Stacking SIPs and nailbase for superinsulation

I have a passive house project in the Colorado Rockies and need heaps of insulation to make the numbers work (R-90 walls, R-120 roof). A local supplier has polyurethane SIPs that come in at R 6.66 /inch, however only to a dimension of 8.25″ thick for approx R-50 for the 8″ panel. I had thought about stacking nailbase SIP from the same manufacturer on top to achieve my R value, but my brain sounded alarm. There would be a layer of OSB that can’t “breathe”-this seems bad. However, being a passive house it is going to very air tight, so the probability for moisture carried into the wall system seems low. However moisture could still enter by diffusion, and then has no place to go. I am now thinking of cantilevering TJI’s ont he exterior of the SIP with cellulose to derive my desired R Value and allow that OSB skin to breathe, but I liked the simplicity of two systems (Load bearing wall system + SIPS) instead of three (Bearing Wall+SIPS+TJI’S).
I could omit the SIPS, but my wall would grow thick as cellulose is significantly less R per inch than polyurethane SIPS, and I would have to build custom 2’+ thick larsen trusses. Double framing does not seem to wrk as I have not found a good detail to avoid thermal bridging at the foundation interface. Anyone?
I know Thorsten up in Alaska is a fan of the remote wall system, and that got me thinking,
but I have never liked the idea of the moment all the siding puts on really long screws. (Sag?)
Thoughts, anyone…….? Really thinking up a storm here….
Erik
GBA Detail Library
A collection of one thousand construction details organized by climate and house part
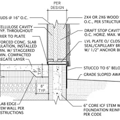
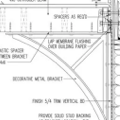
Replies
Actually...Thorsten is no longer building REMOTE
he has a new system that he prefers
https://www.greenbuildingadvisor.com/community/forum/general-questions/19942/sunrise-home
Are you using the SIPS structurally?
Erik, Your R numbers are possibly excessive to put it mildly. Maybe some planning with a experienced PH guru could straighten out your dilemma.
Interesting thought me just had. Has anyone altered their R values on walls and roofs depending on which side faced which compass direction?
LeeCor Systems has a light-weight SIP that does not contain any osb/wood products. This could be an option for you. Check-out one of the two sites: http://www.LeeCorSystems.com http://www.ThermaSteelCorp.com
1_Modified Remote
2_No the SIPS are not load bearing. I have a 2x4 load carrying skeleton.
3_R numbers are NOT excessive for my climate, Zone 7 9000 HDD. Passive House standard is a rigorous one. The building is small, which puts it at a disadvantage (surface area to volume) but this is a development standard for urban infill. I am a PH certified BTW. Compass direction-nice thought, but at night or on an overcast day all sides are equal are they not? However I am pulling HRV intake air from the south and not the north along a similar vein.
4_Thank you! I will look into it!
Just to echo the suggestion by John Brooks: for anyone interested in crazy high R-values, do check out Thorsten's Sun Rise house, because it has many important lessons. One is that if you want a HUGE quantity of insulation, it's in your interest to find a way for that to be cellulose, not foam. Thorsten's system is scalable to any required R-value targets.
Erik,
Thorsten mentions many advantages of the ARCTIC WALL
see comment #9 in this thread
https://www.greenbuildingadvisor.com/community/forum/gba-pro-help/23076/r-value-v-thermal-mass?page=1
If I lived in your Climate I would probably crank the dial up to 11 myself ;--)
6_Thank you for your input. I should have added that I don't have the luxury of unlimited wall thickness, it is urban infill and I need to keep the R value to width ratio as good as possible-hence the foam. Believe me I have checked out Thorstens work. Note the pristine site. I do not have that. Any width increase in the walls turns into reduced areas elsewhere. Hence my SIP/cellulose hybrid approach.
7_Nice link. That was a good read.
Conclusion thus far: My idea of a hybrid wall system SIP + Cellulose seems to be winning for my particular situation. I seem to get the benefits of both systems.
Still looking fo further insight though-thanks all!
Since you are building a small house in an infill development, I assume you're very concerned about your environmental impact. You should therefore confirm that the foam used in those SIPs has a low global warming potential (GWP). See Avoiding the Global Warming Impact of Insulation and other articles by Alex Wilson for more on that topic.
That said, I agree with AJ Builder that you ought to consider building a PGH (pretty good house?) rather than a Passivhaus. You won't be burning much fuel to heat a small house anyway, so hitting those arbitrary PHPP goals is not so important. Or maybe wait for PHIUS to modify the certification requirements based on house size and climate zone. Perhaps they'd be willing to use you as a test case for their proposed new approach.
erik,
i caught your comment on the phius blog regarding climate and size. first, i think it's incorrect to compare CO zone 7 to central europe - it's more like tampere or st. moritz (well, st moritz IS central europe)
second, you seem to be running into some awesome issues meeting PH with your project, i don't see this as an issue w/ passivhaus, as much as it is a 'design' flaw - that is, building detached housing in extreme climates. this is what leads to absurdly high R-values.
is the project as compact as possible?
do you have any southern glazing, and what are window specs? also, if up in the mountains you probably won't be able to use the ultra low U-value glazings (e.g. Kr & high Ar mixes)
are you overframing your windows for a better psi-install value? this can make quite a difference
ventilation recovery rate above 90%?
I appreciate all the thoughtful comments. I guess what I need to do is suggest that I restrict the posts to the title of the original question-stacking SIPS as related to building science. I am well aware of embodied energy and the nuances of the PH standard, as well as the difficulties of what I am trying to achieve. (I have my reasons that go beyond this topic)
10_Careful about maligning PH standards as "arbitrary". They are not. They are just based upon
different conditions.
11_St Moritz-yes if you want to split hairs. I am not talking about geographic anomolies of Central Europe. The fact remains that the PH standard works great in Stuttgart but where I am located conditions are much, much different. With regards to "design flaw" of detached housing this is a larger societal issue which is outside the scope of this topic. With regard to your suggestions, yes, I am very well aware of all of these.....thank you.
Please comments only on SIP stack ups and nailbase stack ups! Not the PH standard nor the application thereof!
No comment
Bad design, bad plan. That's my comment.
You can lead a horse to water...
I would not suggest a foam sandwich around your OSB. Although air and diffusion-driven moisture movement in this assembly should be minimized....you still have to deal with the possibility of bulk water getting to the OSB.
If the OSB does get wet, it will not dry out quickly.
16_ Thank you for your input John! It is nice that somebody weighed in with "building science" commentary rather than quality judgements concerning my project (without knowing all the factors/constraints/motivations). ex Lucas' comment-useless. (My fear about posting to the blogosphere has somewhat been confirmed in this sense-people seem to be quite opinionated).
John, I agree and this has been my feeling as well. Again thank you for weighing in on the question, This confirms my suspicions that there is a layer that cannot dry out should water intrude. One should always assume it will I suppose. I put the assembly into WUFI at 3AM (much to wifes dismay) and my suspicions were confirmed here as well. I think the final solution for the assembly will be a Larsen truss stuffed with cellulose and possibly the SIP /Larsen hybrid depending on how the numbers shake out.
Thank you again,
Erik
" I do think your hybrid wall is a good way to proceed forward."
Eric, no need to be upset. As I said earlier, your alternative plan makes better building science sense. GBA is a great source. Don't let this thread push you away.
;)
Erik,
I am inclined to believe that you are still at a point where you have not committed yet to one approach or another.
Yet, because of your rejection of almost all comments subsequent to the OP, I think it is fair to say that you are being headstrong.
Internet forums are like a box of chocolates...
My opinion:
Stacking SIPS together will, as you guessed, give you an OSB sandwich with very little drying potential.
Better pray moisture never gets in there...
In a 9000HDD climate, R90 walls and an R120 roof seems absurd - even for PH.
Thorsten's Sunrise Home was built in a ~14000HDD climate (~60% more HDD) and yet "gets by" with R75 walls, R115 roof and R60 slab.
So, Mike's comment about a possible "design flaw" seems salient.
If Mike's suspicion about a possible "design flaw" is correct, then potentially there is an opportunity to move to a different (more forgiving) wall assembly AND reduce the total thickness of the walls.
Comment for John Brooks -
When I've talked with Thorsten with about the wall system for his new house, he still thinks of it as a REMOTE wall....minus the peel'n'stick membrane and minus a lot of embodied energy. Still practically airtight. Still with nearly all of the insulation is to the outside of the structural layer.
Comments for Erik -
I have to admit I was tempted to add my own slightly off topic comments as others had. It seemed to me that the comments (in general) were meant to be helpful. LOTS of people read these forum posts. When answers/replies are posted, while they may be directed to the original poster, they are not JUST for one person. For example, until high GWP blowing agents are off the market, I will never get tired of someone bringing up the issue. If you want to avoid side-comments in the future, perhaps you should provide less detail about your situation. For instance, "I'd like to get everyone's opinion on the moisture durability of using nailbase insulation over SIPs in a cold climate."
John Semmelhack,
The ARCTIC Wall does have some similarities to REMOTE
I based my comment on an Email from Thorsten
TC:"....Anyways, hope this was useful. I am trying hard to finish up my report on the new ARCTIC wall system which goes into detail about the physics of the assembly and its benefits. All my data is very supportive and I switched all our construction to the new system. No more REMOTE walls ...."
Erik, your lot constraints should lead you to building a PGH not PH.
You're looking for a square peg that fits a round hole.
Barring that, may the force be with you.
I do think your hybrid wall is a good way to proceed forward.
19_I am only rejecting comments that address topics beyond the basic scope of the original stacking sips question. There is ALWAYS more than immediately meets the eye. Ex Thorstens home may have less R value in the walls and roof, but he utilizes instead vacuum panel doors, a HUGE seasonal solar hot water tank insulated to R-50!!!, thermal shutters,etc. So comparing R values alone is overly simplistic. I am proud of Thorsten for experimenting in his way-it needs to be done. You see my point. He has made decisions based on his scenario, both personal and geographic. Passive House has "rule of thumb guidelines ... R-50 walls for chicago, R-70 walls for minneapolis (zone 6) so a wall assembly in the neighborhood of R-80-90 is not "absurd" for Zone 7.
It is often a matter of choosing where to spend ones money. IMHO, I am of the belief that I would prefer to spend extra money on "dumb" insulation rather than on the complexity and maintenance of a solar hot water system, fragile vacuum panels and the like. These things have moving parts and can and do break. I desire low maintenance, therefore the value judgement that my R values are "absurd" when all I was seeking was the information to confirm my suspicions that stacking SIPS is a vapor sandwich.
Again, I value Thorsten's work, especially the science based work performed in cojunction with the cold climate research center. But assuming because he has used a certain R value I should do the same is incorrect. PH software looks at a building wholistically-site, climate dependent, occupant dependent, surface to volume, utilization, etc. If I happen to be constrained by some variables, then there will in turn be an affect on other variables to complete the equation. This is true of the budget as well. I can guarantee that NOT having a seasonal storage tank and associated excavation and long term maintenance will help my budget and allow money to spare for my "absurdly" thick walls.
Andrea-thanks for the constructive advice on insulation embodied energy, you are helping my move towards a cellulose only assembly.
Sorry if I have been somewhat peeved, but when people begin asking if I am intelligent enough to have designed south facing windows (!) into the scheme and calling my wall assemblies absurd instead of commenting about the building science behind my stacking sips I get frustrated.
Erik
That's the problem with asking for input.
Erik, you are both tall and handsome... I'm sure of it my man.
Ya need to learn to laugh off whatever is passing into your noggin and gettin the best of you. Why I bet you are even smarter than at least two of us. LOL
Enjoy this Thread Erik and smile. No one really wants to break you.. well... we do actually. Welcome to GBA. I think you are a good fit here.
And you should be skiing right now. What's with that? Am hitting the slopes tomorrow.
Feel the love
Erik,
Best of luck to you.
Eric
What I see in this situation is that you have asked a question, in effect, asking those here [who are much smarter than me] to teach you, with out reciprocating. You are refusing to teach 'us' about what situation, what design criteria may cause such insulation values to be required.
By refusing to 'teach' you will be limited in what you can learn
R-90 wall are not a surprise in Colorado and while a r60 wall may work in Denver I've seen a project relocated to Alamosa which jumped the numbers up 30%. A wall assembly in CO is not really subject to a lot of water vapor if properly detailed, but a roof is a lot more at risk. SIPS are making a lot of sense sandwiched to get the numbers on a wall assembly.
Really few walls do survive a "bulk water" situation without ruining the insulation system etc. Question is can you afford the room for expanded polystyrene rather than extruded. One SIP for structural then stack with single skinned with OSB or better CDX. A raised heal truss roof with cellulose that breath would be nice to calm the GWP nerves but I think you do what you have to do to get the numbers.
Thanks for your input Andrew, that was helpful. The panels I was looking at are polyurethane units, and I did indeed consider the "nailbase" variety. Another thought I had was, since I have a load bearing stud wall, have two layers of nailbase SIP with the exposed sides facing towards each other so as to eliminate mid assembly OSB. The fastening of this assembly to the stud wall is something I still need to think about a bit. The innermost layer would have support at the base, but the outer layer bearing the weight of the siding would have to be attached with some very long screws.
Erik,
This is America, and of course you have the right to build a house any way you want. And of course you can ignore the following (off topic) questions if you want.
1. Have you calculated how many BTU per year, and how many dollars per year, you will save by going from R-40 wall insulation to R-90 wall insulation? How much are you willing to spend for the insulation upgrade?
2. Have you calculated how many BTU per year, and how many dollars per year, you will save by going from R-60 roof insulation to R-120 roof insulation? How much are you willing to spend for the insulation upgrade?
Just curious if you've done the math yet...
Martin,
These are VERY valid points (despite being off topic:) and this is an overall part of the decision. I have valued your common sense numbers approach in the past on other items, eg: solar electric. I don't have exact numbers yet pending some other decisions, but will post when I get them.
I am also planning on calculating cost benefit on thermal shutters mainly to satisfy my own curiosity.
Erik
Erik,
I recall that a company named EarthCore SIPs in Colorado offered urathane SIPs up to 12.5" at an advertised R=84. They also offered MgO skins so no OSB in the center if you went with two SIPs.
Erik - you get points for a very thoughtful approach. Are you sure your SIPS sandwich would work structurally? Not sure the fastening would work for shear. We skinned a house with ZIP, 2" PIR, then 2-1/2" nailbase. Allowed us to air seal at the ZIP and get shear. You can get SIPS screws about any length you want.
Not an approach I'd recommend for new construction - this was a reno.
Bill, Thanks for the link! That's super helpful. I'm curious to see how that company works out. I will contact them today. I spoke with a competitor (ICS SIPS) out of Fort Collins and they claim that the manufacturing process is such that panels thicker than 8 1/4" raise the internal core temp so high during the curing process the core chars-lowering R value. I wonder if Earthcore has a workaround??
Dan,
Good point on the shear. I was going to speak with my engineer about screwing the first layer of nailbase through the stud into the sip from the inside with some construction adhesive. The second layer of nailbase (skin out) would then attach with long sips screws. The first layer of nailbase would also be supported by the foundation sill plate.
Martin,
My 3AM thought was that when I calculate the cost per BTU/R value, I somehow need to include in the calculation the cost savings of not having a boiler and associated equipment and maintenance-this is the PH "rationalization" for higher R values.
I REALLY appreciate that this thread has turned around and become productive, and I value the more recent professional comments and critiques.
Erik
Erik, I have recently completed a house in an environment much like yours, 8600HDD, mostly sunny, in Utah. We designed the house using PHPP and other software. We have R32 subslab, shallow depth footers with R10 EPS under/around, R48 12" EPS wall and roof panels, with additional R20EPS added to roof. We got to 0.6 on blower door test. We have likely more than average amount of glass, however it is Serious' s 925 tunes for the different exposures. I am near net zero although we do use solar hot water. It turned out to be more economical for us to add PV instead of the additional required insulation, and that was 2 years ago, and PV has gotten significantly cheaper since.
Kevin,
Thanks for the comparison. I don't know what your square footage/TFA is, but I am guessing it is greater than my local code restricted 650. I ran a building with a higher TFA/volume in PHPP and, as to be expected, things got "easier." Also, if I am not mistaken, the solar PV does not affect the "peak heat load" (worst case) numbers in PHPP, only primary source energy. The hot water solar does help matters in this regard, but adds complexity and maintenance which I am trying to avoid. One of the other differences (I think) between your climate and mine ks that you have more sunny days, where as I have more cold, overcast (worst case) days. This affects the heat gain. Also is your project urban infill or available for full solar exposure? Would love to see images links if you have them!!
Thanks,
Erik
Erik, all your presumptions are valid, as this project was 3700 sqft, in semi rural infill on 10 acre lot. Website is http://www.omearahouse.com, email is on the website. I haven't update chapters on solar, my bad, i hope to have these up in a couple of months