What happens if rigid foam insulation is placed between vapor barrier and a concrete slab pour?

I was recently reading BSI’s 2010 Building America Special Research Project: High R-Value Enclosures for High Performance Residential Buildings in All Climate Zones (Available here: https://buildingscience.com/sites/default/files/migrate/pdf/BA-1005_High%20R-Value_Walls_Case_Study.pdf), and page 35 states that “In no case should a membrane be placed below the insulation as this can allows ground water, flood water, or mix water to be trapped between the concrete slab and the membrane.”
We just poured a ~ 150 ft2 mudroom slab (~ 4-6″ inside the thermal envelope of the building), and I am in the Seattle area with Climate Zone 4-C. Unfortunately, my contractor placed the vapor barrier (10 mil polyethylene) under the double-sided foil-faced polyiso, placed chairs for re-bar on the polyiso (and rebar grid onto of that), and poured the slab ontop of the insulation. Seams in the rigid foam layer were not taped, and 2 extra-deep 4 sqft reinforced pads were placed through square cutouts in the foam layer (with only poly underneath). Image pre-pour attached.
What exactly is the concern here? Perhaps pockets of air + water = mold? Concrete durability?
And is there anything I can do to ameliorate or prevent any related problems now that it’s already poured? We were planning to polish it, but maybe a sealant is better now?
GBA Detail Library
A collection of one thousand construction details organized by climate and house part
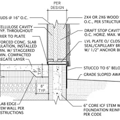
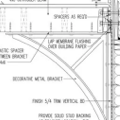
Replies
One concern is before the concrete has been poured, as you have made a bathtub and put foam in it. If it rains the foam will float up and is hard to remove the water. Once the concrete is poured as long as you tie in the poly to your foundation wall waterproofing layer, to keep water from getting in above it, the concern is minimal.
Thanks Frank,
Good point re floating foam. Hopefully the rebar anchored it down while curing, as it did rain some about 2 days after the pour.
It sounds like the concern after curing is mainly with water getting under the cement it over time and simply obviating the function of the poly, is that right? So the consequences are akin to having no poly inderlayer?
And if the slab is indoors and the foundation is reasonably well drained at the footer and the stem wall damp proofed, then perhaps there should be no issue?
Unfortunately, as you can see in the picture I just added to the main post, the poly does not fully extend through the slab where it meets the stemwall. There may be enough poly sticking out into the crawlspace that I can make a sealed seam with the crawlspace floor poly, but it looks to me (post pour) that there is only an inch or two of the poly sticking out— if that.
I’ve just discovered this similar Q&A. Theirs is EPS with taped seams and wire mesh instead of rebar, but otherwise seems pretty similar and also seems unlikely to produce negative problems so long as the foam doesn’t float.
https://www.greenbuildingadvisor.com/question/vapor-barrier-placed-under-eps-need-to-fix