Wall structure for Zone 7 home

Good evening everyone,
I’ve lurked here and over at greenbuildingtalk for awhile now, as I work towards building a home in Steamboat Springs CO (actually north of town a ways).
Anyways, I was hoping I could get some feedback on the wall structure our architect has spec’ed from the home.
Background:
2 story home of 2180 sq ft, with 420 of that an attached garage.
Utilizing a shed roof (no attic) with cold framing.
Our lot is pretty heavily wooded at 8000ft in Zone 7B (dry but snowy).
The architect is focused on meeting code minimums:
Ceiling R-49
Walls R-20 + R-5 (or R-27 interior-only)
For the ceiling the architect has spec’ed 7″ of spray foam for R-49. Because there is no attic, the vaulted ceiling would be sprayed between 14″ TJIs (16″ oc) spanning the whole width.
For the walls they have spec’ed Zip R-6, with 2″ of spray foam (R-14) and 3 1/2 batts (R-13) for a total of R-27+6. This is in 2x6s with 16″ oc spacing, to be clad with fiber cement siding (LP likely).
Does anyone have suggestions for how we might economically improve on these two assemblies? I’d love to get closer to the Pretty Good House aspirations of R-40 walls and R-60 roof, but I’m worried I’ll blow our budget!
Thanks for any advice.
– Corey
GBA Detail Library
A collection of one thousand construction details organized by climate and house part
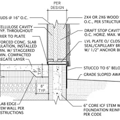
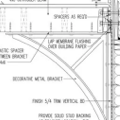
Replies
The design decisions already made make recommendations pretty limited - you have a roof assembly that (generally, with a few small exceptions) will need to be insulated with closed cell spray foam. You have a wall assembly with continuous foam on the exterior and closed cell spray foam on the interior. Without revisiting larger concepts, the only advice that seems applicable is 'more spray foam'. You have 14 inch deep TJIs in your roof, so you can go deeper there. You have 3-1/2 inch batts in the walls, pull those out and replace with more spray foam.
If you haven't started building yet, an alternative suggestion would be to revisit your wall and roof assembly entirely. The Pretty Good House concept includes the idea that perfect isn't always possible, and compromises are acceptable. Projects can adopt some PGH concepts and leave others on the cutting room floor, and still end up with a better project than they started with.
However, the assemblies you've described leave a lot on the cutting room floor. Specifically, the extensive use of foam products is not only an expensive choice, but ignores the low-carbon principal that runs throughout the PGH concept.
If your roof design is modified to have a venting layer under the roofing, cellulose could replace the closed cell spray foam in that area. If you are able to build a thicker wall, a double stud wall with cellulose insulation could replace the spray foam and exterior insulation in that assembly. If those are changes you are interested in making, I'm sure there will be a lot of advice forthcoming.
Either way, best of luck with your project and I hope my advice isn't discouraging. No one learns 'low carbon building assemblies' in grade school, so there is always a learning curve.
EDIT: It's been pointed out down thread I missed that the roof would be ventilated.
You can easily add some batts to the roof under the spray foam to get you up to R60+ pretty easily. With cathedral ceilings spray foam is probably our best option, but you don’t have to completely fill the cavities with it — you need enough for moisture control (which you certainly have with 7”), the rest can be batts or blown insulation in netting.
For the walls, I would skip the spray foam. Spray foam is really a waste in walls due to thermal bridging of the studs. I would use thicker Zip-R on the exterior, and then mineral wool batts in the walls. This would get you around R24 in the wall cavities, but going to Zip R9 on the exterior you’ll get a better performing wall (due to the exterior foam not being affected by thermal bridging) even though the R numbers using simple addition would appear to be the same.
You don’t need spray foam in the walls for air sealing. Detail the Zip sheathing as an air barrier and you’ll be fine, and if you use the airtight drywall method inside in addition you’ll be in very good shape.
Bill
In Zone 7 you need 60% of your roof R value to be impermeable insulation, so for an R49 roof, that is R30 of SPF (~5"). The rest can be batts.
In snow country with 14" TJI, I would recommend getting some venting into the assembly though. Thick snow on a low slope roof is a good insulator and you might end up with a lot of snow melt/ice dams.
To do this, you can staple a sheet good (house wrap/osb/fiberboard) to the underside of the I-joist top flange and spray against it. 5" of SPF followed by 2x6 batts would give you a much better roof than 7" of SPF. You can even bump up the batts to 2x8 stud with a smart interior vapor retarder and get close to an R60 roof.
For the walls, I would follow Bill's recommendation or build with 2x8 24"OC with R30 batts and no exterior insulation. Either case, a rain screen under the siding is a very good thing.
P.S. 7" SPF is only R49 at the start, the long term R value is closer to R39. The 5" SPF+R19 batts be around R46.
Akos, thanks for this. If we wanted to do more R in batts (say, R-25 batts) would we need to increase the foam density to maintain the 60% ratio? (eg 6" SPF for R-41 + R25 8" batts)
As long as you keep the ratio to 60% you can definitely bump up fluffy insulation. You can also push the ratio a bit if you have a good warm side air barrier (ie no pot lights) + smart vapor retarder.
SPF is very expensive and not the greenest building material, I generally try to design it out of a new build. Looking at your drawing, your slope is not that low and you are doing a 2x4 top vent as well. I would go with a simple vented assembly bellow with fluffy insulation and skip the SPF. 12.5" of high density batts would get you an R50 roof for much less money.
Even in zone 7 there is very little energy saved between an R50 and R60 roof.
I’ve had issues in the past when using flimsy film-type materials (like housewrap) as a backer for spray foam. I would use either ripped pieces of thin sheet goods (luan, 3/16” hardboard, etc, whatever is cheap), or 1/2” polyiso instead. Those can all be tacked in place with a staple gun to hold them in place during spray foam application. The spray foam itself will seal them in to provide permanence on completion of the project.
Bill
crawfoco,
I am at 8000' southwest of you. A few other things you might want to consider now.
Have you selected triple glazed windows? You don't mention any window choices, but compared to walls they are perhaps more important than going from R27 to R40 walls. If you punch a few hundred square feet of R3 holes into an R40 wall it really messes with the whole wall values. Much like the studs degrading the spray foam R value. It is easy for windows to be half of the BTU loss per hour in cold weather, which you certainly have up there.
Have you and the architect discussed current fire code rules in your area. In my area, the fire rules have gotten a lot more demanding. Even if you are escaping some code restrictions by not being in Steamboat proper, the state may have overriding control. Aside from clearing vegetation from home and access routes, you will need to review vents for all parts of the house. Dryer, stove, HRV, and especially if you go with a vented roof. Siding choices as well as window material choices may be in play as well. Which, by the way, have you actually confirmed that you can get home insurance?
Given that you are in a high snow zone, have you considered how close to load minimums you want to be? Also, have you thought through where the snow dumps? Will snow brakes be needed or even useful? Even with foreknowledge of the issue, I regret not having put even longer eaves on the north side. The piles stays til nearly the end of April. My main concern is the pile tends to pack up against my siding. No problems yet, but another foot further away would help a lot. Regarding snow brakes, I am of mixed feelings. My pitches are low so I didn't go with them. I skipped gutters on the advice of local experience. The general feeling is that ice build up and the sliding snow just rips them off. (I can post pics of my "snownamis" rolling off the roof if you like.I did make sure the garage doors face south and the roof dumps east, but your view selection may not allow the choice. The snow here is fluffier than the midwest's, but still a pain to move if piled up in front of the garage.
Low pitch roofs are tricky to ventilate and also require the vents to be fire ember resistant. I went with a non-vented design and will also do so on my next build. I used R35 nail base from R Control for the main roofs, covered with Hi Temp Grace watershield then clip style standing seam or PVC membrane for the 1.5/12 roof planes. Framing is a mix of solid wood, TJI and truss, with R19 batts. Do review how batts will be constrained in place, the presence of spray foam may interfere with some methods.
While my non-permeable sandwhich is thicker, my initial roof sheathing is vapor open to the inside with batts and drywall being the buffer. The first deck never sees temperatures below 50-60F so moisture issues in this dry climate should be nil. In your spec, the roof sheathing will be sealed both sides and with the spray foam, difficult to replace sheathing in the future should that be necessary. It is done this way often, but the overall track record is short enough to not offer solid evidence of long term results.
Venting over the roof sheathing with sleepers and second decking is probably safer than trying to utilize vent shoots between TJIs. This will still leave the primary deck sheathing subject to very cold temperatures so flash and batt will still be your insulation choice, provided it is closed cell like Sam said. Best to keep all the engineered wood on one side of the moisture equation. I would be belt and suspenders with the primary deck protected with synthetic roof paper, sleepers, and then whatever high temperature product type will be backed by the roofer (pending code approval). Even at 8000' your roof material will get mighty hot.
I am considering the R12 ZipR product, but be aware that following the nailing pattern to ensure racking resistance is properly transferred to framing is an issue. Even with the thinner grades. Your wind loads may be much higher than in my location, so getting the product put on right is critical. Inset bracing or interior plywood details might help ensure a stiff enough envelope. Do search the GBA questions section for ZipR and read what others say. I am a fan of outsulation and may re-visit that on the new build, but finding crews that will work with you can be difficult.
It is your budget and home, but I find it sad that the builder/architect are only aiming for code min. Your area is probably on par with Gunnison and maybe Leadville, so I would expect more effort to insulate beyond the minimum. Propane may be cheap now, but your home is for the years. Good windows and doors will be the quickest upgrade that pays benefits both in energy and comfort. More insulation is a longer payback and some people enjoy wearing sweaters. Fire hardening beyond the minimum protects your investment and your life.
I appreciate the detailed reply Roger. Lots to digest there!
Thanks for all the replies so far!
Attached is a snapshot of part of the plans, to clarify the roof structure and show the annotation for the wall insulation.
We aren't building yet (currently tightening up the budget, which includes insulation costs) which is why I was hoping for feedback before locking it in. So much appreciated there.
For the roof: Because we are framing a 'cold roof' on top of the insulated ceiling, would it be easier to install rigid foam above the ceiling (under the cold roof 2x4s) than to hang R14 batts in the TJI bays?
For the walls: I've tried to model the wall structure using the BSA tool: https://bsa.ornl.gov/. Maybe I'm doing it wrong, but it seems that with more exterior insulation and batts in the walls, it always calls out that there needs to be a vapor barrier installed. (Which is one of the reasons we went with flash+batt). Am I missing something there?
As far as revisiting the assemblies goes - I'm not closed off to the idea. Since we aren't building yet, nows the time to get the design right! However, because we already have a pretty small floorplan, I wouldn't want to expand further inside with say, double stud walls. Is there another approach to the roof that would work better and not require spray foam?
Thanks again!
Are you working with a builder yet, or just an architect at this point? If your architect doesn't have a lot of experience with energy efficient building, you may want to talk to your builder about what they recommend - they may have experience with a specific assembly, and the more experience a builder has with something the more cost effective their pricing will be.
Looking at your attached drawing, your architect has provided ventilation under the roof cladding. This would allow the installation of dense-pack cellulose between the 14-inch TJIs. It may not be practical for a variety of reasons (lighting layout, subcontractor access, etc.), but the 'cold roof' part of the assembly is the important first step. I missed that in your initial description, I see now you mentioned 'cold framing.' At 14-inches deep, you would exceed the code requirements for dense-pack cellulose insulation in that assembly, but you would fill the entire cavity.
I believe your area is governed by the 2015 International Energy Conservation Code/International Residential Code. If this is correct (and no local amendments supersede the standard code requirements), a Class II vapor retarder is required on the "interior side of frame walls" (2015IBC R702.7). Likely your architect specified kraft-faced fiberglass batts for the 3-1/2 inch thick batts shown in the section - that would satisfy the requirement. I don't know why BSA is kicking out a 'new' requirement for a vapor barrier when you make certain changes - in climate zone 7 one is always required. Sometimes you can get away with a Class III vapor retarder, but some class of vapor retarder is always required (for above grade framed walls).
Changing to a double stud wall wouldn't add a lot of depth - your current wall is 5.5-inch (2x6) + 1.5-inch (Zip-R) for a total thickness of 7.0-inches before drywall and exterior cladding. A double stud wall insulated with dense-pack cellulose with just a one inch gap between the two walls has a thickness of 8.0-inches, an increase of only one inch. This one inch thicker wall uses no foam, includes a thermal break, and has a nominal R-value of R-30. It satisfies the 2015 IRC's alternative u-factor requirement detailed in table N1102.1.4.
That said, there are a ton of possible wall assemblies, I've just provided an example of one that doesn't include foam. If you start with the requirement "no foam in the exterior walls" or perhaps "no spray foam in the exterior walls, but I'm OK with continuous exterior foam", then you can see how your architect and builder respond. They may have a different way to answer the question.
If you want some reading material, check out "Construction Guidelines for High R-Value Walls without Exterior Rigid Insulation" by Lois Arena published July 2016.
Sam, thanks for all this advice. I am working with a builder, who directed me to the architect (actually an engineering firm that has an on-staff architect).
I'll run all this by them both and see if we can come up with any game plans to reduce the use of sprayed foams and reach better R values economically!
Using a parallel chord truss rather than a TJI could be an option. Have the truss sized to the depth you desire for insulation and fill with cellulose instead of foam. Typically I have used Intello or a similar product with this detail.
With cold sheathing (eg Zip-R or sheathing without foam), I'd definitely air seal the interior side. So if you omit the spray foam, use some other interior side air sealing method.