Unvented Attic Insulation Options

Hello. What is the best non toxic options for insulating the attic roof deck for a non vented attic?
I know the codes required an impermeable layer with a vapor barrier as part of the assembly and I’d like to know what you can use for that besides spray foam and rigid boards (or maybe there is a rigid board that is non toxic)?
thanks!
GBA Detail Library
A collection of one thousand construction details organized by climate and house part
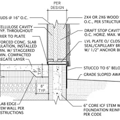
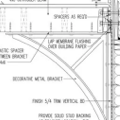
Replies
The way I see it all foam is bad the foam made in a factory under controlled conditions is less bad than the foam made in the uncontrolled conditions of a job site with a spray gun.
Seems to me you if your only choice left to you is an unvented roof assembly maybe you need to reconsider some of the choices that limited you to such a risky and expensive roof assembly.
Walta
Walta, it seems to me that Portnoy is making an honest effort to get good advice. If his query is for an existing home, which we don't yet know, then I don't think your advice is helpful. If it is for a proposed build, then your advice makes a bit more sense. But I still think your advice about not using foam board has too much implicit negative bias and judgement in it.
There are forms of foam board that are not really bad for the environment, or at least no worse than other commonly use insulations. Think about the amount of energy used in producing rockwool. Until that manufacturing process uses only renewable energy even it isn't that green. Spray foam is another matter entirely.
Let's not throw the baby out with the bathwater (2-part spray foam or XPS board). There's no better way of turning people off of green building than to become doctrinaire and religious about it.
exeric I appreciate the support. There are other scenarios such as cathedral ceilings where you end up in the same dilemma. None of us should be judgey on here! Clearly we are all trying to the do the best.
I already have all my hvac equipment there and no where else to put them. Venting the attic is not the best with this scenario. Unfortunately I didn't know about all these considerations when I started.
It is not foam free but encapsulating your ducting in SPF is the best option in your case:
https://basc.pnnl.gov/resource-guides/ducts-buried-attic-insulation-and-encapsulated#edit-group-description
I don't think we know what CZ Portnoy's in. If he lives in the western USA, he wouldn't need to encapsulate with spray foam. Just R8 insulation covering the ducts and then buried in cellulose. In the Eastern half then I suppose the SF encapsulation is required.
Edit: One really big advantage of your sited method is that if you're unlucky enough to have crappy SF installers it would probably be easy to remediate. The reason is that it would be such a limited installation. If I were doing it that way, I would make sure the ducts rested on plastic sheets instead of the ceiling so that remediation would be simple. You wouldn't have to scrape SF off the ceiling that way.
The reason for the SPF is not for R value but to air seal. The biggest issue with attic air handlers is air leaks which what you want to fix first and foremost.
The best way to go about this is to remove or rake to the side the existing attic insulation. Spray foam over wall top plates and any device boxes and encapsulate any registers and ducting in spray foam. Test with a duct blaster to make sure everything is all sealed up and reinsulate with fluffy insulation.
The air handler is harder to insulate properly, the best is to build an insulated dog house over it and seal it to the ceiling bellow. This can be a lot of work and complicate especially with a combustion appliance that needs proper fire separation and combustion air supply.
This gets you close to the same energy savings as a full attic SPF, uses way less foam plus keeps all the foam is completely outside your conditioned space.
@akos, I'm perhaps thinking of this wrong, but my understanding was that the only reason to encapsulate the ducts with spf in addition to the r-8 duct insulation is so vapor doesn't condense on the ducts in summer in humid climates and waterlog the cellulose. Burying ducts under cellulose without spf encapsulation is standard practice in western states because we don't have high humidity. Of course, duct sealing before anything else is added is also necessary. But I think if you did that effectively with a duct blaster then encapsulation would be unnecessary, at least in dry climates. I just assumed that the spf encapsulation of ducts was for locations with humid summers. Perhaps I'm wrong?
The way I see it generally the math for spray foaming the roof does not work.
When you move the insulation to the roof line you just double the surface are you need to buy to insulation to cover. That larger surface area is going to lose at least twice the energy as the ceiling would have and likely more because the cost per R of spray foam is so high people tend to go with lower R values. If you did manage to end up with the same R value you house still loses 15% more energy than before but now your ductwork in inside the envelope if it was very leaky you save 20% there. The best case is you come out 5% ahead. Give the high cost of spray foam and the fact most people sell the house before year 7 is over the chance of recovering the cost is almost zero.
I say the smart move is to patch up the leaky ductwork in the attic air seal the ceiling and wait for the current HVAC equipment to fail and replace it with ductless heads inside the envelope at that time.
Even if you are the exception and stay in the house for 50 years my bet is my plan comes out ahead of spray foam city.
Walta
So your saying to vent the attic? The air handlers are leaky and causing condensation even with my insulated roof deck. Not sure how to fix that.
If you have shallow rafters or a general lack of clearance in the attic, then closed cell spray foam against the roof sheathing is probably your only option. That doesn't necassarily mean it's the only option for you here though, since you didn't provide us with much information about your attic details...
If you have deeper rafters, or you have sufficient clearances to furr them out, I would suggest using some 1/4" wafer board (cheapie version of OSB) to build some baffles in the rafter bays to provide at least a 1" (1.5" is better) vent channel from eave to ridge, fill the rafters + possibly furred down space with batts to get you most of your required R value for your climate zone, then finish off with a layer of polyiso with seams taped and perimeter sealed. I would try to use at least 1" polyiso here, primarily for structural rigidity so that it doesn't bow out too much pressing the batts. Your local codes may require some fire protection under the polyiso too, which is often drywall, but can also be plywood or 1/4" hardboard. You'll want to check on that with your local building department. The polyiso acts to keep moisture out of the insulation in the rafters, and the vent channel will carry away any moisture that finds sneaky ways up there. The downside here is that this is more labor to install than spray foam, so you may find it costs more overall, which may or may not matter to you depending on what your project goals are.
I would strongly recommend you try to find a way to put in a vented attic over using spray foam. Vented attic assemlies tend to be the most robust, and the least prone to moisture problems. This is one of the big reasons why it's recommended to try to avoid installing mechanical equipment in attic spaces, the other reason is ease of access for maintenance. My guess is you don't have a lot of choice with that equipment now though, so you're stuck on that part of things.
Regardless of how you insulate the attic space, it's still worth air sealing all of the ductwork.
Bill
Hi Bill. Thanks for the long reply. I actually did a previous post with my attic details and no one replied. My home is new construction. Plans called for an unvented attic. The insulation was done not to code. Currently there is paper faced batts on the roof deck and with rigid foil faced foam under closer to the interior with a vapor barrier. I'm aware that this assembly will cause issues. I have plywood on floor with insulation under that as well. Attic has no vents at all. I'm in climate 4a. Trying to remedy the situation by either redoing the insulation or adding vents which then leaves me back at the equipment issue. There are two air handlers and an ERV up there along with lots of duct work. Maybe I can find a way to relocate the air handlers to second floor but it won't be easy!
I'm also dealing with my bedroom which has no attic above and was insulated in a similar manner. I can't vent that room because it's a bedroom (cathedral ceilings) and don't want to risk any toxic materials where I sleep. Thanks again
I was typing while you were posting the above.
Are you in zone 4C? 4B?
>"I know the codes required an impermeable layer with a vapor barrier as part of the assembly..."
What you "...know..." in this case ain't necessarily so. It depends on the assembly, the materials, and the local climate (as well as local codes). In most of the US it's possible (but not necessarily economical) to build code compliant unvented roof assemblies without any vapor barriers or vapor retarders tighter than standard indoor interior latex paint.
Got a location? (a postal code would be great, but nearest city/county/prefecture would be fine)
"... the best non toxic options ..." covers a lot of territory, across a large range of costs. (Got a budget?) It depends also on what is meant by "best". (lowest toxicity? lowest environmental hit?)
eg "...the best..." low toxicity solution from an embodied energy & net carbon point of view would be wood fiberboard insulation above the roof deck in combination with cellulose or fiberboard between the rafters. With a sufficient ratio of exterior/total-R there would be no need for an interior side vapor retarder. Both availability & price for the fiberboard would be a problem in most of the US. It's great stuff, very low toxicity (it's wood, after all), high moisture resilience, and carbon negative (since like all wood products, is sequestered carbon.) The favorable thermal diffusivity of wood fiber insulation makes it a super-performer in cooling dominated climates.
The "coming soon" (since before the pandemic began" GoLab/TimberHP products from a mill in Maine may eventually become available, but (alas) too late for my own re-roofing projects.
https://www.timberhp.com/
A similar lo-tox lo-impact product would be hemp insulation (rigid or batt, eg: https://buy.hempitecture.com/HempWool-Specs-2022.pdf )
Cellulose (batts or blown) products using borate-only fire retardents are also fairly low toxicity (toxic primarily to the gut flora of wood boring insects, not mammals). With recycled newsprint type product some people object to the toxicity of the inks, but there are also products using corrugated cardboard as the primary feedstock with little to no ink (though sometimes small amounts of adhesives.)
If you are not re-roofing your options become more limited, but if you can vent the roof deck from soffit- to ridge a wide range of options are still possible. Fiberboard baffles to ensure a 1-2" air gap between insulation & roof deck can be low-risk using wood fiber/hemp/cellulose on the interior side of the assembly. You may need to add depth to the rafters to get adequate R-value. It can also be useful in cooling dominated climates to use perforated aluminized fabric type radiant barrier on the interior facing side, which if secured in place with 1x wood strapping is strong enough to dense-pack blown cellulose against. A vented roof deck cellulose (or wood-fiber/hemp batt) solution is do-able at fairly low cost by a dedicated DIY-er.
Thanks so much. Yeah I'm having trouble pinpointing exact climate zone. Try 11050 for the zip code. We aren't re roofing as the roof is new. The currently assembly concerns me. We have cedar shingles. Under is felt. Under that is plywood. Under that is a paper faced fiberglass (I'm not sure if there is a gap or not). Under that it's the thermax rigid board tightly taped. The foil which is the most interior layer is vapor barrier. I don't know if having an Interior vapor barrier is a good idea and seems to be not code compliant.
Right now with this assembly the attic is 88 degrees. My air handlers are 65 and I'm getting condensation dripping on the plywood floor. I tried to slightly condition the attic with a supply only but it's not sufficient.
Thanks for the help
Everything in yellow is IECC climate zone 4A (green = 5A, blue -= 6A:
http://bcapcodes.org/wp-content/uploads/2012/01/cz-map_new-york.png
Looks like you're in zone 4A.
>"we have cedar shingles. Under is felt. Under that is plywood. Under that is a paper faced fiberglass (I'm not sure if there is a gap or not). Under that it's the thermax rigid board tightly taped. The foil which is the most interior layer is vapor barrier. I don't know if having an Interior vapor barrier is a good idea and seems to be not code compliant."
Are there soffit vents & ridge vents visible on the exterior? If yes, there is likely to be the code prescribed air gap & venting, and leaving it is just fine.
The facers on the batts indicate R30C, the "-C" meaning high density, suitable for cathedralized ceilings. The nominal un-compressed loft of an R30C is ~9.5". Milled 2x12s have a nominal depth of 11.25", so if the facers are pretty much at the same level as the bottom of the rafter edges there would be 1.75" of air between the fiberglass and roof deck (which is good). Even if the rafter bays do NOT have soffit to ridge venting (non-code-compliant), the south facing and sunnier east/west facing pitches are at low risk, but shaded or north facing pitches might be. With 1.75" of space it's well worth adding soffit to ridge venting if somehow that detail got missed. See:
https://s3.amazonaws.com/greenbuildingadvisor.s3.tauntoncloud.com/app/uploads/2018/07/25023949/Compressing%20fiberglass_0-700x310.jpg
With a vented roof deck the kraft facers are good enough as a vapor retarder (not a true barrier, but works just fine), but they are impossible to make perfectly air tight. The foil faced foam is a true vapor barrier, and much easier to detail as an air barrier. Vented roof deck or not, air tightness is far more important than vapor tightness here, so try not to mess it up with recessed lighting cans or other large hard-to-seal penetrations.
>"Right now with this assembly the attic is 88 degrees. My air handlers are 65 and I'm getting condensation dripping on the plywood floor. I tried to slightly condition the attic with a supply only but it's not sufficient."
A sweating air handler is usually a symptom of outdoor air getting in to that space. Air sealing the walls & ceilings should be job #1 (and job #2). In brand-new construction there may also be a lot of residual moisture stored in the building materials, which in an air-tight room would need active conditioning to remove quickly.
HVAC supply ducts/registers all need a corresponding correctly sized return duct, otherwise that room gets pressurized, and some other part of the house gets depressurized, pulling in outdoor air infiltration from whatever the least-resistive path is whenever the air handler is running. If you added a supply vent, add a return, so that the attic air gets full dehumidification, even if the flows aren't enough to dramatically cool the temperature.
Thank you so much for the help. I'm positive not neither the attic or the room with cathedral ceilings has vents at all.
The reason I did supply only was because I didn't want attic air recirculating with the rest of the home. We already had a mold issue on the plywood there. I'm considering a mini split and small dehumidifier instead. Thanks again!
Is it acceptable to add vents to the attic and leave all that roof insulation in place ? (Did u
See pic with foil)? Also would you be concerned with leaving my air handlers in attic?
>"Is it acceptable to add vents to the attic and leave all that roof insulation in place "
If you vent the attic space to the outdoors rather than venting just the roof deck via soffit-to-ridge venting you are likely to make the problem worse, not better. The jacket on the air handler when it's running during hot humid days will be ~55F, whereas the outdoor ventilation air will average dew points >65F, driving the condensation problem.
>"The reason I did supply only was because I didn't want attic air recirculating with the rest of the home. We already had a mold issue on the plywood there."
The mold issue would abate if you condition the space a bit more. The drier the attic, the less mold there is. Keeping it closed up and humid creates mold growth conditions. Even a MERV 8 filter on the HVAC would capture any mold spores, so the risk of circulating mold to the rest of the house is low. A large 4" - 6" deep pleated filter with MERV 11 or higher would even capture 2.3 of COVID viruses in every pass, MERV 13 is even better, but you may need to verify the static pressure on the system when going that high. (Do NOT go with a high-MERV (10+) with 1" thick filters without measuring the static pressure.)
Monitor the relative humidity (RH) in the space- even a $10 AcuRite is good enough. If the RH regularly exceeds 70% for large fractions of an average day you're risking mold. When it's 85F up there the RH will drop (it's "relative" humidity- relative to the temperature), but when the temps drop overnight the RH rises. Checking it in the AM would be more likely catch the peak. Running a dehumidifier would lower the humidity (while raising the temperature), but you need to dispose of the condensate. The central AC would likely fix the humidity problem more quickly & reliably than a room dehumidifier.
Take a stiff wire to depth-probe the rafters- if it's more than 10.5" (it's probably 11.25") simply air sealing the interior side foil faced foam will improve the resilience of the roof deck, even without soffit to ridge venting. It's often pretty easy to add soffit & ridge vents to simple roof lines even after the shingles are installed, and with a 1"+ channel between the R30Cs outdoor air will be driven through the channel via convection whenever there is a significant temperature difference between the outdoor air & roof deck (which is pretty much guaranteed any time the sun is shining.) The roof deck then protected from rot by being able to dry to the outdoors, without introducing humid outdoor air into the attic space.
BPortnoy in response to your question in post #11.
Yes I think vented attic are the best option.
Once you give of on vented attic and move the insulation to the roof line, in my opinion you must consider the attic conditioned space. Just like every other room of your house. The rest of your house is not moldy because you have enough supply and return registers. Only once you can admit to your self you own a conditioned attic you can install or open the vents in the attic so the attic is more or less the same temp and humidity as the rest of you house. As you are finding out unvented and unconditioned attic is a game of Russian roulette with mold and rot and it sounds like you are losing.
Walta
Is something like FourSevenFive details here a good option? They basically say a good air tight vapor variable barrier negates the need for venting of the attic. They do a say a blower door test is a critical part of this. I haven't seen this recommended here, I'd be curious to hear input.
https://foursevenfive.com/blog/yes-unvented-roof-assemblies-can-be-insulated-with-fiberglass-a-wufi-post/