Vapor-open insulation systems?

We have are trying to insulate a historic masonry townhouse and extererior insulation is not an option.
We have been speaking to a lot of German architects and in general they are guiding us toward vapor-open systems.These are usually mineral based materials (calcium silicate derived, perlite) or can be petrochemical based (Remmers ThermaIQ). These materials sit flush against the masonry and idea is that vapor can freely diffuse inwardly or outwardly. They are also mold resistant. Clay based plaster is applied directly to the insulation material so there is no studs, drywall or air space. An example of an American distributor for mineral based insulation is http://amnova.us/
Does anyone have any experience with this or other similar approaches? Why is this not being used more in the US?
Thanks
Daniel
GBA Detail Library
A collection of one thousand construction details organized by climate and house part
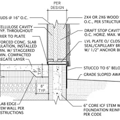
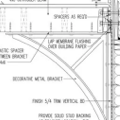
Replies
Daniel,
I know of one U.S. architect who insulates older-brick buildings with vapor-open insulation on the interior side of the wall. Her name is Chris Benedict, and she works in New York City. She insulates old brick buildings with cellulose. You can read more about her approach in my article, Insulating Old Brick Buildings.
The reason that few U.S. architects or builders use this approach is because we have extensive experience with failures resulting from the use of interior fiberglass insulation on this type of building, and these failures make many people wary. There is also the problem of embedded beams and joists, which can become damp with this approach.
So the jury is still out on this approach, in my opinion.
Daniel,
Good question. You referred capillary active insulation materials are used in Germany in building that have brick walls that get very wet - are very absorptive (suck up rain water very quickly), mostly single whyte buildings or very porous brick (which used to be dried by the heat from the interior).
The way to insulate those wall safely and is to very modestly insulate on the interior (r-5, maybe r-10) with those kinds of materials. You will not be able to build a Passive House with those insulation levels, but do make a big improvement in energy efficiency.
What is possible in NYC, since the brick used on the exterior is very hard/non-absorptant in most cases - is to indeed use cellulose. The next step is than to improve both airtightness and smart vapor retarding (to dry to the inside if needed and to manage the vapor drive from interior in winter). Cellulose is capillary active and in combination with INTELLO Plus can allow you to insulate up to R-20-ish (depending on walls composition, orientation etc). This is sufficient in NYC in most cases to get to Passivhaus performance. More information about the dangers on possibilities of interior insulation of masonary buildings in this blogpost - and standard masonary/brownstone interior insulation/airtightness details here.
Thanks for your answers.
Floris, I do question whether our 19th century bricks are not also very porous. I have a related question about moisture. In the links you sent, you show 2 ways to insulation a floor. In one the air barrier is on the bottom of the floor.
http://www.foursevenfive.com/images-ezpages/DetailLibrary/Retrofit/Air%20Barrier%20Detail%20Retrofit%20RowHouse%20Floor2.pdf
In this case, how can you be sure that water does not leak through the floor boards - either from normal use or from a fluke burst pipe? In our case, we are working with original floor boards. There is no subfloor. So it seems that it would hard to get this floor absolutely water tight. Thanks. Daniel
Climate matters (a lot!), where is this historic townhouse located?
This building is in New York City.
NYC is warm enough to get away with a lot of things that would fail in colder locations, but not as warm as German climates, and a highly vapor permeable approach is likely to be riskier from a freeze/thaw spalling point of view than going with an inch of closed cell on the brick with the more permeable goods to the interior side of that.
The January average temp in NYC is about 30-31F, which is well below the dew point of healthy indoor air, and the diurnal temperature swings will deliver something on the order of 100 relatively deep freeze/thaw cycles in a given winter. In Germany most locations average in the mid to high-30s in January with fewer excursions below 20F- you have to go to higher altitude alpine locations to find freeze/thaw cycling comparable to NYC. (Munich might come close though.)
http://weatherspark.com/#!dashboard;a=USA/NY/New_York
But it's still a lot better than climates that dwell below 20F for much of the winter, with numerous freeze/thaw cycles in the spring.
Limiting the rate of moisture diffusion from the interior with ~ 1 perm (about an inch) of foam keeps the now colder bricks from ever loading up with moisture even if the interior is kept at a fairly high 50% RH (though the beam ends might suffer if you did that- 35% RH is safer). This leads to slower drying of the brick during the rainy season, but also lower latent air conditioning loads to the interior during the summer (remember last week?). High summertime humidity is something quite rare in Germany, but it's a given in NYC- in an air conditioned masonry building it can important to have a bit of vapor retardency in the wall assemblies to keep the interior humidity levels down, especially on the sides that get sun, where the stored moisture in the brick can get driven off at extreme rates, ending up in the interior finish wall components.
The cellulose + smart-membrane approach advocated by Floris Keverling Buisman might work- it definitely makes it from a winter-conditions point of view, but may end up with saturated cellulose if the exterior brick/mortar is either too porous or leaks air. The wicking aspect of the cellulose enhances the drying of the brick toward the interior, but the cellulose has to be able to store & re-release that moisture without excessive moisture to keep it from settling, losing R-value, or becoming moldy. Smart membrane vapor retarders run about 1 perm when dry, become highly vapor open when humid, but the spring & summer moisture drives from the exterior may or may not be within the buffering limits of the cellulose when socked with storms like Irene or Sandy, unless there is a moisture-resistant layer between the cellulose & brick (like a flash-inch of closed cell foam.)
In an NYC climate 1" of closed cell polyurethane on the exterior side of the assembly would also be sufficient dew-point control for 9-10" of cellulose on the interior, if you wanted to take it that far.
A somewhat better product for this application than generic closed cell polyurethane would be Icynene's water-blown MD-R-200 product, which runs about 3 perms @ 1" rather than 1-perm. That's still strong class-III vapor retarder, plenty for limiting peak winter & summer moisture drives, but gives the brick a hint more drying capacity toward the interior without being super vapor-open. Not a huge difference, but some.
But before taking any of these approaches it's good to get a handle on just how porous the brick is, how much roof overhang you have (a huge factor on the amount of bulk wetting the brick receives), etc.