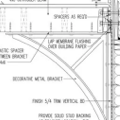
Replies
I would put a couple of 2" or 2.5" PVC elbows into the block wall before you set the partition wall and have it poke up through the bottom plate and end in the crawlspace.
Since you can't drill holes through I-joist flange, not even for wires, you can simplify your life a bit by either using a ledger lagged onto the block wall instead of the last I-joist or at least nudge that one over a bit so you have some room there to work.
If the garage is unheated, I would not have a continuous run of the garage slab under the wall. This can be a big thermal bridge and can cause condensation and mold under the wall there in the winter time. A thermal break of somekind (1" or 2" of rigid") would be good, even better of you bring the rigid all the way down on the outside of your block wall to the crawlspace footing.
Yeah, I know the question is about wiring but I don't like the look of that wall. That bottom corner is a spot that's impossible to insulate and both the wall and the floor will be susceptible to rot. You could solve the wiring question by putting the framed wall on top of the framed floor. That would then give something that could be insulated. Bolt a treated rim joist to the block wall, with blocking to the next joist to support the wall. I'd put treated sheathing above the rim joist until about a half a foot above the pad so that there's a layer of treated wood between the concrete and everything else. Wiring can now go in the wall. The rim joist can be insulated like the other rim joists in the house, maybe spray foam?
bsandersga,
As Akos has intimated, a lot depends on how you are planning to insulate between the two. Cantilevering the common wall over the blocks several inches, combined with offsetting the first TJ might work - and also provide backing for your baseboards.
I know you explained the reasoning, but I'm having trouble imagining how what looks like a 4" step would make an appreciable difference on even a slightly sloping lot. Having the floors flush or the framed one slightly higher makes everything easier, including keeping fumes from the garage out of the living space.
Does your code allow flat slabs for garages? Ours requires a slope, which would make setting it on the walls very difficult.
You have a good point. I will take a good look at the site and if I can make everything level. It was the software I used, HomeDesigner Pro, that placed the slab where it is because of the terrain input and I never bothered to adjust it.
bsanderga,
You can still step down the foundation by any amount you want by adjusting how the floor joists are attached to the exterior walls.
I’ll tell you how I would do it based on experience at my own house, which is not new construction and is 40 years old with the main electric panel located in the garage, with the rooms next to the garage on a slab (so similar problem of getting wires in.) All wires were run from the panel, straight up into the garage attic. Then they went through the rim joist between the garage and family room so they were all in the family room ceiling. Then the wires for the family room dropped into the walls where needed and other wires went across the family room ceiling and on to their final destinations (kitchen, etc.)
My panel is recessed into an uninsulated outside wall so the wires coming out of the top of the panel do not require conduit since they are all protected inside the wall. You could achieve something similar if you build another “mini” 2x4 wall on the inside of your garage wall that is just wide enough to accommodate the width of the panel (maybe 30” wide x 4” deep by full height (8 ft?)) You could drywall the garage side of the shared kitchen/garage wall first for air sealing, then build the second “mini” wall to house the panel. You can have some kitchen circuits coming out of the bottom of the panel and going straight into the kitchen wall if you choose. For most other circuits, you could have them come out of the top of the panel, straight up in your mini-wall until you reach the height of your kitchen ceiling and then through the rim joist and into the kitchen ceiling, and on to their final destinations. Basically, all of your wires will come down from the ceiling, instead of coming up from the crawlspace. Depending on the height of your crawlspace, this could make for much more pleasant working conditions. We have A LOT of wires in our ceilings, including a 6/3 wire for the electric range. If you want to run all those wires through conduit and into the crawlspace, you should check the electrical code because I believe there are rules when running multiple cables through a single conduit.
I am curious to know if this is a new main panel or a new sub-panel? And where is your old panel located?
This is a new main panel. The meter will be relocated from the back of the house to the side of the garage. I want to transfer all the circuits to the new panel and right now they are all under the house in the existing crawlspace. If I don't go through the new crawlspace, then I would have to run everything up a wall, through the attic over the kitchen, and down another wall to the panel. I think I may have figured out a solution. Stay tuned.
“The garage will sit slighter higher than the kitchen, with a step down into the kitchen."
How sure are you that your plan will be approved even if approved I am not sure it is a good idea.
Most garages will house a car or three with 20 or so gallons of gas in each. They tend to leak gas fumes that are heaver than air most codes require the garage to be at 6 inches lower so the overhead doors will be lower than the occupied spaces allowing any fumes to escape harmlessly outdoors.
What you are preposing is risky in that the fumes could settle into the occupied spaces if the concentration became high enough and an ignition source were present fire is a real possibility.
Walta
The plans were approved and building permit issued, but... I am taking your advice and will get the garage floor down lower.
This is my new, more elegant solution. Because the garage is wider than the kitchen, that was causing my conundrum. If I bump the part of the foundation over, just for the length of the kitchen, and build a treated cripple wall, then this common wall can extend across this wall and the a portion of the slab beyond the kitchen. This makes it easy to install insulation, pull wires, and run water line. And, the garage floor can have a slope.
bsandersga,
"This makes it easy to install insulation"
How are you planning to insulate the walls of the crawlspace?
Also: What is the relationship of the floor joists to the foundation they bear on? Will there still be a stepped foundation with them on top, or do they use hangers?
I'd start with a more basic question: is the crawl space going to be insulated at the floor, or at the wall?
If it's at the wall I would consider going all the way around with the treated wall and having it support the joists. Then you can put a nice capillary barrier between the concrete and the rim joist, which is tough if you use hangers.
I am doing what DC Contrarian suggested, Take the wall around with 1/2" polyiso between the treated lumber wall and the block wall, then insulate with Rockwool. It will be a bearing wall on two sides, and there just for insulation on the third side. The fourth side is open to the existing encapsulated crawlspace.
bsandersga,
Is 1/2" of rigid insulation enough to stop moisture condensing in your climate?
https://www.greenbuildingadvisor.com/article/how-to-insulate-a-basement-wall
This is Northeast Georgia. I just located the residential energy code for Georgia. They recommend 1", so that will be just as easy as 1/2". The crawlspace under the existing part of this house (built in 1979) is encapsulated and has a dedicated dehumidifier, no vents, and no insulation and that has been working well for me. Many times better than a dirt floor with the recommended foundation vents.
bsandersga,
I think you have come up with a good solution.
If you are using I-joists, the easiest is to clear span instead of the mid span support. Slightly larger I-joist, saves the labor of the mid support wall and foundation under it.
Your new detail looks better. Shift the 2x4 wall over a bit to make room for a layer of rigid insulation. In most climates code for that is between R5 and R10. The rest of the insulation can be fluffy batts in the walls.
If the other two walls are also outside walls, you want similar R value there as well. Might be simpler to simply use a layer of rigid thick enough to meet code instead of a stud wall+rigid.
This all assumes your crawl is insulated and conditioned which it should be. This is the best option in any climate. Uses less insulation than insulating floors, more energy efficient, end up with warmer floors. Also you can use any floor covering without having to worry about mold.
Good ideas.
The mid support wall is so I don't have to dig out even more dirt and still be able to match up with an existing floor. Since I will be the one building the wall, I don't mind giving it a couple of hours. Also, it will be right under a large kitchen island with a granite top.
For all the suggestions about running large conduits: if the conduit section is more than 24 inches long, code requires that you DERATE the ampacity of the conductors within per the table 310.15(b)(3)(a). If you run 3/4" conduits, you'll have less issue since it's difficult to fit enough conductors in a 3/4" conduit to get into issues with the derating. Note that when you derate, you derate from the ampacity in the 90*C column of the table, assuming you are using 90*C rated wire (THHN, and NM-B too, since the conductors in that actually use 90*C rated insulating materials).
To extend multiple circuits, I would run multiple 3/4" conduits from 4-11/16" (so-called "4-11" boxes) mounted near the old electrical panel. Run individual conductors in the conduits for the multiple circuits. You only need ONE ground wire PER CONDUIT, sized for the largest ampacity circuit in that conduit. This is usually easier than running a bunch of seperate NM cables. Note that it's also possible to share neutrals in some cases, but I generally avoid doing that.
Personally, I would try very hard to install the panel in an interior wall somewhere. Electrical equipment, including circuit breakers, will hold up much better when installed in conditioned space and not outdoors or in a garage. I try to not install any electrical equipment outside of conditioned space except for the meter.
Bill
Is it the cold or the heat or humidity that causes problems?
Generally the problem in unconditioned space is condensation. You get it with cool temperatures and high humidity.