Taping of Roof Sheathing / Wall to Ceiling Vapor Barriers

We building in climate zone 6A. We have planned unvented cathedral ceilings and we are planning to do 4″ (or maybe just 2″ depending on cost) of closed cell spray foam applied to the underside of the roof deck. We are then going to net and blow in fiberglass to the remainder of the cavities between the 16″ TGI’s.
I’m planning on the closed cell foam being my air and vapor barrier on the roof. On the walls the my air barrier will be the taped sheathing and the wall vapor retarder will be latex paint.
Two questions:
1) Should the outside of the roof deck sheathing be taped just like the walls?
2) How do I connect my wall vapor retarder (latex paint) to my roof vapor barrier (closed cell spray foam) or is it not necessary?
Note – We are planning tongue and groove interior finish on a few portions of the ceiling – if that makes any difference to your answers.
Steve
GBA Detail Library
A collection of one thousand construction details organized by climate and house part
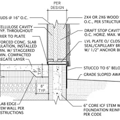
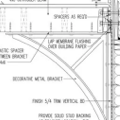
Replies
Steve,
In zone 6 you need at least R-49 to meet code requirements for roof insulation. In a flash-and-batt situation in that climate zone, to prevent moisture accumulation on the inside face of the foam, you need at least 51% of the R-value to be in the foam. That means, at minimum, to meet code, you need R-25 foam and R-24 fiberglass. Despite exaggerated claims by some foam manufacturers, figure R-5.6 to R-6 per inch of foam--so you need a minimum of 4" of closed-cell foam. If you chose to build to less than code-minimum standards, it’s important to maintain the right proportion, or to err on the side of additional foam.
If you plan on filling up the 16" TJIs with insulation, figuring R-5.6/in for foam and R-4/in for fiberglass (it varies with product), you would need about 7" of foam and 9" of fiberglass to balance out at about R-36 each, or R-72 total.
With your plan to install boards on the interior, these ratios are even more important. You should consider adding painted drywall or a variable-permeance interior membrane for moisture control.
As for taping the roof, it depends on the situation; it’s probably not necessary, but it's a good belt-and-suspenders approach, as foam can pull away from framing over time, leading to air leaks. It’s rare but it happens. A lot of builders like taped Zip sheathing on the roof, because it dries the house in quickly.
It’s not critical to connect your interior vapor retarder to your roof vapor retarder, because not a lot of moisture moves via diffusion—enough to include a vapor retarder of some sort, but not enough to worry about small gaps. Where small gaps DO matter is in the air barrier (also called the airtight layer or pressure barrier). At your roof, this would be either the spray foam or taped roof sheathing. What is your wall assembly? Are you planning for the wall sheathing to be the air barrier?
For more information: https://www.greenbuildingadvisor.com/blogs/dept/musings/how-build-insulated-cathedral-ceiling
Michael,
Thanks for the reply. My off the initial off the cuff target for the average roof assembly insulation rating was R60. I'm concerned that 7" of closed cell foam in a roof area of about 4000 sq.ft is going to be cost prohibitive. I wasn't thinking about the ratios of closed cell foam to fiberglass to prevent moisture on the foam. I could end up going with say 12" TGI's (more of them for structural loads) and then I'd need less foam.
I remember my insulation guy telling me his netted fiberglass is about R-4.8 per inch but I don't remember his closed cell foam number. Using your 5.8 for foam then if I use 6.5" of fiberglass and 5.5" of rigid foam then I get a total of about R63 but it is about a 50/50 split. So I'll have to tweak things.
I have an excel spreadsheet set up to calculate the average R value of the whole roof (accounting for thermal bridging of framing), it also calculates the temperatures at various interface points. I'm using an interior design point of 70F (conservative as we have our heating set at around 65F). Exterior design point I'm using the average temperatures of the 3 coldest months averaged from the closes ASHREA source typical of my climate. I assume my goal is to keep the interior of the closed cell foam above the dew point of 70F air at about 40% RH, which IIRC is about 45F. Which is quite warm!
This is without consideration to having a 18" of snow sitting on the roof (we have a low pitch 2.5/12 roof). Considering the snow then the temperature of the underside of the foam will be even colder.
If I were to just blow in fiberglass and not use spray foam (which is the typical roof construction method here) then the temperature of the underside of the sheathing will be well below the dew point and condensation will form on that. Why are we concerned with condensation on the underside of the foam and not on the roof sheathing? Surely any thickness of closed cell foam under the sheathing is better than none at all? Same as any exterior rigid foam on the walls is better than none at all, right?
To answer your question on my wall design. I'm planning from inside to out on a 4x6 stud : Latex paint, sheetrock, blown and netted fiberglass (5.5" @ R4.8/inch = R26), sheathing (probably OSB), Tyvek house wrap, 2" of rigid foam (probably XPS ~ R5/inch = R10) then exterior cladding will be a mixture of hardieboard siding, eifs stucco and rock. the siding will be installed using 1x3 furring strips over the foam. The EIFS I do believe has it's own foam insulation so I'll not need the rigid XPS there. I'm still researching the rock installation details.
The wall air barrier is the taped sheathing, the vapor retarder is the interior latex paint and the water barrier is the Tyvek. This seems like the standard approach for exterior foam walls.
Steve
Steve, R-60 is a great target in zone 6. Correct, smaller TJIs would mean you could use less foam. The exact number depends on actual product specs (beware of marketing claims--I've never heard of fiberglass being over R-4.2/in!)
The new, HFO-blown closed cell foam supposedly stays at a relatively high R-value of 6.5/in or so for a long time. Conventional brands may advertise R-7/in or more, but they offgas to R-5.6 to R-6 over time. Plus their blowing agents are potent greenhouse gases (aka carbon polluters) and best avoided.
It's great that you are doing your own dewpoint calculations. Every situation is different, of course, so it's always better to err on the safe side. You're correct that 70°F air at 40% RH will condense at 45°F. The R-value of snow varies but R-2/in is a reasonable assumption--so 18" is helping you out for sure.
It's a code violation to install air-permeable insulation, such as fiberglass, without roof ventilation, for the exact reason you note--moisture can accumulate at the roof sheathing. There are plenty of examples of this assembly that have worked ok, but also many others that have failed.
After writing an article on flash and batt insulation for Fine Homebuilding magazine a few years ago, I had several people contact me asking why they had liquid water on the face of their foam. In all cases it was either not enough foam, or they were building during winter and had not installed a vapor retarder, so relatively warm, moist air was reaching the surface of the foam and condensing. If you want to create a water distillation feature in your ceiling, go ahead and install a thinner layer of foam than recommended! A very well-done, variable-permeance membrane at the interior (Pro Clima Intello or Siga Majrex) can make this a safer assembly, but it does not meet code, and needs to be perfectly done.
If you care about the environment, I would suggest a different product for exterior insulation. Polyisocyanurate is the usual choice, and EPS can work well; both have blowing agents that are orders of magnitude less damaging to the atmosphere than XPS.
As for the airtight layer, if you're going with an unvented roof assembly, I would just connect the wall sheathing to the roof sheathing. The Zip system makes it all easy.
I -read your link again to refresh my memory of it. Doesn't the ratio of 51%/49% foam/blown only apply to rigid foam boards applied on top of the sheathing. With spray foam applied under the sheathing then I don't think there is such a restriction (don't have access to the codes right now).
I thought the concept was that with exterior rigid foam then you don't want to use closed cell foam sprayed on the interior of the roof sheathing? Quote from the article
"First of all, you can’t use air-permeable insulation (for example, fiberglass batts, mineral wool batts, dense-packed cellulose, or blown-in fiberglass) to insulate an unvented roof assembly unless the roof assembly also includes a layer of air-impermeable insulation (either spray polyurethane foam or rigid foam panels) directly above or directly below the roof sheathing."
It was my understanding that when you use exterior rigid foam then the ratio of exterior foam to interior vapor permeable insulation becomes important because vapor can reach your sheathing, condense and rot the sheathing. However with closed cell foam directly applied to the underside of the sheathing vapor can never reach the sheathing, so the sheathing will not rot?
Maybe I'm misunderstanding and I'd really appreciate any clarifications. We're planning to go to engineering this week and I thought I had this stuff straight in my head which is scary to think I might need to make a design change now I've frozen the design :(
Steve
Steve, check out R806.5 here: https://codes.iccsafe.org/public/document/IRC2015/chapter-8-roof-ceiling-construction. The concept is the same whether the vapor-impermeable insulation is above or below the sheathing--you don't want moisture accumulation at the condensing plane, whether that's sheathing or foam.
(A confusing aspect to Table 806.5 is that the values they list for condensation control assume code-minimum total insulation. Not explicit in the code, but frequently discussed by those of us who specify building details.)
Michael,
Looks like we posted at the same time. Thanks for the clarifications. I was steering away from Polyiso because it was my understanding that it loses a good% of it's thermal properties in cold conditions (which we are in). I originally planned EPS foam but I was going to have to go with 3" of EPS and trying to minimize window sills my builder and I settled on XPS. Although that's not set in stone.
Is it possible to have flush mounted windows to the exterior if the WRB is the Tyvek applied to the sheathing? I was worried about installation details in doing that and water management around the windows.
As for the insulation contractors R4.8, he said with his netting and density that's what he achieves. How do I know if that's BS or not?
Steve
Steve, polyiso does lose R-value in cold weather, but as you move through the wall assembly you pretty quickly gets back into a stable zone, so it's not a major concern if you are installing a few inches on the exterior. XPS ages to about R-4.2 to 4.4/in, despite being advertised as R-5/in. Or you might check out Amvic Silverboard Graphite--it's EPS impregnated with graphite, remains at a steady R-5/in, with relatively benign blowing agents, and has a sleek foil facing.
Yes on the windows; you would just need a way to extend the window openings, sometimes done with plywood window bucks wrapping the interior of an oversized rough opening, or with 2x furring nailed to the face of the sheathing. Or a relatively new product called Thermal Buck, made specifically for this situation. You do need to be careful with detailing flashing. There are a lot of high-quality options to choose from these days. I like products by Pro Clima, Siga, Protecto-Wrap and Grace. If you search here, or ask a separate question, you will find lots of ways to accomplish this.
Perfectly dead air is R-5.6/in, so that's the highest any fibrous insulation can reach. (The blowing agents in foam are less conductive than air, which is why their R-values drop as the blowing agents dissipate and are replaced by air.) The solid portion of any insulation is conductive. BIBS, the best-known blown-in fiberglass system, claims R-4.23/in in their data sheet (http://www.bibs.com/overview/bibs-original/). Even the densest fiberglass and mineral wool batts are R-4.2/in. I would ask your insulation contractor for data sheets showing tested values using the ASTM C518 process, preferably with the third party testing agent listed as well.
Great discussion Michael. Thank you for the guidance.
IIRC the other item putting me off polyiso was that it's not a dense as XPS or EPS and so when you hang your siding off of it using furring strips and long screws then it's not as rigid, relaxing somewhat reducing the axial screw load and thus reducing the friction portion countering the siding downward force making more of that load hang on the fastener.
The discussion on roof insulation ratios between vapor permeable and impermeable insulation has me worried about my wall. Do I need to keep the 51%/49% ratio in the wall for the same condensation reason? Was my statement that any foam on the exterior of siding is better then none, a false statement?
Steve
For walls the ratios are much lower. This is because roofs run much colder than walls on clear winter nights radiating into the night sky, with shingle temperatures well below the outdoor ambient air temperatures, often reaching the outdoor dew point temperatures. Walls tend to track the air temp.
For a zone 6 location a ~35% or higher ratio works for walls, but it takes 50% or higher for roofs.
See TABLE R702.7.1:
https://up.codes/viewer/wyoming/irc-2015/chapter/7/wall-covering#R702.7.1
A typical 2x4 wall has R13, and code specifies a minimum of R7.5 of the sheathing, for R20.5 total. R7.5/R20.5 = 37%
A typical 2x6 has R20 cavity fill, code specifies a minimum of R11.25 exterior to the sheathing, a total of R31.25. R11.25/R31.25= 36%
Of course more exterior insulation is better- those are minimums, not optimums.
XPS starts out as R5/inch, but falls to R4.2/inch @ 75F mean temp through the foam (the test requirement for labeling) as it slowly loses it's HFC blowing agents over time. At 40F mean temp through the foam layer it'll be R4.5/inch or better, even when fully depleted of HFCs. So at 2" you're looking at R9+ performance at outdoor temperatures that matter from a dew point control point of view, which isn't quite enough to get away with standard latex on the interior.
Using "vapor barrier latex" primer brings the paint layer down to the Class-II vapor retardency, which in most cases will be good enough when you're at 80% of the exterior R needed for dew point control.
Steve, most rigid insulation is available in different compressive strengths, but sometimes you have to special order it. What they offer at big box stores is the least-dense they can sell. I think you'd be happy with any product with a compressive strength of at least 20 psi, and maybe 15 psi.
There are some other discussions on here about fastening through thick foam. There are lots of strategies, but it's good to think about them ahead of time!
Thanks for the link Dana, I'll have to double check my calculations on the wall and verify my ratio's and temperatures.
Michael,
My insulation guy confirmed he is using BIBS insulation. He also said that our local county has an approved exception to allow an unvented roof using only BIBS insulation as long as it is combined with a vapor barrier on the inside, some kind of nylon sheeting that is a smart vapor membrane.
Just because code allows it, it doesn't mean it's the right way to do it. However if I were to go with the closed cell spray foam under the roof sheathing it comes at a very premium price. For my roof the quote using just BIBS and membrane is about $15,000 but using BIBS with only 4" (ref the ratio discussion above) it is coming in at about $24,000. 7" of spray foam and I might just have to rob a bank. I'll have to look at a smaller TGI. By the time I add my exterior foam and installation costs I'm in the $45,000+ area just on insulation alone.
I guess if you want something done right I'll just have to open up the wallet. The wife will kill me when I tell her she can't have nice things inside because I blew all the budget on insulation :)
Months ago I installed cheap hygrometers in my current house to look at my "human" generated moisture. Most of the rooms are around 30% to 35% RH 95% of the time. The bathroom right after a shower goes up to about 75% with no extractor fan and drops back to normal in about 3 hours or so. With our air being drier up here in the rockies maybe we've got away with poor roof design thus far.
Steve
> For walls the ratios are much lower. This is because roofs run much colder
You will find Lstiburek's much different explanation of why below.
"If you compare the ratios in Table 1 and Table 2...."
https://buildingscience.com/documents/building-science-insights/bsi-100-hybrid-assemblies
So I ran my roofing analysis again based on my location, see the attached PDF of my excel calcs. BTW I welcome feedback and criticism of my analysis.
I went down in size from a 16" TGI to a 14" TGI.
I ran 5" of closed cell at 6.2 per inch - R31
9" of BIBS fiberglass at 4.18 per inch - R38
Total roof section is about R70 or 44% (requirement is 51%).
However I end up with a temperature on the inside of the closed cell spray foam of 43F. When compared to dew points of 39F and 46F for 35%RH and 45%RH @ 68F air then it seems like a good balance between cost and functionality.
If I assume a 6" snow load then the temperature of the inside of closed cell spray foam becomes 47F.
The analysis is fun.
To meet the 51% ratio requirement I could just use crappy fiberglass insulation. If my fiberglass insulation is only 3.1 per inch then I get 51% ratio. I get a whole wall of R60 (which was my initial target) and the underside of the closed cell spray foam is now at 46F.
It seems counter intuitive to use crappy insulation but it meets the ratio requirement and the code.
Thoughts and discussions?
Cheers,
Steve
The attachment didn't go, trying again:
The average temperature at the roof will be measurably colder than the outdoor air temperature due to radiational cooling on clear nights, when the surface of the roof will be closer to the outdoor dew point, than the outdoor air temperature.
Download and learn to use the WUFI Light 1-D freeware for this analysis.if you're going to be under the lRC prescriptives.
https://wufi.de/en/software/product-overview/
it should be a good deal less expensive to install a vent channel in the TJI's by fastening a solid, permeable material - 2" EPS or plywood will work - to the underside of the top flange, tape the horizontal seams and caulk or foam the edge joint. Then you can fill the rest with enough blown in fibergalss or cellulose to reach your R60 goal. You can use ripped scraps of foam in the center of the vent cavity to stiffen the vent channel material. A good ventilation channel eliminates any worry about where condensation will occur.
Have you started construction yet? Wouldn't a vented, raised heel scissor truss roof have been cheaper and easier? Dump two feet of cellulose on top.
I agree with Bob and Stephen--unless you're in a high-wind area, a vented roof is simple and safe. You can do it with TJIs, or use either scissor trusses or parallel chord trusses, eliminating a ridge beam.
We have not yet started construction. We are in the final design stages and expect to go to engineering next week.
Stephen, how thick would our 2.5/12 pitched single slope shed roof have to be to use a vented raised heel scissor truss? I'm open to all "cost effective" options to get me to the thermal resistance value I need.
Our longest length of roof is 42', will we be able to get enough air flow through it to make it a vented design?
Bob,
Your method sounds like a good idea for making a vented roof with minimal impact to our current design. With your method though there would only be span-wise flow of air as air wouldn't be able to circulate between the cavities. Do you think 1-3/8" gap is enough to vent a 42' long 2.5/12 pitched roof?
I'm not sure I understand your comment about using ripped scraps of foam in the center of the vent cavity? Are you thinking of preventing sagging of the foam between the TGI's by supporting it from below using a scrap piece held in place with the sheetrock?
Oh I just had a thought, are you talking about scraps put above the the foam to prevent the foam from being pushed up by the insulation and touching the underside of the roof deck? Is plywood really permeable enough for this?
Dana,
I didn't think about the radiated heat loss from the roof. You're right it is probably quite significant and should be accounted for.
Steve
> Was my statement that any foam on the exterior of siding is better then none, a false statement?
Yes, warmer sheathing is better and as little as 1" can work well, even in zone 6.
https://www.nrel.gov/docs/fy14osti/60143.pdf
https://buildingscience.com/sites/default/files/migrate/pdf/BA-1313_Moisture%20Durablity%20with%20Vapor%20Permeable%20Insulating%20Sheathing.pdf
JON_R: Both of those links point to analysis of VAPOR PERMEABLE insulating sheathing. The Building America study stipulates that there must be the minimum ratio for dew point control in winter, but is looking at risk to the sheathing from exterior moisture drives of reservoir cladding when the exterior WRB and insualtion are high-perm.
Foam is not (very) vapor permeable. Even 1" of unfaced Type-II EPS is at best semi-permeable, a bit lower-perm than interior latex paint on wallboard.
Steve: The combination of radiational cooling and the low permeance of roofing materials (=zero drying toward the exterior for unvented roofs) are both factors for why there is a different prescriptive ratio for walls and roofs in the IRC.
Dana,
You eluded to it in reply to Jon - ref wall construction - What your saying is I could be making things worse for the wall design by adding less than code "ratio" of exterior foam to my wall (my foam R will be greater than code requirement of R-5 but the ratio might not be per the spirit of the code). Because the foam is not vapor permeable and it is mounted against the Tyvek which is mounted against the sheathing then even although Tyvek is vapor permeable the sheathing can't dry to the outside because of the low permeance of the foam.
So with latex paint class 3 retarder on the inside and foam on the outside how do these walls dry? I see lots of them going up everywhere around here. that and double studded assemblies.
Because I'm trying to achieve R-30 or greater on the wall and code requires R-20 + R-5 continuous I'm making it harder for myself requiring much thicker exterior foam which then makes siding attachment harder and installation of windows more difficult.
Reference your roof/wall/code comment, I fully understand.
Jon,
The building science document talks about vapor permeable insulation and moisture driving inward through the insulation through the WRB to the sheathing. Does that mean that using EPS or XPS in 2" or more where the permeance is much less than mineral board will prevent this inward driving of moisture to the sheathing?
Reduces, not prevents and even 1" of exterior foam has this effect.
If anyone has data showing that 1" of exterior foam (note that facers are not foam) combined with the right amount of interior perms makes a wall perform worse than 0", let's see it.
Building Science writes: "Vapor-permeable exterior insulation, such as mineral board or expanded polystyrene foam, are one such product that may be used to achieve these benefits."
Also note that they show a wide variety of external perms (using the WRB). Low perms (1 to 2 as is likely with foam) work well and typically only high external perms (> 10) are a problem.
2" performs better in Minnesota than 1", but not by much (Fig 24). No exterior insulation performs poorly.
Steve: With only standard latex paint on the interior (3-5 perms), the assembly can dry toward the interior.
A "smart" vapor retarder under the wallboard (under 1 perm when the proximate air is dry) can reduce the wintertime moisture accumulation without reducing the drying capacity, since it becomes more vapor open than latex paint when the proximate air inside the cavity is high enough to be a mold problem.
Half perm "vapor barrier latex" primer will reduce the total moisture accumulation too, and it'll still dry toward the interior, albeit more slowly than through smart vapor retarders + standard latex paint.
As long as the exterior foam is ~1-perm or greater the assembly can still dry toward the exterior. But foam with facers are usually well UNDER 1-perm, and foil facers woudl be under 0.1 perms. Even at 2" unfaced Type-II EPS will be above 1 perm. At 1" it would be above 2 perms.
The sheathing itself is less than 1 perm when dry, but becomes more vapor open as it's moisture content rises.
The prescriptive R20 + R5 c.i. thermal performance requirement in chapter 11 of the code is in contravention of the prescriptive R11.25 continuous insulation to fly with only latex paint (Class III vapor retarders) found in chapter 7:
https://up.codes/viewer/wyoming/irc-2015/chapter/7/wall-covering#R702.7.1
https://up.codes/viewer/utah/irc-2015/chapter/11/re-energy-efficiency#11
Jon R:
Figure 24 is plotting peak moisture content against vapor permeance. The perhaps more relevant chart may be Figure 25, the annual average moisture content, and Figure 26, the peak interior side moisture content. But it does indeed appear to be favorable to be at roughly 1 perm at the WRB/exterior foam level, even in International Falls (zone 7A).
Looking at Figures 24 & 25 s it looks like the sweet spot for International is ~1 perm, which protects the exterior side of the sheathing from high summertime moisture drives, and results in the lowest peak content, and about the same average moisture content as lower-perm WRB. That would put an inch of XPS or 2" of Type II EPS in the right zone, independent of other factors.
But in Figure 26, the peak moisture content in International Falls with only 1" is pretty close to the 20% mark (at which dry rot becomes a real risk), independently of the WRB's vapor permeance. On P33 (p43 PDF pagination following Figures 24-27 that they conclude:
"In summation, vapor-impermeable WRBs may be utilized only when at least 1 in. of
exterior insulation is used in climate zones 1 through 5. A minimum of 2 in. (greater than R7.5)
of exterior insulation should be used in climate zones 6 and 7."
Basically BSC is saying that it may not quite need to be the prescriptive R11.25 for 2x6 walls as per IRC chapter 7, but it does need to be over R7.5. The 2" of rigid rock wool is about R8.
So for zone 6A adding 2" of unfaced EPS would be close to the ideal for vapor permeance and would be OK on R-value, but 1" isn't quite enough. At only 1.5" Type II EPS would be performing at about R6.75 or higher during the coldest weeks of the year, which is probably enough to make a difference.
edited to correct myself: The BSC modeling was done on 2x4 /R9 through R13 walls, not 2x6/R20. The IRC chapter 7 prescriptive for 2x4 walls in zone 6 is R7.5 in zone 6, but in zone 7 locations such as International falls it's R10. So if R7.5 is just barely enough in International Falls it would appear that you can cheat the IRC by as much as 25% on the exterior R, but not by half. A mere inch of EPS, or even 1.5" is not really enough for a 2x6 wall in zone 6, but R8.5 might be. At 2" EPS would perform at R9 during the winter weeks that mattered in a zone 6 climate on a 2x6/R20 type wall.
Here's a proposed rule for less than recommended levels of exterior wall foam:
a) select a wall design that will work with no exterior foam (lots has been written about this).
b) add any amount of unfaced EPS.
Jon,
That makes sense to me.