Unvented small crawl space details for helical pile foundation

Hello
I’ve done some reading here on GBA and Building Science Corp. I am hoping I’ve understood the details and just wondered if I could sanity check and get any inputs from yourselves.
Climate 4c. A small 300sqft new cabin with a small 4-6” gap to grade under the floor. Floor structure is a steel perimeter frame with infilled timber joists floor sat on helical screw piles.
We can’t build any higher nor can we pour a concrete slab for various reasons.
Plan:
– – 2” second hand rigid foam insulation laid on top of a thin gravel layer over the levelled earth, I understand insulation here doesn’t offer much benefit but I think code wants to see it and it’s a small area so not very costly
– – Heavy gauge poly laid onto insulation with seems sealed and taped
– – Insert helical piles through the poly and insulation then seal the poly at each penetration with a gasket
– – Bring poly up the perimeter and seal to the steel perimeter beam
– – 2” rigid foam insulation vertically at perimeter to the top of floor level encasing the steel beam at the outside and bury into the ground 6” or so to get below frost depth (the face of insulation would in turn sit plumb with our proposed 2” of exterior insulation on the walls above)
– – Protect exterior insulation with cement board or edpm
– – Introduce conditioned air to the mini crawl space and add an extraction point via our HRV
– – No plumbing in the space which can instead go directly out the back wall
Your thoughts welcome. Thank you
GBA Detail Library
A collection of one thousand construction details organized by climate and house part
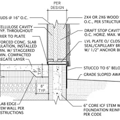
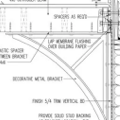
Replies
owen,
I suspect it would be much easier to entirely fill the area under the cabin with compacted fill and a layer of foam, rather than leave any gap. Code issues aside (once you build a crawlspace it has various requirements, including ones for height) I don't see any practical advantage to having a 6" void below the floor.
I'd get the piers in place, construct a perimeter out of PT wood, and add whatever proportion of gravel and foam you think is appropriate.
Whichever plan yo0u go with, I'd reverse the sequence of construction and place the foam and poly after the piers are down. The chances of either of them being intact or level after driving piles though them is vanishingly slim.
Hi Malcolm,
It would be nice to fill with clean fill but we need to wheel barrow everything to site about 100 yards down a path, and volumetrically even this small cabin that's a lot of wheelbarrows! We could of course sit the perimeter and joists closer to grade but I thought getting some conditioned area circulating would be helpful, however we'd definitely prefer it sit low as possible.
Noted on your reverse sequence, my thought it would be easier to cut a patch small holes in the poly for the piles then to try and work around them but we can of course do either!
Thank you
How are the helical piers being driven? Normally you'd use an excavator which I think is what Malcolm is thinking of.
I'm with Malcolm I think. Code is a crawl space has to be a minimum of 18" above grade, I'd think of this house as more like a slab on grade with no space, supported by the helicals.
Are you using concrete at all? Normally helicals are set in concrete to give them lateral stability. I'd be thinking about keeping rodents out, that foam against bare earth would be luxury housing for mice. A layer of gravel that is too tight for mice to fit through and the individual stones are too big for them to move is usually an effective barrier.
A perimeter of PT plywood with battens sealing the seams would work as an air and rodent barrier. I agree that the pile installation should be first, then the steel frame. Then the perimeter plywood and leveled gravel base. I think I would install enough foam to nearly reach the underside of the steel frame, then slip the poly over the foam and seal it as good as possible. Your floor system is then entirely inside of the thermal and vapor envelope, so pretty safe from decay. You probably call this a "concrete-less slab foundation" to avoid crawlspace access issues.
Interesting design challenge. As we get more of these helical pile foundations, we're going to see more variations on the theme. The code officials are going to have a hard time keeping up and if you're in an area with aggressive code enforcement, they might make you get an architect or engineer's stamp for this design. I've done several of them with grade beams and either slab-on-grade or CMU foundations on the grade beams. So far, I've never done one with a lightweight frame on top of the piles, except for a couple of decks, and they don't count.
DC, the piles are driven with a hydraulic head, there is no concrete involved. We tested a small pile getting to about 1 ton load at 4-5' depth then a large pile nearly 2 tons. As they will sit close to the ground, there is no lateral load issues. But this is of course being considered by the structural engineer and will follow their advice. Photos of the test pile attached.
Peter - noted regarding the PT ply, this would cover my vertical insulation at the perimeter I think? Indeed the idea is get everything inside the conditioned space so to speak. We are also coastal and just 100 yards from the ocean, so I am keen to get the galv steel piles and steel frame inside the conditioned space and away from salt laden air, even if the galvazing should last a few decades. If the building science supports this design in principle, I will endeavour to get the inspector on board.
We don't have an 18" crawl space rule here, but suspended timber floors are supposed to be 6" from grade, that is when this space is ventilated to the outside however which means insulating between all the joists and having thermal bridges at all the steel and joist locations.
owen,
Are you sure you aren't conflating two things? Structures built on piers and open at the permitter are often allowed to be close to grade as long as they areconstructed of pressure treated materials. But once y9u close them in they are both practically and by codes considered to be crawlspaces with all their attendant requirements.
The project sounds Interesting. Where are you that you are 100 yds. from the ocean but not worried about flooding a ground level structure? Some of the homes on the barrier island I have a place on are built on helical piers, but usually tied into a grade beam and then either reinforced CMU walls (bad idea) or solid pilasters (better where flooding is possible, particularly where there may be fast moving water).
Is that a hand held driving head? What brand and torque ratings may I ask.....
I just had a bunch of piles driven last week with a hand-held auger. Up to 2100 ft lbs. It had a 10-foot arm that was braced against something solid, then four guys held the head as it went in to keep it straight. The first one was braced against the foundation and the rest were braced against preceding ones.
It could generate a lot of torque but they had trouble getting down pressure when they hit obstructions.
Hi Malcolm. I’m located in the UK so different code rules here. The floor joists would be pressure tested regardless though as that’s what’s readily available here.
So the key here is an effective system rather than strict code compliance.
Nick - we up a cliff from the actual ocean so no issue with flooding. But we can certainly here the waves crash!
The head is hand held and has an outrigger pole for bracing. Designed actually but a family friend so it’s a convenient option! According to the website it’s rated to 4,000nm.
Yes I have seen these hand held units work here in the US. A long outrigger/ handle on one or two sides allows two guys to hold it steady while the head drives the pile. Great for driving piles from inside through a hole cut in a floor or basement slab in order to shore up an existing structure. I have seen guys put the outrigger/handles out windows and such to get a stable grip....Good luck with the project!
Hello
I just wanted to update in case anyone else comes across this thread. Building inspectors have approved the detail below for this application.