Trying to determine best assembly to insulate an old church roof being converted to office

We are looking to keep the existing roof decking and rafters exposed in a church in Atlanta, Climate Zone 3. We have read Martin Holladay’s FHB Article about unvented, Super Insulated Roofs, and Joe LUtiburek’s article BSI-036 Complex 3D Air Flows talking about the subject. One of the big differences (really somewhat minor) I see between the two recommended details is the best place to locate the fully adhered air barrier. Martin shows placing it at the outermost layer right on top of the new sheathing, right below the roofing material. In this case asphalt shingles. Joe showed it layed first, directly applied to the existing roof deck with multiple layers of rigid insulation and new sheathing for nailing surface above. Curious what the best apporoach is for our climate zone.
We are shooting for R-20, expecting to get to that with two layers of rigid. We will definitely stagger the seams. I saw that Martin also called out to tape and seal the seams at the top layer of the rigid insulation. Is that an insurance policy, or a very critical part of the assembly. I’m wondering about the ability of the top layer of OSB to ever breathe and dry out should it get wet. It would seem that it couldn’t dry downward toward the rigid, and the fully adhered membrane would keep moisture from going upward.
GBA Detail Library
A collection of one thousand construction details organized by climate and house part
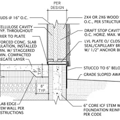
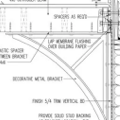
Replies
Eric,
When you refer to a "fully adhered air barrier," I assume that you are referring to peel-and-stick products like Grace Ice & Water Shield.
In most cases, I don't think that it makes sense to use a peel-and-stick product as an air barrier -- except under the rigid foam when following the PERSIST method (in other words, when 100% of the insulation is on the exterior side of the rigid foam).
The detail in the Fine Homebuilding article was not, in fact, my detail; it was a detail pulled from the GBA detail library. I'm sure it will work, but it isn't necessarily a detail I would have drawn up from scratch.
The easiest way to create an air barrier for a roof assembly is to tape the roof sheathing (OSB or plywood) seams with a high-quality tape. Many builders are using Zip sheathing and Zip tape these days as an air barrier.
If a roof assembly includes rigid foam, taping the seams of the rigid foam is a way to improve the airtightness of the assembly and to reduce the chance that the seams of the rigid foam will telegraph through the roofing.
Roof assemblies in cold climates (I'm excluding Atlanta) should include one or two courses of Ice & Water Shield near the eaves as insurance against ice dams. I don't think that applies in your case.
Martin,
Thanks so much for the feedback. We want to leave the interior side of the roof deck uninsulated, with all the insulation coming from rigid on the outside line of the roof deck. Doing a whole layer of peel and stick seems somewhat intensive. Part of my question in reviewing the details was whether it was truly necessary, or just an awesome level of belt and suspenders protection. Taping seams makes sense. We've had good luck with Zip wall systems, haven't ventured to their roof deck products yet. This might be the project to try it on. If not zip roof sheathing, taping the upper layer of rigid seems like it will also be an effective way to provide the air barrier. Any guess how much the long screws that attach the upper sheathing through the two layers of rigid to the lower roof deck will compromise the air sealing?
Eric,
In your climate zone, the 2009 building code calls for a minimum of R-30 roof insulation; the 2012 code will increase that minimum requirement to R-38. So your plan to install R-20 doesn't meet code requirements; you should consider doubling the thickness of the rigid foam. That might be easier with nailbase or SIPs than a site-built assembly.
I wouldn't worry about the screw penetrations compromising the air barrier.
Martin,
We are falling under the commercial section of IECC, and the building qualifies for Historic Tax Credits, exempting us from IECC anyway. R 20 gets us there with Comcheck as a renovation without taking any historic exemptions regardless too. That said, we are really trying to figure out what thickness of insulation will give us the be bang for the buck from a long term cost/value standpoint. The walls of the church are 19" thick granite with interior plaster, no other insulation there. Lots of stained glass, but we will be redoing storm windows, exploring options to do insulated glazing for the storm windows as well.
We have been discussing doing a nailbase with the contractors, as they are a little leery about not having that on the 6/12 slope. I've been trying to think through the compromise in continuous insulation by interrupting with the nail base. We are talking about 2x4s in a vertical orientation at 4' OC for attachments. If we do this, it would seem that going with the zip panels would be an easier approach to air seal above the nailbase.