Which comes first?

Considering using raised heel (12inch height)trusses on 9 feet high exterior walls framed with 2x6s. Can I sheath the walls with 4×10 panels (probably OSB) on the deck , leaving the upper 12 inches of each panel above the top plate, tilt it up and then lower the trusses into place and secure them? Or will I have to sheath the walls after the trusses have been placed? Presumably having temporarily braced the studded wall.
GBA Detail Library
A collection of one thousand construction details organized by climate and house part
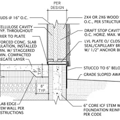
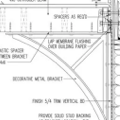
Replies
Brad,
Like a lot of questions the answer is: it depends. The usual sequence is that the bundles of trusses get dropped onto the walls by the delivery truck and then one at a time get moved into position, secured, and braced. That bundle is never entirely square, and the chances of getting it in-between the sheathed walls is pretty slim.
Two ways I can thing of doing it with the walls sheathed are:
- Pay the truss plant for the crane truck to stay and stand the trusses one at a time.
- Leave one piece of sheathing off each side of the house where the bundle can sit.
Before sheathing the walls, you'll want to get the truss supplier to give you the actual height of the heel from the top plate to the underside of the top chord. That will be different than the total heel height of 12".
Thanks.
So if I add an 8 inch wide strip of 3/4 ply to the top of the top plate to facilitate air sealing, I could still pay for the extra crane time or leave out an 8 feet section or so of the ply strip on each side to accommodate the bunched trusses.
Brad,
Yes that would work. It worth heeding Doug's caution though. It will be harder to move the trusses into position if the sheathing is there and either the wall or the trusses are out a bit.
I do see the attraction of what you are trying to do. Once it's all up, having continuous sheathing from foundation through the trusses , with all edges nailed, is great.
I agree with what Malcolm said and also the trusses may not be exactly the length you have specified. 28' might be 28' 1/4". If you would like to have the wall sheathing in place I would do so and end it somewhere on the double plate. Then set the roof trusses, one on each end of the house first and pull a string between them at the ridge. Use the string to center the remaining trusses. Now you finish up the sheathing on the energy heels making adjustments by shimming or a reduced sheathing thickness if the truss length is a bit under or over to get a smooth exterior plane.
The building inspector will likely want to see rafter ties on the inside regardless of how it is sheathed.
Malcolm’s usual is different than my usual, so Ill offer an alternative of how it goes for myself.
Trusses for houses, because of length, will come by semi on a roller deck trailer and they roll them off the semi trailer onto the ground. They can do this by sliding the wheels forward to tilt the trailer and then release the rollers allowing gravity to take over. Of 4 truss plants that are the closest to me they all do this so you don't need a crane on delivery day.
Trusses are jigged on a big table at the plant and the length is usually very accurate. All dimensions are on “truss sheets” developed by the truss designer for your approval, basically a blueprint for the truss and contains all the information the inspector will want and the framer as it notes all required bracing. Every unique truss has its own truss sheet. This would contain heel height dimensions.
Since house trusses can be large and unwieldy we usually crane a truss at a time on set day instead of craning up multiple trusses, it goes faster for us and is safer than trying to slide trusses walking a top plate.
As to your walls, its nice to sheet on the deck, so you could use 4x9 sheets, set the roof and nail on the remaining strip after the fact. If the ceiling is the air barrier there is no penalty for the sheathing joint at the top plate.
If you trust your framing and the truss plant you could install as planned but if the trusses are even a 1/4” over you will be fighting and beating stuff with a sledgehammer while an expensive hourly crane operator watches in amusement. I have done what you described but only on 1 side. I was thinking it would be a fast alignment for the trusses but its harder to walk on the wall so we abandoned that method and just nail the strip of osb covering the heel on during siding.
In addition, sheathing the raised heel rafter ends after setting the trusses will allow you to cut the sheathing to fit between the rafter tails. Leave a space between the top of the wall sheathing and the roof plywood to accommodate the air chutes. Getting a tight fit between the wall sheathing and the air chute keeps blown insulation out of the eaves.
I've no truss experience, so salt this heavily, but would it work to just leave off the nailing for the top couple feet of the sheet so there's some flex? Would still allow you to have the sheets in place when the walls get lifted, but would then get nailed off completely after trusses go in...?
I just installed my parallel chord trusses this summer, so a little easier than gable trusses I would imagine.
I left off the top course of wall sheathing completely. We craned all of them up at once, then rolled them out one at a time, blocking as we went.
In one section our sheathing stood proud of the top plate and of course that was the area where either our numbers were off or theirs, can't remember now. It made it very difficult to get the truss into place, especially on a second story.
After we sheathed everything, the engineer did not require clips because the sheathing was doing the job of the bracket.
We’ve gone completely away from traditional rafter ties or hurricane clips as some people call them and now use basically a long timberlok hex head screw driven through the top plates into the truss.
Works pretty slick.
Another benefit is they provide one more connection tying the two top plates together.
Do they require the top plate to be screwed to the studs instead of nailed if you use this method? Im used to seeing steel strapping that ties the truss, top plate, and top bit of the stud together, and another similar strap on the bottom of the stud tying it into the foundation. The idea is to resist uplift forces from sucking the roof off.
Bill
Bill,
They replace the usual truss clips where one of the four nails is in the lower top plate, the other three are in the upper top plate. So they are sort of tied together, but still rely on the sheathing to keep the plates on in winds. The truss screws are much the same. They go into the lower plate on an angle, and are threaded along their whole length, so the plates are connected. But again there is no connection between the plates and wall studs beyond the nails into their end-grain.
Neither solutions are designed for hurricane prone areas.
Thanks for that Malcolm. Sounds like the bolts replace a different type of connection than I was thinking of. I do mostly commercial work, and we commercial people usually build with steel which is always bolted or welded, so no issues with pull outs, so I’m not as familiar with all of the intricacies of wood structural connections.
Bill
Bill,
There must be some more robust connector for high wind areas. I've just never had to use them.
I’m glad I asked the question.
Thank you.