Cold Walls in Addition

New here but have been reading the amazing content and wanted to first thank those who contribute their expertise to us laymen who seek to make better decisions for our environment and energy efficient spaces. Truly grateful for your willingness to share your knowledge!
In late 90’s we purchased a 1904 built home in S. Illinois that had a garage with living room behind it added in mid 80’s. The garage and living room are attached on the West side of the main two story house. The living room is 18′ x 30′ with entire North, entire West, and half of East wall (where attached to main house) exposed to exterior. The living room is attached to the garage along the South facing wall so the garage insulates (to a degree) the living room from the exterior and is not much of a problem. However, the living room suffers from extremely cold West, North and East walls in the winter.
Doing some research I found that the framers sheathed the exterior of the 2×4 framed walls with a outward foil faced 1/2″ foam (maybe fiber-board – yellow color) with no plywood sheathing at all. Uninsulated vinyl siding was hung over the foam sheathing. The walls look to have fiberglass batt insulation in the cavities with a plastic sheeting over the interior studs, then 1/2″ drywall, then wood paneling over the drywall. The addition was built on a 2.5′ deep crawl space where they did at least put the same 1/2″ yellow foil faced fiber or foam board on the interior of the poured concrete foundation and they did fill the floor cavities with fiberglass batts. The floor still gets a little cold too in the winter. The old part of the house sits on a two wythe clay brick basement foundation with poured concrete basement floor. The house is heated with hot water boiler with large ornamental iron radiators in old part of house and cheap fin tube perimeter hot water heat in addition. They never worked well together because the fin tubes had to be heated to a very high temp to provide any heat to the room which made the old part of the house extremely hot – regardless of closing each hand valve to almost closed on each iron radiator.
This isn’t about the heating system but wanted to give the context.
Question (finally): We want to remodel the living room addition and wanted to get a better insulation value to stop the cold wall effect in the winter to be more comfortable & save energy. While I realize that perimeter heat’s purpose is to provide a warm curtain on exterior walls, I am concerned that if I remodel and install cast iron baseboards (Burnham Baserays – better matched heater to old part of house) that I will still have what seems like either thermal bridging or just badly insulated walls or both and will still use just as much energy to heat the room in the winter, still be uncomfortable and possibly worse, have condensation trapped in the wall due to more heat loss with better heating system. My thoughts were to rip out the fin-tube baseboards, carpet, paneling, drywall and fiberglass batting. Then, install cut 2″ x 1.5″ stud caps to thicken the wall cavity to 5.5″, install mineral wool batts for 2×6 walls inside the bays, continuous & taped polyiso (not sure of thickness yet) directly on expanded studs, then drywall. Ceiling (attic with 5.5″ fiberglass batting between trusses) will stay as is. However, if you feel that the ceiling is not insulated enough either please let me know. Wife wants solid wood flooring but I want to go back in with carpeting for the additional floor insulating value (my perception).
I have read a lot of back and forth exchanges on thermal bridging and adding polyiso on the interior behind the drywall as well as using mineral wool instead of fiberglass in the cavities. I am worried that the exterior foam will not allow moisture to dry from inside-out after installing polyiso on the interior with drywall over it. I don’t know if the exterior foam was taped or not. Our budget will not afford both exterior and interior remodeling and because we don’t intend to stay in the house for but another 5 years, I want to provide some sort of fix to have more comfort now and not pass along the headache to the next owner but without blowing my nest egg over it. I know there is a problem and I’m the type who cannot just pass along to the next owner.
Also for more context: some fixes I have done to the entire old part of house: had new double insulated Andersen windows and doors installed as well as blown-in insulation put in exterior walls, new 200 amp panel and wiring throughout entire house (except living room), new 80% efficient HW boiler with newer more efficient circulator and added a circulator for the living room zone, new roof, new flooring etc. Old part of house is very comfortable after its remodel but it has one-by sheathing on exterior and interior of the true 2″x4″ and 4″x4″ framing. Old part of house is very well built/framed. New addition was a jack-leg build in my opinion.
Thanks in advance for any suggestions/recommendations.
GBA Detail Library
A collection of one thousand construction details organized by climate and house part
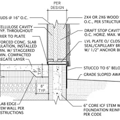
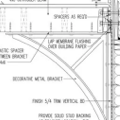
Replies
All the insulation in the world is useless if the wind is still blowing thru your house.
Seems to me you need blower door directed air sealing done. They use a fan to depressurize the house measure how much it leaks. While the house is depressurize, they use smoke to find the leaks later they fix the leaks and measure again. In a house as old as yours it is very likely to be extremely leaky. 20 air changes per hour would not be uncommon at 50 Pascals.
If you don’t care about knowing the numbers, taping a box fan into a window and some incense sticks will locate the leaks.
Walta
In my response to OhioAndy I noted that the former owners layed caulk everywhere they could to seal air gaps but that doesn't stop the cold air blowing into the cavities as you state. That just keeps the warm air from escaping - although it seems that where there is a gap (like near an electrical outlet) there is a cold draft inward rather than feeling my warm air being sucked outward. Guessing my heat is going up in the attic and it is creating a stack effect with the wall cavities being basically open to cold windy drafts. I'm hoping that there's no mold in the walls - although if it's so open to the exterior there is plenty of air movement to dry out any moisture migration.
As poorly built as 1980s additions are, as a remodeler I look at them as relatively easy to upgrade--at least compared to old farmhouses! As Walta says, the lowest hanging fruit is finding and stopping the air leaks. It could be that fixing those (i.e. crawlspace vents, no sheathing, ceiling leaks) is accomplished by upgrading to continuous insulation. WIth vinyl siding and no sheathing, upgrading to a continuous 2" exterior foam might be the easiest approach, leaving the drywall, fiberglass batts, and maybe even the present 1/2" exterior material right where they are.. Crawlspace encapsulation--or at least an upgrade of what you have--is also a wise investment, particularly if there's presently no vapor barrier on the ground. Maybe then take the floor fiberglass and stick it in the attic after sealing up leaks in the ceiling. I'm guessing window replacement is not warranted in the first round.
The former owners put silicone caulking on every wall corner and ceiling corners -not sure about the wall to floor though. They also did lay a plastic moisture barrier on the ground in crawl space. I've given all of the scenarios a lot of thought and am frozen with indecision. Your 2" exterior continuous insulation over the existing 1/2" r-board is one I thought about too.
How would I address the soffits where the 2" foam will meet up with it? Would I push the 2" exterior foam right up to the soffits and caulk that joint before hanging siding again? Also, would I need to add one-by furring strips to nail the siding to create an air gap between the vinyl siding and the 2" foam? Guess it would also be a good idea to caulk all of the sill plate joints at that time as well. Can insulation be blown in on top of batt in the attic? Thinking that might be easier than adding batts on top of batts. I don't care about losing the attic space as storage.
Thanks for your response.
The silicone-in-the-corners trick is an unfortunate attempt to fix the infiltration problem (I hope it's not actually silicone, which doesn't take paint.) If you decide to go with exterior foam, even 1" would be safe for dewpoint control in your climate zone, given the nominal R-11 already in the walls. Then that layer can be detailed as a very good air barrier and WRB, too. You might consider adding 7/16" OSB as a structural sheathing underneath the foam, and detail that as the air barrier with an acrylic tape, but if this is a budget situation and the walls are braced well enough, you can skip it.
As for the soffit, yeah, the question arises of how far to go with all of this. Of course it would be best to remove the soffit and run continuous foam up to at least the top of the doubled wall plate, or even better to within 2" of the roof sheathing, but I have also dealt with "the budget situation" by leaving the soffit in place and ending the foam there. You do what you can. This ain't NASA. And of course, you reinstall the old siding, just use longer nails and find the studs, might have to add in some new vinyl where the trimwork requires.
You’re wanting to fix this comfort issue is admirable but from a financial point of view and your plan for selling in only a few years means you will not recover the money spent on insulation before you sell in fuel saving and buyer fail to perceive any value in insulation. New siding and exterior insulation never make economic sense until the old siding has failed and replacement is the last option.
How many thousand of dollars are you willing to give away for the warm feeling you will have in your heart knowing the next owner is unlikely to recognize your efforts should you succeed?
Walta
Man, Walta, that's a pretty dark way to follow through on your initial great advice. You're right, sort of, but you're also extrapolating a strict conventional ROI analysis onto this OP's question that even he was willing to push away. Our grandchildren ask us to try a little harder than that, and people who come to GBA get enough of that discouragement elsewhere.
It sounds like you might benefit from zoning the radiators. The fin tube radiators may not be undersized, they may just not be controlled properly. Putting them on their own thermostat may give better comfort and should be a lot cheaper than replacing them with cast iron. Cast iron and fin tube have roughly the same BTU/foot rating so the replacement probably won't solve your comfort problem anyway.
I zoned this room a few years ago, installing a new pump dedicated to the room. Both zones operate on their own thermostats. I cannot run the fin tubes at the temperature it requires to produce the heat output the room needs unless I overshoot the heating needs in the old part of the house. Also, fin tubes cycle my boiler way too often while the old part of the house's cast iron radiators keep each room evenly warm - especially since splitting the zones. I've spent two years trying to find a happy medium to no avail.
Walta has a point in how far do I want to take this but I have no crystal ball on when we will pick up and leave exactly and would like both comfort and efficiency until that day. Wife wants the paneling and old carpet gone and wants more comfort in that room and I figured I'd try to make the room more comfortable while doing the rest of the work that was going to get done anyway. Reading Martin Halladay's many posts on this subject, I came to the conclusion that addressing heat loss and thermal conductivity at the same time would be the approach to take. I planned to caulk every seem and joint before installing drywall. Adding blown-in insulation on top of the batts in the attic as well.
I'm just wondering how much the interior r-board will cut down on the cold wall effect - if I am able to address the heat loss through the attic and where the addition joins the old house. It should be better than what we have currently - I would think. I appreciate your suggestions below. They are all valid points that I will inspect further.
I think it's jumping to conclusions to assume that the problem is lack of insulation, it sounds like you have a poorly designed heating system, with the old part of the house over-radiated (the radiators are too big) and the new part possibly under-radiated. While adding more insulation is always good I'm not sure that's going to solve your comfort problems.
I can see two ways of improving your heating system performance, neither one of which is particularly expensive: either add more feet of fin tube to the addition, or put a tempering valve onto the zone for the old part of the house to have it run at a lower temperature. Replacing the fin tube with cast iron baseboards is not going to solve anything, they have the same output per foot more or less as the fin tubes, they're just quieter.
I can give a better assessment of how your system is working if you tell me:
- How many feet of fin-tube in the addition?
- What water temperature you're running now?
- What water temperature makes the addition comfortable and the old part of the house too hot?
- What state and county you're in? (I'll use that to look up your weather records.
See attachment for the addition layout. The room is approximately 450 sq. ft total including the pantry areas and area in front of each pantry. The red areas are the proposed CI baseray lengths. However, the actual fin tube heaters lengths (28 linear ft total) for each wall are as follows:
Exterior wall showing 14' baseray: 8' fin tube
Exterior wall showing 6' baseray: 6' fin tube
Exterior wall showing 5' baseray: no fin tube
Exterior wall showing 10' baseray: 8' fin tube
Garage wall showing 7' baseray: 6' fin tube
Pantries showing 4' baseray currently have no fin tube and both 4' long walls are exterior walls. The pantries area leads up 3 steps to our kitchen and this is where the addition connects to the older part of the house. These pantries are both cold as ice in winter time. The ceilings in pantries are drop ceilings with the same batt roll insulation over them as what is in the attic above the living room. Planned to drywall the ceilings in the pantries and hit them with blown in insulation too.
- "What water temperature you're running now?" Newer boiler has Hydrolevel 3200 plus with OA reset max 180f and the minimum it'll let the boiler get down to is 120f due to the condensing protection that keeps the circulator from operating when return water gets to 120f. It'll get 180 f during design days and the stat in the living room never gets satisfied.
- "What water temperature makes the addition comfortable and the old part of the house too hot?" 180 F is max I'll let the Hydrolevel take the temps to because the iron radiators get dangerously hot at that temperature. 180F never satisfies call for heat on design days and we have to run a Vornado 1500 watt heater to satisfy call for 70F in room.
- "What state and county you're in? (I'll use that to look up your weather records." Southern Illinois, St. Clair County
"Replacing the fin tube with cast iron baseboards is not going to solve anything, they have the same output per foot more or less as the fin tubes, they're just quieter."
Reading many forums on the comfort and efficiencies gained with CI holding the heat longer and thus radiating for longer periods will mean that the cold/hot cycling should be minimized.
Re tempering valve: I've thought about that one as well and it is a great idea. Real estate around the boiler is the problem there and old CI pipe is what is supplying the old part of the house. I cringe at the thought of breaking into what could be a pandora's box with what could be 75 year old 1-1/4" CI. Assuming that the tempering valve is a thermostatic mixing valve that would be installed between the supply and the return somewhere? My circulators are on the return side of the system and I read (PM Engineering) that putting a thermostatic mixing valve
on a system setup like mine would mean that most of the hot water will flow back into the boiler and not enough to supply the house. Did I interpret the article wrong?
Thanks again for your time! I really appreciate it.
"Reading many forums on the comfort and efficiencies gained with CI holding the heat longer and thus radiating for longer periods will mean that the cold/hot cycling should be minimized."
For comfort what you really want is something that starts putting out heat as soon as it turns on and stops putting out heat as soon as it turns off. Otherwise your system is prone to delays in heating up and then overshooting once it reaches temperature.
The reason people like cast iron baseboards is that they are silent, finned baseboards make noise. The finned ones actually do a better job of maintaining temperature.
But here's the thing: you said that at 180F your baseboards can't maintain room temperature on your design day. Unless they're not working, ie there's air in the system or a blockage, you just don't have enough of them. Cast iron baseboards are going to give you the same BTU/linear foot, if you put in the same amount of them you're going to get the same amount of heat, and it still won't be enough.
That said, it looks like you're going from 28 feet of fin tube to 50 feet of Baseray so it's a healthy upgrade. Just back of the envelope, the existing 28 feet should be good for 15,400 BTU/hr at 180F water temperature, and you say that's not enough. The 50 feet of Baseray provides 27,500 BTU/hr at 180F.
The room looks to be about 300 square feet? I don't put much stock in rules of thumb, but as a sanity check you're at 50 BTU/hr/SF now and going to 90. Your design temperature is 10F, and those are kind of eye-popping numbers.
More back-of-the-envelope:
It looks like the addition is about 15'x20'. Three walls exposed to the exterior, about 50 linear feet. I don't know how tall the walls are, but let's say 10' to make the math easier, so 500 square feet of walls, 300 square feet of floor and another 300 square feet of ceiling. So 1100 square feet of exterior exposure.
The formula for R-Value is square feet times temperature delta divided by BTU/hr. With a design temperature of 10F your delta is 60F, so at 15.4 btu/hr your average R-Value is 1100*60/15400= 4.3 and at 27.5K it's 2.4.
Those numbers seem really low. Please correct my assumptions. But I'm just worried you're going to spend a lot of money on new radiators and they aren't going to fix your problem, there's something else going on.
"The addition was built on a 2.5′ deep crawl space where they did at least put the same 1/2″ yellow foil faced fiber or foam board on the interior of the poured concrete foundation and they did fill the floor cavities with fiberglass batts. "
This indicates to me confusion on the part of the insulation installer about where the building envelope was. If the crawlspace in inside the building envelope then the floor shouldn't be insulated, if the crawlspace is outside then the walls shouldn't be insulated. This kind of situation is actually incredibly common.
I would go around the house and make sure that the building envelope is continuous. If you're seeing 20 air changes per hour, my calculator says that an effective leakage area of 1400 square inches. That's almost ten square feet. That's not coming from 1/8" cracks where the drywall meets the floor, that's coming from big holes. It's depressingly common that the insulation guy will insulate the wrong part of a wall it it's at all complicated. Or insulate three sides and leave one uninsulated. Or just skip sections that no one can see in the crawl space. Plumbers and electricians will make holes and remove insulation without a second thought. To the extent you can view them you need to look at floors, ceilings and exterior walls and look for holes that aren't sealed and gaps in the insulation.
Where the addition joins the old house is a frequent spot that isn't sealed or insulated. It's also a spot where the insulation guy often gets confused about what the envelope is and seals the wrong area. It could also be that the old part of the house is poorly sealed, in the old days they didn't think that rooms that weren't heated needed to be sealed or insulated, it was common for attics and basements to be essentially open to the outside.
The way that air leaks work is that they create a pressure differential in the house, so where you feel the draft isn't necessarily where the leak is.
Thank you to all who have responded to my question/concerns. Upon thinking about the faced polyiso install on the living room walls as described in Martin's Musings "Walls with Interior Foam" (https://www.greenbuildingadvisor.com/article/walls-with-interior-rigid-foam), I got to thinking about the fact that the builders placed a plastics sheeting vapor barrier between the drywall and the insulated studs making the cavity dry to the exterior (if need be).
Question: Would installing a foil faced polyiso as prescribed in Martin's Musing article - furring the face of polyiso with 1x's and installing drywall to the furring - leaving an air gap between the two surfaces trap moisture in that cavity? Essentially no moisture should be allowed to get into that cavity if it's sealed on both sides of the cavity - right? Is this a situation where using un-faced r-board would be a better idea - allowing any moisture in the cavity to dry to the interior - since it wouldn't be allowed to dry to the exterior? We are thinking about scrapping the idea of adding the faced or un-faced r-board to interior walls due to fears of trapping moisture between the r-board and new drywall. However, at just about $650 for all r-board and furring materials to install, it seems like a very inexpensive way to add r value to this room - considering we are having to re-drywall the room anyway.
Your thoughts/ideas are very much appreciated.
Thanks, BW
Re: DC Contrarian
"For comfort what you really want is something that starts putting out heat as soon as it turns on and stops putting out heat as soon as it turns off. Otherwise your system is prone to delays in heating up and then overshooting once it reaches temperature."
I have to politely disagree with your opinion on the comfort factor created when a space is warmed quickly but also cools quickly because that's exactly what one gets with fin tubes vs cast iron emitters. In a high heat loss home, all this means is that as soon as the fin tubes lose all of their stored energy (within minutes) they stop emitting heat and the room quickly becomes cool again and the boiler is required to fire again sooner to mitigate the quick heat/quick cool cycles. Cast iron's ability to store more heat and emit for longer periods means that boiler firing and circulator cycling will be cut down and the room will stay warmer longer./more comfortable longer.
"The reason people like cast iron baseboards is that they are silent, finned baseboards make noise. The finned ones actually do a better job of maintaining temperature".
Also, we like the comfort of radiant heat that the CI puts out over the convection heat that fin tubes put out - not just the noise factor of fin tubes. Radiant heat is less dusty as it doesn't require pulling air through them to heat the room. The fin tubes required cleaning periodically - which was a PIA - especially with those of us who have cats. Cat hair in the fins were terrible. Guess where the cat liked to be all of the time? Fin tubes also project from the wall more and are just plain unsightly (okay, those are my wife's words - not mine). Also, my smart thermostats learn the delta gaps over time and mitigate the overshooting to a degree (pun intended).
"That said, it looks like you're going from 28 feet of fin tube to 50 feet of Baseray so it's a healthy upgrade. Just back of the envelope, the existing 28 feet should be good for 15,400 BTU/hr at 180F water temperature, and you say that's not enough. The 50 feet of Baseray provides 27,500 BTU/hr at 180F."
Actually, my calculations were based on what appears to be 1 GPM and not the proper 4 GPM that is reality here. Therefore, my linear foot calcs were wrong I think. My total linear feet is now 27. At 180F supply on design day, my BTU/hr output will be 13,770 - overshooting the calculated heat loss of 12,700 btu/hr for this room. That's a safety factor as far as I'm concerned.
Not trying to be argumentative but CI is what we are going in with and this is not a cost issue. It is a comfort issue. These old fin tubes are going because we don't want them anymore and the cost savings of doing most of the renovation work myself offsets the additional few thousand these CI baseboards is costing. Fin tubes coupled with cast iron regardless of zoning cannot be done without adding extra tempering valves and controls and if one is going to go through that expense, why not just go in with cast iron that will have similar characteristics to the outputs and comfort of the old part of the house? Also, having to take out the fine tubes and its thin walled & leaky copper piping to do the reno anyway, I cannot see myself reinstalling them again.
I do appreciate your comments and advise as I know you are just trying to save me added costs.
Thanks again, B_Dubya
OK, I won't try to talk you out of cast iron. But if you're replacing 28 feet of finned radiators with 27 feet of Baseray or similar, and you're not satisfied with the heat you're getting now, you're not going to be satisfied afterwards either -- because both have essentially the same output curve.
Something about your description just doesn't add up. My gut is that 13K BTU should be ample to heat that room, I would look into whether the heating system is really delivering that or whether there is some issue with the zoning or controls. With proper zoning it shouldn't at all be an issue that the different zones have different radiation types or if one zone is over-radiated.
The point of my post #15 is that a heat loss of 12K BTU for 300 square feet sounds really high too. My back of the envelope calculation is that it equates to an overall average R-value of just over 4. To put that in perspective, just drywall and plywood sheathing, no insulation at all, is going to give something like 1.3, plus whatever the air trapped in the wall gives. Just a 2x4 wall with fiberglass, which is pretty much the minimum that you can call "insulated," gives R13. Basically this calculation is saying your walls, ceilings and floors are closer to uninsulated than insulated. And your experience -- that 28 feet of finned radiators running at 180F can't keep up on design days -- indicates that your actual loss is even greater than your calculation. But this is 1990's construction, not 1890's construction, and the expectation is that all of the walls are going to have some level of insulation.
I'd feel better if these inconsistencies were resolved before you went and spent thousands of dollars on new equipment.