Vapor barriers on CMU above-grade walls

Hello,
I am doing a design for an interior remodel on an existing commercial building. We are in Denver, CO which is Climate Zone 5 and a dry climate. The exterior wall is just 1-wythe of exterior painted 8″ CMU (a.k.a. concrete block). There is no existing interior framing or insulation. I have no way to find out if the CMU cells are insulated or not. Typically the local contractors would provide a 6″ metal stud wall with fiberglass batts placed directly agains the CMU wall to meet code compliance. I have not yet heard of this being a problem with condensations, mold, etc…. But, I plan to glue a 2″ layer of XPS rigid foam to the CMU with the joints taped and sealed. Then add a 3-5/8″ metal framed wall with fiberglass batt insulation and 5/8” gypsum board. My question is, do I need to have any vapor barrier between the CMU and the XPS in this application? Or, do I need to have the fiberglass batts wrapped in plastic?
GBA Detail Library
A collection of one thousand construction details organized by climate and house part
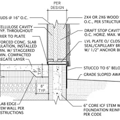
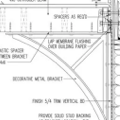
Replies
The basic answer is that you don't need or want a poly sheet between the foam and CMU, but in most cases it wouldn't hurt anything.
But the rest of the design can be tweaked to advantage, at a net cost savings with higher thermal performance.
>"Typically the local contractors would provide a 6″ metal stud wall with fiberglass batts placed directly agains the CMU wall to meet code compliance."
That would actually fail compliance on U-factor basis if metal studs are used, since the "whole-wall-R" would be about R8-R10, where you actually need R15. Your steel stud 2x4 wall going to have similarly undercut performance of your steel stud 2x4 wall too, but as-described it would just make code-min performance.
> I plan to glue a 2″ layer of XPS rigid foam to the CMU with the joints taped and sealed. Then add a 3-5/8″ metal framed wall with fiberglass batt insulation and 5/8” gypsum board.
DON'T use XPS- it's by far the least-green insulation material in common use today, with a CO2e footprint an order of magnitude higher than EPS or polyiso, R for R. The high global warming potential HFC blowing agents (a mix that is primarily HFC 134a with a gwp ~1400x CO2 @ 100 years) that give it the higher initial performance than EPS diffuse out over time, and it's only warranteed for 90% of labeled R at 20 years, and will eventually hit about R8.4 @ 2" at full depeletion. EPS is blown with low impact isopentane (~7x CO2 @ 100 years) most of which escapes the foam at the factory where is recaptured, not vented to the atmosphere. The R-value of EPS is stable over time.
Polyiso is blown with a mix of similarly low impact hydrocarbons. See:
https://materialspalette.org/wp-content/uploads/2018/08/CSMP-Insulation_090919-01.png
In zone 5 only R5 is necessary for dew point control on R13 batts at the foam/fiber boundary on the above grade section, so 2" of any foam (even low density Type-I EPS, at about R7.8) would be enough to skip interior side vapor retarders. Using steel FURRING rather than studs penetrating the fiber layer would dramatically improve the net thermal performance of the fiber insulation. It's pretty easy to install continuous sideways-stacked R15 batts behind 24" o.c. hat furring installed in 2x4 top/bottom plate channels, and only slightly more difficult to install it in 16" o.c. furring. The channels are usually a true 4" , and 7/8" hat furring leaves a 3/8"compression (rather than the full 3.5") at the furring, but guarantees the batts stay in place.
If using polyiso keep the bottom edge off the slab by a half inch or so to avoid moisture wicking, but EPS can rest on the slab.
It's fine to use foam with facers, but unfaced EPS would also be fine. At 2" Type-II EPS is somewhat more vapor tight than interior latex paint on wallboard, so ground moisture coming through the foam would happen at a rate slow enough to never become a problem.
Dana.
Thank you for the thorough response and also for the reminder about XPS insulation. I will change the XPS to EPS. Also, I never thought about spanning hat channels between the top and bottom plate. I was under the impression that they are not self supporting. So, in that configuration, the batts would be laid horizontally, unsupported in the 4” cavity and the hat channels would be outside of 4” top and bottom plates?
Thanks
The hat channels would be inside rather than outside the 4" top/bottom plates (the 3.5" thick batts could not be a friction fit in a 3-5/8" to 4.0" space), but yes the high density batts would be stacked horizontally, perpendicular to the usual orientation in a studwall.
With harder to find 2x3" steel top/bottom plates the hat channels could be placed on the outside of the plates. The box stores near me carry 3-5/8" steel stud materials, most commercial distributors carry 4" goods. Nobody seems to stock shallower studs, but 7/8" deep furring is usually available. A former co-worker of mine went the hat-furring in 2x4 top/bottom plates route using 3" of HFO blown closed cell foam (R21) and no fiber insulation, a proposal that came from a contractor. (Not exactly DIY-able, and pretty expensive compared to 2" EPS + R15 batts.)
Thank you again. I might run this idea of the hat channels through the contractor.