What kind of exterior wall to build above foundation susceptible to capillary suction and ground moisture?

hello all … im gonna give details on my scenario, and invite any comments
i am in the middle of renovating a 1story 3000 sq ft ranch house that sits perched on a very high water table. the main reason for the renovation was due to major moisture infiltration into the home, along with the horrid stuff that comes along with the wet on paper and wood.
the house was built on a poured concrete foundation recessed 2 to 4″ below grade with a 9″ concrete ledge … 7″s of the ledge above grade (similar to a reversed brick ledge). So the sill plate is 2 to 4 inches below grade sitting behind that concrete lip, and the bottom of the rim joist is slightly near flush with the surrounding grade. The original exterior stud wall was built vented to the soffit, around 12″ open to the soffit vent going into the attic. The attic ridge was not vented, they had 2 12″ vent fans trying to control the humidity. We were pumping out around 100 liters of water every 2 to 4 days via humidifiers within the building envelope. In dead winter the water table is around 1′ to1.5′ below the foundation footing … come Spring its gotta be right on it … come Spring rain its 1.5′ above it.
So we ended up gutting the house, it had an amazing plaster job (unfortunately).
Exterior excavation work: dug down to the footings on the exterior foundation, installed drain tile, put in 1.5″ rock up level to the sill plate, used Drylock on the exterior wall, put 3″ XPS foam all the way up flush with the rim joist around the whole foundation perimiter.
Crawl Space excavation work: put in interior drain tile around foundation, put in 3 sump pumps, dug out all the nasty dirt (septic was installed 15′ up slope of house and most likely washed in), installed radon piping, drilled 1/2″ weep holes 16″ oc under each joist, drylocked the top/bottom of interior wall leaving middle with no waterproofer … letting it dry to the interior…. hoping to break any capillary suction up into the above stud wall of the house. And then added 5″ of 1″ rock upon the 3000 sq ft crawl floor. Now before we added the rock in the crawl, the rim joists were getting hammered with moisture, and the majority of the sill rotted at the foundation corners. To fix that issue i am in the process of removing the sill plate, installing Solidguard LSL sill plate in leiu, putting Protecto sill sealer with 40 mil membrane underneath, cutting 1/2″gap in concrete rim ledge between the embedded rim joists so as to be able to run Grace Vycor or Carlisle 40 mil barrier along concrete rim down underneath Sill Sealer. Im pretty much trying to isolate the house from the concrete foundation, which the foundation has amazingly held up like a champ. Im in the process of putting XPS foam and a Griffolyn liner somewhere between the crawl space and the house floor joists.
Now heres my loaded question, what on God’s green earth (i really did have the greenest yard in town before excavation) do i put on that exterior stud wall (above the foundation wall)? My initial thoughts were that i had a few options:
1) Polyiso Foil faced 2 to 3″s on the exterior of the stud wall, leaving the stud wall cavity totally uninsulated … able to dry to the interior. Whats that do to the drywall though? the plaster took the moisture with no trouble.
2) Put the Polyiso foam on the inside of the stud wall, no cavity insulation, let it dry to the outside …
3) build another wall inside the foundation wall… similar to double wall framing technique but without any cavity fill … this wall version would have plywood or plank board (enabling it to breathe the moisture if it came up thru the foundation via capillary suction) on the outer exterior wall covered by a wrb wrap, then build a wall behind the outer wall with ZIP panel sheathing (to make the building envelope air tight) with 2 to 3″ of Polyiso directly behind the ZIP….. pretty much sandwiching the ZIP and Polyiso in between the exterior and interior stud walls. To make it air tight I would nead to find a way to seal to the floor and ceiling … I am contemplating putting down 60 psi XPS foam on the floor with dimple membrane above it, warmboard on top of the dimple matting for radiant heating. For the ceiling I would need to put up Polyiso or XPS with furring attached to the bottom of it followed by wood paneling or could risk drywall. …. this would be an expensive step!!!!
Lots of lines here … to note, the ceiling joists got hammered with moisture, especially by the fireplace (hence apprehension about cap suction) … fireplace ended up sinking (during the renovation) 2 inches and thus got taken out.
I guess i could wait till mid Spring to build the final wall details out, in order to see if i cut off the moisture drive from the foundation wall. We had the AC go out during a summer week averaging 100 degrees with rain, very humid here in Illinois … and the hardwood floors were puddling with water …couldve been the open stud wall to the soffit and non vented attic, along with no vapor barrier in the crawl. Though the way those Rim Joists were crystalling with frost this winter makes me hesitant. Could always do the obvious in jacking up the house or grading down (not much of an option on the grade) … lots of cost on jacking up a house in the shape of a T. Definitely hesitant about ever venting the soffit and attic again… Although its the obvious thing to do in a dry climate … I may look to bring these into the conditioned envelope … unless i could find a way to keep the moisture off the ceiling joists ….The rafters and roof sheathing amazingly didnt change color but held up. If i could build from scratch I’d be putting the house on piers … but we do get cold weather here in Illinois.
Thoughts?
GBA Detail Library
A collection of one thousand construction details organized by climate and house part
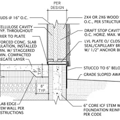
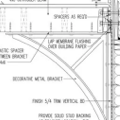
Replies
here's a quickpic of an identical house foundation setup similar to the one i am dealing with ...
typo in foundation depth, the footing is down about 32" below grade .... 39" wall height total .... 7" high ledge at 4" wide.... sill plate sits 2 to 4"s below grade flush with bottom of 7" ledge.
picture
Jon,
It sounds like you have invested tens of thousands of dollars in a house that (perhaps) should have been demolished.
Did you every consider jacking the house up two feet and extending the foundation? Alternatively, it might have been useful to use excavation equipment to lower the exterior grade -- assuming that a new lower grade could have been sloped away from the house.
In any case, you aren't describing a pretty picture. If you have managed to install a layer of Grace Vycor between the foundation and the sill plate, at least you've introduced a capillary break between your wet foundation and your above-grade wall. That step is essential, so I hope the job was done conscientiously.
I think that your above-grade walls can be built conventionally. Here's why: either you have licked your problem of wicking moisture or you haven't. If moisture is still wicking into your above-grade walls, your house is doomed, no matter how you insulate your walls (unless, of course, you rebuild your above grade walls with CMUs or ICFs).
If, on the other hand, you have solved the problem of capillary wicking, then your walls should be OK, and you should build the wall assembly you prefer.
Martin
thank you for the reply. Yeah thank goodness Ive done the work myself, otherwise the hole in my pocket would be tenfold.
My initial thoughts on the solution were to find a way to isolate the house from the foundation. Im waiting on a bid to get the house jacked up ... if its in a good price range we may go with it. Though, getting back to a few points I have in mind:
1) Can 60 psi XPS foam be slipped between the top sill plate of the upper stud wall and the rim joist that sits below it .... successfully? We could then hurricane strap the sill to the rim joist, and make our own isolation cap without jacking the house up 2 ft. I guess i could contact Owens on this.
2) How do I know if we've stopped the capillary action up thru the stud wall without finishing the wall? I guess I could sheetrock a portion now and watch it. Simple moisture meter, sit it out and wait? Would raising it 2 ft even help if the suction is that bad to begin with?
3) What is the usual cost on pouring a new ICF wall per sq ft. Contractor cost per say ... just in materials
4) The obvious question i should be asking, what kind of engineer should I be looking for to help answer these questions, and is there a link to a list of them in Illinois.
thx