Air Sealing and Insulating Attic With Plaster-and-Lathe Ceiling
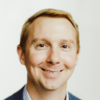
1. How much effort should go into air sealing? The contractor quoted ~$200 for this line item, which seemed surprisingly low given how much effort is described here (https://www.greenbuildingadvisor.com/article/air-sealing-an-attic).
2. Should I be concerned about the added weight of the insulation and catwalk on the ceiling? (I saw several posts about this, but they didn’t address plaster & lathe. (https://www.greenbuildingadvisor.com/article/will-thick-cellulose-cause-your-ceiling-to-sag)
3. I understand plaster is a poor vapor barrier. Would it be beneficial to spray foam (open or closed cell) the bottom 2-3″ to create a better seal? (I saw this post: https://www.greenbuildingadvisor.com/question/closed-cell-foam-on-attic-floor, but it also didn’t address plaster) Would that add strength to the ceiling and help allay my concerns about weight?
4. Are there any other best practices, pitfalls, or things I should think about to make sure the house gets the best possible result?
Thanks!
GBA Detail Library
A collection of one thousand construction details organized by climate and house part
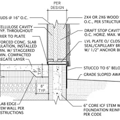
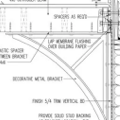
Replies
Thomas,
1. That seems low to me as well. I'd want the contractor to detail out what his quote includes.
2. No clue. Maybe you should have an electrician move the breaker panel so it is easier to access.
3. I think the spray foam would be wasted if you plan to keep a ventilated attic. I'm also wondering why you want to remove the existing fiberglass. Is it contaminated? If it is in good condition, you could leave it in place and get away with installing less cellulose.
4. From everything I've read, you want to complete your attic air sealing before increasing insulation. It is also helpful to have someone do a before/after blower door test. That will help you to identify leaks and also evaluate the effectiveness of your efforts.
Hi Steve,
Thanks very much for the reply.
1. Thanks for the confirmation.
2. Good idea about moving the breaker - I'll do that. That will make it easier to access, as well as remove the need for a catwalk. If I ever need to reach the other side of the attic, I imagine I could just put some plywood or foam boards on top of the cellulose and walk on them without compacting it too much?
3. My thinking with removing the old fiberglass is that cellulose will do a better job of reducing air leakage. My worry is that even after air sealing penetrations, the plaster & lathe ceiling will let a lot of air through to the attic.
4. Good idea on the blower door test, thanks!
Best,
Thomas
1- a lot of effort. To really do a thorough job, you’ll probably need to remove at least some of the existing insulation. You have to seal every penetration (wires, pipes, anything), and all areas with multiple structural members coming together that have any gaps — including gaps between things like sistered boards — that connect the attic air space with the stud cavities of any walls. $200 sounds low to me, and probably just gets some canned foam in obvious holes. You really want more than that.
2- insulation, generally no. Plaster and lathe is usually pretty strong, but brittle if you try to cut it. Blown insulation on top shouldn’t be a problem. The catwalk MIGHT be a problem. Try to tie the catwalk into the structure so that it doesn’t stress any of the ceiling, including midspan areas of rafters. You don’t want to worry about cracking.
3- you don’t need a vapor barrier on a ceiling that is also the floor of a VENTED attic. I wouldn’t waste any spray foam here.
4- make sure you put in some baffles out the eaves before putting in blown insulation, especially if you plan to add some soffit vents. Soffit vents will work much better in combination with ridge vents than gable vents will. I would seriously consider blocking the gable vents and adding soffit vents as part of this project to maximize the venting you get with the ridge vent.
I would move that electrical subpanel into an interior wall. This is probably not terribly nice difficult to do. Replace the subpanel with a large junction box sufficient to make all the connections. This probably means at least a 12x12x4 box. Any commercial electrical supply house will have these, don’t limit yourself to only what the box stores have. Get a new flush mount panel to mount in a convenient studwall cavity. They make panels sized specifically to mount this way. Run new wiring from the junction box to the new panel to make all the connections. This could end up being less work than building a catwalk, and it will make any future work with that panel much easier.
Your home is of the right vintage for two concerns: knob and tube wiring, which can’t be buried in insulation, and type R insulation, which gets brittle with time and can be damaged if moved (and also if it gets wet). I’d replace any of either that you find while doing the rest of this project.
I’d add some lights in your attic controlled from a switch near the access hatch too if you don’t already have them. If you have pull chain light sockets, wire them into a switch by the hatch. It’s so much nicer to open the hatch, flip a switch, and be able to see than to stumble around in the dark looking for the next pullstring. I’ve done this in my crawlspace too.
Bill
Hello Thomas. I'm in the process of addressing a similar situation. 1914 build in MA zone 5. Unconditioned attic with unvented eaves + ridge and gable vents. Plaster and lath ceiling below the attic, minimal loose insulation on the attic floor. I will be leaving this attic as unconditioned space to be filled with 15" blown cellulose, thorough air sealing, adding a catwalk, and a well insulated access hatch.
1. I've learned from Building Science Corp and others that priority order of my structure control layers are water, air, vapor, and thermal. The first two being especially critical. I would spend the $$$ on a thorough air sealing of your ceiling. Which means the exiting insulation at least needs to be moved to do that. But first ...
2. What is the condition of your 100 year old plaster ceiling? In my case, the lathe was coming loose from the joists, the plaster badly cracked, etc. We decided to take it down and replace. In other areas of the house, new wallboard was installed directly over the old plaster and lathe.
3. Not sure yet what we will do for the ceiling vapor barrier. Maybe Membrain or vapor barrier paint.
4. Advice? I had an IR scan done of the premises which was very useful to confirm that I had essentially no insulation installed. I will likely do a blower door just before the walls are closed.
If you have a plaster and lath ceiling, it's probable there's at least one or two layers of oil based paint and/or primer, which is a class II vapor retarder. If you are concerned about vapor diffusion.
Hi all,
Thanks very much for the additional advice. In case you're interested, I've attached a photo of the attic as it stands now with the electrical work done.
1 [Air Sealing]. I've had another conversation with the contractor about air sealing. As suspected, that was only for sealing the major penetrations. The contractor suggested that spray foaming the floor would probably cost less than doing a robust manual air sealing job (labor is fairly expensive in my area).
This is the only real major decision remaining for the project, so I'd appreciate any perspectives about tradeoffs between sprayfoaming or more traditional air sealing. I've seen these two articles that seem to suggest spray foam is a good idea, just potentially more expensive:
https://www.structuretech.com/blog/covid-19-and-home-inspections
https://www.greenbuildingadvisor.com/question/closed-cell-foam-on-attic-floor
2 [Weight]. Thanks for the confirmation that plaster can hold the weight of additional insulation. With the sub-panel now next to the attic hatch, it should be easy to access with no need for a catwalk. However, there is an existing storage platform that is situated over several internal walls, so should be quite well supported. I don't plan to use it for storage, but might raise a small section of it using these: https://www.loftzone.com to have an easy place to stand.
@WoobaGooba: Good question about the condition of the plaster. From the house side, it seems to be in reasonably good shape. If you have any suggested articles that show what to look for on the attic side, I'd appreciate it.
3 [Vapor barrier]. Thanks Bryan and Zephyr7 for the advice on vapor diffusion.
4 [Other advice].
- Baffles: Good suggestion - I've thought about soffit vents before; I'm not ready to do it now, but will install 2" baffles like these: https://dciproducts.com/smartbaffle for when I do add them in the future.
- Attic lights: Good idea, thanks! You can see them installed in the photo, along with a convenient switch by the sub-panel.
-IR Scan / Blower Door: Great idea. I had a blower door done a few years ago, but would be curious to see a before & after.
-I'm also thinking about the attic stairs. I want to keep them (vs. replacing with a hatch), as it will be easier to access the sub-panel, and cheaper. This FHB artcile (https://www.finehomebuilding.com/2014/01/08/insulating-attic-stairs) recommends a nice looking pre-made solution: http://essnrg.com/the-energy-guardian-pull-down-ladder-cover.
Best,
Thomas
Evaluating condition of the plaster and lathe ceiling. From below, sight along the plane of the ceiling with a bright light. Any obvious sags or cracks? Probe several areas of the ceiling by pressing with your hand, any movement? From above, can you see the lathe separating from the joists? Depending on the condition, repair could run from spot refastening, go over it with new wallboard, drop and replace.
The worst of my sub attic rooms had both the ceiling joists bowing, substantial cracking, and lathe coming loose. We dropped the entire ceiling and installed a "strong back" above to pull the joists back into position. See pic. The catwalk will also rest on that.
We are somewhat spoiled in my area as Mass Save often provides substantial discount for air sealing and blown cellulose.
Any issues with rodent "presents" in the existing insulation? I have in the past removed insulation because of that. Its not cheap, IIRC $2K-ish for 25 x 45 attic. But Mass Save covered 75% of the new blown cellulose. Check with your local energy providers re: any energy rebate programs.
Ditto Zephyr's knob and tube comments.
Simpson makes some nice joist hangers that will work better and also are often easier to install than wood stubs when tying in a strongback like that. Something to think about for next time :-)
Bill
Im going to assume that black duct shaking around is for a bathroom exhaust fan. Try to replace as much of that run as you can with rigid ducting which will get you much better performance from your fan. Flex duct is easy to install, but the trade off is lots more back pressure and less airflow from fans (or HVAC ducts) as a result.
Bill