Insulating Finished Basement Walls

My daughter in Virginia has a home with a basement apartment. The walls are below grade, partly below and fully exposed to outdoor air. The interior is wood 2 x4 stud framing covered with gypsom wall board. She would like to insulate these walls to improve comfort and a contractor 7proposed blowing in dense-packed fiberglass. But all my reading indicates filling the space with insulation will make the concrete wall colder and unless you can keep the water vapor in the interior from migrating thru the insulation, you will promote condensation on the wall and liquid water problems. I don’t think blown-in, dense-packed fiberglass will keep water vapor from reaching the concrete, especially in the summer when humidity gets very high. My only thought is to apply rigid foam board over the gypsom wallboard, caulk top and bottom joints, tape the seams, seal & gasket the electrical boxes and cover with a new layer of gypsum wall board. Can you think of a simpler approach using some type of blown in product? I don’t think high density, vapor proof foam can be injected into a wall cavity; can it?
GBA Detail Library
A collection of one thousand construction details organized by climate and house part
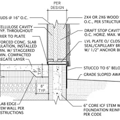
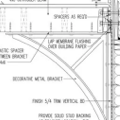
Replies
I don't think entombing a wood studded and drywall wall between below grade concrete and rigid insulation is a good idea that wall will rot away.
Short of removing the wall and starting over with rigid or spray foam against the concrete, you might be able to strip the drywall and spray foam the stud cavity. Not ideal since the studs will bridge to the concrete.
You want to keep the ground moisture away from organic materials that will host mold (wood, drywall,etc), and you want the interior condensing surface to be above the inside dewpoint.
In my basement I started over, ripped everything back to the concrete, and started with 2" of rigid foam and sealed the gaps, and the rim joist with cut and cobble methods and tape.
The thing about basement walls is that it is very difficult to impossible for moisture to escape from them. So when you're constructing a basement wall, you want to do everything you can to avoid materials that will absorb water, and everything in your power to keep the water out in the first place.
The blown fiberglass will absorb water, a lot of it, so I wouldn't consider it suitable for a basement to begin with. But the deeper issue is controlling moisture, if you haven't ensured that the basement is moisture-free then adding that insulation is going to make a situation that might be bearable now much worse.
There are four ways that moisture gets into basements:
* As groundwater that comes up from below. This is avoided by having perimeter drains and possibly a sump pump.
* As rainwater that runs down the walls. This is avoided by having a waterproof rain screen that allows the water to flow down to the bottom of the wall, where it is collected and diverted by perimeter drains.
* Through capillary action as moisture wicks through the masonry. This can be avoided with a barrier.
* Through condensation, when warm humid air contacts a cool surface. In Virginia, this is going to be a huge issue. To fight it, you have to seal the walls to keep outside air out in the summer, and also seal the walls to keep interior air from contacting the cool parts of the wall. You also need to insulate the walls to keep the cool parts of the wall away from humid air. Removing humidity from the inside air -- using either AC or a dehumidifier -- also helps.
If you have not air-sealed the walls, insulating them will make condensation worse, because the cool parts of the wall will be even cooler.
So in short, I don't think this is a good idea.
> As rainwater that runs down the walls. This is avoided by having a waterproof rain screen that allows the water to flow down to the bottom of the wall, where it is collected and diverted by perimeter drains.
It's better avoided by keeping surface water at the surface. Only if that fails do you bring it down to the footing drain.
Unfortunately, I think you are right. I had hoped to hear about a wonderful spray in vapor proof insulation that could keep water vapor from reaching the concrete.
If you're contemplating new drywall, I wouldn't bury the existing drywall, I'd rip it out. That will give you a chance to inspect the studs and see if there's any moisture damage going on. You will be able to do a much better job of air sealing the wall with the studs exposed, especially at the rim joists which is a big leakage spot. You also gain a few inches of space in the room. The difference in cost is really the disposal cost of a few sheets of drywall.
Yes, she could do a much better job with the drywall removed. But it will have to await an opportunity when it is not occupied. My daughter has the same notion. So by thinking this through she has at least avoided making the concrete colder and the condensation more likely. It is unfortunate that an insulation contractor suggested blowing in the fiberglass. You would expect better advice from someone who does this every day. Thanks.
I guess you would all agree that a 2 inch layer of high density sprayed foam insulation is the surest way to keep water vapor from reaching the wall?
Closed cell spray foam does a good job at that. The problem is that when it's applied they use a chemical that is a potent greenhouse gas, so it's really bad for the environment. It's also quite expensive. If the walls are reasonably straight you can do just as well with foam board with the seams taped, at a lower monetary and environmental cost. I'd recommend either polyiso (https://www.lowes.com/pd/Johns-Manville-Common-2-in-x-4-ft-x-8-ft-Actual-2-in-x-4-ft-x-8-ft-AP-Foil-1-R-13-Faced-Polyisocyanurate-Foam-Board-Insulation/3851107 ) or EPS (https://www.lowes.com/pd/Insulfoam-Common-2-in-x-4-ft-x-8-ft-Actual-2-in-x-4-ft-x-8-ft-1-R-7-7-Faced-Polystyrene-Garage-Door-Foam-Board-Insulation/3014190?cm_mmc=shp-_-c-_-prd-_-bdm-_-google-_-lia-_-102-_-sheetinsulationandaccessories-_-3014190-_-0&placeholder=null&ds_rl=1286981&gclid=Cj0KCQiA2uH-BRCCARIsAEeef3lF7HEb7bqGgtMLBVq2UcevXBjgLd3PPPrMNYl_uhBgrRrZKlxF5HYaAuAcEALw_wcB&gclsrc=aw.ds). There is also XPS foam, which I would not recommend because it also releases harmful gases in its manufacture (https://www.lowes.com/pd/Kingspan-Insulation-Common-2-in-x-4-ft-x-8-ft-Actual-2-in-x-4-ft-x-8-ft-1-R-10-Unfaced-Polystyrene-Foam-Board-Insulation/999972968). The EPA was ready to ban XPS foam last June but the Trump administration gave a last-minute reprieve.
Polyiso has the highest r-value per inch, but it is somewhat absorbent and shouldn't be used where there is a risk of liquid water. It has a foil coating which makes it vapor proof.
If you have a seriously irregular wall -- like stacked stones -- then spray foam is pretty much the only option, short of building a straight wall in front of it.