What is the best approach to insulating my MCM home?
I’m in the midst of a total renovation of a late 1950’s house and am afraid my head might explode trying to decipher all the intricacies of insulation options.
I have found this website to be something of a beacon of intelligent, well thought out answers to those of us who don’t know where to turn for such guidance.
The basics-
Located in central Indiana, along the southern border of 5A.
Single story with a walkout basement.
1000 sq ft of “butterfly” roof, 500 sq ft of “shed” roof.
Continuis screened soffit venting on sides with rafter ends
New epdm roof over 1.5”-2” of polyiso
Exterior-fiber cement siding/ Tyvek/ old Celotex fiber panels
Interior- totally gutted- 2×4 walls, 2×8 rafters
The questions-
Am I correct that due to the polyiso on top of my roof decking, I do not want a vented roof insulation system? If so…would 4-5 inches of friction fit polyiso(cut & cobble), sprayed with 1” of closed cell foam be acceptable? What about high density fiberglass batts?
Which would you recommend on the walls- open cell foam or “spider” …or something else?
Any input would be greatly appreciated. Thank you
GBA Detail Library
A collection of one thousand construction details organized by climate and house part
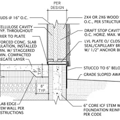
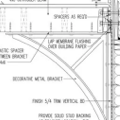
Replies
User-7127449,
First of all, can you tell us your name? (I'm Martin.)
I don't know what "MCM" stands for. Maybe "McMansion"?
Q. "Am I correct that due to the polyiso on top of my roof decking, I do not want a vented roof insulation system?"
A. Yes, except in the unlikely event that your roofer included a ventilation channel between the top of the polyiso and the underside of the EPDM.
Q. "If so...would 4-5 inches of friction fit polyiso (cut & cobble), sprayed with 1” of closed cell foam be acceptable?"
A. If you are talking about blocking the soffit vents, that sounds like overkill. All you need is an air barrier to block air from entering the soffit vents. One-inch-thick polyiso, installed in an airtight manner, would work.
Q. "What about high density fiberglass batts?"
A. Now I'm thinking that you're talking about installing insulation on the underside of your roof sheathing. In Climate Zone 5, a roof that combines rigid foam insulation above the sheathing with fluffy insulation below the sheathing needs at least 41% of the R-value of the roof assembly to come from the rigid foam layer. Generally that means that the rigid foam needs a minimum R-value of R-20. Your roof only has R-10 of rigid foam in the 1.5-inch-thick sections, and that's not enough. That limits your options. For more information on this issue, see "Combining Exterior Rigid Foam With Fluffy Insulation."
To address this mistake, you can either skimp on the fluffy insulation, and end up with a poorly insulated roof, or you can install closed-cell spray foam on the underside of the roof sheathing -- thereby encapsulating the sheathing in two vapor-impermeable layers, which isn't ideal -- to make up the missing R-10.
Q. "Which would you recommend on the walls- open cell foam or Spider ...or something else?"
A. Almost any type of insulation will work, if it is installed conscientiously. Careful installation matters more than material selection.
In zone 5A you want at least 41% of the total R to be above the roof deck. IRC code min R is R49, so that means 3.5-4" of polyiso above the roof deck, R30 rock wool batts (or Spider) in the 7.25" deep rafter bays gets you to compliance on an R-value basis.
But with the R10+ thermal break over the rafters you could get there with about R40-R42 total on a U-factor basis. What is the roof deck material/thickness and can we assume a half-inch gypsum ceiling?
Assuming R10 above the roof deck, 2" of HFO-blown closed cell foam runs about R14, which puts the first condensing surface (the interior side of the closed cell foam) at R24 in from the outside, and leaves 5.25" of cavity for fiber insulation. If you filled that with 1.8lbs density Spider or rock wool batts it would perform at about R22, bringing the center-cavity R to about R46, and it would almost certainly make code-min on a U-factor basis.
At 2" the HFO blown closed cell foam would still be in the middle of Class-II vapor retardency, plenty tight enough for protection of the roof deck against wintertime moisture accumulation, but also sufficiently vapor open to be a reasonable drying path.
You could also get there with 2" of HFC blown foam (about R12), but HFC245fa has more than 500x more environmental impact than HFO1234ze. In my area 2" of HFC blown foam would run about $2 per square foot, HFO blown foam would run about $2.50 per square foot.
Sorry Martin, my name is Don, and MCM = mid century modern. I REALLY appreciate the input from each of you. Unfortunately I can’t increase the thickness of the polyiso between the roof deck & the epdm. Dana, the roof deck is plywood, either 5/8” or 3/4”, and the gypsum board will be 1/2”.
To meet code on a U-factor basis requires dropping below U0.026 or R38 "whole assembly", with the thermal bridging of the framing and the R-values of all layers factored in. Worst-casing it:
Assume the exterior foam +roofing adds up to at least R10
Half inch gypsum is worth R0.45
The plywood is worth at least R0.77- R0.94
At a typical 7% framing fraction the 2" slice with the R12-R14 closed cell foam is worth at least R9.4 (HFC foam) to R10.4 (HFO blown foam) after thermal bridging with 7% of the area being R1.2/inch wood framing.
The 5.25" deep slice with the R22 fiber is worth R18.85 after thermal bridging.
Interior & exterior air films add up to about R0.8 in winter, R1.15 in summer.
So add it up: R10 + R0.45 + R0.77 + R9.4 + R18.85 + R1.15 = R40.6 "whole assembly", or (U=1/R) ...
U0.0246
...which is lower than the code-max U0.026...
...and thus meets code on a U-factor basis, despite having less than R49 at center cavity. With HFO blown foam and using the annual average R values for the air films it'll do even better.
If the rafters are 12" on center or something your framing fraction could be higher than 7% which would give you a bit less margin, but you'd probably still make it.
The 7% framing fraction is the default assumption California uses, settled upon after a wide survey of existing real house designs. Your real framing fraction will be lower if it's a simple roof design with no skylights, dormers, hips, valleys, etc, but could be higher if it's fairly complex. Most mid-century butterfly roofs very simple two intersecting planes, and would likely have a lower framing fraction than 7%. A shed roof is simpler still, possibly an even lower framing fraction.
[edited for correcting arithmetic error]
head REALLY spinning...I am in awe of your knowledge. You have provided incredible advise on how to get my roof insulation up to code requirements. I realize I would not meet those requirements if I were to simply block off my soffit ventilation and fill the 16" OC rafter cavities with 7.5" of mineral wool, but would I be putting my roof deck in danger of moister damage?
Don,
1.5 inches of polyiso = R-10
7.5 inches of mineral wool = R-28
Total roof assembly = R-38
Percentage of total R-value coming from polyiso = 26%
Minimum requirement is 41%, so that proposal fails the test.
You'd hit pretty close to code-min on a U-factor basis with R30 rock wool batts in the cavities, but with only R10-ish foam up-top there's some risk of moisture damage if using only latex ceiling paint as the interior vapor retarder. Even in zone 4A code prescriptives call for R15 out of R49 to be outside the condensing surface (= roof deck).
That's a bit more than 30% of the total. R10 out of R40 would be only 25%.
With low density R25s (R24, when compressed to 7.25" in a 2x8 cavity) you'd have R10 out of R29 total, which would still only be 29% of the total, not quite good enough for the cold edge of zone 4A.
A flash-inch of closed cell foam would provide sufficient vapor retardency to protect the roof deck, and leave a 6.25" space for the fluff. Compressing rock wool R30s (or 1.8lb Spider) into that space would yield about R26, and you'd have R16 outside the condensing surface (which is now the foam), yielding a total-R of 42. R16 out of R42 is 38% of the total, and in most cases would be good enough for the WARM edge of zone 5 (even if it it's not quite the prescriptive ~41% for zone 5 in the IRC.) That stackup might just duck under U0.026 and meet thermal performance compliance on a U-factor basis too, using only half the amount of spray foam. That's probably worth running by the code officials, assuming you need their sign-off.
With an inch of closed cell foam on the underside of the roof deck it's already fairly well protected even without the R10 up top. See Table 3 in this document:
https://buildingscience.com/sites/default/files/migrate/pdf/BA-1001_Moisture_Safe_Unvented_Roofs.pdf
Look at the "1" ccSPF + spray fiberglass" column. Then come down to the zone 5A Chicago row. With 1" /R6 of foam and R32 fiberglass look favorable for the roof deck with dark colored roof, and only a slight risk with a light colored metal roof. The paper doesn't assess the condensation risk in the fiberglass, but the roof deck is pretty solid. That's at the cold edge of zone 5A, with NO insulation above the roof deck. Your situation would be much less risky, given your higher wintertime average temps, and the foam above the roof deck.
Martin: Most rock wool batts in the US designed/marketed for 7.25" deep rafter bays are R30, not R28. (In Canada the R28s are more common.)
As if you guys haven’t provided me enough information...
75% of the ceilings of my home are the vaulted rafters we have been discussing, the remainder being flat ceilings with a cavity of “attic” space above-2’ being the maximum height tapering to nothing. I do not intend to have access to these areas once drywall is installed.
Would it make more sense to simply insulate under the entire roof deck in the manner you have described(it is all quite accessible) or should I nsulate the flat ceilings separately with mineral wool batts(insulating the portions of the wall as well)?
If the exterior foam is over the roof deck in the low-height attic area, your not allowed to add attic floor R to roof deck R to meet code on an R-value basis.
Installing batts snug to the roof deck and air-sealing the attic from the outdoors is the right way to go there too.
Be sure to insulate any exterior walls from the attic floor up to the roof deck insulation too, and install interior side air barriers on both the roof & wall fluff. The interior side air barrier can be something flexible and at least semi-permeable to water vapor (housewrap is fine), as long as the ceiling is going to be air tight and painted. If you're not sure how leaky the ceiling will be (maybe somebody will cut a big hole to install lights at some later point), using a smart vapor retarder such as Certainteed MemBrain or DryRight detailed as an air barrier would be cheap insurance. See:
https://www.certainteed.com/resources/3028122.pdf
DryRight is available through Menards, MemBrain is available at HD & Lowes. They may need to be ordered online.
I'm not sure what, if any difference there is between the two. Both are 2-mil nylon, DryRight is blue, MemBrain is clear.
Don,
If your attic "tapers to nothing," it's basically useless for insulation purposes.
I'm not sure what your mean by "insulate under the entire roof deck in the manner you have described," but if you choose one of the methods advised on the GBA web site, while simultaneously meeting minimum code requirements and keeping your local code official happy, then you are all set.
Would the use of a product such as DryRight or MemBrain only be appropriate on the walls and ceiling within the attic area? Not to be used between the gypsum on the walls and the spider or open cell foam insulation...nor between the rock wool insulated ceiling and it’s gypsum?
Don
Don,
Your question is confusing.
First, I had to research DryRight. It turns out that DryRight is the CertainTeed brand name for its fiberglass batts with an attached layer of MemBrain ("smart" retarder).
In theory, you can use DryRight (or unfaced fiberglass batts plus MemBrain) in most locations where you would ordinarily use fiberglass batts. The smart retarder won't cause any problems, and it sometime provides benefits by slowing the diffusion of interior moisture toward the exterior during the winter. Sometimes the upcharge for the smart retarder is a waste of money, however.
In order to evaluate whether the use of an interior smart retarder makes sense for you, you'll have to describe the entire assembly where you are thinking you might use it (that is, each layer of the assembly, from the interior to the exterior or vice versa).
Sorry Martin,
From outside in-
Walls: fiber cement siding, Tyvek, old Celotex fiber panels, 3.5” of open cell foam or spider, 0.5” gypsum
Roof: epdm, 1.5” of polyiso, 5/8” plywood, 1” closed cell foam, 6.5” of rock wool, 0.5” gypsum
Wondering if a smart retarder such as Membrane should be installed behind gypsum.
Thanks again,
Don
Don,
In your climate zone, building codes require the installation of a vapor retarder on the interior side of your walls. MemBrain is one option, but vapor retarder paint (applied to the drywall) would probably be cheaper.
With the roof assembly, as Dana noted, you've got only 38% of the R-value in the foam layers instead of the 41% required by code. Making the spray foam layer a little thicker is one way to improve the stackup (in which case no interior vapor retarder is needed). Or, if you decide to stick with the 38% ratio, interior MemBrain might give you enough of a safety margin to get away with the 38%.