Sub slab detailing

I was planning on several inches of sub-slab gravel with a passive soil gas vent through roof covered with sealed poly vapor barrier under R-20 XPS with radiant tubes and a 4 inch concrete slab. Slab edges insulated by 1 inch XPS inside the ICF foundation walls. The soil is sand and glacial stone. My assumption was more sand was to be removed to allow for gravel but I just found out that the concrete crew brought in some of the sand as the sub-slab base. There is a perimeter drain of 4″ flexible poly wrapped in a sock to keep out the fines that drains into a sump. Does sand work in this set-up? Will water drain to the perimeter drain through sand and would there be any point to venting the sand for soil gas?
Second problem detail is the two footings running the width of the foundation that were supposed to covered with 2″ of foam before the bearing walls were put in. Thanks to the truss company’s advice, the builder deleted the foam so I now have untreated wood framing on the footing at the level where the poly vapor barrier is supposed to run wall to wall. How can I seal these for air and moisture? And, how do I wrap the sub-slab foam around wood framed walls? Naturally, the floor trusses, sub floor and upper walls went up before I could ask any questions about this detail.
thanks for your thoughts,
Don
GBA Detail Library
A collection of one thousand construction details organized by climate and house part
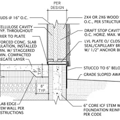
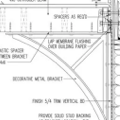
Replies
Don,
I'm a little confused. Is this a slab-on-grade foundation or a basement slab?
Martin,
Kind of half of each. It has 2 walls below grade - north and west - and walk-out on the other 2 sides with 4 foot frost walls that wrap around the below grade corners about 10 feet where the fill will taper to the walk-out level. (The building inspector wouldn't allow shallow, frost protected footings.)
Don,
I'm still a little lost here. Tell us again why you plan to put untreated wood framing on a concrete footing. That isn't usually done.
I, also, find your description confusing. And, though it's water under the bridge, shallow frost-protected foundations have been accepted by the International Residential Code (IRC) and should be allowed in any jurisdiction unless restricted in seismic or high-wind zones. Your sand/stone soil would have been perfect for this approach.
But sand is an acceptable sub-slab media if well compacted. While it isn't as porous as gravel and will retain more moisture, it should drain adequately to the perimeter drain and to the radon vent. Make sure the sump pit is a gasketed radon-proof version.
Any basement level wooden bearing walls should have been built on top of the slab. If this was not done, then I would demand that your builder remove them (using whatever temporary floor shoring is necessary) and rebuild them after the slab is poured. The sub-slab insulation and vapor barrier should be continuous and there should be no wood buried in the slab.
My response to Martin's last post didn't seem to get through. And I'm sorry I'm not better at describing this clearly. I didn't think the bearing walls on the footings were acceptable, especially without PT wood. Wanting to get things closed in before the weather gets worse, the builder decided to leaver the slab until later and get the walls closed in. I'm 4 hours away from the building site so things happen during the week while I'm working. From now on, I guess I need to be very specific about details as I thought the builder was on the same page for these details.
Robert, I do appreciate your feedback on the sand. We were planning on a gasketed sump pit. With the footing breaking up the sub slab area, I presume I need to tie the radon vent into the perimeter drain to give the soil gas a way to get to it.
On the history of the foundation, this is in Upper Michigan and Michigan was still under the 2006 IRC the last time I checked earlier this summer. they finished hearings to adopt the new code in June but I don't know which code verison or when it takes effect.
If the drain is inside the perimeter footings (under the slab) and terminates in a sealed sump container, then it can do double-duty as a radon vent if tied into a vertical stack through the roof. But an uninterrupted sub-slab air/vapor barrier is still necessary to control soil gas infiltration.
As for shallow, frost-protected foundations: Provisions for FPSF are included in the 2000 and 2003 edition of the International Residential Code (IRC). The American Society of Civil Engineers developed a standard, "Design and Construction of Frost-Protected Shallow Foundations", ASCE/SEI 32-01. This standard is referenced by the 2000 (by amendment) and 2003 International Residential Code (IRC). ASCE/SEI 32-01 is also adopted by the 2003 International Building Code (IBC) which allows FPSF to be used on multifamily buildings, houses four stories and above, very large houses, malls, schools, and offices.
Don,
Still trying to visualize this. If the examples of untreated lumber on the footings are wall bottom plates, then they should have been pressure treated. Using untreated lumber is a code violation, and the builder should fix this problem at the builder's expense.
If this is an exterior wall -- and not just a wood-framed wall on the interior side of a concrete wall -- then there should be sill seal under the bottom plates. Sill seal is required by code.
Martin,
Pictures would be easier for me but we have a 36 x 52 ICF foundation with 2 footings running the 36" direction. These were supposed to be covered with poly, R-20 foam and slab but the interior, load bearing walls were put in before the slab so are sitting on the footings, 8 inches below the final floor grade. No pressure treated wood used. I'm trying to figure out how to get an air and moisture seal and radiant tubes under the slab with 2 walls in the way. the builder is telling me he won't bury the walls in concrete but they will be wrapped in foam so they won't rot. I think we need to pick them up and put poly, foam and slab under them.
Donald,
You said, " I think we need to pick them up and put poly, foam and slab under them."
Absolutely. You should stop all work and all payment on the project until the builder remedies this properly. And then keep a close eye on him to make sure he doesn't take other irresponsible shortcuts.
I called him and stopped things yesterday and we are meeting Saturday.
More background on the frost protected foundation: when I was getting bids, I had several builders and 1 concrete contractor in the area tell me "no way, the inspector won't allow them" I figured I'd save the fights with the inspector for some of the upcoming battles like him insisting on a poly vapor barrier rather than push him on this. Maybe this should be a new Q&A: how and when does one decide to go up against the inspector to get approval to use energy efficient techniques that aren't common to an area?