What’s the best way to address insufficient foam R-value outside the vapor barrier in Zone 5?

We’re in new construction now, and had to put the brakes on due to moisture in the wall assembly. Our wall design meets code for Zone 5 (Illinois), but we want to make sure we never have a problem with mold.
We’re using Ox Engineered Products Structural Insulated Sheathing (SIS) 1″ polyiso R-5.5 and 2 x 4 stud cavities filled with un-faced mineral wool, Roxul R-15. The Ox SIS (formerly Dow) has a perm rating of 0.3, so its use requires drying to the interior. It is meticulously taped and sealed, so it is also our air barrier. The Roxul is very vapor-open (roughly 30 perms).
After putting the insulation in, within a few hours condensation began to form on the inside of the SIS panels. With the attic closed and insulated to R-49, we pulled all insulation and warmed the interior to 70 degrees, with just the R 5.5 on the walls. We brought in dehumidifiers. After drying for a couple of weeks we installed a test section putting Roxul into the stud bays and covering with painted drywall (one coat of latex). With indoor RH of 30% at 70 degrees we tested for 36 hours during a cold snap where the low temp was 6 degrees. After pulling the test section, the SIS was wet again. Moisture in the studs at sheathing before the test was 12%. Afterward it was 15%.
With siding already on, it seems to me we have two options, and I’d appreciate expert advice.
Option 1: Flash & batt with closed-cell spray foam to “thicken” the vapor barrier, then fill with Roxul.
Option 2 Put the full 3.5″ Roxul in and immediately install an air-tight smart vapor retarder on the interior, to go under the drywall. Moisture in the studs at sheathing is now down to 9%, rim joists are at 11%.
We’re building as non-toxic as possible because of chemical sensitivities in the family. Is there a non-toxic spray foam? What about Icynene ProSeal Eco (MD-R-210)? If I did the math right (using Joe Lstiburek’s equation), 1.5″ of spray foam would protect the first condensing surface inside the wall assembly from dewpoint with -15 outside at 70 degrees and 30% RH inside. Is 1.5″ the right amount? Since we’ve already paid for the Roxul, I want to minimize additional expense.
Or, can we effectively keep vapor drive from becoming a problem during the heating season by using a smart vapor retarder? If so, which one? Intello from Pro Clima is very vapor-closed under dry conditions at 0.17 perms, but it opens to only 2 perms at 70% RH. This concerns me. Some mold experts say 70% is the threshold to support mold growth, but many say it’s 60%. On the other hand, Certainteed’s smart vapor retarder, Membrain opens up to 10 perms at 60%, and is even more open as moisture increases. But the Membrain is also more vapor-open under dry conditions, with a perm rating of around 1.0 under 60%. Is this enough protection against vapor drive into the wall assembly during heating season?
Martin, I’d value your thoughts and would love to learn from discussion among the GBA community.
GBA Detail Library
A collection of one thousand construction details organized by climate and house part
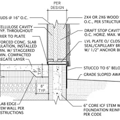
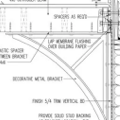
Replies
For a zone 5 location R5.5 is sufficient exterior R for dew point control even if you were using wood sheathing rather than the SIS:
http://publicecodes.cyberregs.com/icod/irc/2012/icod_irc_2012_7_sec002_par025.htm
Your problems are related to installing it when it's cold outside, and the likely air-leakage during/before installation of the wallboard.
If you added a smart vapor retarder it would be more than adequate, but for maximum resilience you could use cellulose + smart vapor retarder, since the cellulose would safely "share" the moisture burden with the structural wood without damage or loss of insulating function.
While 70% RH is indeed the mold threshold, 2 perms is significant drying capacity, almost as vapor open as a couple coats of latex paint. At some humidity level below 70% it's still drying at a pretty good clip. The 10 perms of MemBrain @ 60% RH has almost no additional effect on the drying rate, since the paint would then be the limiting factor, but it's a good product that would serve well in this application. MemBrain is sub-1 perm @ 30%RH (not 60% as indicated in your post), which is more vapor-tight than dry OSB. Keeping it 30-35% RH in the winter is still a healthy humidity for the humans.
Dave,
In my judgment, this phenomenon is occurring because of construction moisture and the fact that you don't have a good interior air barrier.
I admire the thoroughness of your testing. I understand that you have been running dehumidifiers, and that your experiment included the installation of drywall. But your wall assembly should work as soon as everything is installed and construction moisture dries out.
Remember, even if you follow the guidelines in the code (summarized in my article, Calculating the Minimum Thickness of Rigid Foam Sheathing), some moisture may still condense near the sheathing. But if you follow the guidelines, any moisture in the wall cavity will dry to the interior in April and May. If the rate of annual drying exceeds the rate of annual wetting, you should be fine.
With SIS sheathing it doesn't really matter if there is condensation on the sheathing, since XPS tolerates moisture just fine as does the rock wool. Make it air tight and the total moisture accumulation in the stud bay will be quite low.
The fact that only the colder edge of the studs will adsorb that water means that the moisture content peaks would be higher than in a wood-sheathed (or cellulose filled) assembly. But the average temperature at the stud edges is high enough that they will dry quickly in spring no matter what, as long as you don't make it too vapor tight to the interior.
Martin and Dana, thank you for your very helpful insights.
I have a few observations and questions and would value further discussion.
Early last week I put up a test section. Drywall covered 3 stud bays with insulation plus smart vapor diffusion retarder (Membrain). 3 bays were with insulation only. The vapor control layer went up immediately after the insulation went in. Over the past 8 days, we had temps of -1 on two occasions, so it was a good opportunity to observe wall system performance. Yesterday, I pulled the drywall and checked sheathing for moisture. On the “insulation only” section, water droplets had formed on the sheathing, and stud moisture increased from 11% to 13%. On the section with the smart vapor retarder, the interior sheathing was dry to the touch, and stud moisture decreased to 10.5%. I think we’re on the right track.
QUESTION 1
Martin, I’ve read on several occasions where you affirm the point we’ve picked up from Joe Lstiburek’s research that vapor barriers can be highly effective even with minor imperfections like small holes or tears. Since the carefully taped and sealed SIS panels already meet the air barrier requirement for code, is it worth the extra labor and expense for the smart vapor retarder to be installed as a secondary air barrier vs the installation method for just vapor control? I’d value suggestions for window detail and for handling electrical boxes. After finishing, what about nail holes for hanging pictures?
QUESTION 2
How dry is dry enough for the lumber? How will we know for sure when all conditions are ready to re-install insulation, vapor retarder and drywall? Would it be wise to wait for weather to warm a bit, so the low temps don’t put the interior of the sheathing below indoor dewpoint since we’re drying to the interior? I’m inclined to think the test results mentioned above suggest we can move ahead anytime, as long as the vapor management layer goes up immediately after insulation goes in. Still, I want to make sure to play the timing right. The interior of the SIS panels are a laminated wood fiber, but they are slick. We learned earlier that if too much moisture accumulates on the SIS it will run down and saturate the floor plate. When we had our initial moisture issue several weeks ago, after pulling insulation we found standing water on the plate, with plate moisture levels as high as 70%. Although, Roxul can handle moisture without injury, it does not absorb water. My highest concern is for moisture running down and collecting on the plate after walls are closed in.
QUESTION 3
Which product is best suited for our application? Dana, after reading your post I revisited the performance curve for each product. To my eye, their graphs look like this:
Pro Clima Intello… under 55% less than 0.5 perms; 60% 1 perm; 70% 1.8 perms
CertainTeed Membrain… 30% less than 1 perm; 40% 2 perms; 50% 3 perms; 60% 6 perms; 70% 8 perms
Membrain would be the more cost effective solution. Would it offer enough protection to handle moisture from drywall mud during construction? Would there be a material difference in the wintertime protection between the two products? We’ll use an ERV to keep indoor humidity from going much over 30% during heating season. Is there a way to predict the limits of low temperature protection for these products with our wall system, based on modeling?
Assumptions: R-15 + 5.5, 0.3 perms between exterior foam and sheathing, smart vapor diffusion retarder under ½” drywall, 2 coats of latex, indoor conditions 70 degrees at 30% RH.
QUESTION 4
Is it okay to put 3 ½” of Roxul directly on the rim joists, then seal with one of these products? Rim joist moisture is currently 11%. What about soffits in 50’ of cantilevered areas? Is it okay to put in 2 layers of Roxul to meet the code requirement of R-30, then go straight up over the opening with the vapor retarder, sealing the edges inside each joist bay?
QUESTION 5
Would you recommend doing a blower door test before insulating, to reveal any weaknesses in the SIS air barrier while it’s still easy to address them? Is there a simpler way?
Thanks again for your help in navigating through all the variables and for your ideas about effective solutions.