What to do about rainwater trapped inside my sub-slab build up?

I have been losing a little sleep over my preparations for pouring a slab. I got 6-mil poly laid, 3″ of xps and wire mesh on top middle of last week when it was in the 70s, called for inspection and then called off the scheduled pour the next day because temps suddenly dropped into the 20s as this cold/snowy/rainy spell blew in to the mid-Atlantic. Now rain/melted-snow/sleet is puddling underneath the xps on the poly. I feel like this could be a problem, but I don’t really want to pull all of my 100 sheets of xps fitted around and over plumbing and electric piping. The water is trapped between air and vapor barriers (poly below, xps and concrete above) with nowhere to go. Ugggg. Am I silly to worry or silly not to spend a full day dismantling and reinstalling all the sub slab build-up once the sun comes out and it warms up?
GBA Detail Library
A collection of one thousand construction details organized by climate and house part
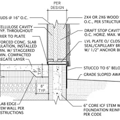
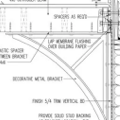
Replies
Hmm, you are worried about pouring concrete containing hundreds of gallons of water over some.....water
There is going to be some extra moisture to escape from the assembly. I would not see a problem unless you are looking to occupy in 6 weeks.
Your poly is supposed to be tight to slab. Redo time.
All the water under the slab has to go up through the slab. And future ground water too. Not a good assembly.
BSC says poly tight to concrete.
AJ Builder,
So where does the xps go in the build up? under the poly against the gravel? wouldn't it degrade over time being constantly exposed to ground moisture? If it makes a difference to responders, this is a slab on grade with 10-15" of 57s compacted under the assembly. I didn't tape or seal the poly or xps using Joe Lstiburek's rationale in a post on this website that the concrete slab is the air barrier in the assembly.
Jonathan,
The proper place for polyethylene is directly under the concrete. You put it in the wrong place. As you installed it, it can indeed hold water for a very long time, leading to flooring failures. If water ever works sideways from the edge of your slab due to a heavy rainfall, this mis-placed poly can be a long-term nightmare.
You need to get a piece of rebar and make 400 or 500 holes in the poly, by punching the rebar through the seams of the rigid foam. Help all that water to drain. Let the sun shine on the foam for a day or two. Then install new poly where it belongs -- on top of the foam.
This is interesting, and either many slabs here are wrong, or it is a debatable topic. Hmmm. Most folks that I have seen lay the poly on the compacted gravel, install the foam, and (sometimes) staple their PEX to the foam. This, from the DOE, shows the foam on top of the poly. http://www.google.com/imgres?imgurl=http://www.energysavers.gov/images/floating_slab_on_grade.gif&imgrefurl=http://www.energysavers.gov/your_home/insulation_airsealing/index.cfm/mytopic%3D11790&h=266&w=320&sz=17&tbnid=psF6bwl4t9tjDM:&tbnh=98&tbnw=118&prev=/search%3Fq%3Dslab%2Bon%2Bgrade%2Bconstruction%26tbm%3Disch%26tbo%3Du&zoom=1&q=slab+on+grade+construction&usg=__vvq_Vc4ebxIpcpX93G_Pi95UrSI=&sa=X&ei=CM-TTb7pKYnmsQPPp5TKBQ&ved=0CD4Q9QEwBQ
For a situation like Johathan's, I wonder if a wet/dry vac sucking through a 1/2" tube could remove the bulk of the water, then leave the slab bare for.... several months??.... a few years??
Thanks Martin, et al. I'll do as you said. I'm working off a set of drawings from my well regarded architect, so I'll make sure and mention this to him. And as John said, I have seen at least several installations done this way (most people locally- zone 4A- only insulate if they are doing radiant floor).
.
John Klingel,
Here's an article on the topic from Joe Lstiburek:
http://www.buildingscience.com/documents/insights/bsi-003-concrete-floor-problems/
Martin: Thanks. I read that article a while ago, and see the logic about the sand getting wet. However, I did not see (maybe I missed?) any foam under the slabs in that article, and I see a slab with foam under it being very different from a slab w/ sand under it (if you have liquid water against the slab). Sure, if you have something that will soak/wick water in, like sand, you have a potential problem. I don't, however, see how foam is anything like sand in that regard. I also see a problem without the sand and foam if you let the slab get wet; won't it also wick in water? Maybe concrete won't wick as fast as sand, but it will wick up to a few kilometers vertically, so it is going to wick horizontally, unless I am missing something. I think the problem is water, not sand. It seems to me that you have a serious problem if there is liquid water around a slab, sand or not. All that is to say I can't wrap my pea brain around foam being the culprit.
John,
You're right -- foam is not the culprit. The problem is the location of the poly, which always belongs directly under the concrete. You don't want to create a little lake under your slab. When the poly is directly under the concrete, it can't hold liquid water. If the poly is 3 inches below the slab, there are all kinds of cracks and wrinkles and areas for water to collect. Remember, the poly was rolled out over an uneven, slightly-out-of-level surface consisting of raked stone.
The poly can hold gallons and gallons of water; before anyone can install the finish flooring, all of that water has to dry up -- evaporate -- through the concrete. That can take a long time.
Yes, gallons and gallons of water. Probably more than a hundred gallons over the 1750 square feet of slab. But its all done, and a modest 4 hours of work. We're keeping the concrete as our finished floor to provide thermal massing for our passive solar, but we will eventually want to seal it after some stain, so a dry slab is necessary. Thanks again, Martin, for getting me (and my architect) on the right path.
Martin: I understand, and I think there are two related issues here. (1) One is "wet, initially". What I am having trouble with is whether or not that "several gallons" makes stink to the concrete, esp if the truck driver mixes the concrete just a tad dry, but still within specs. How much water is added to a cubic yd of concrete normally? It seems to me (lacking the answer to the previous question) that the foam would have to be floating to have enough water there to raise hell with the concrete. Then too, don't people usually flood concrete several hours after it has been poured, or put poly over it to retard drying? So the concern with water under the foam initially is, as I see it from my point of view of limited knowledge, not warranted. (2) Issue two is "down the road", and I think that is what JL was getting at with his article. Certainly, if you keep letting water get into the slab, you've got problems. But, I don't see foam causing any problems, as it is not going to wick in water like sand would. So, I don't see how Jonathan has a problem, if he waits for those "several gallons" to dry out before putting down vapor impermeable flooring. I see the real question question for him as "How much longer will it take for the excess water to dry out before I install flooring?" That, I'd like a concrete expert to comment on. I think you should wait a month or two for a normal floor to dry, so is another month sufficient?
I read Joe's article and have to agree with John. foam isn't sand. Concrete takes 60 days to cure anyway and I am thinking in this install there is no difference between the placement of the poly above or below. Hell, the gist of Joe's article seems that I would poke a few holes in the poly and forget about it.
Last slab I poured, poly was under. Finished with an industrial epoxy. There is exposed rock in the corner[garage] that water runs down in the rain, enough that I installed and under slab drain. Eight years in it is dry and the epoxy is holding tight.
next slab I pour? Well, these guys feel pretty strongly about it so I would have to consider it above the foam, but I do have to say I tend to like my insulation dry if I can get it that way....
Approx 21 yds on concrete means approx 500 gallons of water in the concrete. An extra 100 gallons seems like a concern, for sure. Now, armed with info, I will have to take measures to plan for drainage (a few holes?), or bite the bullet and put the visqueen on top. I just hate the thought of the concrete apes tearing the visqueen mercilessly with wire mesh. The use of tough "poly" or doing it yourself sounds in order. BTW: I also found that one engineer here put his poly below the foam to protect it from radon, which is prevalent here in the shist areas; I never thought of that.
I have successfully put the VB (I don't use poly) under the insulation, and I think in a lot of jobs it's not going to matter one way or the other. This is in a situation where footings and stemwalls are poured first, then the slab prep and slab are installed. We do not use sand, we use coarse gravel with no fines. We make sure it is very, very flat, probably putting more work into that stage than a lot of people do. Then the VB goes down, and it's rolled up to the top of the walls all the way around, as well as taped at all overlaps and penetrations. Then the foam goes down, butted tightly everywhere. Then the rebar, tubing, and concrete. After the slab pour the VB is trimmed off around the edges. There is no appreciable air space in the whole thing, and there aren't any points of entry for water at the edges.
In the OP's scenario, with some water under the foam, it seems likely that the weight of the wet concrete is going to push the foam downward, causing the water to come up thru the cracks and join the mix, where it will bleed out along with the other hundreds of gallons of water already in the concrete. Sounds like he has nothing to lose by poking some holes and putting more plastic over the top of the foam, but it's hard to see his current situation as fatal, and like someone else mentioned, there are a lot of slabs out there done this way.
My motivation has always been to keep the foam dry, protected from any possible vapor from below. It's probably not a worthy goal.
David: "My motivation has always been to keep the foam dry, protected from any possible vapor from below. It's probably not a worthy goal." I think it may well be a worthy goal, if you have any gases that can effect the foam. That is something I'll have to read about. If one can get the slab poured before heavy rains come, I'd prefer the foam on top for the reasons I mentioned. Thorsten Chlupp puts his heavy poly down, then a foot of foam, followed by 20" of sand (if he has enough solar radiation at the site to rely heavily on passive solar, I believe), then caps it with the slab. He also uses stained concrete floors, allowing water to escape through the slab; a critical variable. Given the OP's situation, I think it was wise to pump most of the water out, as others recommended. Now that I know how much water is added to the concrete, 100's of gallons under the foam could be problematic. Too, working hard at keeping the gravel flat is well worth the effort. How else do you know how much mud to order? BTW: When you use rebar, how do you hold it up (blocks and tie wire?) and where do you put the PEX? Tied over the rebar, or stapled to the foam? I'm thinking of using rebar, 16 to 20" OC, and tying the PEX along it. Problem is, they should both be at the same elevation in the concrete. Maybe with a ton of foam under the PEX it can be stapled right to the foam without any ill effect. That takes us off-topic, so email me at jolinak at gci dot net if you'd care to. thanks. j
Use 6x6 or 8x8 wire mesh and tie the PEX to it. You can prop up the mesh with blocks of foam and pull them as you pour the mud, or just use your cumalong to pull it up into the concrete as you go. Try to avoid getting closer than 1.5" to the surface to prevent ghosting through the surface.
Aaron: I was planning on using concrete blocks w/ tie wire, being a bit of a control freak (and not trusting the cats who will be pulling things up. One "oops" and I'm screwed.) Foam would be cheap and fast if the crew is good; good idea. j