Size of Framing Lumber and Exterior Insulation

Building a house in the city in zone 5/6 where space is constrained by city by-laws.
So can’t build a 20″ double-stud wall or something of the like.
So given the two choices — 2×6 w/ 2″ exterior vs. 2×4 w/ 4″ exterior, what would you choose?
Seems obvious that more exterior is better from a thermal performance…but what are you giving up in structural integrity, etc.? How does the answer change if you want to hang a heavy cladding like Brick or Stone?
GBA Detail Library
A collection of one thousand construction details organized by climate and house part
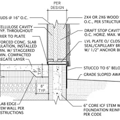
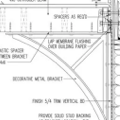
Replies
Heavy cladding sits on the foundation or a steel shelf bolted to the foundation. The size of the studs won't effect any of it.
Where stud size matter is height of walls and number of floors. Since 2x6 24OC is about the same lumber cost as 2x4 16OC, it only makes sense for 2x4 framing if you are very tight on space.
The 2x4 wall needs 3" of rigid to be about the same assembly R value as a 2x6+2", so you save about an 1". If your setback are tight, that might be worth it.
Hello Maxwell,
Like many people, I refer to Joseph Lstiburek who founded Building Science Corp in Westford, MA. Your idea of 4" of foam with at 2x4 wall is very close to Joe's "Perfect Wall". I recommend that you read this article - which I am sure most GBA'ers would not hesitate to reference.
https://www.buildingscience.com/documents/insights/bsi-001-the-perfect-wall
You can google "building science perfect wall" to read lots more and gain lots of confidence that you have the opportunity to build an amazing wall assembly.
Joe suggests about the perfect wall:
> it represents 500 years of evolution; and
> it will last 500 years
With the exterior insulation, you are potentially using XPS which consumes lots of carbon to produce and this is not entirely green. However, part of building green is also about building something that lasts, and lasts, and lasts.
As for double stud walls, I found an article from Joe L. himself and this was his perspective: "There are in fact some beautiful Passive Houses. But double walls are tricky to construct, increase the risk of moisture damage and in my view they don’t make a lot of sense. Give me a single advanced frame 2x6 wall with lots of insulating sheathing any day. I did the double wall thing 30 years ago before there ever was a Passive House. It was dumb then. It is dumb now."
Source: footnote 3 on this link
https://www.buildingscience.com/documents/insights/bsi-063-over-roofing
He mentions 2x6 but if you have only space for 2x4 then you are just using a variation of what Joe and Building Science Corp are suggesting.
Now lots of people on GBA build double stud walls (I did) and BSC does actually study the optimal double stud wall. This said, if the gurus are saying ds walls are "dumb", then don't lose sleep over not being able to build this really wide assembly.
In terms of structural integrity, my understanding is that you can build two floors with 2x4 walls, and we did. But one thing I wanted but could not manage to do is to get a structural engineer to tell you how to improve the structure of the house.
Examples:
> the corners of the house are a weak point and there are ways to solidify them and 2x6 studs do not really solve the problem anyway;
> wind shear can be addressed with a 3/4" exterior sheeting instead of using 1/2" exterior sheeting;
> installing hurricane ties, or going further and strap/link all the different layers from the foundation to the roof together to improve resilience against strong wind and earthquakes;
> having walls studs closer together; floor joist closer together; roof trusses closer together.
Simpson StrongTies sells a bunch of metal pieces that are designed to improve the structural integrity of a wood building
https://www.strongtie.com/strapsandties_woodconnectors/category
https://www.strongtie.com/holdownsandtensionties_woodconnectors/category
You can do other things to improve your home to improve resilience but not related to structure...
> use tilt and turn window with very low U value (high R value)
> taping the seams of the roof deck, in particular if you use H clips
> have hail resilient roofing materials
> build a slab with (with shorter foundation walls that are backfilled) to avoid potential floods
> put a drain in each room that has running water
> put your hot water tank in a room that has a floor that is built like a shower pan
Some videos about a house built like this
https://youtu.be/XYo868vXZ5Q
https://youtu.be/hTwq-qUnr9I
You also asked
How does the answer change if you want to hang a heavy cladding like Brick or Stone?
You may want to consider using stone or brick that you is built up on and rests on the foundation. That perfect wall article shows the brick in the assembly so it obviously works. You would likely end up with lots of thermal bridging with metal supports if you wanted to "hang" stone or brick - but I don't think you need to "hang" it.
Thanks for the super detailed reply.
To be clear, I wasn't pining for a 20" double-stud wall. I'm quite content that for my climate zone, I can get to a comfortable place based on an approximately R30-35 assembly. Just trying to think of the best way to use the 10" or so of thickness I'm allotting to the wall in the best way possible.
Thanks also for the other tips. I definitely want to put a big floor drain under every one of my water-using appliances (hot water tank, dishwasher, clothes washing machine). My question is that for a drain like that that's rarely (if ever) going to be used, I assume you can't use a P-trap because it'll dry out. And if so, how do you keep smells and gasses from coming up into the house?
1. The floor drains - a couple of important tips.
- Check this video out. It is a lot more fun than reading my long response. I do talk about details not contained in the video so hope you read below also.
https://youtu.be/864WzLG1w2Q
1 a) Trap Seal Primers
- With every floor drain, you have to install a trap seal primer. We did install some in one house back in 2007 but we did not install the trap seal primers. We just occasionally fill the traps with water - but it is not a great solution and I don't think this is allowed anymore. You can pay $800 for an electronic device or you can install a $150 device with what I believe is a called a vacuum breaker. (install manual link)
https://www.watts.com/dfsmedia/0533dbba17714b1ab581ab07a4cbb521/22914-source/2915911-pdf
The trap seal primer is connected to a pex pipe that connects just above the p-trap (image in link below). The TSP allows water to flow under very low pressure into the trap. I have 3 TSPs in my house serving 6 drains. One TSP services 4 drains alone. Each TPS model will have its own specs.
https://www.startpage.com/av/proxy-image?piurl=https%3A%2F%2Fqph.cf2.quoracdn.net%2Fmain-qimg-4e4cd5de1ed6a43bec60915f68d1e11d.webp&sp=1667517281T14ec5195952a406ab46aea3220de7924d30eaff8b558c53efede1a6e0557fbec
- You can minimize evaporation from the p-trap with a "barrier trap seal device", but you would still need the trap seal primer.
https://www.zurn.com/products/building-drainage/traps-primers-specialties/z1072
1 b) Venting or avoiding venting the p-trap
- In my province, if you install a 2" floor drain, then you need to have a vent after the p-trap connected to the vent stack that pops out of the roof.
- If you have a 3" drain then you don't need a vent where I live. Check your own plumbing code.
- Connecting the drain to the vent stack can create headaches in tight space because it is just more plumbing but consider that 3" drains require larger drain pipes. You can check your building codes and decide which solution, 3" (no vent) or something smaller (with vent), would work best for you.
1 c) Placing the floor drains
You need to plan inadvance and understand how you intall the floor drain and how you will finish around them. I mean that you need to think a couple steps further than just installing the ABS or PVC drain pipe. If you don't plan the latter parts of the install, you could end up with your floor drain above the finished floor or something almost level with the floor that looks ugly (like what I have). Planning and geting cooperation/buy-in from your plumber will be really important.
1 d) Shower pan for the hot water tank
Based on something I saw Matt Risinger do in his Youtube videos, I build what amounts to a shower pan in the location where I will have the hot water tank. I built a raised curb around the the tank to deal with any water that might rise a couple of inches. My "shower pan" is not as perfect as a real shower pan but it is built to sustain 1 maybe one leak every 5 years. Building a shower pan that is used every day requires more attention to detail. I just used differnt Schluter membranes with tile over top. The hot water tank installer had some nice complements for what I did.
2. Building height with 2x4 walls
We did build 10' tall structural 24 walls. This required an engineer to provide details, which includes a number of "columns" or "posts" within the 2x4 structural walls. Those posts are made up of either 2, 3 or in a one spot 4 of the 2x4's side by side. The engineer we used employs this method regularly so it was not a big deal.
You will not have your exterior sheeting (OSB or plywood) right up against your 2x4's, which may also increase the need for an engineered solution. When you have columns in the wall, that likely requires some a little bit extra rebar in the foundation at these "point loads".
Having higher ceilings does involve extra costs.
Notes for consideration:
> Having columns in your 2x4 wall removes space for insulation in the stud bays, but that is the beauty of having a layer of thick exterior insulation.
> You need to be sure you are not putting plumbing in the exterior wall, but this plumbing in outside walls is frowned upon anyway. You can run electrical wire through the 2x4 but no PEX, ABS or PVC pipes.
> Intead of header over every window, I would highly recommend one continuous header below the floor joists - all around the perimeter of the house. With a 2x4 wall that might require some engineering, this continous header would allow you to make future modifications or move windows at the last minute. Talk to your engineer or designer.
As a last note, I recently found out about this crazy new Air Exchanger made in Canada, based on European technology. DualCore HRV – TEMPEFF RGSP-K. It is more expensive than most but if you are looking at a Zehnder or something similar, this is in the same price range.
https://www.greenbuildingadvisor.com/question/dualcore-hrv-temeff-rgsp-k-anyone-used-installed-or-specd-this-new-canadian-hrv
Thanks a ton for this info.
I hadn't seen that Risinger video before, but that is exactly what I want to do in all of the wet areas of my house.
Appreciate the tip on the 2x4 columns. That's a good idea and something I'll ask about with the engineers.
And the ERV looks really interesting. I'm going to look into that also. My default assumption was that I'd go with a Zehnder unit, but this might be more appropriate for Canada.
Thank you!
Unless you are doing the work for the drains yourself, you really need to get your trades on board. They need to understand why this is being done.
Sharing sites like this one can quickly explain to them why this is important to you.
https://www.apega.ca/members/benefits/insurance-spending-accounts/home-and-auto-insurance/most-common-property-insurance-claims
It will be much more difficult to secure things through 4" of exterior foam compared to 2" of exterior foam. Anything over about 2" is considered "thick" exterior rigid foam, and it complicates trim details and securing exterior cladding. 4" is better from an insulating standpoint, but 2" is easier to work with from a construction standpoint. That's another thing to consider here in addition to just R value performance of the wall.
Bill
Could you use EPS as the first layer and use ZIP-R or the blue competing products? If the exterior is brick or stone, I would think that OSB from the ZIP would handle those items that you mentioned. No?
The issue isn't having something strong on the outer surface of the foam, the issue is the difficulty of securely attaching ANYTHING (including something like Zip-R) through 4" of foam. Yes, you certainly CAN use foam this thick, it just makes things more complex, since you need very long fasteners, you have to accurately "aim" these fasteners to get them into the framing behind the foam, and you have to deal with the tendency for the thing you hang to want to sag by pulling the fastners down sideways through the foam. It's doable to make this work, you just have to be careful.
You wouldn't need Zip-R here. You could just put a layer of plywood or OSB over the thick foam to provide a mounting surface for trim details and cladding. There is no benefit to using Zip-R here, you could use anything (plywood, OSB), or regular Zip. The EPS is already your insulating layer.
Bill
Thanks to all for the responses. Any sense of what are common height restrictions with 2x4 framing? I'm planning on building a house that 33' tall at its peak, but the main walls are about 25' high. I'm in neither a seismic zone and we're far enough in land that we don't have to worry about hurricanes and we're not in an area that sees tornadoes.
maxwell_mcgee,
Do you mean continuous stud walls, or several stories?
Our code limits the height of continuous 2"x6" load-bearing walls to 12 ft, before they need engineering. Typical (8 ft) 2"x4" walls are often required to have a tighter spacing if they support a second storey and roof.
Two stories for the bulk of the house. 10' ceilings on the main floor, and 9' on the second floor.
However, there is a wing of the house which has cathedral ceilings, and there, it's a single continuous wall that will reach up to ~25' to the peak of the gable roof.
The plan right now is to build with 2x6 construction, 16" OC (our house plan and placement of doors/windows does not lend itself to 24" OC.
So default assembly will be from inside to out:
- latex paint
- 5/8" drywall
- Intello Plus membrane
- 2x6 stud wall 16 OC with fibreglass batt inside (good densepack cellulose installers hard to find here -- want to consider alternative insulations though)
- Zip R-12 (2" polyiso + 0.5" OSB sheathing)
- rain screen
- 4" brick / stone cladding
So this assembly will dry to the inside.
My thought was maybe we can do something different without changing the thickness of the wall assembly. Something like:
- latex paint
- 5/8" drywall
- Intello Plus membrane
- 2x4 stud wall 16" OC with fluffy stuff inside (maybe hemp wool or sheeps wool?)
- 0.75" plywood sheathing (for extra structural rigidity)
- WRB (something vapour open...maybe a siga or proclima product?)
- 4" of exterior insulation (I'd love to use wood fibre, but worried about availability and price)
- rain screen
- 4" brick/stone cladding
So this assembly could dry in both directions. Also moves more of the insulation to the outside (less condensation risk) and reduces thermal bridging. Both should have similar nominal R values (in the 30-35 range) but effective R-value on the second should be much better given the greater amount of exterior insulation.
What I worry about is (a) structural integrity of the second assembly, (b) price/availability of the products and (c) the ability for the builder to actually put this second assembly together well. They're super comfortable with the default 2x6 + Zip assembly...this second option will be pushing them outside their comfort zone.