Vapor barrier for four-season room

As I turn my screened porch into a four-season room, I am confused on the need/risks of adding a vapor barrier to the floor. When the porch was built, a vapor barrier was installed somewhere into the concrete slab; and the current floor has ceramic tiles. I am framing a new floor on top of the existing tiled floor. My plan for the floor insulation is to have a layer of 2″ XPS foam between the joists (I already have the boards and would like to use them), taped, and mineral wool batts on top of the foam. Do I need a vapor barrier on top of the tiled floor? Don’t I risk “sandwiching” moisture between the two vapor barriers — the one in the concrete and the one on top of the tiles?
GBA Detail Library
A collection of one thousand construction details organized by climate and house part
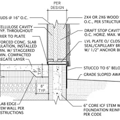
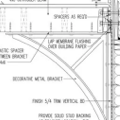
Replies
The vapor barrier that would have been installed in the slab would be to help keep ground moisture from coming up into the finished floor. That's a bit different from the usual applicatin (in heating dominated climates anyway) of keeping moisture from moving from the indoor spaces into the wall assembly where it can condense and cause moisture issues.
I don't think you'll have a problem with your assembly, but I would put the XPS down first, then frame the floor on top of the XPS. You might not even need to frame out a floor -- in many cases you can just put down a plywood (or OSB) subfloor right over the XPS, then install the finished flooring on that subfloor just as if it was a "regular" floor with plywood/OSB over floor joists.
Bill
Thank you, Bill!
With my assembly, I still wonder: where would the moisture stop: at the XPS foam, or at the new vapor barrier?
I love, and had discussed on this forum, the option of having the XPS under the joists. In my case, as I have approximately 8.5" in height to frame, I believe that I should use 2"x6" joists over the foam boards. a) Will they be OK for a 15' span? b) Would you feel comfortable having such joists, and the weight of the floor, press on the 2" foam? (It's Foamular 250.) Should I use floor joist hangers? Will the floor be rigid enough? c) Speaking of subfloor, is DryPly plywood recommendable? Will it be rigid enough? Will it by any chance prevent the floor (that is, including its insulation) to dry properly if need be?
Thanks!
I would add a second layer of XPS (or use EPS, which is both cheaper and greener), and put a 3/4" plywood subfloor over the top of the foam. No joists. No mineral wool batts.
Foamular 250 is rated for 25 PSI, which is 25 pounds per square inch. That's 3,600 pounds per square foot. Typical live load for residential structrures per code is 40 pounds per square foot. Add 20 pounds per square foot for heavy dead load and you're at 60 pounds per square foot -- under 2% of the rating for the foam. You'll be fine with no joists using just the foam for support :-)
Note that if you use the cheaper Foamular 150, you're at 15 PSI, or 2,160 pounds per square foot. A lot of EPS is rated for 10 PSI, which is still 1,440 pounds per square foot. The plywood subfloor acts to spread out point loads (table legs, etc.), which would otherwise be where the foam might have a problem due to the *concentrated* point load. For distributed loads using a subfloor, you'll have no problem using the foam for support.
Bill
Thanks Bill! I confess that what you describe is a new approach to me. I like it, but I wonder (1) what the city's inspector will think of it, and (2) whether I will ever find a contractor who goes for it (I have encountered a lot of resistance to building-science-driven ideas).
There are several aspects that are not clear to me, unfortunately:
- We are talking of 7" of rigid foam (right?): will that just be contained by wooden boards along the perimeter of the room, and maybe glued to the existing tiled floor underneath?
- Would the OSB or plywood just be sitting on top of the rigid foam, and only be secured along the perimeter to the wooden boards, which would form a sort of "box" for the floor?
- There is a bit of slope to the existing floor (8.5" step where the house is, 9"-1o" at the opposite wall): How am I going to compensate for that? With joists, ripping or shimming them would have been an obvious option, or maybe hanging them using joist hangers, maybe with some perpendicular sleepers, or blocks, for further support. With foam only, I have no idea how all of that should be addressed.
There are aspects that confuse me:
- Will EPS attract moisture, or is that not a problem?
Why so much foam? I had assumed you wanted to insulate the floor with a combination of rigid foam and batts to get to some R value. If you need to raise the floor to match the height of some other floor, then that's a different problem. Normally you'd use somewhere around R10-R15 under the slab (assuming CZ5/CZ6 here). That's 2" (R10) or 3" (R15) if using XPS. You don't really need to glue it, you can "float" the floor. I would secure the plywood at the perimeter though, and you can run some long tapcons through the assembly into the slab too if you want some extra insurance.
I would use some floor leveler to level things out prior to putting in the foam. It's easier to start with a flat/level surface in this case than it is to try to fix it later.
If you need to bring the finshed floor up to the level of some other floor, now I'd change things up a bit. I would put in enough rigid foam for R value, then frame out above it but without using batts. You could rest the floor joists right on the foam, although it would be better to put some 2x4s on the flat with the floor joist on top of that to spread the load out a bit. This is probably cheaper than a plywood/OSB layer over the foam, then joists, then a plywood/OSB subfloor. You could use floor leveler under the foam to level things out as I mentioned earlier, or you could rip your floor joists to different depths (or at an angle, depending on how you need to orient them) to even things out. There is no need for joist hangers or anything fancy, since the foam can still support the load.
XPS is somewhat better for this application in terms of moisture tolerance, but very little difference. The bigger difference is that it will probably be easier for find compression rated XPS than EPS, and inspectors are likely to want to see that rating.
Bill
Thanks, Bill! Indeed, I do have to frame a 8.5" high floor, to make the new floor be flush with the rest of the house.
Now, to your suggestion (rigid foam with joists on top, then the subfloor), I wonder how, instead, the following compares: joists (on sleepers?) against the existing floor, and a 1.5"-2" of foam between the joists and the subfloor? Wouldn't ripping or shimming be easier this way? Also, wouldn't the joists be more firmly holding the floor if they are sitting on the existing, tiled floor (or on the floor sill plate, widened, depending on how much correction I need to make for the slope in the existing floor)?
Also, under either option, why not add fluffy insulation between the joists? The added R value would come at a cost, but it's only one room, and it might be worth using that empty space to add more insulation. Don't you think?