Thermal break with TJI rafters

I’m a New Hampshire based builder- close to beginning construction on a small spec house. I’d like to build to a higher standard which has unique challenges: most new construction builder grade homes in this area do not employ green tactics. I need to be careful not to price myself out of the market.
I’m considering a double stud wall system with 7″ of open cell foam, 2×4 on the exterior and 2×3 on the interior. This won’t be much of a deviation from standard construction and won’t add a great deal of cost.
The gable roof has two different pitches, the front is a 12/12 and the rear is a 6/12. It’s 1 1/2 stories and the second floor will have a flat, vented insulated ceiling (likely cellulose blown to R60) under the 6/12 pitch.
The 12/12 will be mostly open to below. I’d like to fasten a layer of OSB under the the 11 7/8 ” TJI rafter flanges. This will create a substantial ventilation channel and leave 10″ for cavity insulation; I’m not sure what that will be yet, possibly more open cell foam as that contractor will already be on site and it has the added benefit of air sealing. We’d also use a smart vapor retarder.
My question involves creating a thermal break with the TJI rafters. Is this necessary? How much conductivity will happen through the 1/2″ OSB web? How does the rest of this assembly sound like a cost effective solution?
GBA Detail Library
A collection of one thousand construction details organized by climate and house part
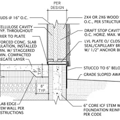
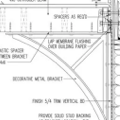
Replies
One more important detail: The TJI rafter run is 18 feet. The second floor flat ceiling will tie into the TJI at 12 feet, hence the need for a vented assembly.
And my name is Chris! Having a little trouble with profile set-up.
Chris, there is almost no thermal bridging through the web of a TJI (that's info straight from Passivhaus headquarters). There is thermal bridging through the flanges, web stiffeners and structural ridges you have to use with TJI rafters, however.
Using the top flange as a grounds for plywood or rigid foam baffles can be a good approach. 10" of open cell foam will only get you R-36, though--not enough to even meet code in NH, much less be considered high performance. Dense-packed cellulose is similar. You can add rigid foam at the interior of the roof assembly until you reach at least R-49, or preferably R-60 for prescriptive "Pretty Good House" performance.
I usually find the least expensive way to build a good "cathedral" ceiling is to frame with dimensional lumber and hang a 2x4 on gussets below the rafter to create as deep a cavity as you want, with a built-in thermal break. Then use 1 1/2" Accuvent insulation baffles and fill the cavity with dense-packed cellulose. Take care in transitioning your air barrier from the exterior wall sheathing to an interior variable-permeance membrane at the ceiling.
At the exterior walls, if you have not built with 2x3's I don't think you'll like them, and the only benefit from your stackup would be if the studs are offset. If you're building two walls anyway, why not include a bigger cavity, at least 8" and preferably 10-12", use 2x4's for all wall framing, and fill the cavities with environmentally friendly cellulose instead of petroleum-based foam. (The average cellulose-insulated home uses the amount of newsprint a person would read over 40 years!) Or build with 2x6 walls and wrap the exterior with rigid foam. Or frame with 2x6 or 2x8 and cross-strap the interior with 2x3's (search "Mooney Wall" for details).
Thanks Michael!
There wouldn't be bridging at the structural ridge as it is isolated within the attic cavity, 10 feet higher than the insulated ceiling.
The studs would be offset. I agree, 2x3's are terrible to work with and I generally avoid them. This building lot has a constricting dimension, and I've had to keep my building width narrow. Each inch is valuable, thus the 7" wall. Another consideration could be to use 2x3 interior wall plates and 2x4 studs on the flat. With the open cell foam, I'd have R 25 in a 7 inch wall, a good thermal break, and air sealing. A 12-inch cavity would be ideal with cellulose as you suggest- bit of a learning curve here. Hopefully my next project won't be as constricting. Going to look into the Mooney Wall too.
Ultimately, I hope to devise a system with reliable subs that will allow me to be competitive with conventionally built homes.
Chris, you might want to consider just framing the walls with 2x8's. The energy savings of the options we're discussing are not very large. Thermal breaks are great but the important number is the whole-wall R-value. A 2x8 is about R-9, not terrible, especially if you use 24" o.c. framing. The extra effort of thermal breaks and double studs starts to pay off when it allows you to do thicker walls.
Another option you might find cost-effective is 2x6 framing with 2 1/2" Zip-R sheathing. You'll probably need to get a new framing gun to shoot the 4" nails required, but it allows you to use standard 2x6 construction and insulation, and keeps all of the framing warm and dry. You're sheathing the building anyway so it's not much different than your normal process.
If you are not very careful you will end up living in this house.
Most new home buyers do not know what a TJI rafter is or why they would want to care about learning. The stuff behind the walls just does not interest them. They only plan on owning the home 4 years and thousands you are hiding in the wall pays off over 20 years so to them it is a bad investment.
Your competition will put that money into fireplaces, pot lights, tray ceiling, big bath tubs and custom cabinet. If theirs sell and yours will not you could be forced to move in and sell your current home as it is the only way to get out without showing a loss.
If you want to build green the safe thing is to find a customer sign a contract and build what they want.
Walta
Chris,
Michael is giving you good advice. You might also want to read this article: How to Design a Wall.
I'm building a similar roof assembly but using 14" TJI and 1" EPS foam instead of OSB as the vent baffle. I still haven't decided on whether to up the R value by furring out the rafter, but most likely won't. ...gotta draw the line somewhere before I go broke!
For the walls, have you considered the Bonfig wall approach? It's 2x6 with a foam strip on the interior side of each stud with a vertical 1x3 over that. It gives a pretty good thickness of wall and a thermal break without having to deal with window bucks on the outside or double stud walls. Fine Homebuilding did a story on it a few years back. I think the author's name was Bonfiglioli thus the Bonfig wall's name.
Thanks guys!
Andrius, I was considering an option like that- seems like a pretty simple process. And a material and labor intensive as a double-stud wall can be, it'll always be faster than wrapping the exterior of a house in 2 layers of foam and then furring. Not to mention the complexities of windows- and all of this stuff has involves ladder moves and staging. Simply won't work for a spec house. I'd really like to create a brand at a good value.
I'm using OSB as a baffles in the TJIs for installation purposes as I can simply fasten the sections with a finish nailer. Never fastened any sort of foam anywhere without a significant amount of cursing. Thanks for the heads-up on the Bonfig Wall.
The Bonfiglioli approach is a clever idea and it saves a little energy, but not a great amount. Center-of-wall value for a wall with 2x6's 16" o.c., using 1/2 lb foam or densepacked cellulose, is about R-18.6. Framing with 2x4's and using 2" Zip-R would give you R-21.1, an improvement of R-2.5. Knock 8-10% off that for plates, rims and headers and you have an R-2.3 improvement, roughly 10% of the whole-wall R-value.
Walls typically account for roughly 10% of total energy loss, so you'd be saving 1.0% of total energy loss-something on the order of $15-$20/year on a typical house. Not too bad, as far as energy improvements go--when doing energy modeling I figure anything over a 5% return on investment makes financial sense.
If you bump up to a 2x8, 16" o.c. wall, your center-of-wall value is R-24.5. Compare that to a 2x6 wall with 2" Zip-R at R-25.1. In that case the extra effort for Zip-R strips would not be worth it, but your adjusted improvement for 2.8's is R-5.3, or 28% better than the 2x6 wall, saving on the order of $40-45 per year.
What about a hybrid approach? EPS strips and then 1x furring over a 2x6 stud wall? This would create a thermal break and opportunity for cavity insulation the same as a 2x8 wall. Cost would be similar too as a 2x8x8 is about $3 more per stick than a 2x6x8.
Chris, there are lots of ways to build a wall. If you haven't read Martin's article you should definitely check it out: https://www.greenbuildingadvisor.com/articles/dept/musings/how-design-wall. Ultimately you have to decide what makes the most sense for you. In my world, labor is very expensive, so the fewer pieces that have to be installed to reach a specified whole-wall R-value, the better, but if it makes sense for you to rip and install EPS strips and then install strapping, that's certainly a good assembly.
Chris,
I'd heed Micheal's advice. If this was your own house, and you were performing a lot of the work, then it is a different equation, but spec building is about all about cost vs return.
You might find it useful to look through the threads and blog on GBA of Jimmy Nguyen's build. He details the unexpected labour involved in simple tasks like blocking between raised-heel trusses, and how his build exceeded the expected time-frame.