Strategy for attaching 2×3 “service cavity” wall to exterior wall?

I’m building a house with a 2×6 “air sealed” exterior wall w/ OSB on the inside and then a 2×3 “service cavity” wall that is inside of the conditioned space and will not have any insulation of its own, nor any care taken to seal the penetrations into it.
The 2×3 service cavity wall is installed vertically and has a depth of 2.5 inches. In all ways, it looks like a “normal” 2×4 stud wall, just 2.5 inches deep instead off 3.5 inches.
The bottom plate is attached to my concrete slab with powder actuated nails.
But… how do I attach the rest of the service cavity wall to the exterior wall?
I originally thought I’d just toe-nail it on the top plate and maybe a few places in between. But these 2x3s are super lightweight and toe-nailing just blows through them like a bomb went off.
Some thoughts I have for alternatives:
1. Get some mending plates and connect the exterior and service cavity top plates together that way
2. Get some 4″ screws (or similar); pre-drill some holes; and just screw the service cavity wall to the exterior wall
3. Maybe try nailing through the 2x3s (even on edge) with 16d 3-1/2″ nails? Not sure what a nail would do going through a stud the long way…
What would you do?
GBA Detail Library
A collection of one thousand construction details organized by climate and house part
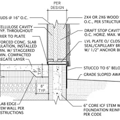
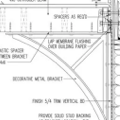
Replies
Kurt,
I have to admit I've never framed a wall with 2"x3"s, but is it necessary to attach the two walls? If it was an inner 2"x4' wall you would just build it like any other, attaching the top-plates to the trusses, or if perpendicular to blocking between the trusses. Is it because it is too flimsy that you need to connect it to the outer-wall?
There are two reasons I think I need to attach the walls together.
The first is that this house does not have trusses but instead rafters and ad-hoc dimensional lumber ceiling joists. The joists depend on the interior walls for support, so they can't be installed until the interior walls are in. The interior walls connect to the service cavity walls so they can't be installed until the service cavity is in. So the service cavity walls must be installed first and thus there's nothing else but the exteriors walls to connect to. I suppose I could just temporarily clamp them in place until everything else is up... but that seems a stretch.
The second (and potentially more important) reason is because I am planning on sealing the gap between the service cavity walls and exterior walls with tape. I think I need to or else the purpose of the service cavity is bunk since there will be a direct air path from the outlet openings into the attic. Since the gap between the walls must be sealed, that implies the walls must also be attached together.
I'm not sure I understand the entirety of the wall system you have in mind, but another thought is to connect the top plates of the two walls with plywood. This both connects them and creates the air seal, assuming joints are sealed/taped. This would be a more robust air seal than trying to seal the two top-plates alone together.
"The interior walls connect to the service cavity walls"
Could you just connect the interior walls to the load-bearing exterior walls, in a more traditional manner? It seems like the 2x3 wall should be relegated to serving as a service chase and not performing structural tasks unless it's really been designed to.
My thinking was this: if I connect the interior walls to the exterior walls THROUGH the service cavity, then the service cavity is essentially blocked whenever that happens. My goal was to keep it open as much as possible to allow for easy passage of electrical and plumbing lines.
Although as the design progressed, I realized that more of the electrical and plumbing was going to route through the attic anyway and mostly just drop vertically down to the outlet point... so it probably wouldn't matter.
Kurt,
Not to belabour the point I make in post #12, but it's worth taking to time to move from looking at the services as abstract "electrical and plumbing" and look at each wall in terms of what actually will occur there. Where are the drains going? Will any of them fit in a 1 1/2" service cavity? Will water lines? What actually is penetrating the drywall except an odd outlet on most walls? Where are the wiring runs. All these can be anticipated and known before framing, allowing informed decisions about how big the cavity should be, or whether it makes sense at all.
Ah, that's a great idea! I wish I had thought of that earlier in the design when I was trying to get another 1/2" of height -- this would have tied the walls together; effectively sealed them; AND given me might extra height.
Doing it now would add an extra 1/2" that would need to be accounted for in everything else that follows, alas. So I'll keep that in mind if I ever build another house. Heh.
I think you're making this way more complicated than it needs to be. Design your house so it stands with just the exterior walls and the bearing walls. Then plot your mechanicals out, and put service walls where the only alternative is running an HVAC duct or a DWV pipe through an exterior wall. You should find that's almost nowhere. Supply pipes can be easily routed and should be in interior walls anyway. Wiring takes up so little space there's no sense in not insulating around it.
Where you need a service wall attach it ceiling and floor. Don't be afraid to cut big chunks out of studs if needed, they're only holding the drywall up.
There's no need to attach to anything other than the joists above and the floor below.
Cut the bottom plate to length. Mark the location of the studs on it, and put it in place. Measure the distance from the bottom plate to each joist in case they aren't the same. Cut each stud to two inches less than the measured length (top plate thickness plus 1/2").
Assemble the wall on the ground. Nail through the top and bottom plates into the studs. Stand the wall up, and put a piece of 1/2" plywood between the top plate and the joists above. If your measurements are perfect it should fit perfectly. If you're human, shim as needed. Get the whole assembly square and plumb. Nail the bottom plate to the floor and the top plate to the joists.
If you've already nailed the bottom plate you probably don't want to take it out. Toe-nailing is the norm, I'd do it by hand with 10d nails. Blunt the tips to keep them from splitting the wood. It doesn't need a whole lot of nails, just two to keep the stud from twisting or sliding and the nails don't hold any weight. Once the drywall is on the whole assembly will stiffen up.
Kurt,
I like option 2. I ripped a bunch of 2x4's for ceiling strapping and found that #10 GRK screws went through the lumber without splitting it. I believe they are touted as "self-drilling" so no pre-drilling is needed. This should connect the walls pretty quickly I would imagine. You can countersink them so they are out of the way.
https://www.homedepot.com/p/GRK-Fasteners-10-x-4-in-Star-Drive-Bugle-Head-R4-Multi-Purpose-Wood-Screw-150-Pack-100141/203525216
I also experimented with mending plates. I found that I beat them up too much to be useful- at least with a framing hammer.
I used left over roof foam screws to build temporary staging planks, wound them straight through the 3 1/2 sides of 2x4 with no predrilling. 4 inch foam screws are probably 150 bucks a thousand.
SPAX screws are my favorite self drilling screws for wood. The modified torx drive they use is excellent.
This place has decent pricing, particularly on the LONG ones:
https://www.ultimategarage.com/shop/index.php?cPath=310_298
Also, why go through all the effort of a 2.5" deep service wall and not put a least some cheap batts in there? Have you considered mounting the 2x3's horizontal on 24" centers? You can leave gaps or drill holes to go vertical.
Matt, I'm not planning on putting insulation in there mostly because it's entirely unneeded. Recommended wall R-value here in Phoenix is R-13 and my wall construction as-is is going to be R-25 or so. Modeling in BEopt showed no improvement over R-13. So if I do have extra insulation, I'm more likely to throw it up in the attic, where it does make a big difference, even in my climate zone.
As far as vertical vs horizontal -- yeah, I struggled with that for quite awhile. There were pros and cons for both. I went with vertical in the end mostly because I could just attach any conventional outlet box to the studs without any special thought given. Attaching outlet boxes to horizontal studs seemed like far more of a pain.
Ahh, okay I am in the Northeast and have that mindset. You are better off pushing thermal mass than more insulation.
For horizontal studs, I think you can just mount the box horizontal unless that look bothers you. Unless there is code against this, I would have to check.
Also I just found this: https://www.homedepot.com/p/Slater-1-Gang-Horizontal-Plastic-Switch-Outlet-Box-PH122R/304234070
If you use 4” square boxes and mud rings, the orientation of the box (horizontal or vertical) doesn’t matter since the mud ring can be installed either way to get the device openings oriented the way you want. The mud ring only attaches to two diagonal corners, and it can be rotated 90 degrees easily while the box remains fixed.
Bill
The logic behind most service walls still eludes me. They double the labour, increase appreciably the materials and depth of the exterior walls, all to create a cavity, the vast majority of which will be empty.
I can see perhaps using them in targeted areas where there is a cluster of plumbing and wiring, but otherwise they seem a lot like using a hammer to kill ants.
Malcom, I'm sure you've mentioned this in some thread or another here on GBA, but I'm curious—if you don't mind me asking—what a typical wall stack-up you build/prefer looks like?
The other comment you made in the 'air sealing BS' thread indicating your preference not to build 'fragile' systems relying on no air-leaks, go me curious too. I seem to recall (maybe?) you mention applying rain-screen battens direct to sheathing, which would imply no exterior insulation?
Tyler,
My ideal stack up for the houses I design or build here is coloured by a few things. Our climate on coastal Vancouver Island is very temperate, and the vast majority of the sites I work on are south facing with views. Our building code also mandates insulation at what would in most jurisdictions be considered quite efficient levels. In an all electric house built as I describe below, the plug loads dominate.
So a typical project includes a trussed-roof with generous overhangs, 2"x6" walls with batt insulation and a rain-screen cavity, plywood for all sheathing, perimeter and sub-slab insulation, good air-sealing, and ductless mini splits with supplemental electric resistance heat. Because of the orientation of the houses, the desire for a lot of south facing glazing, and the good net-metering situation here, it makes sense to increase the efficiency of the windows, and make provision for solar panels over increasing the efficiency of the walls.
The only vulnerability of a house built like that here is a tendency of mold to discolour the underside of the roof sheathing, but in the absence of some other problem it doesn't cause rot. They are pretty basic but robust assemblies that can stand quite a bit of damage over time without it contributing to any failures, and importantly there isn't much that is unfamiliar to the average builder or sub-trade.
Okay, here is at least my thinking on the subject. Building a modern super energy efficient home requires it to be extremely air tight. Here in Phoenix, the most important aspect of that is actually the interchange between conditioned space and the attic -- attics are egregiously hot here so the stack effect is notable. One of the biggest air leakage components I see in my current (very not-energy-efficient) house is all of the many electrical outlets.
I built a home theater a few years ago and one of my goals for that was to be perfectly air tight, for soundproofing reasons. I did install outlets in the walls, which meant sealing them. It was tedious and error prone and not inexpensive. I spent the time and money to do it right and so it absolutely worked... but I just don't want to have to deal with that in the house I'm building.
My thinking, then, is that if I put in a service cavity that is already in conditioned space and just do one blanket air seal between it and the attic, then I can put outlets in the wall willy-nilly and never have to worry about any air movement. It will remove a lot of very precise tedium.
From the point of view of someone who might come in later to renovate or adapt a house, one built with a trussed accessible attic, a crawlspace, and service cavities like those you propose, would be a dream to work on.
but using a hammer to kill ants is fun.......
Keith,
I find watching birds eat them very satisfying too.
FWIW, I did some experimenting today on attaching the wall using the three methods I proposed.
1. The mending plates did work on the top plates, but they were a tad finicky. Plus, they are harder to use around doors and windows. Still, it is apparently an option.
2. Several people mentioned that they had success with screws and, indeed, those worked a treat! I used 3-1/4" 9x "Spax" self-drilling screws in my test and they did the job... but I would like them to a tad longer. I'm going to get some #10 4" screws tomorrow. I'll put one each on each side of the windows and doors and then a few on the top plate, where necessary.
3. Nailing almost worked but mostly didn't. Maybe if they were ring-shank nails? As is, they had a strong tendency to just pull out since even 3-1/2" nails only embedded 1" into the frame. This was the only option that I'd consider not working well enough to use at all.
Just throwing this in here, but it makes more sense to do a service cavity horizontally for ease of wiring. Your recepticles end up sideways. This one was a bit of a different project in that 2" of thermal break was added on the interior as the exterior was not touched. Wall is 2x6.