Spray foam & wood roof deck

100 year old residence is located in Zone 5 w/i 50 ft of ocean/bay & has a 100 mph design wind load requirement. It is located high on a hill & completely exposed. Vented eave ridge is not advisable in this area do to high driven rains. The home will not be the primary residence, therefor optimal heating, venting & dehumidifying will not be maintained 24/7.
The energy code requires 49R roof assembly for the proposed occupied attic w/ cathedral ceiling. 49R requirements & existing 2×8 rafters, limits choice of insulation to closed cell spray foam.
The GC has proposed 1/2″ plywd over exist 1″ sheathing boards w/ “Shnglemate” underlayment & lifetime asphalt shingles. An additional vapor barrier would be the typical latex coating either underside of insulation &/or drywall.
I’m concerned, like most, the deck wont be able to dry to exterior.
Is a high perm or low perm underlayment advisable? What perm rating is wise? 5? 16?
My research has left me rather confused.
#1 when researching red cedar siding, the cedar institute(?) advised old time bldg felt because it acts as a wick and will draw vapor from the warm interior towards the colder outside. Would this be advisable for asphalt roofing application?
note: the FEMA hurricane advisory recommends a fully adhered underlayment (ice&water shield) over whole roof & organic shingles (has lower tear off rate than synthetic). I assume such an underayment would be nonpermeable, but agree that nothing including ice & water shield is guaranteed not to fail.
GBA Detail Library
A collection of one thousand construction details organized by climate and house part
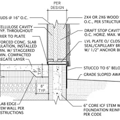
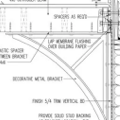
Replies
Sheila,
Most types of synthetic roofing underlayment aren't vapor-permeable, and manufacturers of these types of synthetic underlayment forbid the use of their products an unvented roofs. It sounds like you are planning to create an unvented roof.
If you prefer the added benefits of roof ventilation, you can provide a ventilation gap above the existing sheathing by installing 2x4s on the flat, either 16 inches on center or 24 inches on center, from eaves to ridge, followed by another layer of plywood or OSB.
Another way to provide roof ventilation is to make site-built ventilation baffles in each rafter bay from the interior, by inserting 1.5"x1.5" sticks into the corners of the rafter bays, followed by plywood. Then the spray foam can be installed against the ventilation baffles.
Roof decks NEVER dry toward the exterior- the shingles & felt layup is about 0.1-0.12 perms, practically a Class-I vapor retarder.
If you are re-roofing (and it sounds like you are), the "right" thing to do is to add R20-R24 as rigid foam above the roof deck, and open cell foam or dense-packed cellulose/fiberglass under the roof deck.
http://publicecodes.cyberregs.com/icod/irc/2012/icod_irc_2012_8_sec006.htm
That way the structural roof can still dry toward the interior, but has sufficient exterior R for dew point control on wintertime moisture drives. As long as ~40% or more of the total R is on the exterior, it's fine to use adhered membranes above the roof deck, and keep the interior side relatively vapor-open.
The exterior foam can be held in place with a non-structural nailer deck through-screwed to the rafters at whatever fastener spacing meets your wind loading requirements. (In less stringent applications pancake-head timber screws 24" o.c. works, but you may need to tighten that up slightly.) The nailer deck may need some sheets replaced when you re-roof if you wait until it leaks, but it's in no danger of taking on moisture from interior-side vapor drives, only from the exterior. Venting the nailer deck is possible, but probably not worth what it would take to make it tolerant of 100mph winds.
With R20 above the roof deck and even with standard density R25 batts you would only be at R45 center-cavity, but it would outperform R49 due to the fact that the exterior foam insulates over the thermally bridging rafters. Dense packed cellulose (3.2 lbs minimum density) would give you about R26 in milled 2x6 rafters, (R29 in full-dimension 2x8s). Dense-packed fiberglass (1.8lbs minimum density) would deliver R29 in milled 2x8s, and R32 in full-dimension 2x8s.
To hit a reliable R20 on the exterior with rigid foam in a zone 5 location it's best do use 2" of polyiso against the roof deck (R12-R12 nominal) and 2" of Type-II EPS (R8.4 nominal) between the polyiso and your shingle nailer deck (which can be half-inch OSB or half-inch plywood.) This is because polyiso lose performace at very low temps, whereas EPS gains performance. at low temps. By putting EPS on the exterior it keeps the polyiso sufficiently warm that it delivers nearly it's fullyrated performance, whereas the colder EPS will exceed its rated performance.The dual-foam stackup outperforms 4" of all-polyiso or all EPS during the season that counts.
Filling the rafter bays with closed cell foam would add some structure, but at high-R it's a climate disaster due to the extremely high global warming potential of the HFC245fa blowing agent that is used for nearly all closed cell polyurethane. )That stuff has about 1000x the global warming potential of CO2!)
Rigid XPS (blue board, pink board) has a similar issue, since it's blown with HFC134a at about 1400x CO2. But EPS and polyiso are both blown with pentane, at a comparatively modest 7x CO2 GWP.
BTW: The notion that #15 felt or #30 felt "...acts as a wick and will draw vapor from the warm interior..." is pretty far off the mark. The #15 felt commonly used under siding is fairly vapor retardent when dry, but becomes moderately vapor open when wet. But #30 fel is fairly vapor tight, period, and when covered by asphalt shingles it behaves pretty much as a vapor barrier (though still more vapor open than Ice & Water Shield.)
Yes, we are designing for unvented space do to driven rain. RE: site-built, wouldn't you have vent ridge?
Asphalt shingles don't seal down well the first year if installed close to winter..... in winter... late Fall. The North side won't seal down till the following summer.
What's your northern exposure?
AJ that's true unless your roofing contractor torch's them down. A qualified roofer knows the tricks.
Sheila Sullivan,
Call your roofing manufacturer to find a qualified trained roofer in your area.
Richard what? Please post a manufacturers instructions that detail torching shingles.
IMO nuts. Proper way to roof in high wind area is to roof when the sun is high to seal down your shingles.
One huge problem in construction today is impatience. Like the blog of late where concrete is being poured inside a tent. Good idea but bad timing!!
1- Plan your home and get all your permits allowing for 6 months, there will be delays, and site plan reviews that get kicked a month or two due to review.
2- Break ground in the spring,
3- Frame homes all summer and roof them weathertite.
4- Fall to winter is time for mechanicals, insulation, time for the frame to acclimate and lower a bit in moisture content, which leads to less drywall nail and screw pops...
5- Keys handed over in winter to spring, not roofing or concreting then!
Lastly, once the home is done.... take some time to move in... and only then plan your first in home holiday... I have had families plan huge holidays unbeknown to me to happen a week after we complete our broom swept job. Forget it. It can be done, but... I now warn customers not to plan anything till they possess the home and we are out.
Richard, are you a residential GC or a expert roofing company? Torching shingles PDF please... we do not and will never torch down shingles. We warm bundles of shingles in cold weather and avoid cold weather shingling.
AJ your over stating my comment of torch down and by no means was my comment challenging your knowledge. It's common practice around here to use a torch to warm the shingles during winter installations. It may not be a published method, but it is consistently done successfully in the northeast and there are cases where these roofing contractors have burned houses to the ground doing so.
Thank You everyone. No we will not be roofing this fall but next spring. We are in the planning process.
Re: R806.4: Do I understand correctly: Rigid board is req'd on the top of the roof sheathing if we were to use open cell permeable insulation but rigid board is required underneath closed cell impermeable insulation (therefor between rafyers & gwb ceiling)?
or re: R806.4: Is this correct: rigid board insulation is required above the deck only if we use open cell permeable insul?
Sheila,
I don't think you are describing the code requirements properly.
Code requirements vary depending on:
1. Whether you want to build a vented assembly or an unvented assembly.
2. Whether you want to use just one kind of insulation or are considering a mixture of insulation types.
All of the options are explained in this article: How to Build an Insulated Cathedral Ceiling.
If you describe what type of roof assembly you want to build --vented or unvented -- and your preferred insulation materials, I can answer your questions better.
As noted above:
1. un-vented, do to topo & location concerns: on a hill exposed to panorama of NE-SW winds from ocean & bay.
2. the home owner would prefer not using foam or plastics at all any where. However, there are various requirements/restrictions, which have left us with no choice but foam whether alone or hybrid.
Requirements: Zone 5, R-49, a minimum 100 mph design wind load (because of topo we wish to enhance wind design, the home lays completely w/ 100' of bay).
Restrictions: the existing conditions are 2x8 rafters spaced irregularly (~16" O.C.), the home is in a Historic District.
I have reviewed the options:
1. Hybrid: 4" cc foam @ underside of deck + 3.5" HD batt, however; total R-Value wont reach 49. I reviewed this option because the occupants might be less exposed to the toxic(!) foam.
2. Rigid Board @ t.o. deck: would require 3"+ rigid board to meet ~40% R-value. I believe this would impact the current profile of the soffits @ the eave, I am concerned re: the visual impact @ the eaves & the ability of any GC being able to demarcate the irregular rafters to insure the insulation is adequately secured, especially re: topo concerns.
Your thoughts
Also in addition to above: I am highly concerned re: placing non permeable materials (cc foam underneath & underlayment/asphalt shingles above) on both sides of the existing wood deck. Especially since one side will be cold the other warm, therefor; the wood deck being right @ the point of condensation.
Are my concerns re: this warranted? What is the industry standards re: this?
I'm not up on light frame, pitched roof construction. My area of experience is steel framing, flat decks pitched w/ insulation & interior drains.
Sheila,
Q. "Re: R806.4: Is this correct: rigid board insulation is required above the deck only if we use open-cell permeable insulation?"
A. No. If you want to install air-permeable insulation (for example, fiberglass batts, mineral wool batts, or cellulose) against the underside of your roof sheathing, then you must also install rigid foam insulation on top of your roof sheathing with a minimum R-value (in your climate zone) of R-20 (for example, 5 inches of EPS or about 3.5 inches of polyisocyanurate).
If you decided to install open-cell spray foam against the underside of the roof sheathing, you don't need to install any rigid foam above the roof sheathing. But the open-cell spray foam still needs to meet minimum R-value requirements -- which in your case means R-49 -- and it needs to be protected on the interior with a layer of gypsum wallboard that has been painted with vapor-retarder paint.
Sheila,
Q. "I am highly concerned re: placing non permeable materials (cc foam underneath & underlayment/asphalt shingles above) on both sides of the existing wood deck. Especially since one side will be cold the other warm, therefor; the wood deck being right @ the point of condensation."
A. I addressed your concern in my first answer. If you are concerned about this issue, then you should really consider a vented roof assembly. The vent channels can either by below the existing roof sheathing, or above the existing roof sheathing. You might want to re-read what I wrote in my first response.
The R-ratio is important- you can't put only R20 on the exterior then put R38 under the roof deck in zone 5. The exterior insulation has to be at LEAST 40% of the total R for dew point control in that climate zone. (R20 is ~40% of the prescriptive R49 code-min.) It's the ratio that determines the average temperature at the roof deck, which is intended to be above the dew point temperature of the conditioned-space air. In zone 5 that is presumed to be 38-40F, which is the dew point of 30-35% / 68-70F air.
Open cell foam (even at the full R49) may be more vapor permeable than ideal, and is a potential problem for the roof deck. Half pound foam would still be about 2.5-3 perms @ R49. (At R20 it's sometimes north of 10 perms.) Ideally you'd want it to be under 1.5 perms, but over 0.75 perms, which gives it reasonable drying rates, but a slow enough adorption rate during the winter months that it's not a problem.
Also, at R49 open cell foam you need 13-15" of foam, applied in three lifts of at most 5" each, with curing/cooling time between lifts. Doing it any faster has both fire-safety and function issues- it can self-ignite while curing if done too thick/fast, and can have shrinkage/adhesion/cracking problems.
With plank sheathing open cell foam on the interior is usually going to be OK, but with OSB or plywood on the roof deck it's worth paying more attention. But it's better to use an exterior rigid-foam approach (at or above the IRC chapter 8 prescriptive R20), with R30 or less in cellulose between the rafters, tight to the roof deck. Even an R45 center-bay value in this stackup would outperform a code-min R49 between rafters, due to the exterior insulation thermally breaking the more thermally conductive rafters.