Stability of wall when using exterior insulation
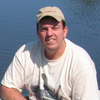
Does anyone else wonder about the structural integrity of the finish layer on exterior walls when they’re constructed with exterior rigid insulation?
I’ll assume the builder supports the windows and doors appropriately by tying them into the structural layer. But what about the weight of the finish layers that are well out from the structural wall?
For example, take a wall with 4″ of XPS insulation held to the structural framing/sheathing with 6″ screws. Then layers of other materials for rain proofing etc., and ultimately the finish material like cement board or maybe even stone veneer. So the finish layer could easily be 5″ out from the structural layer of the wall.
There could be a significant bending load on all of the screws, especially a good sized wall with few windows or other openings. Almost like a 5″ thick floating wall, held on by a bunch of screws with a lot of the weight 5″ from the point of structural contact.
GBA Detail Library
A collection of one thousand construction details organized by climate and house part
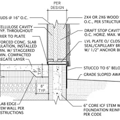
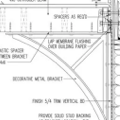
Replies
This is an oft traveled path, with well engineered solutions. There are specs for the fastener types, spacing, depth of stud penetration etc depending on the thickness of the foam + furring and the weight/type of cladding. See:
https://www.greenbuildingadvisor.com/article/fastening-furring-strips-to-a-foam-sheathed-wall
T. Barker,
Dana is right. Very heavy types of cladding can sometimes be a problem with very thick rigid foam, but for most foam thicknesses and siding types, this isn't a problem. Just choose the right fasteners for the furring strips, make sure that the fasteners hit the studs, and use enough fasteners.
As Dana noted, you can find more information in this article: "Fastening Furring Strips to a Foam-Sheathed Wall."
NOTE: This post has been edited to reflect an error I originally made calculating the psf of the furring. I still think builders should use caution.
I need to spend some more time on this, but after initial review of several references this issue should not be taken lightly.
Current working links to a couple of documents:
1.) Research Report (updated Aug./2018) https://www.drjcertification.org/system/files/drj/ter/node/726/drr130304attachingexteriorwallcoveringsthroughfswood.pdf
2.) Code Compliance Report (updated Aug./2018)
http://www.appliedbuildingtech.com/system/files/abtgrr_1503_02_attachment_of_exterior_wall_coverings_through_fpis.pdf
Most of the current Hardie siding products combined with 1x4 furring will just barely fall into the 3 psf column in the tables. However, the Hardie Artisan Lap siding will fall into the 11 psf column. Many of the stone veneer products will fall into the 18 psf column in the tables.
So for example, "HardiePlank" siding with 1x4 furring, ignoring wind design requirements for a moment, and just considering weight of cladding. Yes, with specific fasteners you should be good with 4" foam, assuming 16" OC framing. If 24" OC framing you need to be a little more careful with fastener spacing.
But if you are using Hardie "Artisan" siding for example, you are into the 11 psf column (with furring), and there is only one specific case where 4" thick XPS would be allowed, and the builder needs to use at least 0.162" dia. nails, every 8", and penetrate the wall framing at least 1-1/4", assuming 16" OC framing.
For many cultured stone products, looking at the 18 psf column, there is only one specific case where even 2" foam would be allowed without custom engineering design.
It seems to me that all builders need to pay close attention when using any amount of exterior foam and cladding on a building.
I think Martin wrote an entire article on this topic- most uses screws - here is a link to the Simpson catalog see page 11
Oops here is the Simpson Link
https://embed.widencdn.net/pdf/plus/ssttoolbox/s1whq1ewsi/F-F-SDWS14.pdf?u=cjmyin
T. Barker,
The fasteners with exterior insulation are mostly in tension, not bending. The insulation, fastener and furring strip form a small triangular truss structure, the load through the screws is fairly small. There is a good report that looks at displacement and fastener loads with various insulation thickness and siding options.
https://buildingsciencelabs.com/wp-content/uploads/2017/11/CCBST-2017-Structural-Testing-Screws-through-Thick-Exterior-Insulation.pdf
Very interesting.
I believe this is the full report, which is needed to thoroughly understand the test and results. https://cdn01.rockwool.com/siteassets/o2-rockwool/documentation/technical-guides/commercial/structural-testing-of-screws-through-thick-exterior-insulation.pdf?f=20181004102146
The insulation and strapping create a stiff assembly and take some of the load in compression. Combined with friction resistance between the layers, bending/deflection is significantly reduced. In the range of most cladding loads it's still primarily a bending problem when screws are installed at 90 degrees.
The big take-aways for me were that:
1.) Within the limit of most cladding loads (i.e. up to 25 psf), and even up to 45 psf, deflection is surprisingly small in all cases. I would argue negligible.
2.) Semi-rigid Rockwool is every bit as good as stiffer XPS boards regarding deflection, and insulation thickness between 3" and 12" does not significantly change the deflection either.
3.) Not necessary at normal cladding loads, but ideally screws would be installed at 45 degree upward angle.
4.) If I was going to install 4" or more of exterior insulation I would consider (but probably wouldn't) upgrading my sheathing to 3/4" plywood because of the increased chance of screws missing the framing.
Still need to remember that this research covers a specific case with 0.20" dia. Heco-Topix 8.0x (or equivalent) screws, spaced every 12", 16" OC.
Same with the Simpson Strong-Drive timber screws mentioned in a post above. Substantial screws at 0.22" diameter, recommended 24" spacing for most cases. Although their conditions would exclude Rockwool semi-rigid board (probably incorrectly according to this report).
> Semi-rigid Rockwool is every bit as good as stiffer XPS boards regarding deflection,
The Building Science link shows about 30% less deflection with XPS.
> ideally screws would be installed at 45 degree upward angle.
Is there any concern that such an angle would direct bulk water to the sheathing?
Not clear to me is if there would be any advantage to adding glue. Less potential for movement against the foam, especially if long term creep reduces compression.
"with 0.20" dia. Heco-Topix 8.0x (or equivalent) screws, spaced every 12", 16" OC."
Having to use screws of that type and spacing mean the cost of fasteners moves from a background incidental item to one that impacts the house budget.
I agree.
The authors said further research needs to be done to assess alternate screw diameters.
> Semi-rigid Rockwool vs. XPS.
Yes, but 30% of what amount? In this application that difference in deflection is so small it does not have any practical impact. So in my opinion, "every bit as good" from a deflection perspective.
>Screws at "45 degree upward angle". So the head of the screw would be lower than the point of the screw that gets embedded in the framing. So driven into the assembly from lower to higher. I can't see how water would be directed to the sheathing.
30% difference may allow fewer or cheaper screws for the same deflection.
Agreed on "45 degrees up towards the interior".
So how do we reconcile this RDH Building Science information with the IRC tables and also with tables from various fastener manufacturers like Simpson SDWS Timber Screws? How would you convince a building inspector what to allow?
Best would be to have the structural engineer spec the details. The only downside there is depending on the engineer's CYA factor, you might be putting in a lot a of screws.
I guess I was lucky with my build as the inspector never asked about the details of the exterior insulation and siding.