Questioning the Quality of Framing Lumber

MikeTXMS
| Posted in General Questions on
Hi, y’all.
I’m pretty new in the USA and don’t know what is normal, what isn’t here.
I signed contract with some builder in TX, to build home foe me and my kids.
Now we’re on the framing step.
Unfortunatly, I see some 3 strange types of damage and I’m not sure should I hire some inspector for this. May I ask you for arvise and for your ideas about damage?
How it works in the USA and is these parts normal?
Thank you very much for you help
GBA Detail Library
A collection of one thousand construction details organized by climate and house part
Search and download construction details
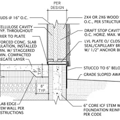
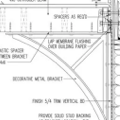
Replies
also some parts have these damage
Mike,
Based on the photos I'd say:
#1 and #4 show incidental mold. I wouldn't worry about it.
#2 and #5 look like boards with a wane edge. They still probably grade as #2 or better - that is acceptable for framing - but not perhaps what you would choose if you were high-grading at the lumberyard yourself.
#3 worries me a bit. It looks rotten.
If it were me I'd talk to your contractor about your concerns. I don't see anything in the photos that would make me get an inspector involved unless there is a lot more of #3 type wood used.
Malcolm, thank you very much.
May I ask you about boards after "bark beetle insects"? Can they be used for framing in USA? In my native country it isn't allowed. So I'm a little bit concerned about this.
Also I have some parts like this(on new photo). I read a lot of information about insects in houses, so a little bit scared. :)
MikeTXMS,
I will have to part ways with Malcolm on the buggy wood. Beetle kill to my experience does not hollow out galleries in the main part of the tree, but instead galleries out the layer just beneath the bark, which kills the tree by cutting off food and water transport. Even the lumber I have received with the large grub tunnels (not sure what they turn into) does not look like the garbage wood in your last photo.
If wood like this was delivered to my site I would have some very testy words with the lumber yard. While the particular choices you show may not be load bearing, I would certainly not have much faith in drywall, electric boxes or cabinets being attached to such garbage. If this is representative of the standards your builder has then expect problems everywhere.
If an inspector is okay with this, what else would he pass. Your number 5 photo shows the surface gallery effect of beetle kill. The black mold is not a long term issue unless you develop moisture in the walls or structure. If the three really atrocious pieces are all you have, then shame on the builder for being so indifferent. If you start finding a lot more then speak now or forever hold your peace.
Thank you, Roger.
Now I don't worry about this mold :) I'm "stone jungle" guy from the big EU city, so don't have any experience with wood. :)
May I ask you about boards after "bark beetle insects"? Should I scared about these holes in the wood?
That last photo was from the stairs.
But external load-bearing walls have a lot of holes after bark beetles. Even roof parts have holes after these bugs. Also some of them are cracked up to 2/3 in depth.
I just don't know best way. I saw that other homes on this step in this line have similar issues. I want home for my self, not for rent. So a little bit confused with all these questions.
I'll wait for you ideas\advise. Thank you one more time.
Some of the wood pieces should have been culled during the framing (like the 3rd in your initial post and the one with the big split). A bit of care makes the work of trades down the road much easier.
I would just ask the builder to sister/replace any of the ugly ones. Since all are stamped, the building inspector would pass it as is.
It is pretty common see this type of low quality wood on construction sites. Worthwhile to have better relationship with your lumber yard so they send you better material. I'm not proud of it, but framed non load bearing interior walls with similar quality wood for myself.
Thank you, Akos.
I'll meet my construction manager to discuss this.
How I understand in my city(Austin TX) they have problems with workers and materials. City is growing to fast.
I'll push him to replace ugly parts. Thank you so much for ideas and support :)
I would look for lumber grading stamp that should have been on every board when delivered.
The rules and licensing of inspectors are very specific. It is unlikely anyone would forge a grade stamp but anything is possible. I am not an expert but some insect damage is allowable however your photo is the first time I have seed damage that appears to have been done by termites as shown in this photo.
I would be tempted to send termite damage photo to the company that grade stamped the board.
https://www.esf.edu/wus/documents/IllustratedGradingGuide.pdf
Walta
Thank you, Walter.
Good idea. Now I'll ask my construction manager to check quality.
Based on stamps I should have 2nd grade wood from Canadian Mill Services Association.
Most of the insect damage looks like wood boring beetles. These are also know as "bark beetles" locally. Damage is usually restricted to the wood just below the bark, but they can go deeper. Occasionally, Old House borers have similar lifecycle and damage. Your extra photo (the one with all the open galleries) looks more like carpenter ant damage. That piece of wood is really pretty bad and should not have been used. None of this wood needs any treatment, as the kiln drying process generally kills this sort of bug. I agree with the others that you should have a talk with the builder about changing out the really ugly pieces.
Thank you, Peter.
It's really important for me to have this support. I'm really appreciate.
I'll speak with my construction manager.
Bark beetles eat the living part of the tree, and rarely go deeper than the outer layer. Bark beetles don’t go after sawn lumber.
The damage to the wood with the hollow galleries is classic carpenter ant damage. Carpenter ants don’t eat the wood, they just hollow out the softer parts to make passageways and “rooms” for their colonies. The difference in appearance between carpenter ant damage and termite damage is that carpenter ants are very neat and tidy, leaving smooth surfaces and passages clear of debris. Termites eat the wood, and tend to leave ragged cavities and detritus all over. Both types of insects prefer wood that is moist.
Regardless of the cause, I would NOT use wood like that in new construction! That one column you show looks bad enough to be compromised structurally. I’m amazed the framers even installed it. Lumber yards will generally take back severely damaged boards like that, so it’s probably not a problem to get any replaced. I’d also talk to my sales rep at that lumberyard and ask that they do at least some visual check of things and not waste my time delivering garbage anymore.
The black areas look like mold. That’s not a big deal, but I’d clean them with some bleach solution anyway as a precaution. The insect damaged wood needs to be replaced, and I’d recommend inspecting all the rest to make sure there is no hidden damage anywhere. Look for bore holes.
All of this makes me think that lumber was stored outdoors for a while and was allowed to stay moist. Moisture allows mold to grow and also provides the conditions the insects like for their nests.
Bill
Thank you Bill.
I'm really appreciate for the help.
You're tight. Lumber was stored outdoors for about 6 weeks. During this time he had 2 hurricanes.
MikeTXMS,
The galleries in the cambium layer of a tree will not have any effect if the tree is harvested and processed properly. In past years, most of that type of bug damage would be sliced off the log becoming flitch wood, generally consigned for firewood. Given that every bit of the tree is used more aggressively than in the past, it is not too uncommon to see what I was taught to call "barkers". These are typically the smaller stud sizes cut from the very outer part of the log. A little bit of bark clinging to an edge is not aesthetically appealing, but the real problem with barkers is their tendency to be more prone to twisting and bowing.
Each log is cut for maximum production of desired stock sizes and the 2x8 and 2x10's will be cut from the "sweet" bits. The 2x4's and smaller tend to be pulled from the outer parts where they still will fit. Unfortunately, the 2x8' and 10's cut dead through the center of a log have their own issues.
Production forests are not like the old growth forests which produced the clean, straight lumber in the 40's and 50's. Remodeling older homes offers an education on what we have pillaged. Just the same, grading is meant to ensure the structural integrity of your home. No. 2 should not have the ant tunneled trash you pictured. The split ones might have had a hard fall in the lumber yard or maybe the tree cracked before harvest. The crew should have culled it in any case.
The mold is not an alarm, nor is the blue stain coloring of the end piece of the truss pictured in your #5 comment. Blue stain is common in standing dead trees and not fatal to the strength. Even the little bore holes are not too concerning. What does concern me are your mentions of deep splits in the material like the one picture. In your #5 comment you seemed to say that the roof elements had the little beetle holes AND some were split. This would be very concerning.
The roof trusses can be made from different grades of wood on an element by element basis. Some elements can use lower grades while stress critical elements must use much better graded stock. Splits in any element must be considered suspect. The engineer at the truss supplier is presumably putting is license on the line with each job. He may not see what the crew is crunching together, which he really should check on regularly. I am pretty sure the engineer would not want to be liable for a failed truss. Digging out or patching a failed truss is a pain after the decking goes on.
Before freaking out, do make a close inspection of the trusses if you are really seeing splits on them. Take photos and show them to the contractor. I would make them present written assurance that the cracked elements are still in spec. Try to do this before the roof sheathing goes on.
Just curious to know if the builder offers a home warranty on the structure for defects. Does this builder have a reputation to protect? The current insane demand shouldn't allow accepting crap.
Thank you, Roger.
You're completely right. Unfortunately in Austin TX, we have crazy home market. Even builder with good reputation use "new" and "unexpected" workers.
I got email from construction manager: "We use various grades of wood some are #3’s for dead wood and blocking and most are #2’s. We will replace the affected areas or add new one’s next to the existing studs. This can be done anytime as long as it is done before sheetrock. "
Also I'll visit this object on the Monday to see construction manager.
In the same time I see in my contract:
"The Warranty does not cover termite treatment or damage. At Closing, Builder will deliver to Buyer a certificate from the pest control company that applied the termite treatment for the Home. "
and
"Beams, joists and posts will sometimes split as they dry. Parallel splitting is usually not a structural concern because such inconsistencies in wood are
anticipated in the structural calculations of wood products. Diagonal splitting that extends from one side to another and is more than 1/2 inch deep
may weaken the beam. Under the Warranty, Builder will repair any structural component that is determined to exceed this standard within a period
of ten years after the closing. Cosmetic components will be repaired one time within the first year of the Warranty. Repairs may include additional
wood framing to the existing beam/post secured with nails or bolts."
I would be stunned to find lumber like those bored out pieces being used in a building that I was having constructed. It would cause me to completely lose trust in the builder. It would be interesting to see more photos of that framing because I expect that the lumber defects are not the only issue.
Thank you, Ron.
That the part of my question. I don't have experience with all these parts, but even I understand that somethings is going wrong with this object. Seems, it make sense to find some inspector, that can control this from my side.
After my email about current situation(thanks for y'all guys !!!) , I got email from builder: "We will replace the affected areas or add new one’s next to the existing studs. This can be done anytime as long as it is done before sheetrock. "
Wow, missing with a nail once I can understand, twice is maybe a bad day, but THREE TIMES!?!
That stud that is cut halfway through is an issue too. Anything with insect bore holes should really be replaced, but AT MINIMUM if they're still ok structurally (only a hole or two straight through like a drill would make), I would inject the holes with canned "pest block" foam. Holes can be air leaks, and can let moisture and insects in in the future.
Get all this stuff fixed while the place is open when it's easy to do. Anything that is left is there forever after the walls go up.
BTW, I agree with the other comments about the use of #3 lumber. Anything structural should really be #2 or better. #3 would be OK for blocking I suppose, but I'd never even consider it for anything load bearing.
Bill
Thank you, Bill. I'm in strange situation.
My construction manager tells me that it will be fixed\replaced, but "after". So I think that I should find some local certified person, that can read this thread and make official decision to push my builder. Builder is from top 5 in the Texas. :)
Not an expert but an admission that they are using grade 3 lumber I find shocking.
Look carefully at the fine print specifications page of your home plans. Mine has boiler plate line that reads. All wood framing to be used shall be NO.2 SO. Pine.
To me that is a huge red flag!
Is #3 approved for structural use?
Walta
Thank you, Walter.
Unfortunately I don't have this information in the home plan :(
Production builders move fast and expect their framing crews to move even faster. #3 for blocking is fine, but when they move too fast and they're missing a stud there's the temptation to grab a #3 just to get it done right now and hope nobody notices later.
The house won't fall down over this. Wood framing is ridiculously redundant as a whole system. BUT, it doesn't look good and it doesn't make the builder look good. You're paying for full #2 studs so that's what you should get.
Every home is built from a set of plans even the biggest production builder. The builder could not get a building permit without a full set plans. Every full set of plans will have a specification page. If the builder is unwilling to share the plans with you go to the permit office and ask nicely to see the copy on file with the permit application.
A agree that there is very little danger of structural failure but if they are willing to cut corners on the wood framing what other corners are they cutting?
I would be surprised any licensed architect and or engineer would put their name on plans that spect #3 lumber.
I would be surprised any permit office would knowingly approve plans that that spect #3 lumber.
Walta
I doubt very much a typical city building department actually read everything in the plans that are submitted with permit applications.
I have myself seen cities skip important details (lot lines and surveys), and I had a city inspector shut down one of my utility projects once without the authority to do so because he didn’t understand the difference between a non-exclusive private easement and a public right of way (a very important difference, since it has to do with who actually owns the land). In that particular case, I just went back to my office and called the city’s attorney (who is friendly in that particular city) and explained what was going on. I had an official apology from the city engineer the following morning.
BTW, all my permits in that city have been approved within about 24-48 hours for the past several years which has been a nice “sorry” from them :-)
Bill
I got answer in email from construction manager, that it's common in Texas and they use this approach a few decades.
Of cores the builder says #3 is OK every dollar saved go into his pocket. My question is do the professionals that drew the plans think #3 will work enough to put it in writing and risk their reputation and license.
Maybe it is the norm in Texas I would not know. I am in Missouri you would need to show me in writing.
Walta
Thank you, Walter.
Unfortunately I'm new in this country and with this process. What I should to do in this case? If I have official email from the builder that it's planned and it's ok. Should I try to find somebody who can check this? Who it can be?
Check with the architect who drew the plans first. Their name, and usually their contact information, should be in the text block of each set of plans. Tell the architect your concerns, and show a few of those pics (especially the one of the column that is mostly eaten away).
A LAST RESORT is to ask a building inspector, but that can be problems for your project so don't do that until you've run out of options. The inspector can "red tag" things they don't like, but that risks stalling your project, and upsetting the contractors.
Bill
Speaking as someone that’s worked in the trade, you have to be your own advocate when building a home. You WILL have to make them redo a job or three. If the crew still likes you when they leave, you’ve likely been had.
I’d have them replace any bark beetle eaten lumber whose job it is to do anything other than hold sheetrock. Unless you plan to sell the home inside of 20 years, then buy everybody sandwiches and call it a day.
I am kind of torn about what I would do if I were you. In my mind you are very early in this home build. The way I see it when you are building a home you are married to the build you choose until the house is complete. Breaking up will be pain full and likely expensive. I would likely try to stick it out unless there are big other issues.
Do I think your house will fall down? NO.
Will the lower quality wood be a problem in the future? Unlikely.
If you choose to make a issue out of the #3 wood.
1 Demand the builder provide you with a full set of construction plans and read the speciation page.
2 If the builder refuses to provide the plans or you do not want to confront him. Go to the building department and ask nicely to review the copy on file. Another option is to contact the architect that drew the plans and put his stamp on the plans.
Walta