Thermal bridging
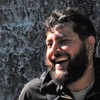
Hello!
I am building a workshop on a 1980’s 20’x8′ trailer that used to have a mobile construction office on it. I originally thought I could just fix some things here and there but realized after some weeks of teardown that it would be better to re-build the whole thing with green building in mind.
Another thing I have wanted to limit my exposure to off-gases from polymers. Exposure to plywood on the inside and un-treated wood is pretty much what I have been aiming for. Heating of the workshop will be with a small woodstove. I have ordered wood trusses and will have an un-vented ceiling; I had planned on leaving a small gap at the top of the roof-line for air movement.
My current floor build…I want to apply the insulated envelope logic to all of my trailer surfaces. I am starting off in the flooring and this what I’ve got thus far: trailer frame | Treated 2×4 studs | Treated 3/4″ plywood | 2″ XPS| 3/4″ un-treated plywood. I will not be trying to insulate the cavities in between the trailer frame and wood studs.
Regarding the floor build…
-Should I add house-wrap as the last barrier before the 3/4″ un-treated plywood?
Regarding exterior walls…the plan is: un-treated stud | 1/2″ plywood | housewrap and flashing along windows, bottom and top sills, etch | 1×4 furring as a rain screen | 2″ XPS | metal siding
My roof was going to mimic my exterior walls but now I am concerned about not having enough insulation on my roof. I really don’t want to expose myself to insulation, like the foil-backed polyiso I keep seeing everywhere.
Many, many thanks in advance!
Jonathan
GBA Detail Library
A collection of one thousand construction details organized by climate and house part
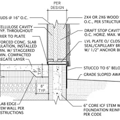
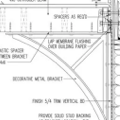
Replies
>"-Should I add house-wrap as the last barrier before the 3/4″ un-treated plywood?"
No- it serves no purpose there, if you tape the seams of the treated plywood, the seams of the foam board, as well as the seams of the un-treated plywood for air-sealing redundancy.
>"...it would be better to re-build the whole thing with green building in mind"
...
>"...2″ XPS..."
XPS is perhaps the LEAST GREEN insulation material in common use today, due to the HFC blowing agents used, the most of which (HFC134a) has a lifecycle global warming potential more than 1000x CO2 @ 100 years. As the HFCs diffuse out over a few decades it's performance drops too. While warranteed to 90% of the labeled R-value, at full depletion 2" of XPS is only good for R8.4- the same as EPS of similar density. (Same polymer, different blowing agents & manufacturing process.)
EPS is blown with comparatively benign pentane (7x CO2 @ 100 years), as is polyiscycanurate, which uses a more benign polymer chemistry too. Most of the pentane used in EPS escapes the foam and is recaptured at the factory, often burned for process heat.
If 2" is your limit on foam thickness, use polyiso. When sandwiched between 3/4" plywood on both sides the somewhat lower compression numbers for 1lb foil faced polyiso becomes irrelevant, and you get a labeled R12-R13 out of it rather than an R10 (and falling) performance out of XPS, or R8.4 out of 1.5lbs density "Type-II" EPS.
On the walls a foil facer adjacent to the rainscreen gap adds another ~R1 or so to the whole-wall performance.
What US climate zone?
Dana,
I'm stuck between polyiso and EPS. From the GBA articles I've read, the polyiso performance decreases with lowering temps and with time. EPS does the opposite: gets better and lower temps and doesn't degraded with time. This is my synthesis at this point.
Also: can EPS handle the compression of this trailer build? The perimeter is 2x4 stud, 8' walls with 2x4 trusses.
Jonathan,
It's probably just a typo, but on your walls you want the rain-screen furring outside your foam.
Hi Dana--thank you for the speedy reply!
Yikes on XPS! I live in SE Michigan, so Zone 5A.
I have to keep perspective on this build. It is a workshop. If I have to sleep in it for some reason or another, I know I will be roughing it with my woodheater.
The polyiso performance at low-temps is pretty disheartening, given the cold bitter winters of the Mid-West.
Do you have a diagram for an un-vented roof design? I want to make sure I understand where the soffit is in this design.
Jonathan,
Q."Do you have a diagram for an unvented roof design?"
A. Yes -- see below.
Q. "I want to make sure I understand where the soffit is in this design."
A. The soffit is the same place it always was.
Hi Martin,
Would it be possible to use foil-faced polyiso in between the rafters and also omit the plywood sheathing on the interior? I would still be putting EPS on top of the roof sheathing and plan on using 1x4 spacers instead of 2x4 spacers as ice dam prevention vents. Metal roof on top of all of that.
What are the risks of not insulating my roof "well enough" for my climate zone?
Many, many thanks; thank you for your service.
Jonathan,
Q. "Would it be possible to use foil-faced polyiso in between the rafters?"
A. I don't recommend the cut-and-cobble approach between rafters. The best way to use rigid foam is as a continuous layer of rigid foam on the exterior side of the sheathing.
Q. "And also omit the plywood sheathing on the interior?"
A. Plywood sheathing on the interior is unusual. Of course, you need plywood or OSB sheathing on the exterior side of the rafters -- as well as a second layer of plywood or OSB (or 1x4 or 2x4 purlins) on the exterior side of your rigid foam (if you choose to install exterior rigid foam). On the interior side of the rafters, most builders install drywall, not plywood.
Q. "I would still be putting EPS on top of the roof sheathing and plan on using 1x4 spacers instead of 2x4 spacers as ice dam prevention vents. Metal roof on top of all of that."
A. If I understand you correctly, the 1x4s will be installed like purlins (parallel to the ridge). I've never heard them described as "ice dam prevention vents," but they are a possible substitute for the second layer of roof sheathing above the rigid foam -- as long as you choose a type of metal roofing that doesn't require continuous sheathing.
The design as it is leaves me with 10" of EPS on top of the roof sheathing. Those are gonna be some long screws to drive.
A continuous 10" of EPS exceeds code minimum for roofing when it's a continuous layer. You'd need AT MOST 8.5" to get there on a U-factor basis (U0.026= R38.5 "whole assembly R, which includes the R-values of all structural layers, the roofing itself, and the interior & exterior air films.) That's still a pretty long screw. Going with 6" of continuous polyiso is easier.
If you install R15 batts between the rafters and some ceiling gypsum you could knock that back to 6" of EPS, or 4.5" of polyiso and still make it on a U-factor basis.
Dana,
Thank you for your response. As I live in Zone 5A, I was looking at EPS over polyiso given the change in performance at lower temps of polyiso.
I have looked at trying to buy recycled EPS in my area and its pretty scarce. I also find that most people only have 1# EPS.
At the moment, the plan is:
Roof
3 staggered layers of 2", 1# EPS (rated at R-8), thus giving me R-24
+
3.5" of Roxul in between the rafters, held by 3/8" plywood (no gypsum board for me), thus giving me R-15
R15+R24=R39, which I can live with
Walls
1/2" plywood | Tyvek Housewrap | 1x4 furring | 2" of 1# EPS| Metal Siding
Floor
3/4" treated plywood | 2" of 1# EPS | T&G plywood
Martin,
My original design was to leave the rafters open and in this build as it is a mobile workshop.
I have already ordered the trusses to be made of 2x4; this really only leaves me with 3.5" inches of space in between the rafters that I could insulate. Now I'm just trying to get as much insulation as possible within the 3.5" rafter cavities and on top of the roof sheathing...
I will end up going with 2x4 spacers on top of the roof.
The building is only 160 square feet. If it's pretty air tight, a very small wood stove will overheat it no matter what you use for insulation. A few inches of (reclaimed) foam on the floor, walls and roof should be more than adequate. Ten inches of polyiso on the roof would be overkill.
Since it's on a trailer, do you need to comply with any codes?
Stephen,
I can't argue with the code #s; I am just trying to keep the sorption and mold from ruining the framing and plywood. I heat with woodheat and am pretty terrified about how hot its gonna get in this superbly built structure.
I am going to take a step back and ask what type of work you are planning on doing? How often are your working in there? Are you planning to heat or cool this place 24/7 to some extent or only when you are in there?
The reason I ask is that many work shops require very large air exchange rates to keep the air quality acceptable. This is a particular challenge in small shops where one dusty operation can produce tremendous particulate concentrations. Is this a wood shop or a small electronics or art shop? For a lot of wood shops, even with decent dust collection, it makes sense to run a fan in the window and use radiant heaters to stay comfy while doing any sort of dust making.
Matt,
If I am around, I plan on heating/cooling the space. If not, all that will be in there will be tools, storage, and a freezer or two.
I don't plan on doing any dusty work, if I can help it. I prefer to work outside when I am going to make a mess.
You bring up excellent points--thanks!
I’m in SE Michigan too. There are several insulation dealers in the area, and they all advertise on Craig’s list. One is out towards port huron, another is in Taylor if I remember correctly. Search for “polyiso” or “rigid insulation” in the entire metro Detroit area and you should find some sources for discounted and occasionally also reclaimed rigid foam insulation, usually polyiso but often EPS too.
Bill