Vented over-roof, except furred space not vented
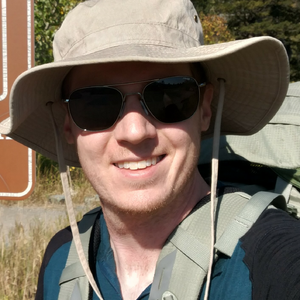
Hi GBA — Looking for advice on a roof stackup. I’ve got existing 2×6 rafters at 16″ OC and 1x board sheathing, to which I’m planning to add Adhero as an air barrier, followed by 2 layers of 3″ thick reclaimed polyiso, topped by 1/2″ CDX sheathing, underlayment, and roofing. We’re struggling to figure out how to attach the new sheathing through, though…
The most straightforward answer is “use long HeadLOKs fastened through to the rafters”. This is fine for uplift, but runs into a couple issues:
– The edges of the sheathing panels will be difficult to support
– There isn’t good engineering data available on HeadLOK screws resisting perpendicular loads through 6″ of foam (their tables only go to 4″ and my engineer and I can’t find a good way to calculate allowable load on the screws)
– In order to keep the plywood flat, we probably need to use a lot more headloks than would be necessary structurally, which is a lot more thermal bridges and a lot more long screws that are hard to aim at rafters.
Around GBA, I often see people talk about the “vented over-roof” thing, with flat 2×4 battens on top of the foam, fastened through to the rafters, and then sheathing applied to the battens. This solves a couple issues — the sheathing could be nailed to the battens on any pattern necessary to keep it flat, and the battens could be screwed to the rafters with countersunk screws Rothoblaas-style, some straight in and some at an angle, which is easy to calculate and specify the screw patterns.
However, my roof isn’t “simple” — I have an 8:12 pitch on the front, with 2 dormers, and a 2:12 pitch in the back, so eave to ridge venting isn’t really feasible — I don’t think I can have a ridge vent where a low-slope roof meets a steeper-slope, and the dormers block a bunch of paths anyway. I’m not sure why, but my gut says leaving an air space in the assembly without ventilating it is asking for trouble / moisture accumulation.
A hybrid approach would be to embed the battens in the top layer of insulation, but that’s a lot of cutting & cobbling of insulation and also sacrifices a few points of R-value.
Am I missing anything here? I know this type of assembly is tricky in general, and I wouldn’t be doing it this way if it weren’t a renovation situation — just wondering if there’s some approach that I’ve missed in my research!
GBA Detail Library
A collection of one thousand construction details organized by climate and house part
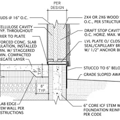
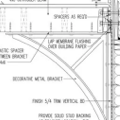
Replies
I don't know about calculating it, but gluing the whole assembly together would add a lot of strength. Like a SIP.
>air space in the assembly without ventilating it is asking for trouble
I tend to agree and IRC code for roofs contains various forms of "direct", apparently to prevent air gaps. On the other hand, fiberglass batts (mostly air) effectively form a non ventilated air space in some assemblies that work fine. So maybe it also depends on the cold/warm side perm ratio or where in the assembly the air space is. Would be good to have a definitive answer to "when/where is a non-ventilated air space OK".
Example: "The air-permeable insulation shall be installed directly under the air-impermeable insulation." Given that the former is mostly air anyway, why?
>Given that the former is mostly air anyway, why?
I think the theory here is that "mostly air" isn't the same as "open space" -- "mostly air" fluffy insulation works because it mostly prevents the air from moving around, ie convection, while open space would let convection currents happen.
As to why an air space presents moisture issues, though, I'm not certain on the theory there!
I would look at deck screws:
https://www.iko.com/innovi/document/6300071-078-pds-iko-innovifast-insulation-fasteners-en.pdf
Follow the pattern for the slope/wind speed you need. These are rated for going into a wood deck, so you don't need to hit rafters. They are reasonably priced and readily available at most commercial flat roof suppliers.
The current roof I installed is standing seam on strapping over rigid with dormers. The assembly is not meant to be vented so there are a lot of spaces that dead end. I've never worried about moisture buildup in there.
Thanks Akos -- I did run across that style of screw, and the ease of installation is certainly attractive, but I hesitated for a couple reasons:
1) Their ratings all seem to be for either penetration through a plywood/osb deck, or at least 1" actual of solid wood -- my 1" nominal board sheathing is 3/4" actual, and also has a lot of knots and imperfections.
2) Their patterns seem to involve a lot of screws -- which is both costly, and a lot of little thermal bridges that add up surprisingly fast and would also be a bunch of very cold metal points poking below my roof deck, which seems like it might present condensation issues? Would I need to go around spearing blocks of foam on the points of all the screws?
Having just completed a simpler version of what you're describing, I've got a few lessons I can share.
1). It's easy to over fasten the insulation to the deck. I only used one layer, but I really went to town, in hindsight. The insulation only really need be held in place while you're getting the furring strips installed. Try to limit the number of screws you put in to that layer. I even had thoughts of using truss plates between multiple layers instead of screws just to keep layers from sliding around, without over penetrating the deck.
2). I put a 2*4 on the flat over 2" of foam, going into 2*6 rafters. I used a combo of headlok, Spax powerlag, and Simpson strong drive screws as an experiment. The heakloks we're my least favorite of the three. I used the 6" version of each. The headlok were much more flexible than the other two, and if the grain on the rafters cupped out to one side, it seemed that even on a dead center approach, it would follow the grain and bust out the side of the rafter. These were yellow pine, maybe it's not an issue with SPF or eastern white pine.
The powerlag were probably my favorite. You can get them in boxes of 200 or so off the net, and it brought the price down to a little less than what I could source the headlok a for. They drove easier, and straighter, and that made my impact batteries last longer. Bonus for the torx head instead of the other spline bit. The Simpson screws were just a little much for the application. Just too beefy for what was really needed.
3). I had about a 90% first-hit rate for getting a screw into the center of a rafter, having not prescribed the 2*4, or marking all that well. It sounds ok at first, but by the time you put in 500 screws, that's a lot of misses, and now a lot of holes in the all of the layers, short circuiting all the fancy work in between. With 6" of foam, and the 2*4, I really don't know how you'll achieve a good hit rate. I would pre drill the 2*4s on a centerline using a drill press before hand, so you can be sure that screw gets started dead straight. Youve got to be 100% aligned else you'll try 2-3 times in a few places before you really get it in there. You'll know, because it'll other screw easy, or the impact will really crank all the way down.
The spots I missed, sometimes I didn't get again on the 2nd try, and it made me feel bad :)
4) using polyiso, I could suck the head flush into the SPF 2x4 without really compressing anything to a noticable degree, with all three fasteners. (I'm pretty sure the Simpson screw would have sucks through the building though had I let it)
5). My building was small, so if I thought I missed a screw, I'd leave it and go on to the next one, and I redid all the misses at once. Try not to get off the roof and check, unless you've got a helper calling the hits or misses as you go.
Other thoughts:
If I had to do it over, I would have set up a jig and a press to pre drill my fastener pilot holes to be more perpendicular to the rafters. A little deviation goes a long way when your target is small and far away. If I had to try and accomplish what you describe, I would consider eating the cost while lumber is cheap and screwing a 2*3 or 2*4 to the decking first, with normal #10 x 4" exterior screws, 12" oc, and lay a first layer of 1.5" insulation, and then go over that as normal. You'll come out time ahead in the long run, and end up with fewer bad penetrations. The screw length alone will pay for the difference in cost.
This is already going to be expensive, at least choose an option that is constructable, achievable, and has good results.
Thanks for sharing your experience!
Putting a flat 2x4 on the deck first is something I'm thinking about -- at least it'd be a wider target to aim for! Or, putting flat 2x4s somewhere in the middle of all the foam, thus splitting one long screw shot into two shorter and more manageable (and lower cost) screws. One thing I've definitely learned on this project is that construction estimation is hard -- I can add up the cost of the insulation, and the cost of the wood, but "yeah, I guess we need some long screws and some tape" is suddenly another thousand bucks!
Those screws add up quick! So does the tape, but it's only money, right?
I think you'd be better served, structurally, to put it on the bottom, and have a zero gap and large gap, rather than two small gaps. The 2*4's are the furthest inside the insulation and more protected from the dew point, and otherwise your structural connection is really just unaligned screw shanks with some distance of wood in between. It's also easier to line them up when you can use an existing line of nails on the deck, instead of guessing again over the first layer of foam.
Try finding the spax contractor pack up codes, and seeing if a place will order them for you. Often times you can find some online, like this one.
SPAX 3581820801710 5/16 x 6-3/4" T-Star Washer Head HCR (High Corrosion Resistant) (Exterior) PowerLag Screw (250 Pieces per Pail) https://www.amazon.com/dp/B08B5FQX3C/ref=cm_sw_r_cp_apan_glc_fabc_FXE7KYNGCYZZPJZDF023
Jonny, I had a very similar project a few years ago. I had planned on using nailbase or SIPs but both presented problems. I ended up using 3 layers of 1 1/2" polyiso, using 2Xs in an "L" shape to create perimeter nailing, and for the top layer of foam I ran 2x sleepers with foam in between the sleepers. It was still challenging, as the existing framing was all over the place and hard to hit with the long screws, but we got it done.
Thanks for sharing the photos -- your 2x perimeter is a pretty clever detail, I may end up copying that!
Hi, Nail base mfgs have installation documents and fastening schedules. You might be able to use that as a design method or reality check