Where to put concrete perimeter insulation on a double wall assembly to avoid thermal bridging

Hi Everyone,
I am planning to build a slab on grade energy efficient home in NH, climate zone 6. I am aiming for a whole wall assembly R-Value of between R-40 to R-46. It seems that a double stud wall with dense pack cellulose is the most economical and practical way of achieving this.
In doing research on GBA and on other websites, almost every foundation design I saw for a slab involved either putting all of the insulation on the exterior perimeter of the foundation wall/slab or splitting it 50/50. There are several problems I saw with this design that I am trying to figure out a solution for.
1. It creates both a difficult flashing detail where the foam meets the sheathing (foam sticking out 2″ inches), unless you go with cantilevered LVL bottom plate, or a 2×6 exterior stud cantilevered, which is are both expensive options. Additionally you have to deal with applying some form of protection for the exterior foam.
2. If my goal is to have 4+ inches of EPS foam separating the foundation wall from the slab, wouldn’t it make more sense to have all of the foam on one side of the foundation wall? With only 2 inches of exterior foam against the foundation wall, it looks the two inches will allow cold to more easily spread into the foundation wall, which will then only have another 2″ of foam (with an ICF foundation) insulating the slab from the wall.
I was unsure what to do until I read the recent GBA article titled “A case for double-stud walls” https://www.greenbuildingadvisor.com/article/a-case-for-double-stud-walls.
In this article the author described putting the entire perimeter insulation of 4″ EPS foam on the interior side of the foundation and relied on the walls 12″ thickness to extend the interior wall beyond the foam. This would create a continuous layer of insulation from the foundation wall up into the wall cavity. Since the interior stud would be partially resting on foam, the author called for using a plywood layer under the bottom plates to provide rigidity for the interior stud. This would effectively create a cold foundation wall, but warm interior slab. I initially had a hard time figuring out how this was done, as there were no pictures of the slab/wall detail in the article and nobody in the comments seemed to mention doing this method, so I went ahead and created a detail that I thought represented what was described and attached it to this post. In my case, the wall is 13 inches, so its possible I may be able to have the plywood only under the interior stud. One detail I didn’t see mentioned was the creation of a foundation wall “Chair” where the top 4 or 6 inches of the foundation wall height are slimmed down to 6″ thick to allow for more interior perimeter EPS insulation.
In doing research on youtube, I also found a builder in Canada who seems to have done a similar approach. https://youtu.be/qO7M_nYQAII?t=475
The whole point of this post is that I am just wondering if anyone else has done a wall/foundation assembly such as this and also if anyone foresees any problems with building a foundation in such a manor. Does it seem that this assembly would actually perform better from a thermal and cost efficient standpoint? Or for example would having a cold exterior foundation wall create a thermal bridging problem up into the wall cavity (my initial thought is no).
I appreciate everyone’s help. Thanks!!
Chris Roche
GBA Detail Library
A collection of one thousand construction details organized by climate and house part
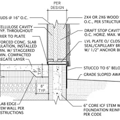
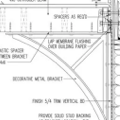
Replies
I'm curious - why have a slab at all? Also, why not a continuous 6" for the foundation wall? Concrete isn't a very green building material.
We are doing a slab because we wanted stained concrete polished floors, as for the 6" foundation wall I have not yet sent in the house drawings for engineering approval, so 8" was just a precautionary amount in case that's whats recommended due to soil conditions and wall span lengths. Its going to be a 50' long wall. The property is also full of ledge so a basement will be cost prohibitive.
Chris,
- No reason your detail won't work, as long as the outer wall is the load-bearing one. If the walls are deep en0ugh to cover the insuation I agree it's much simpler solution than exterior insulation with all the attendant problems of protecting and detailing it.
- Have you modelled the house to optimize insulation levels? At first glance the 12" under the slab seems excessive.
- I'm not sure it makes enough difference to warrant the step in the foundation to get another 2" of insulation there. I'd leave it all at 8"
- You don't need to thicken the slab edge, or pin it to the foundation. It isn't load-bearing, and pinning it means any differential movement between it and the foundation walls will cause cracks.
- If you are building and standing the walls together, the plywood at the base should extend under both bottom plates.
Malcolm,
I appreciate your feedback. I agree the 12" does seem a little excessive. I could possibly shrink that to 8 inches, however I was thinking the extra foam doesn't hurt and will make the back-fill a little easier. My aim for this house is to be .5 ACH or less, R40+ walls and R75 attic. I have done some heat loss estimates, but haven't played around much with foam thickness.
I also agree about the step, I have seen it referenced before but haven't seen any details on how its actually accomplished. I will play around with it some more. In the above mentioned article the interior stud is entirely floating on foam (with the help of a plywood bridge), which seemed a little risky to me, but I suppose if foundations are floating on high density foam, why cant a non-load bearing wall?
Your point about concrete makes sense, I suppose a concrete crack is much worse than a drywall cracks.
That is a good point about the plywood base, haven't yet decided if it will be built as a single wall or separately, I was thinking it made sense to cut it short so that it is 1 less layer at the outer stud that I will need to worry about air sealing.
> any differential movement
My guess is that the slab will sink some, taking the inner wall with it.
Because of the compression of the 12" of foam?
If the EPS foam is of the correct density, I would think that the back fill compaction (potentially settling) and concrete shifts during curing would be the bigger concern for movement of the slab
Chris,
With proper fill and compaction you shouldn't see any appreciable settling. The detail you are suggesting (minus the 12" foam and double-wall) is the standard one for all slab on grade houses and sees no problems. For the very small amount of movement that occurs in both settlement and seasonally, de-coupling the slab from the foundation wall helps allow this to happen without real consequence.
My guess is that soil shrinkage from drying would dominate. Is there data to rule out a little foam creep (gravel against foam does create higher loads than one might think) or foam shrinkage (from aging)?
That's what I don't know because I've never used thick enough sub-slab foam to have to consider it. We do know from widespread use of slab on grade with stem-walls, that subsidence isn't an issue as long as the substrate is correctly prepared.
I would think the slab and foundation would eventually move independently, and with the interior wall riding on it would cause issues. And the foam looks like a highway for bugs to get inside the house.. I'd use rock wool.
I built and lived in a double wall house (for many years) with very nearly the design
you're proposing. Mine was also in zone 6 ( at 7000 FT. Elev.) in Az. All electric house
(2400 Sq. FT.) - no heat bill ever exceeded $105 for an entire year (heat only, no lights,
water heating or cooking included in this cost). Mine only had 4" of XPS under the slab - mabey Arizona has higher soil temperatures than N.H. but I assure you that your design
is on the right track! I hope this is reassuring - good luck!
Thanks for the reassurance! I know insulation benefits are not linear per inch, so maybe that's why you have been so comfy for so cheap. Congrats on building such a nice house.
Hi, user-6935182. I’ve read your posts on your recommended wall details (2x6 - polyiso - 2x4) and am planning on building my new home in that manner. I had some additional questions about details and wondered if I could email directly? I’m also in Sisters, OR like the other member you advised. If you’re up for some questions, my email is [email protected]
Thanks!
Do concrete finished floors typically get control joints cut in them?
Tyler,
Yes. You can mitigate the cracking by using a lot of reinforcement, but control joists are more common. If you don't like open joints, you can grout them or fill with sealant.