Surviving winter before demolition

Hi, I have a 180 year old house in central MA, zone 5 that my parents used to own and mom still lives in which I initially wanted to renovate so she can stay there. I had structural engineers assess it and they advised it would be smarter to demolish and rebuild. A couple folks here on a previous post also cautioned about this potential. There are big structural issues before we even get to the air sealing and insulation stuff and it would probably never be as efficient as I want or that is sane. So, I’m looking into demolition, new foundation (same walk out basement with lots of above grade room) to be finished living space this time and interested in a high performance 800-900 sq ft or so modular unit to put on top to equal roughly a 2 story 1500 sq foot place.
– I’d love any thoughts on good modular companies / units up to the standards prescribed on this site.
– How do I save the old growth wood timbers all over the house and mitigate demo costs by doing so?
– Could you recommend a way to cordon off part of the main floor to squeak through the winter using far less energy? I won’t be able to do any work till after winter. Is there a way that people do this with building materials like lining the room they’re staying in with taped polyiso etc and only heat that part to a livable temp to keep warm during remodeling/construction?
I’m quite sure the wood stove will keep the pipes safe as has been the case for decades. But the electric heat helps make rooms livably warm (not just above freezing) and can get astronomical and I’d love to do some interior temporary unfinished air sealing/insulating to get through the winter using far less energy before demolition. I’d appreciate any thoughts.
GBA Detail Library
A collection of one thousand construction details organized by climate and house part
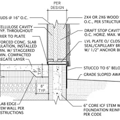
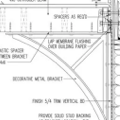
Replies
Google is your friend. Do searches for “passive prefab” and “recycled lumber Massachusetts” (or New England).
Depending on the condition of your timber frame (and original flooring and sheathing, if any), you should be able to get somebody to deconstruct and take away your house once the siding, lath, plaster, etc. has been removed. Conceivably you can get some money for it. At the very least, it probably won’t cost you anything. Obviously, be aware of lead paint risk during demolition of walls and such.
If by “save” you mean re-use for the new house, that is very likely a pretty expensive proposition.
Unless your timbers are extraordinary don't expect a big financial windfall. If it's 180 years old that's circa 1841, depending on where you are in New England by then they were using balloon framing and dimensional lumber, most of it is likely to be 2x which has nominal value. Disassembly takes a lot more labor than just knocking it down and carting it away.
A piece of timber that's 12x12 and 30 feet long has real value. A piece that's 2x4 and 8' long, not so much.
Thanks for your insight. Yeah, that’s the thing I have several 10 or 12x’s that are between 25 and 40 feet long - The entire original frame. It’s built on a hill and walk out basement so the timber framing starts at the top of the basement above grade brick wall.
I know that demolition is the easier less expensive way to go but the thought of just trashing old growth lumber and then the embodied carbon stuff seems tough. Plus it seems that that lumber would be worth not an insignificant amount.
Generally cordoning off part of a house doesn't save much energy, because interior walls don't have much insulation. The energy required to heat a house isn't determined by the floor area or the volume, but by the insulation level and area of the exterior envelope. Cordoning off part of the house doesn't change the exterior envelope so it doesn't change the heat loss by much.
Right but I mean creating an insulated envelope on the inside of the walls, the largest one being an exterior wall, of just a small part of the house like one room to get through the winter. Using taped polyiso as one example for more air sealing and for thermal conductive heat loss protection.
If I were looking to build a 1500 square foot house I would go with two stories above ground, a basement, and a 500 square foot footprint. Basements are expensive to build and the space they provide is never as nice as above-ground.
Yeah, it’s a walkout basement in a hill with the whole 35 feet of south facing front wall above ground and open and the door and windows get straight up bathed in sunlight all day, so it’s solid living space if built like part of the house and not a cellar. The foundation on exactly half the house (above grade part of basement level) would only go up a couple feet (stepped along with the hill grade) and the wood framing would start unless we decide to ICF or something for the whole basement. The hole is already in the ground and I need to do a new foundation in the hole anyway if I’m going to do anything at all. So I figured I could buy less modular on top and use the bottom floor as living space since it has to be made regardless.
Not to be a gloomy Gus, but when I hear about a foam-lined room in a building heated by wood my first thought is you better be on good terms with your neighbors, because that's who the news teams from the local Fox affiliate is going to interview when the firefighters pull your corpses out.
I think the simplest things is just going to be to move out a few months earlier than planned.
This was really great to read and truly made me belly laugh. I was thinking of doing this well away from the wood stove but, I hear you. Yours and walt’s comments seem clear that I should bail on the squeaking out another winter or just deal with one more year Of the same.
Help me understand your goals.
Do you want to find a way so your mother can stay in the structurally unsound cold drafty house for one more winter and then tear it down in the spring?
I do not think it is possible to recover the cost of building an insulated room in the house from the reduced fuel usage of a single winter.
Sound like a terrible way to live. I say move her out now but something tells me she is not on board with the rebuilding plan and is not moving out in the spring or ever.
Walt
Thanks for your reply Walter. She wants to stay there but is actually fine with rebuilding it or moving in with my aunt who just lost her husband too. Moving would mean a new job for her is all. I was thinking I would be the one to stick out the winter, not her. And continue build planning. I travel often working media production stuff and am fine with sinking myself physically into solving the issue with the house and not have an extra housing bill while im at it due to staying there. But while I’m not looking for miracles, it seams there are no good options for energy consumption mitigation this winter.
It's really common for people to live on-site in a camper during construction. If it's a neighborhood where that won't cause a problem with the neighbors. At the end of construction sell the camper, you'll probably get close to what you paid for it. Although I hear that due to COVID campers are hard to find right now.
I'm building a house in Washington, DC right now. One morning there was a Winnebago parked on the street in front of the site (covered in bumper stickers). DC tends to attract the crazies from around the country so I just shrugged. Later that day I had a meeting with a subcontractor, and while we making small talk he pointed at the camper and said, "That's smart, living on site to keep an eye on things."
Later that day I talked to the guy who owned the camper, he had driven from out west -- I think maybe Idaho -- to come and protest. Nice enough guy, was gone the next day.
Oh man, that’s a cool story. I know exactly what you mean. Used to go to DC all the time and seen em around the country. And the Idaho guys had a good idea it seems. I’ll check out campers. Any ideas about cold weather Ones? Maybe I could rent one. But my guess is that it would probably be about the same as getting hotels on real cold nights.
Nobody seemed to ask this but how extensive are these structural repairs and are they definitely not repairable. I know it would be impossible to seal this home to the level of a modern home but this site would help you get the best with what you got. Unless the house is impossible to fix which it sounds like it is by your post I would think the energy savings would not equal rebuilding an entire house.
Hi Hammer, ha, well the house was built in 1840 as a cape. Sometime before 1988 when my parents bought it someone converted the attic top floor to 3 bedrooms by putting in a full dormer so the back/north side is very low slope roof. Half the top floor ceiling is currently torn out and you can see the under side of the roof and the structural engineer could see how “they did it wrong”. Never put a ridge beam in so once the original triangle truss system was removed when they put the dormer in, the ridge beam would’ve been needed to properly support but wasn’t there so for decades the front original steep slope of the roof has been pushing the middle story walls out. And the 12x12 40 foot long beams that are on top of the middle story walls and bottom of the roof rafters (would be a top plate in today’s building) are showing this w/cracks and outward and rightward movement evidence. When you’re on the middle floor looking at it you go “why’s it doing that” and then the top floor tells you why. Add to that the walk out basement above grade brick wall below that needs to be totally replaced. Oh and most of the huge 40 foot beam that is the sill at grade level in the back (south side) is rotted. New slab for about 75% of the bottom floor/walkout basement is needed because there never was one also. And on the main middle floor there’s a cross beam that wasn’t supported properly decades ago (they think load bearing walls were taken out) and is sagging and in the process of failing. The fact that it’s an old growth tree log is probably the only thing saving it.
So. It appears that trying to fix these things only to then try to do the energy retrofit stuff only to hopefully hit code most likely seemed like a bad option. The engineers said that if there was one of these problems then yeah, but the opinion was that there’s not a lot to save in terms of sound building status or whatever. The materials though, i can’t imagine just sending it to a landfill.