Sanity check on unvented cathedral ceiling assembly

Climate Zone 6b – New Build
I’ve read the how to build an insulated cathedral ceiling found here:
https://www.greenbuildingadvisor.com/article/how-to-build-an-insulated-cathedral-ceiling
I’m looking for a sanity check on my design and to possibly explore a lower cost option suggested by an insulation contractor.
Using the information in the link above I set up my roof with 14” TJI rafters. The plan was to apply 5.5” of ccSPF to the underside of the roof deck in the rafter cavities. Then I was planning to fill the remained of the cavity with BIBS blown in fiberglass. No vapor barrier on the inside.
This method gives me about an R~67 in the cavity with R~34 coming from the ccSPF and R~33 from the BIBS. This gives me a ratio of almost 51% of vapor impermeable insulation to the whole cavity value.
Using inside design temp of 68F and an outside design temp 22F (average of the 3 coldest months) and 35% humidity I get the inside of my ccSPF coming in at a temperature of 45F well above the dew point of the air.
I’m very confident this will work well, however ,the ccSPF is expensive and an insulation contractor suggested using 2” of ccSPF under the roof deck then using ocSPF to get the R value I’m looking for. If I was to then spray 12” of ocSPF I’d have about R~13 from ccSPF and R~43 from ocSPF making a total R~55. This will be cheaper than my original proposal. However because the ocSPF is vapor permeable and the ccSPF is vapor impermeable I’m confused about where my first condensing surface will be?
Will my first condensing surface be the ocSPF because it is an air barrier? If so, I think this will be a workable solution. My calculations show the inside surface temperature of the ccSPF will be 33F which is below the dewpoint of the air, so if that’s my first condensing surface it wont work.
What are your thoughts on the second method and are there any other suggestions that might help me make a smarter choice in the roof insulation strategy?
Cheers
Steve
GBA Detail Library
A collection of one thousand construction details organized by climate and house part
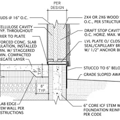
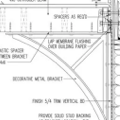
Replies
According to Figure 6 in this article: https://www.buildingscience.com/documents/building-science-insights/bsi-100-hybrid-assemblies you still need to follow the same ratios with ccSPF + ocSPF as you would with ccSPF + BIBS.
So, for climate zone 6, my understanding is that you would still need 50% of your R-value to be in the ccSPF regardless of if the layer below is ocSPF or BIBS in order to comply with the code requirements in table R806.5.
The reason your ocSPF doesn't count as "air-impermeable" insulation for code purposes is this line: "R806.5 - 4. In Climate Zones 5, 6, 7 and 8, any air-impermeable insulation shall be a class II vapor retarder"
Regardless of which way you go with the design, make sure to spec an HFO-blown ccSPF, to avoid the tremendous GHC emissions of conventional ccSPF!
But note the missing remainder of the quote: ", or shall have a Class II vapor retarder coating or covering in direct contact with the underside of the insulation." IMO, a smart-retarder like MemBrain would satisfy that without restricting inward drying. On the other hand, meeting code doesn't necessarily mean it's a good idea.
Apparently, reversing your proposed order would also meet code - ie, 12" of OCSF with 2" of CCSF (a Class II retarder) applied under it (vapor retarders belong on the warm side).
Also consider 6" of recycled EPS insulation with 2" of CCSF applied under it. Fill the remainder with fiberglass.
The upside-down assembly with the ccSPF below the ocSPF is a pretty clever idea!
Personally, I wouldn't want to be the first person to try an experimental roof assembly on an inherently challenging roof type, but it's certainly thinking outside the box!
Steve,
If you don't need the full 14" depth to support your span, you might be able to save a bit by going with cross purlins and some rigid insulation above.
Going with 11 7/8 TJI with 2x3 purlins on edge with 2.5" plyiso in-between would mean you can drop the spray foam thickness down to R20 (~3").
For lowest cost, it is best to design spray foam completely out. Go with a vented roof or unvented with exterior rigid insulation. Spray foam should be last resort.
With at 14" TJI why not vent it with a 1.5" air gap under the roof deck using the flanges of the TJI for spacers and install 12.5" of half pound open cell foam? That yields about R46 at center cavity, but would still meet IRC code-min on a U-factor basis due to have about 1/3 the thermal bridge of a milled lumber rafters.
That solution uses less polymer than 3.5" of closed cell foam, and would protect the roof deck very well, and would beat the thermal performance of a code-min R49 / 7" HFO blown foam due to the longer path through the thermally bridging web.
If a minimum R49 at center cavity is a "must", 0.7lb foam would deliver R50 @ 12.5", and still uses less polymer than 4.5" of 2lb foam.
If the ceiling is going to be finished with gypsum board, a layer of half-inch foil faced polyiso between the gypsum and the TJI/ocSPF vented solution would bring it up to code min on an R value basis with half-pound foam, if that's any cheaper.
There isn't much financial rationale to going better than code-min performance with that roof assembly. The difference in performance between an open-cell R49 and the more expensive hybrid unvented R67 using closed cell foam delivers less energy value than spending the upfront cash cost on rooftop PV solar.
Going high-R on roofs/attics only makes financial sense when the insulation is fairly cheap, such as low density cellulose on the attic floor. For cathedralized ceilings stick with code-min, or even less using an Energy Rating Index path to code compliance by improving performance on some other part of the house where it's more cost effective.
I do need the 14" TJI for structural. Thanks for your comments Dana. The problem with a vented roof assembly for me is that we have a low pitch roof 2.5/12 shed roof and longish runs from the low end to the high end. I have one run that is 42' in length and another that is 39' in length. I think my roof design moved me out of being able to effectively vent. Would you agree or is venting still possible?
I like your logic about sticking to code min but I need it to be unvented. I have to have a 14" TJI and trying to manage the condensation potential I came up with the solution I did. The logic in my home design was to be sensibly better than code in every area. With R-49 code minimum I had a target of R-60 minimum in my head for no other reason than it seemed like a good target and thought it might help with minimizing snow melt but it's not one that I have to meet, my ego will survive :)
Because I'm in a heavy snow zone I wanted to make sure I had good roof insulation and obviously more importantly air tightness to help prevent ice damming without the use of heat tape.
I have a PV system planned.
I didn't go with the exterior foam on the top of the roof deck because my builder was scared of it and told me it would cost more than going with ccSPF and BIBS.
Steve
Steve
I have no doubt that with some unknown increase in air and vapor tightness (perhaps simply open cell spray foam instead of batts), the reduced ventilation created by your long, low slope roof would still result in drier sheathing (and less ice melting) than many other successful vented and unvented roofs. If you don't have much wetting, you don't need much drying.
Very conservative is to build to unvented specs and have a vent (even a limited one).
That's right- a 2.5:12 roof is not a zero slope roof, and with the air tightness of ocSPF it won't need much venting. A gap of 1.5" is 50% more than code min, which helps a lot.
Given the low slope an interior side vapor barrier such as 4-6 mil polyethylene or a layer of 1/2" or 3/4" foil faced polyiso would keep the wetting to an absolute minimum.
Deleted
Jon,
I'm not sure how you build to unvented specs that require ccSPF directly applied to the underside of the roof deck and provide ventilation.
Steve
You set air dams against the flanges of the I-joists as Dana mentioned above to create the vent channels. Then, you spray ccSPF against the air dams, followed by the remainder of ocSPF. You still get the dewpoint management within the SPF that an unvented roof requires, but you also get ventilation above the dams just in case any heat, air or moisture gets through the SPF sandwich. Even in a lower slope shed roof, the vent channels would provide *some* additional drying and ice dam protection.
Watch your south side overhangs, though. Once you have a roof with that little heat transfer, ice dams can still be caused by solar heating of the siding warming the air that rises up and into the soffit vents.
Spraying the air dams/chutes with ccSPF is putting the low-permeance layer on the "wrong" side of the assembly. Use something fairly vapor permeable such as half-inch MDF for the air dams, put the low perm stuff (such as foil faced polyiso) on the interior side.
> how you build to unvented specs that require ccSPF directly applied
Venting on top allows one to meet both specs. Or settle for coming close to meeting both specs and ignore the "directly applied" part (which you can do since you still meet vented code specs).
Peter's approach would be drying to the inside. Dana's approach would be drying to the outside.
In Dana's suggestion I'd use MDF on the top flange of the TJI, fill the cavity with ccSPF or BIBS then 0.5" of foil faced polyiso with taped seams on the inside of the TJI. Then mount the sheetrock under the polyiso, then we have tongue and groove paneling below that on one pitch?
In Dana's approach could the polyiso be replaced with polythene sheeting class 1 air barrier?
Looking at my roof design I have one section of roof I don't think I can vent because of the slope and direction of the TJI's. It's 2 shed roofs with the pitch being 90 degrees to each other. There is a fold (valley) where the 2 roofs meet. I'll see if I can find a picture.
Steve
See attached jpg.
Yes, a valley is a problem. That makes it effectively impossible to to vent unless the gap is much deeper than the TJI flange, and vent holes can be drilled in the TJI webs to allow air to flow parallel to the beam (on both sides) at the bottom of the valley.
Valleys in low slope roofs (vented or unvented) are also TERRIBLE idea in high snow load areas. Even on higher slope roofs valleys become snow-traps.
I wanted no valleys in my roof but that's how it ended up not by my choice. The architect and a couple of builders said it would be no problem and is done all the time. That's the roof I have and so I'm stuck with it now.
Sounds like your architect designed you into a corner. It makes me mad sometimes, having a high performance building that is easy to build and attractive are not mutually exclusive options.
With the snow and low slope, your stack-up or Dana's R49 suggestion bellow is probably the best. You might be able to get something like your contractor suggest working if you top vent the sheathing but it would still be riskier than the spray foam solution.
Either way that valley will be trouble, make sure that a larger than normal area is covered by peel and stick there.
Dropping the beam that supports the valley bellow the TJIs would eliminate a big thermal bride and help with ice damming as well.
Steve,
You're right about the descriptions above. I was not necessarily endorsing the approach with the ccSPF against the air dam, but it would work as I described. For the record, my own cathedral ceilings have air channels above fluffy insulation, with foil-faced polyiso on the interior as air/vapor barrier and thermal break. It's worked fine for 20 years.
In zone 6b, you don't need a class I vapor barrier, and I would shy away from poly sheeting. Poly seems to be the worst of all worlds, easily damaged, hard to detail, trapping moisture, sweating in the "wrong" season, and such. By attaching the foil vapor barrier to a layer of insulation, polyiso seems to avoid most of those problems. In 6b you would do fine with a "smart" membrane, or even just latex vapor retarder (class III) if you've got good air channels above the fluffy and good air sealing. However, the added thermal break of an inch or more of polyiso is a big benefit without much added expense or installation difficulty. Taping the seams of the polyiso for air sealing is easy.
Your description of two intersecting shed roofs that join in a valley does sound like a roof that can't be vented, if it is a cathedral ceiling. That one would have to be treated as an unvented roof.
Another consideration is that metal roofs are not as impermeable as often thought. Use a permeable underlayment+mesh and you are likely to have some upward drying through it. Even .3 perms is significant when there is only .05 perms of diffusion wetting and no air leakage from the interior.
Note that wind and thermal and barometric cycling will increase these figures (probably very significantly):
https://web.ornl.gov/sci/buildings/conf-archive/2013%20B12%20papers/171-Pinon.pdf
So back to the original question knowing that venting this particular roof pitch is not on the agenda. Is there a better way to set up my roof insulation in an unvented roof instead of 5.5" ccSPF and 8.5" of BIBS or ocSPF?
My insulation contractor recommended fiberglass BIBS in the full 14" TJI cavity then using a smart membrane on the inside. Looking at the 2015 IRC code I didn't think this was legal and besides advice here steered me away from that option.
Steve
Cost-wise it's be cheaper to do a code-min R49 with 4" of HFO blown ccSPF (R27-R28, installable in a single pass), followed by 5.5"- 6 " of half-pound open cell foam (R20-22-ish, installable in a single pass) to hit the code-min R49 with plenty of dew point margin at the opencell/close cell boundary. Don't even bother filling the remaining 4"- use it as your electrical chase. The 6" of open cell foam will cost about the same as the foregone 1.5" of HFO blown foam (going from 5.5" HFO blown ccSPF down to only 4"). The total combined polymer use would be the same as 5.5" of 2lb foam.
Take the cost savings from that and apply it elsewhere. The difference in energy use would be more than covered by spending that money on an expanded PV array, but there may be even better bang/buck elsewhere in the design.
Is the beam supporting the valley another TJI? From a snow-load/ice dam potential point of view that beam has the potential to cause the lower half of the valley to fill with ice at times if there isn't an adequate thermal break. (Another advantage to putting continuous foam above the roof deck.)
Dana,
Thanks for the R-49 thoughts. I like your approach on that. I just thought the roof would be the best place to spend money on insulation because heat rises and I thought apart from windows most of the heat would be out the roof.
Good thoughts on the thermal bridge created with that beam. The beam is actually a steel wide flanged I beam 12.5" tall x 6.5" wide. The TJI's are hung off of it like the detail attached. This is a huge thermal bridge that I need to address and had overlooked until now.
The only way I can see to address this bridge is on the inside with rigid foam between the I beam and the drywall. Any suggestions very much appreciated.
Yeah, the steel beam is even worse than wood. You could make a wide, flat valley by placing 3"-4" of rigid foam on top of the wood nailer over the beam. Valleys don't have to come to a point.
You could use successive layers of 1" foam, with each layer getting wider and the gaps filled with canned foam. Then a wide pan flashing to line the whole valley, extending a foot or two up the sloped roofs.
Peter,
I think this is what you are proposing? The drawing doesn't show the plan flashing. I put it to my engineer, architect and builder to get their responses.
Since you are going to have to be trimming out that I beam on the interior, why not just drop it completely bellow the TJI? This would eliminate any thermal bridging.
Also check with your engineer, you might be able to get away with less than a W12, I think the W12 was speced to match your 14" TJI.
Also does the I beam poke through to the exterior? If it does, it needs to insulated on the outside as well otherwise it will sweat in the winter. If you this is difficult, you might be able to fasten some 2x12 extensions to the I beam web to support your roof overhangs and keep the steel inside.
Yes the beam goes all the way out to support the eves. Is the sweating process you are talking about considering the outside portion getting cold and conducting heat away from the inside portion. Now the inside portion will be close to the condensation temperature of the inside air?
This is getting difficult to find a good fix for. I'll have to talk to me engineer about extensions to keep the steel inside.
Steve
Yup, that is pretty much the problem with structural steel through the walls.
Another option might be to keep everything as is and fully encapsulate the I beam including the bottom flange with say 4" to 5" of CC spray foam. This would put the beam outside your thermal envelope and would solve both problems.
This is a reply/question to post #10....
How low slope can you go with this type of venting? 1.5:12? in climate zone 5
Sorry about the hijack, Steve....
Dana - What about 12" I joists, plywood roof deck on the I-joists, 1-1/2" air space, 1/2" MDF (? air sealed?), 10" BIBS (or would ocSPF be better, 1" foil faced polyiso (air sealed), 2x4's on the flat for an electric chase, then 1/2" gypsum board? I don't think this gets to R49 but I'm in Michigan so I think it''ll be code (R38 for the roof?)
Steve - what are you planning to clad your roof with? I'm I'm planning on having standing seam metal roof - ice and water shield on the whole deck. Our current insulation plan is similar to yours - ccSPF (~ 4") under the roof deck than BIBS. It would sandwich the sheathing between 2 impermeable layers. Makes me wonder why I can't put 1-2" of foam board above the deck and less ccSPF beneath it.... seems to me that the sheathing is sandwiched either way.
We are trying to limit the thickness of the roof for esthetic reasons - 12" looks thick to us already....
https://www.greenbuildingadvisor.com/article/sandwiching-roof-sheathing-two-impermeable-layers
Alan,
I'm using 30 year shingles. I do plan ice and water shield on the whole deck. Putting foam on the outside was ruled out by my builder early on. I'd need at least 6 inches on the outside for our climate and that was going to problematic with attaching solar panels and would make the fascia very thick. He also told me it would be much more expensive than going the approach I proposed in the original post.
I'm interested in GBA experts opinion of a hybrid approach like you state with foam on the outside AND ccSPF on the inside. It's almost like the valley detail I'm looking at proposed by Peter Engle above.
Steve
I wish we could get off the spray foam solution to so many roofs. Open cell or HFO blown closed cell may be greener than the usual ccsf, but it's still petroleum based plastic and hardly green. And what's with a builder refusing to install exterior foam, which is widely available recycled?
Rant over.
Dana,
I had always thought that going with code minimum was like getting a C- in school. We should strive for better than code. The plan for my house was to be better than code by some financially viable logical margin in all areas.
My original thinking was that the roof would be one of the spots I should try to get a bigger margin to the code with the thought that heat rises, the stack effect, radiant heat loss, the ice damming issue. I thought that spending more money of the roof made sense. It seems you disagree. I'd like to understand the logic in targeting the code minimum roof?
Steve
>"I had always thought that going with code minimum was like getting a C- in school. We should strive for better than code. The plan for my house was to be better than code by some financially viable logical margin in all areas.
My original thinking was that the roof would be one of the spots I should try to get a bigger margin to the code with the thought that heat rises, the stack effect, radiant heat loss, the ice damming issue. I thought that spending more money of the roof made sense. It seems you disagree. I'd like to understand the logic in targeting the code minimum roof?"
--------------------------------
Sure code-min is like a C-, but if you have to ask your mom for another $200K to pay a tutor under the table to fix a screw-up on part of the test is it "worth it", as long as you ace the rest of the package?
Code minimums were based on what is cost effective on a typical assembly. For roofs that means a vented attic with cheap open blown or batt insulation. An un-ventable low angle cathedralized ceiling where hitting R49 would cost 10x that of open blown fiber on the attic floor is not the "typical" the code developers had in mind. The high expense of even getting code-min on prescriptive R-value basis is often nonsensical. At some roof performance level the additional cost of raising it to code on a prescriptive U-factor or R-value basis stops making sense whenever improving the rest of the building envelope to offset the additional energy use of a "sub code" roof is cheaper.
Section R405 of the IRC even allows using energy use simulation tools as a path to compliance, precisely for those reasons. There are plenty of R38 (center cavity-R) roofs on "better than code" houses that got there on whole house performance basis.
https://codes.iccsafe.org/content/iecc2018/chapter-4-re-residential-energy-efficiency
Heat doesn't rise, hot air does. But with an air tight roof assembly stack effect pressures don't matter. But the ice damming issue DOES matter, which is why it's worth getting rid of the valley, or at least the steel I-beam, and going for at least code-min on a U-factor basis.
The steel I-beam at the valley is worth designing-out. Seriously- I'd grade that a thermal & moisture/ice management F! A gluelam beam of similar capacity would have orders of magnitude lower thermal conductivity, and would STILL be too much of a thermal bridge for managing ice formation in a valley.
If you're keeping it steel, a continuous 7" of roofing polyiso (R40 labeled, R35 derated for temperature) above the structural roof deck gets you to beyond code-min on a U-factor basis (=U0.026 max, which is R38.5 "whole assembly") with a useful level of thermal break over the steel, and enough dew point control to allow you to install 14" of cellulose or 1.0 lb density fiberglass (not dense-pack) the cavities for R52 in the cavities, and a whopping R90 at center cavity. That's pretty expensive. Going with R20 open cell foam under the roof deck would be an R60-ish roof, but going less than that on the above roof deck foam is a problem- that steel looks like an ice dam disaster.
Actually, just the valley roof on it's own is would be D grade for roof design in a high snow load region. Any chance it can be converted to a ridge/hip? A ridge on a low angle roof may develop thick pillows of windslab on the leeward side during in a windy snowstorm storm, but it doesn't trap snow. A thermal bridge on ridge beam doesn't produce much water/ice for re-freezing, since wind scrubs it thinner than elsewhere, even an a relatively low pitched roof. If converting from a valley to a hip it's still worth designing out the steel, but going for an unvented 4" polyiso above the roof deck (R23 labeled, R20 derated for temp) and 8" of open cell foam (R30) on the underside of the roof deck would beat code min on a U-factor basis (due to the thermal break over the ridge beam & rafters) despite being roughly code-min on an R value basis.
That's still a heluva lot more expensive than 15" of fluffage on the attic floor, and you may still get better bang/buck going lower than code-R on the roof, spending that money on other upgrades, earning your "B" for "Better than code" on a performance basis rather assembly-by-assembly on a prescriptive R / U-factor basis.
[edited to add]
I apologize for not re-reading the original post- I was thinking zone 5B, not 6B.
Any under-the roof deck insulation should not exceed the derated R of the polyiso above the roof deck. So in the valley configuration with the steel I-beam and 7" of exterior polyiso the cavity fill needs to be less than R35 to have sufficient dew point control. Going with 8" of open cell foam, 8" damp sprayed 1lb Spider or cellulose would be about it, but that would still be an R65-R70 nominal roof. If converting the valley to a hip with a steel or glue-lam beam 6" of exterior polyiso (R34 labeled, R30 derated) and 7" of open cell on the interior would do it.
Steve,
I was away fro the weekend, but yes, the drawing you posted was what I described. I also like Akos' suggestion of dropping the beam below the I-joists and using wood lookouts to support the eaves, thus bringing the entire steel beam inside the thermal envelope.
I'm sure Dana can further explain his reasoning above, but it seems that it's a simple financial comparison. SPF is expensive and solar PV is getting cheaper. At some point, adding local PV energy generation is cheaper than more insulation, with the same reduction in source energy intensity.
Peter,
I'm not sure I like this from an interior aesthetics view point. That would require either and exposed I beam in the livingroom or the beam to be fully enclosed with drywall. That fold in the interior ceiling is to be a feature where we have ceiling tongue and groove wood joining there creating an aesthetic view. Note I have planned to have mudded and taped drywall between the tongue and groove and TJI's as my air control layer.
I like Akos's idea above of encapsulating the I beam in foam keeping the I beam on the outside of my thermal envelope. I think I'd be able to encapsulate all sides of the I beam except the top flange where the wood nailer and hangers are attached. Now the problem becomes how do I attached the sheet rock to the underside of the I beam when we have 3" of foam around the I beam. I might have to fur down the TJI's to line up.
Steve
You can lag 2x lumber to the I beam web and go with slopeable face mount hangers. That would eliminate the top nailer and buy you an extra 3".
3" of ccSPF is about an R20 thermal break. From an ice accumulation /damming point of view in a roof valley design it calls for something like twice that (or maybe even 3x.) See the discussion in response #36.
See also (particularly but not exclusively the footnotes):
https://www.buildingscience.com/documents/insights/bsi-063-over-roofing
That house in a zone 5A location with a relatively high snow load, but also a much steeper roof which allows the valleys to empty a bit with the aid of gravity.
Dana (Post #36 & #37) and everyone else, thanks for your great feedback. The plan was always to build a "pretty good" home. As such I've been trying not to sweat some of the things my architect, engineer and myself got wrong but this seems like a big one.
We have steel all over our house in outside walls. He have 2 steel moment frames, a steel lattice support column and this steel valley beam which has 2 additional wings that go out from the valley beam. Each one of these beams is supported by a steel column. See pic (missing one of the moment frames). At the time of reviewing the plans I had no idea steel would be such an issue.
Taking the steel out is too late. It's already fabricated. Changing the valley to a hip is too late. The house is 80% framed. It would be a huge change that would require major change to deck overhangs and water drainage paths, re-engineering and re-submission to the county for approval.
With respect to the ice damming in the valley, I can fix that. I can put in a line of heat tape up the valley to take care of the damming. Okay so it's not the heat tapeless house I wanted but it's a fix that will work for the damming.
What I'm concerned about is the dew point control and potential of future hidden water damage. Dana is suggesting 7" of exterior foam but I think I'd have to apply that over the whole roof area. I know there are many houses in my area that use steel in exterior walls and roofs. Most are typical old school code minimum houses. Are they just lucky that there is no water damage from dew point control or is there an approach that I am missing?
The original proposal from my general and insulation sub contractor was to fill the 14" TJI cavity with BIBS and then use a smart MemBrain on the interior. That's the strategy they have used in other similar un-vented roofs.
Dana's link in post #37 implies that even in areas without the steel I'll still get significant thermal bridging from the TGI's so I'll for ever have icing and water damage issues from here forward.
Is the only way to fix this by using 7" of polyiso on the exterior across the whole roof? I'm pretty gutted at what this means and all the other problems it will create such as how to ensure structural rigidity to mount my solar panels and how to finish the fascia as I have little room for further overhangs due to my lot setback requirements.
Steve
Heating portions of a roof to stop ice dams sounds bad - until you run the numbers.
Ice dams only occur in some weather on small portions of the roof (eg, the cold eaves). Even then, it doesn't take much to heat the upper surface of the eave to a temperature greater than the roof above it. About the same btu/sqft as is coming through the roof from the interior (a very small amount as long as you have reasonable insulation). The yearly heat needed to prevent ice dams with well designed electrical heating is in the noise. And it fully addresses the problem. No idea why so many are focused only on passive insulation/venting that still results in colder eaves and some re-freezing on them.
Regarding thermal bridging - they key is to get some insulation in place. Something like R10 over very small areas doesn't create much heat loss.
Steve,
There is nothing wrong with building with steel provided it is insulated.
My home has two large steel beams to support a balcony, they just had to be insulated properly.
In your case, the 3" of spray foam over the beam is not enough especially since it is in a valley. All you have to do is bump that up to 5". There are many ways of hiding that in the interior depending on how you want to finish the ceiling.
For the rest of the structural steel in the walls, it is always best to insulate on the outside of it, depending on the thickness of steel you will probably loose about 1/2 the R value of the fluffy insulation in the wall near it, this is why exterior insulation is your friend.
For your ice dam issue, it might help to strap out the roof deck and top vent it. This way you can run channels across the valley in the roof all the way from the bottom to the higher part.
Even though you have a low slope roof, there is still a pretty big height difference and stack effect will kick in. A bit of venting will help with moving any warm air out from underneath the snow. This should help in keeping roof icing to a minimum.
>"Dana's link in post #37 implies that even in areas without the steel I'll still get significant thermal bridging from the TGI's so I'll for ever have icing and water damage issues from here forward."
The thermal conductivity of carbon steel at temperatures that matter is between 20-30 Btu ft / (h ft2 oF), the thermal conductivity of OSB runs about 0.085 - 0.09 Btu ft / (h ft2 oF). That's means there is about a 250- 300x more heat moving through a steel I-beam web than through a TJI web of equal thickness & depth.
Put another way, the thermal bridging of a TJI is under 1% of the thermal bridge of a steel I-beam. So while you might still see some ice striping at the TJI it's not going to build a glacier the way the steel I-beam does.
>"Is the only way to fix this by using 7" of polyiso on the exterior across the whole roof? "
A heat tape is a band-aid. Insulating between the steel and the great outdoors is the right thing to do, even if it's not the full 7".
At just 4" of polyiso you'd have a derated R20, which makes a BIG difference, but that would limit you to R20 under the roof deck (say, 5.5" of open cell foam) to have sufficient dew point control at the roof deck from interior moisture drives, so you're "only" a R40 center cavity. But with an R20-ish thermal break over all the structural good it's not particularly a problem for hitting or beating code on a whole house basis if you're doing the walls and windows better than code, and it might even make code-min (barely) on a U-factor basis.
Going much lower than R20 for the thermal break would be pushing your luck- it really depends on just how much snow load you need to manage. Three feet of snow has a real R value, three inches not so much. With the valley the deepest snow is likely to be at the valley, deeper than what would accumulate on a dead-flat roof. How much snow builds up on flat roofs in your area?
I've had more than 6 feet in the valleys on my roof at times after successive nor' easters, and I have something like a 6:12 pitch. But I also get sticker denser maritime snow than you're likely to get in zone 6B- it's not apples to apples when it's 15-20% H2O snow vs. 6-10% H2O snow. (Yes, I have to shovel the snow off the roof sometimes, but not every year.)
Dana,
This was one of the hardest winters we've had in 20 years. You could drive up my street and see the roofs on homes that are air tight compared to the homes with leaky roofs and ice dams and icicles everywhere. It was very telling. There is a full on passive house down the street from me that easily had 2.5 feet of snow all winter long on his roof and only the tiniest of icicles along the drip edge. That was this year, some years the snow can only be a couple of inches. I wouldn't like to bank on an X depth of snow for its insulating properties.
If I do the 4" or more of valley insulation then under the deck in the those areas I use ccSPF I'm essentially not allowing the roof sheathing to dry in any direction. However I planned to use an Ice and Water shield across the whole roof deck so the sheathing wouldn't be able to dry in any direction anyway. Is this okay? Nobody ever answered Alan Afsar's similar question in post #25 above.
Looking at the link Alan posted it seems that the general consensus is that the roof decking doesn't need to dry out but it is advisable to do so if possible. Maybe this is the lesser of two evils for me.
Steve
>"If I do the 4" or more of valley insulation then under the deck in the those areas I use ccSPF I'm essentially not allowing the roof sheathing to dry in any direction. However I planned to use an Ice and Water shield across the whole roof deck so the sheathing wouldn't be able to dry in any direction anyway."
I was recommending 5.5" of open cell foam on the under side rather than closed cell foam, which allows it to dry toward the interior. But at 4" of closed cell (R24 - R28-ish) the roof deck can still dry (extremely slowly) toward the interior. Most 2lb foam would still be in the 0.2-0.3 perm range, the low end of Class-II vapor retardency, not a true vapor retarder. At 5.5" most half-pound open cell foam is in the 6-7 perm range, an order of magnitude more vapor open than 4" of closed cell.
The Ice & Water Shield is less than 0.05 perms, so it really is getting on to an order of magnitude tighter than 4" of closed cell foam.
Steve, my situation is like yours (I think) - figuring out insulation details too late in the process... What's clear to me is that I needed to be on this site and reading articles on the Building Science Corporation's website prior to designing our house... or finding an architect and builder who know all this information already.
Fortunately, I do have an architect and builder who are interested in working with us to get it air sealed and insulated well.
Alan,
I've been on here reading and learning for well over a year. My general contractor, architect and engineer were all onboard and keen to do an air tight pretty good home before I awarded them contracts. The reality is nobody did anything different than they had always done. I kept having to guide them from my reading of several green building books, Fine Home Building, this site and friends who have completed "pretty good" homes.
My general is very easy to work with and he is willing to go the extra mile in air sealing but the subs attention to detail is in question and my generals ability to identify and seal holes will become evident when we do our blower door test.
There are a few things I missed being a rookie in this crazy house building business. I totally spaced on the steel being such a huge thermal bridge.
Going back to your original post, you stated...."Using inside design temp of 68F and an outside design temp 22F (average of the 3 coldest months) and 35% humidity I get the inside of my ccSPF coming in at a temperature of 45F well above the dew point of the air."
I've been waiting for someone else to raise the point, but no one has, so I will ask the community. Isn't it a mistake to use an average of the coldest months as the design temperature in order to calculate the dew point. Shouldn't the dew point be calculated at the coldest temperature, or at least the average of not more than a couple of days of the coldest temperature? If there's several days of extremely cold temperatures, the inside of your CCSPF is going to be colder than 45 degrees.
Hugh,
Thank you for asking this question. It was one I asked myself about 18 months ago when I started my dew point analysis. I started off using the 99% cold day but I found this article on GBA that said I should use the average of the three coldest months.
In a few comments to my past posts Jon R has been challenging me on that decision (with some great references) and now I'm wondering if I should increase my margins in the wall and roof and use the 99% cold day as well as use an interior class II vapor retarder (but that's a post for another day). Here is one of Jon's links, reference table 8:
https://www.buildingscience.com/sites/default/files/migrate/pdf/BA-1316_Moisture_Management_for%20High_R-Value_Walls_rev.pdf
I'd be interested in what others here have to say about my dew point numbers. One saving grace is Utah is a very dry climate so things can dry out quickly. That all assumes you have permeability in the direction you are trying to dry. Another reason I'm questioning using foil faced polyiso on my exterior wall.
Here is the GBA link and relevant text:
https://www.greenbuildingadvisor.com/article/are-dew-point-calculations-really-necessary
While some builders perform dew-point calculations for the coldest day of the year — that is, the design heating temperature — ASHRAE has developed a simplified calculation method based on a temperature that isn’t quite so low. (Details can be found in ASHRAE Fundamentals, chapter 27.) According to building scientist Joe Lstiburek, calculating the dew point for the coldest day of the year isn’t particularly useful, since a small amount of condensation for a few hours during the winter won’t lead to any problems. (The condensation just dries out when the weather warms up.)
So if you know where to look up the monthly mean temperatures for December, January, and February for the location where you are building — data are available for many locations at the Web site of the National Oceanic and Atmospheric Association (NOAA) — you can calculate the winter temperature to use for your dew-point calculation.
Steve
> Shouldn't the dew point be calculated at the coldest temperature?
It depends on your goal. Prevent *all* condensation/sorption at that point in the wall or prevent enough that it usually doesn't cause a problem?
Part of the problem is that some authors have created confusion by using "dew point" when they are talking about a much higher "nominal dew point" based on averages.