Wall Assembly Help – New Construction – Asheville, NC

The amount of information out there is daunting to say the least! My family is just now getting over a bad mold problem that we encountered on our last home in South Carolina. As a result, my wife and I both have varying degrees of MCS and we’ve both been sensitized to Asperigillus. I won’t get into the details of the past, but we are building a “healthy” home based on Joseph Lstiburek’s book “Mixed-Humid Climates”
Due to recent posts and relevations on spray foam, I’m almost at the point of axing my initial thought of using open-cell foam throughout the wall cavities, roof decking, and basement walls. I could really use some help here. Current details:
1) Location – Asheville, NC area (Zone 4 I think, maybe 5)
2) 1700 SqFt on 1st and 2nd story above grade, another 700 SqFt in the finished basement.
3) Basement will have daylight on 2 sides.
4) Foundation drain wrapped in gravel, covered with filter fabric, beside the footer. Sandy fill on top, then backfill with dirt. I’d love to use coarse backfill but that would be another $5k according to my builder.
5) Delta Foundation Membrane over the footer (below the foundation wall) as a capillary break.
6) Foundation wall damproofed very well with spray on application. Drainage board over the application.
6a) Interior foundation wall covered with 1″ XPS, then framed with 2X4 studs.
7) Lose gravel fill below slab, with a soil gas depresurization system (passive), rigid foam insulation over that, then vapor barrier, then slab.
8) 2X6 exterior framing.
9) Cement board siding over housewrap
10) Geothermal (3-ton), sized by an engineer as well as the HVAC technician. 2 X 300 ft wells.
11) Desuperheater for supplemental hot water heating
12) Whole house dehumidification and ventilation system for fresh air and humidity control (Ultra-Aire 100V)
13) All hardwood flooring
14) Asphault shingles over conditioned attic space.
15) Other green features that I can list if needed.
We’ve cleared the lot and poured the footers. I’m pretty happy with the foundation design and water mitigation strategies that are in place, but the wall assembly has me scratching my head. I was all set to use BASF Entertie, Open-Cell Spray-Foam for the wall cavities, the rafters, and the basement wall (was going to have 1″ of XPS on the basement wall with 2X4 framing and open cell foam, then sheetrock).
Due to the large number of posts about Spray Foam off gassing and improper application, I think I’ve decided to axe that and follow Riversong’s advice with Dense Pack Cellulose (National Fiber). I only want the stuff with Borate and no Ammonium Sulfate.
With that said, what would you reccomend for my wall assembly? No vapor barriers of course. I want a wall that can breath. We had no plans for a rain screen, but I could probably have them install one if needed over the wrap. Should I use foam on the outside of the wall structure? Is the Dense Pack insulation enough (similar R value to the open cell spray I might add). And finally, what about the roof deck and the basement. Can I (or should I) use cellulose in those areas?
Confused in NC!
Thank you all so much!
Mike
GBA Detail Library
A collection of one thousand construction details organized by climate and house part
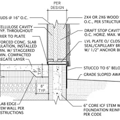
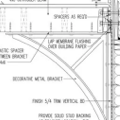
Replies
Michael W.,
1. There are a great many ways to build walls; no way is perfect, they all have advantages and disadvantages. I'm partial to 12-inch-thick double stud walls insulated with dense-packed cellulose, but I also like foam-sheathed 2x6 walls. You ask the question, "Should I use foam on the outside of the wall structure?" I'm tempted to say, "You certainly can," but it sounds like a trick question, since you also wrote, "No vapor barriers of course." Well, I guess that rules out rigid foam.
2. Now that you have decided not to use spray foam, you had better add thicker rigid foam to the inside of your basement wall. The code minimum requirement in your climate zone is R-10. Of course, more is better.
Thanks for the quick reply Martin!
From what I've read on my climate, I need to allow the wall to dry in both directions, right? I was referring to interior plastic vapor barriers, but I see your point. I had read that if you have a thin sheet of XPS with a perm rating of 1 (I think) that it wouldn't be a barrier (although I'm sure it would slow things down a bit).
Same goes for the basement. If I'll be using Cellulose down there then wouldn't I need to limit the amount of rigid foam insulation to allow the concrete to dry to the inside when wet?
Thanks!
What would be your suggested insulation strategy in the Asheville, NC area? Assume a 2X6 wooden wall assembly, a daylight basement (details above), and an attic space that I would like to be conditioned. I would rather not use spray foam insulation (although I would consider it in those hard to reach places. :)
Mold resistance is the #1 priority, followed by energy performance and the lack of off-gassing chemicals from foam.
If we went with the foam sheathed walls, would you recommend 1" of XPS on the outside with Dense Packed Cellulose in the stud bays? Would something similar work in the basement (XPS on the interior)? How about the attic? Could we use cellulose under the rafters instead of having it blown on the attic floor? Should we use an exterior XPS sheathing on the roof as well?
I really appreciate it!
Thanks, Mike
These would be my suggestions for a safe well-insulated home in your climate zone that would sidestep common sensitivity issues.
Roof: I'm guessing that you are hankering after a conditioned attic so you can safely run HVAC ductwork up there. A better strategy is to get the second floor ductwork in the first floor ceiling by means of some carefully placed dropped soffits. Then you can pile cellulose on the second floor ceiling to your heart's content - cellulose is much more effective on the ceiling than at the roof deck, not to mention easier and less expensive to install.
Walls: dense pack cellulose plus SIS or non-structural foam board to the exterior to eliminate thermal bridging.
Basement: Line the walls with R10 or better foam board if you're not initially heating and cooling it, add framed walls to the inside of that when you finish it with additional insulation of your choice.
Also: avoid OSB in engineered framing lumber, cabinetry etc. LVLs should be OK.
Michael,
Since you've already had to deal with mold, are sensitive to it, then consider two things:
1, Do super insulate as Martin suggested. What ever the plan is, have a WUFI study done on the wall. Especially if there will be a vapor closed foam used. The WUFI study should be done by someone who understands your climate, may well indicate a potential problem and allow you to avoid it. I imagine dealing with mold a second time would be disappointing.
2, I would advise trying to back away from foam if possible . Since you stated that you want the wall to dry both ways, that means a relatively high permeability both ways. Cellulose is a good product for sensitive people. You can take it a step further by using a cellulose product as exterior insulation also. Consider a Homosote roof board in place of foam boards on your above grade wall. Place them behind a rainscreen.
Since your going to probably run AC, make the envelope tight and then ventilate!
Okay... That was 3 things.