Suggestions for a natural gas direct-vent fireplace that is super airtight?

We are building a custom home in central North Carolina where the builder will work with us to a certain degree to get the high efficiency, super insulated, air tight house I want to build. But depending on what it is, we have to work within the framework of their existing building methods and their preferred vendor list.
We want the house as air tight as we can get it while doing things in an economical, bang for buck way with simple, common materials. We’d love our blower door test to be below passive house standard, but aiming for as much under 1ACH50 as we can get without having to do anything too elaborate. Builder by default does some good things with air sealing. But they are only trying to get to 3ACH50 to meet energy star requirements. So we are hiring out additional resources to add additional sealing while under blower door test with smokers to try to get as close to or below 0.6ACH50 as we can with just closed cell flashing and caulking, etc…. Wanted to do AeroBarrier but they don’t have a dealer in the area yet.
So we are doing 9” thick double 2×4 wall construction with dense pack cellulose and an additional 1” of rigid XPS insulation on outside of OSB sheathing (builder does all their houses with the XPS. So just letting them include so this doesn’t require any re-training for their framers and window installers and siding guys to just leave it. And the extra insulation for included price is fine by us 🙂 hahaha). We are also doing raised heel roof trusses to get max blown in cellulose insulation all the way to the outside framing and Zola’s passive house level triple pane tilt & turn windows and doors. So ~r40 walls, >r60 attic. Primary HVAC will be American Standard’s 20 SEER variable speed forced air system with gas furnace (limited by builders preferred HVAC vendors). Systems will also include ERV and whole house dehumidifier and whole house humidifier to ensure rock steady humidity-controlled levels year-round. All ducting will be inside conditioned envelope thanks to mechanical room in Superior Walls walk out basement and 18” tall web trusses between each floor to allow ductwork to run in between floors so nothing has to route up into the vented attic (builder refuses to do sealed, conditioned attic).
anyways, with that bit of background out of the way, on to the point of my post and my questions….
The wife refuses to have a house without a gas fireplace in the great room / living room for ambiance, aesthetic, and for the few instances a year in the winter where she wants to flip the switch and lie there by the fire and get overheated/warmed.
So we are not looking to put in an actual old school open fireplace creating what amounts to a massive penetration into the air sealed house space, but rather a glass front sealed up direct vent natural gas logs “fireplace” that will pull its own external air for combustion and vent directly outside without leaking anything into our space or having anything about the assembly create air leakage and mess up the rest of our efforts at air sealing the house. This is not a primary heating source. Just an occasional use item. But I don’t want it to be a huge hole that destroys our blower door results while it sits idle 98%+ of the time.
I’d love to convince her to do an electric fireplace or some form of fake video display to create the same visual effects. But it won’t happen. So, I need to figure out how to give her what she wants without it resulting in a huge air sucking penetration that destroys the hard work we are doing to get a well air sealed, efficient home where we have tight control over the fresh air exchange.
With all that wordiness in mind:
1) What brands/models of direct vent or similar natural gas fireplaces are there out there that specialize in being tight air seal if installed correctly?
Or
2) is this a case where most any glass front direct vent gas fireplace can be made air tight if we just do the following XXX things to seal up the units and the venting pipes and hope we don’t run afoul of city inspectors?
I would appreciate some insights and suggestions. I know we are asking for trouble by introducing the gas logs and yet also wanting to air seal the house. But no amount of negotiating has worked to date re: switching to electric fireplace, etc. Thank you in advance for your assistance and suggestions.
GBA Detail Library
A collection of one thousand construction details organized by climate and house part
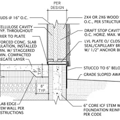
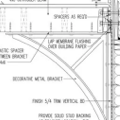
Replies
have you considered a ventless? if allowed in your area. no wall penetrations other than the gas line. great room /living room sounds like decent square footage, you have a controlled make up air system and occasional non primary heating source covers most considerations
I would never even consider a ventless fireplace in a super tight house. Ventless is really bad even in a leaky house. There is no way that a HRV/ERV system could deal with all of the combustion products produced. You would just be asking for serious health risks.
I don't have any specific products in mind, but others on this list might. From my experience with these units in general, I think the firebox and vent are going to either be pretty well air sealed or pretty easy to seal. The difficult part might be the thimble through the wall. These are concentric sheet metal cutouts, with air spaces on purpose so that heat is not conducted to the building framing. You're generally not allowed to use spray foam or anything else to fill the gaps, and that will make it very hard to air-seal.
the sheet metal direct vent setup is different from a condensing unit PVC setup. I would look into air sealing with a high efficiency pvc dv model
Thank you for this suggestion. I didn’t even realize there was a product like this. I found 2 options online, the Mantis line and a combo product from Nu-Air in Canada that I’m not certain is actually available to purchase yet.
I’m not sure the Mantis units are big enough flame window to satisfy, but going to look much closer at this unit. With it only needing 1.5” PVC venting it should be pretty easy to seal up around that penetration to the outside.
Are there other options in the condensing fireplace category to check out? Thanks.
I have a Heat & glow cosmo42 gas fireplace. It seems to be very tight. As a heating appliance it is NOT very effective, as a decorative item to set a mood it is great. I understand conventional style units do put out a lot of heat.
I did take the time fire calk around the flue pipe and make sure the fireplace is fully inside my conditioned space.
http://www.heatnglo.com/Products/Cosmo-SLR-Gas-Fireplace.aspx
Walta
H.T.,
First of all, can you tell us your name? (I'm Martin.)
Peter is right. You don't wand a ventless fireplace. For more information, see these two articles:
"Avoid Unvented Gas Heaters"
"A Ventless Gas Fireplace Doesn’t Belong in Your Home"
One other point: If you are planning to build a double-stud wall, you don't want to include any rigid foam on the exterior side of your wall sheathing. This article explains why: "Exterior Rigid Foam on Double-Stud Walls Is a No-No."
Thank you everyone for your replies.
I agree with the posts regarding ventless. I have zero desire to have combustibles,etc in my breathing air. I don’t think a ventless fireplace is permitted in new construction in my area anyways. I was looking to a direct vent with both the combustion air being pulled from outside and the exhaust fumes,etc being vented back outside and is fully separated from the air inside the house specifically to avoid having any of the combustion byproducts mixing with our breathing air.
Walter, thank you for the fireplace suggestion. I will look at it. I have a feeling the solution I'm seeking may end up being what you did; picking a good quality unit and then trying to find code compliant fire caulking that is permitted to be slathered all over every possible leakage spot and seal up things as much as possible that way. So I just have to find the specific products that are code compliant and the inspector will be happy with so it handles high temps without issue... kind of the gas fireplace version of mastic the HVAC guys uses to seal up ductwork...
Martin, thank you for your response. I’m Shane :). I apologize for my ignorance and confusion. But the article you linked (https://www.greenbuildingadvisor.com/question/suggestions-for-natural-gas-direct-vent-fireplace-that-is-super-air-tight) says:
“If you are building in Climate Zone 1, 2, 3, or 4, your exterior sheathing won’t ever get cold enough to have moisture accumulation problems. In those climate zones, it’s permissible to install 1, 2, or 3 inches of rigid foam on the exterior side of a double-stud wall.”
Where the house is being built in central North Carolina, I’m technically in climate zone 4. but the house is literally a couple miles away the border of the line separating climate zone 3 and climate zone 4. So with that in mind, the 1” of xps on top of the OSB isn’t a problem, right? The xps is sitting on the job site ready for framing to start. So if I need to address this, I definitely want to do it now before they attach it to the house! :)
Should I put something like Benjamin Obdyke Hydrogap housewrap between the OSB and the 1” xps rigid insulation just to be safe to allow some ventilation and drying and keep the non permeable xps from directly touching the OSB? I’m already planning to have the builder use the hydrogap on the elevation spots that we will have painted thin brick veneer sheets in lieu of stone veneer. It’s not a huge expense to just wrap the rest of the house in hydrogap to get the little air gap it offers if you think I really will have an issue with our double wall construction plus rigid insulation on the outside?
Thank you again everyone for your thoughts. I greatly appreciate it.
Shane
how did you address the dryer? is it in a mechanical room where it would not affect the air seal issue?
Apologies, I totally missed this post. We actually have 3 laundry areas in the house, one on each floor (second floor laundry room for the three bedrooms up there and any guest laundry from first floor guest suite, a stack in master closet for first floor master, and a laundry room in the basement that will be finished later when we finish the basement).
We have a 13 year old LG set that is getting moved to the basement laundry spot when we move to be used sparingly. If and when we finish the basement, we will using something like the Braun EV100 or a magnetic vent cover that many threads on here have recommended.
For the main part of the house, We intend to purchase new machines for our master and second floor laundry room and in both spots we are going with condensing ventless dryers so we don’t have to have dryer vent penetrations at all.
So we are solving the dryer vent penetrations by not having any :). Or at least we are going to try to not have vents. I’m not 100% convinced yet of the ventless dryer technology until we get one and give it a go....and have read many conflicting reports. So I’m having it piped right up to the point of penetrating the outside in the basement wall. If the ventless dryer works for us, we ar done. If it’s a failure we drill the vent out and switch machines and go to the various vent covers etc that try to seal up the penetration when not in use and we take the hit on air sealing I guess....
Hopefully the condensing dryer works for you. I was looking for ideas. Consumers are normally ahead of the market on good products. Hopefully you two find and enjoy a good firebox. We have a ng high eff mod-con tankless driving a 30 gal standing tank for domestic water. The tankless uses 3in PVC for its direct vent and it's in the mechanical room. The standing tank has an additional heating coil that feeds a second tank. That tank is for the hydronic furnace. Every bit of our system is blended custom, ( like the builders you mentioned). It shouldn't be this hard to find good products. We're happy with our existing home and neighborhood so we're trying to make improvements here.
My fireplace is not on an exterior wall. It is almost dead center of the house, so all I had to do was get the ceiling of the chase drywalled before the flue went in and 20 inches of caulking around the flue before the outside of the chase got drywalled. It was almost painless.
Even if you had an exterior wall just insulate drywall and tape the inside of the chase before the fireplace goes in. the only fire calk will be around the flue pipe.
Walta
Shane,
Your case is unusual, for a variety of reasons. You are correct that in your climate zone, the chance of damp wall sheathing is low, since your sheathing doesn't get very cold in the winter. So the 1 inch of exterior rigid foam, which greatly limits outward drying of the sheathing, is less risky than it would be farther north. And you're also correct that my published advice on this topic seems to allow the approach you are taking.
The history behind my advice to encourage rapid outward drying of wall sheathing on double-stud walls is as follows: Several field studies have shown that the moisture content of the sheathing on a double-stud wall increases during the winter to worrisome levels, only to drop when warm weather returns in April and May. Fast outward drying of the sheathing during spring weather seems to protect these walls -- admittedly, we're talking about cold-climate walls -- from rot.
In your climate zone, I suspect that the moisture content of the wall sheathing won't get as high in February as it does in Massachusetts -- but I don't know of any field studies to back up my suspicions. If my suspicions are correct, your walls will probably be OK.
All of that said, here is the basic question: Why are you adding 1 inch of XPS to a double-stud wall in Climate Zone 4? Without the XPS, your wall already has an R-value of R-33 -- and it's not as if you need a higher R-value than that in your mild climate. So why limit outward drying -- an added risk factor -- for such a small benefit (an additional R-5)? Especially with XPS, a type of foam avoided by green builders (because XPS is manufactured with a blowing agent that his a high global warming potential).
My advice: Stick with the double-stud wall, but get rid of the XPS.
Martin,
Once again, thank you so much for the reply. I appreciate your comments and knowledge sharing.
As I mentioned in my original post, the builder’s standard build practice uses 1” xps on the outside of all their houses. They have all the details of how to do the xps and trim out the siding, window details, etc. with the xps included. So rather than ask all his framers and window guys and siding guys to alter what they normally do and have been trained for, I figured just leave it there and enjoy the extra little bit of r value the 1” xps provides. The exterior 2x4 wall is the structural wall. This way, The only tweak I had to negotiate and convince the builder to do was adding the second 2x4 non structural wall to the inside to create the much deeper insulation space than his standard 2x4 wall cavity. His trim carpenters for interior finishes have to work around the deeper window wells and doorway cutouts. But that was an easier thing for him to price and sign on for than some of the more elaborate building enevelope designs I tried to get him to take on. I originally tried to get him to go for much more rigid insulation of the outside. But that proved too much for him even when I showed him your articles from this website on how to do window and door trim details and how to work around the siding issues. He didn’t want to have to teach his guys how to do things with thicker rigid insulation than the 1” he has been using. So we finally settled on this compromise of leaving the exterior essentially exactly the same and increasing the inside insulation space by adding the second framed wall as it more closely matched what he does on a normal home he builds. His insulation guys do dense pack cellulose as well. So he gets to use his normal insulation contractor. They are just doing lots of dense pack instead of fiberglass batts in the 2x4 cavities and could easily quote him the difference in price.
I did also get the builder to agree to my hiring out an additional crew that specializes in air sealing to come in after his normal air sealing guys and before they insulate everything. The builder is going to put the sheet rock lid on the second floor and then leave the house for a couple days. The crew will come in and do a blower door and smoke all the leaks. They are then going to caulk and flash with closed cell everything they can in the wall cavities, and focus especially on the rim joist areas and seal the attic/second floor transitions. Finally, they are going down into the 98% unfinished superior walls basement and seal up between basement and first floor. I will be finishing the basement within the next year, but wasn’t wanting to pay the $200 per square foot price the builder wanted for polished concrete, some sheet rock and paint down there. I knew I could hire out my own subs for a fraction of his quote. My music room for my stereo and the theater room are down there.. so it’s ok to wait and let me do that up right before I hire out the finish for a fraction of the price. I’ll worry about the air sealing of that space then.
I want the house as tight as possible so that we control the air quality of the house through the ventilation system, where we can filter the crap out of it. My wife has awful allergies and the pollen can be brutal here in NC. Instead of dirt and pollen and allergens being sucked in everywhere from outside with a leaky house, we are trying to be as tight as possible so the fresh air is forced through our array of HEPA filters and MERV filters so it’s as clean as we can reasonably make it and she has a place of relief from the bombardment of allergy inducing stuff she deals with every day.
Anyways, I hope that explains why there is 1”xps on the outside of the house. It’s to make things as consistent in construction steps to the builders other houses as possible. I’d love to have a builder that wants and encourages doing everything possible to build passive house or net zero or whatever. But unless we find an individual lot and seek out that specific custom builder, this was the closest th8ng we could find. We had the “restriction” that we had to build our house in the specific neighborhood that we chose. So we only had 6 different builders signed up to build in this custom neighborhood to choose from. Our builder we chose was the only one of the six that would customize things hardly at all (I don’t consider going to a design center and pick one of 5 options for kitchen faucet a “custom” builder :) hahaha). So it’s a balance of trying to find ways to get what we want that this builder would agree to do balanced against trying to do as much of his standard building practices as possible to keep the builder comfortable and on board.
As to why I’m doing double wall construction and wanting such high r value, I may be showing my ignorance... but just like growing up in Canada was about keeping the heat in with highly insulated house (or is it keeping the cold out? Potato potahto, tomato tomahto?), living in NC is the same, just in reverse. Here it’s keep the cold in (or is it keep the heat out) for the majority of the year. I don’t want to pay to run the A/C nonstop if we can insulate the house well enough that it stays cool longer... and when we do get the NC version of winter with temps in the 20s,30s, and 40s then my super insulated house will stay warm much longer, meaning the hvac runs less and uses less power, than the poorly insulated houses right beside mine..... meaning much lower power and gas bills.... at least that’s my theory... if I’m missing something, I’m happy to learn to correct my misconceptions. But I can’t see how a well insulated and air sealed house isn’t a benefit in all the different climate zones?
Edited to Add: I tried to take everything into account that I could within the limitations the builder placed on us to help the house not just up the insulation level. We chose a color scheme for the house (white and light grey) so that we could do a light color shingle. Our Shingles are actually energy star rated “Silver Birch” color. The roof decking is radiant barrier style decking to hopefully reflect back as much heat as we can and not even let it get in. Southern facing side of house has extended porch and overhangs to provide more shade and limit direct sun through the windows and doors. I made sure we could keep all hvac ducting out of the attic and inside the conditioned space. I’m still working on the builder to let me use another hvac vendor so I can do high SEER ductless split systems instead of Heat pump style forced air and all that ducting. But if I’m forced to use his guy, I’m at least trying use the best system they offer in American standards 20 SEER variable speed unit. I just can’t stomach the quote I got as their 30 year partnership means competitive pricing went out the window long ago and I could practically do an entire geo thermal system from other vendors for what these guys want for a compressor and air handler.... but I digress.. The builder wildly underpriced the cost to do double stud walls and dense pack. So it was a no brainer to do it and increase the insulation in the house along with the other tweaks I tried to get incorporated to make the house as efficient as possible.
Thank you in advance for your thoughts. As I said, if encouraging drying of the OSB by keeping the xps off it directly touching is something I should be doing, I want to look into it before they start framing the house in a week. Putting something up like a dimple house wrap like Hydrogap or equivalent can likely be easily done without too much stink by the builder compared to changing things at the last minute to completely eliminate the xps. I’d prefer to try to keep the xps because of the reasons mentioned unless it really will cause a problem with the overall assembly. Thank you again for your thoughts.
In understand that the XPS is already on site, and making a change now may be difficult. that said, what about changing it to EPS? They can use the same construction details, but EPS is cheaper and more vapor permeable, allowing faster drying to the exterior when the weather is warm.
Shane,
Good luck with your decision. Ideally, a double-stud wall doesn't have any exterior rigid foam, but in light of your mild climate and the attention you will pay to air sealing, I think the risk of any problems is low.
You'll have to decide how to proceed -- and I'm sure that your decision will depend on negotiations with your builder, and may depend on whether the exterior foam has already been purchased.