Quantifying global warming potential of various rigid foams?

It’s easy enough to find the GWP of blowing agents used for various rigid foams. For example, from the info I’ve found on GBA and elsewhere:
EPS (all types) uses pentane, GWP=7
Typical XPS uses HFC/HCFC blends, GWP=1430
Soprema Sopra XPS-30 uses undisclosed formula, GWP=1
What I haven’t found is how much blowing agent is used to produce, say, a pound of each type of foam. It seems like that’s an important number.
That is:
Does it take twice as much pentane to produce Type I EPS (1lb./CF) vs. Type IX (2lb/CF)? Or half as much? Or is there any difference?
How does the amount of HFC/HCFC required to blow typical XPS compare with the amount of pentane required to blow EPS?
How does the amount of Sopra’s blowing agent per pound compare with the amount of agent per pound used for typical XPS and EPS?
It seems if Sopra uses 7X the amount of blowing agent per pound as Type IX EPS, the actual carbon footprint of using either below grade would be about the same. (Assuming one can simply multiply the GWP of the agent by the quantity of agent used.)
Can anyone point me in the right direction?
GBA Detail Library
A collection of one thousand construction details organized by climate and house part
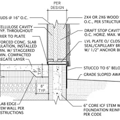
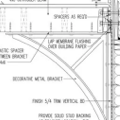
Replies
I don't know of that is published data anywhere, and it might vary based on manufacturing process too, i.e. one manufacturer might use more or less blowing agent per unit of foam made compared to someone else. Another thing to consider is that the blowing agent is often recovered during manufacture, I know that is commonly done with EPS. That's similar to how metal processing plants typically collect their scrap leftovers to be melted down into new material to be reused. A lot of effort goes into many manufacturing processes to limit waste, to keep costs down.
There is also a new "green" variant of XPS out there, which apparently is more available in some regions than others -- I haven't seen it at all in my region yet.
What you might want to try to do is to determine how much blowing agent REMAINS in the finished product after manufacture, which would be the blowing agent that would presumably diffuse out into the atmosphere over time.
Bill
Hi Bill,
Thanks the reply. Sopra XPS-30 is the greener XPS available in my area (I'm just across the border from WA State, which has banned HFC/HCFC blown XPS). I used it for my build.
I assume there's as much recovery of blowing agent as possible during manufacture, but presumably there's not only losses in recovery, but also some the remains in the product, as you say.
So I suppose what I'm after is *net* quantity of blowing agent consumed per quantity of foam, during or after manufacture.
With a little more looking, I was able to find environmental product declaration for EPS, typical XPS (Owens-Corning Foamular), and Soprema Sopra XPS 30.
1 M^2 of thickness measuring Rsi 1 (R-value 5.68) of EPS has GWP=2.79 kg Co2 eq.; Foamular GWP=58 kg CO2 eq; and Sopra XPS 30=GWP 2.06 kg CO2 eq. These figures are all cradle to grave.
Assuming I read the LCAs correctly, that means typical XPS is still really bad compared to EPS and greener XPS like Sopra (like 20-30 times worse), but the difference is not nearly what just comparing blowing agents might suggest.