Welded Wire Mesh vs Rebar

I am in zone 4a. Pouring fully insulated (3″ XPS) monolithic slab for my dirt cheap pretty good house. I will be using the concrete as my finish floor and I will have 3/4″ pex radiant.
Options for reinforcement I am considering:
Rebar 16″ O.C. #3 (3/8″)
Welded Wire Mesh 6×6 W1.4 10 gauge (about 1/8″ diameter wire) 8’x20′
Regardless I will have 2ea #4 rebar in footer/edge beam
I am not sure which route is stronger.
The 8×20 panels will be about half price, but will have to sit on ground and be lifted as the pour happens. Also, they are 6″x6″ squares, so pex will be at odd locations.
The 3/8″ rebar would be spaced exactly at 16″ (pex spacing) and would be on chairs.
Making sure the mesh is lifted is not a problem in that I will have a good size crew of help, and I can assign one or two detail oriented guys the job of making sure that happens.
I THINK, but do not know that the wire mesh is a stronger route. I deduced this by a visit to the micro helix website (I am not using this). But their calculator recommended 4lb per yard for mesh and 11lb per yard with the rebar schedule.
Thank you for your advice.
-Mike
GBA Detail Library
A collection of one thousand construction details organized by climate and house part
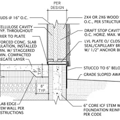
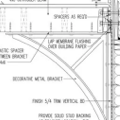
Replies
Mike, welded wire mesh provides control against cracking due to shrinkage but it does not add structural strength to the slab. The welded joints are not strong enough to resist the loads imposed. Rebar is "deformed" (the term for the rough surface) and minimum overlaps are spec'd in building codes because the concrete can grab onto the rough surface without slipping. A mat of #3 rebar will cost more to install but is a better system.
For control of fine cracking you could add poly micro fibers. One of the best things you can do to prevent or reduce cracking is to allow the slab to dry slowly--the chemical curing process requires moisture, so when concrete dries before it cures you end up with relatively brittle concrete.
Ahh, thank you for clarifying this. If I use WWM is fiber additive a waste? Or more crack resistance the better...belt and suspenders or throwing money out?
WWM and fibers are both meant to control relatively small cracks, so I usually just spec fibers, but if a builder prefers WWM I'm fine with that--I just recommend being careful about keeping the mesh in the center of the slab, which is harder than it sounds. There is no reason you couldn't use them both together.
There is also a stainless steel fiber additive that is supposed to be as strong as rebar, but I have not tried it or know anyone who has.
For the radiant you may be better off with 1/2" pex with more but shorter circuits. It's much easier to work with. Make sure you use O2 barrier tubing.
3/4" can be tough to bend in a tighter radius.
Josh, I was not going to even plumb for radiant to save money; but, my friend had 1500ft of 3/4" pex left over from his house and shop, and he gifted to me, so it is 3/4" or I don't install pex. It is that kind of pex that is stretched and compresses onto a fitting and if it gets kinked a heat gun can bring it back to normal (not that I plan to test this theory).
-Mike
Make sure the pex you have has an O2 barrier. Without that you won't be able to use any cast iron parts without running glycol.
Mike,
If you go with mesh, use concrete chairs for support. The chances of consistently elevating the mesh you pour are almost none, and you really don't want to be hooking the mesh to pull it up when it has pex attached.
Malcolm, since the squares on the WWM are 6" apart, when the crew steps on it won't it deform the 10 gauge wire if on chairs? If it was 3/8" rebar @ 16"OC, they would be able to step between.
In absence of responses yesterday, I went with my buddies approach and picked up the WWM for the field. So mesh it is. :)
Use more chairs. If you are standing on the mesh and trying to pull it up a couple of feet away, it will at best be up in some spots and be on the bottom in others.
Check the specs for pouring slabs with mesh put out by any industry association or PEs. They all use chairs.
OK, I will lookup the proper chair spacing and do it. I sure do not want it in the bottom of my pour. BTW, what is a PE?
-Mike
PE means “professional engineer”, people with that designation are licensed by their state. It is someone who can seal drawings for submission to the city. Many of these guys are structural engineers or civil engineers, but “PE” alone does not denote any particular engineering specialty.
Bill
FWIW, you may not want to use fibers if the concrete is going to be your finished surface. The fibers show up at the surface and can look a bit funky. I see this all the time in trowel-finished concrete, but not sure what happens if you polish the concrete mechanically after curing.
How do you plan to finish it?
Peter, good point. If they are micro-fibers, polishing shears them off and they aren't noticeable. But we had a nightmare on one job when the batch plant used heavy-duty fibers by mistake, and the slab was not polished, just trowel finished. They eventually had to polish (grind) the surface, but only after trying to get the fibers to lay down using exterior-grade sealer, which stunk up the house and didn't fix the fibers.
Peter,
In shop side, I plan to leave it concrete and only seal it as welding spatter will not go with any pretty finish as far as I know? Do you know of an attractive route that can withstand shop conditions?
The house side, will be acid stained.
I was trying to find out about the fiber as a problem for the acid stain. I read in one case you can torch the concrete surface and they will burn off. I contacted my local ready mix and he said no problem aciid staining with fiber in concrete?? Of course, he does not finish concrete, he delivers it. If it is a problem, I will not use it... Maybe I use it in the last truck for the shop entrance area where heavy vehicles will enter the shop??
For the shop, I wouldn't worry about the fibers or the finish - You're talking about trucks, welding spatter, etc. That calls for a heavy duty slab, and the patina it takes on over time is just part of its charm. I would definitely go with the fibers and the rebar.
For the house, the fibers could be more of a cosmetic concern. The fibers are selected to be alkali resistant, but I have no idea whether that means they are also acid resistant. Probably. If you are going to polish and seal the interior floor, that will probably grind off the tips of the fibers, but you might still see some staining effects of different uptake in/around the fibers and in field of the concrete away from the fibers.
Your local batch plant is normally a great resource for information about their product. They don't want you to be unhappy, and they've probably heard nearly everything that can go wrong with their product.
I prefer to use micro fibers in my slabs. I never have an issue with finish with them, the fibers don't stick out, as long as you finish the concrete well, trowel to a glass finish. It'll being a good layer of cream to the top.It makes for a more matte and uniform appearance compares to grinding finishes.
Rebar makes use of more space than wire mesh. If you work into wire, then much saver space more than rebar welded. Rebar vs. wire mesh can have costly differences. Rebar remains stronger and ensures consistent contact in the soil, whereas wire mesh is unpredictable and often results in a weak concrete foundation. I found a good review https://bestmigwelders.org/hobart/ on Google search; you can check it also. It might be helpful for you.