Concrete Floor Finish

Hello All,
Designing a slab-on-grade residential house in Idaho. Are plan is to use the concrete slab, with a 600 or so polish, as the finished floor. I found some info. a concrete finish standards.
Gloss – Level 2 (400-grit resin bond, producing a low-sheen finish
Aggregate Exposure – Class A (Class A is defined as 85 – 95% Cement Fines and 5 – 15% Fine Aggregate).
I am thinking this should be noted on the foundation/slab page of the construction docs and also in the sub’s contract.
Any thoughts, helpful suggestions appreciated.
Thanks.
GBA Detail Library
A collection of one thousand construction details organized by climate and house part
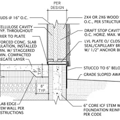
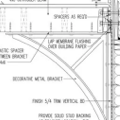
Replies
Idahobuild,
It depends on what look you want. The Smooth is one up from what a well power-troweled slab looks like. The Aggregate Exposure is much like traditional Terrazo.
Hey Malcolm,
I guess I am mostly looking for a way to make the concrete as easy as possible for the finish/polishing guys to get the desired finish by reducing the work needed to 'fix' the work of other subs. To that end I was looking for a way to tell the foundation sub that the completed work shall be completed to some level without the implication that they should do the polishing. Does that make sense?
I don't know of well-understood, universal standards for concrete finishing; I think it might be more effective to share a few images, some showing what you want and, importantly, of some showing what you don't want.
If there are well-understood, universal standards, I would like to know what they are so I can include them in my specifications.
Seems like the foundation sub and the finisher need to be the same company or at least work as a team.
Walta
There are a couple standards when it comes to polished concrete and concrete in general. For concrete in general, Floor Flatness FF and Floor Levelness FL numbers are used to denote the requirements. I would think this isn't very critical for a residential project as long as it isn't terrible and I doubt anyone measures in residential. I think you just want a good finisher so the flatness is conducive to easier and more even polishing. (https://www.concretenetwork.com/industrial-floors/flatness.html)
For polished concrete specifications, there are two main things to specify - class of aggregate exposure: A-D (how much will be ground away) and level of sheen: 1-4 (what the final grit and polishing steps will be). Generally, the more aggregate exposure and the higher sheen levels will involve more work/cost.
(https://www.concretenetwork.com/concrete/polishing/levels.html)
Things to potentially watch out for: Fiber in the concrete mix (some types can be polished where others will fuzz), do you want specific aggregate colors for exposure, control/expansion joint treatment, planning all your sub-slab work as patches will show, wall protection/finish as it is wet and messy work, specification of densifier/hardener, protection of concrete before polishing as the polishing won't remove stains, protection of concrete after polishing with some sort of sealer, and probably a few others I am not thinking of.
Helpful details aaron_p. I found the Aggregate and Gloss info. earlier but hadn't seen/heard of the FL/FF specs/guidelines. I'll definitely look into the FF/FL link that you've provided. I would agree with walta100 in that the two jobs should be done by the same sub, or at least work closely, unfortunately I 1) don't know that I'll be able to find a foundation sub that has staff for the polishing bit of the job and 2) though I can guide a cooperative environment for those chosen to complete the work; I'd prefer to provide a minimum direction/specification and then let the 'cooperation' improve the final product from there.
Aside from applying a FF/FL spec. would it be helpful to also specify the "fiber additives are NOT to be used"?
Early in the project, I was considering expansion joints in the field of the slab, however, there will be in-slab radiant heat and I don't know that I would feel safe having the saw run across the floor. I think that I've settled on just calling the inevitable cracks in the conc. "character marks" and saving myself some grief. I'll seal the cracks, as they occur, with a quality sealant.
I've taken notes to discuss densifiers and hardeners with the polish sub.
I'm not an expert on the types of fiber mesh, but my understanding is some newer microfiber types are better for polishing. (https://www.concreteconstruction.net/how-to/fibers-in-polished-concrete_o) I think the fiber mesh may be able to reduce some of the cracking that occurs in slabs and seems to be easier to work with than welded wire mesh. It seems to be hard to walk on the welded wire mesh and keep it in the center of the slab where it is most beneficial. Rebar with larger spacing between the bars also seems easier to work/step around. Since you are doing a layout without control joints (which seems like the right call to me) I would explore working with the concrete sub to find the right fiber mesh. Also, I would recommend having them pour a little extra slab somewhere with the same concrete for polishing/grinding testing - or sometimes we have them do a mock-up in place somewhere that will get covered up with a floor finish later.
"I am thinking this should be noted on the foundation/slab page of the construction docs and also in the sub’s contract."
You definitely want it all over the drawings. In fact, I recommend a pre-construction meeting with your general and whoever is doing the concrete and finishing work, which should be the same sub-contractor. Make sure they spell out how they plan to protect the finished concrete during the remainder of the construction work.
And of course, anything that is not in writing doesn't exist. So ... an agenda for the meeting, with follow up minutes approved by all participants afterwards.