Buying Sheathing in 2021

Lumber prices are crazy at the moment. Standard ZIP is around $50 a sheet in some areas. So I wondering how builders are adjusting. Are you moving to other materials such as glass fiber sheathing, which seems to be a cheaper alternative to ZIP or exterior plywood?
GBA Detail Library
A collection of one thousand construction details organized by climate and house part
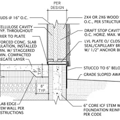
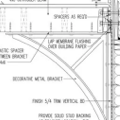
Replies
Steve,
If these prices persist it will be interesting to see if builders start using bracing for shear and eliminating sheathing altogether. I know low-end production builders already do that in some regions, but there have been some high performance houses (like Lucas Durands) featured here on GBA which did the same.
That isn't an option for residential buildings here in high-seismic coastal BC, but I'm in the middle of framing two 900 sf commercial workshops that rely on let-in bracing, and use horizontal strapping for the walls and roof. That is saving about 7K.
One trick I like is, for a double-stud wall, to use wood bracing, but don't bother letting it in--just put it in the cavity between the two walls.
But then, it still seems like omitting sheathing completely leaves opportunity for mechanical damage to whatever other layer serves as the exterior air barrier, and could allow mice to chew through a little too easily. Maybe 1/4" plywood, although I don't know the current availability and pricing on that is attractive enough.
Charlie,
Good point about the bracing. It's been a while, but I think Lucas Durand had a mid-wall air-barrier.
1/2" Asphalt fiberboard (no longer structural shear-rated due to moisture sensitivity) from Blue Ridge Fiberboard is running at 25% of the cost of 1/2" OSB if you can source it locally. Possibly a combination of bracing and this stuff? I dislike how toxic it probably is, but that process supposedly pest-proofs it, and it's probably little different from the chemical binders in roof shingles. Highly vapor-permeable, and *probably* a lot stiffer than something like Thermo-Ply when it's not doused in water, by virtue of thickness alone.
This is such an interesting question and set of comments. I think an article, "Buying Basic Building Materials in 2021," is in order. I imagine there are builders out there finding alternative products/construction methods to skirt the crazy cost hikes. If anyone reading this thread is interested in informing that article, let me know ([email protected]). I think it could be a really helpful post.
this would be great, this must be paramount on everyone's mind right now. The issue is that once you've started a build the cost to stop and resume a year later makes it almost out of the question, so it's a bit like watching an unstoppable train wreck in slow motion.
I wonder if gypsum sheathing or other commercial solutions will become more popular on the residential side.
My 1950s house in SE PA has what appears to be gypsum sheathing (with black paper). Did it used to be popular, then not?
My early 1990s home had gypsum sheathing (a surprise substitution by my builder). I'm sure he did it for cost reasons since the home was being built on fixed budget.
I ran into the same problem with steep prices. Used let-in diagonal bracing throughout and sheathed with foamboard insulation. Strapped it with 1x4, and sided with full dimension 1x8 clapboard.
Last week I had an ICF Builder tell me that the price of lumber has made ICF more competitive; but I'm sure the moment more Builders go to ICF, the price will go up too. It's worth checking it out though.
That’s interesting. Concrete and styrofoam aren’t green of course, but it would make for a pretty robust structure. That could be a plus for my exposed mountaintop site. AAC would be another option if the r-value was better. AAC plus exterior foam maybe?
I get the argument that ICFs are not too green, but if I were to live in a hurricane area, and I have the budget to do it, I won't think it twice. At least in tornado zones we can add more connectors and tiedowns.
How green is to rebuild several times the same house time after time? Add headaches, lost property, lost lives... Any price to that?
>"How green is to rebuild several times the same house time after time? Add headaches, lost property, lost lives... Any price to that?"
That's why I always say you have to look at the entire system and not any one part. Some people like to think wood foundations are greener than concrete, but concrete can easily last a century or more, I doubt very much wood can. As soon as you have to do a rebuild, you've far more than cancelled out any advantage the wood foundation may have had in the beginning. The same goes for insulation and the rest. You need the best overall mix considering the lifecycle of the structure. Focusing in on any one particular item is often counterproductive.
Bill
I have solved the crazy increase in lumber prices by not building. There is only so much I can pass onto a future homeowners and most of the price increases will have to come out of my bottom line. Too risky to build specs right now.
Kye,
Good move.
We are in the middle of real estate boom here right now. Despite the huge increases in both material and labour prices framing packages are pulling out of our local lumberyard in a constant stream, and housing starts are at an all-time high. Something has to give and I'm not sure things are going to be very pretty when it does.
Agreed!
I'm old enough now to have seen the crashes several times, it's always ugly. I choose not to be a victim of it myself...
People always say a crash is coming, and it may be, but there also seems to be this massive stratification of income groups that was accelerated by the pandemic. The wage earners in service fields got clobbered. They weren't the ones buying high performance houses before and they are even less likely to now. The people who could work from home made more money and spent less. They can afford little fixes and upgrades. The tech, finance, and upper management in the companies that have been thriving have been making money hand over fist. They don't care that a lumber package went up by 20k.
What all this means is that there is still demand and it's not likely to suddenly disappear like when people were playing games with the financing side. The 2021 boom is less reliant on financing than 2008.
It doesn't mean that the market for housing isn't completely messed up, just that it's messed up because of income inequality rather than financial manipulation.
Densglass is not too bad to work with. Nice to be able to score and snap with a knife but it does itch. Autofeed screw gun makes the job simpler but still takes longer than osb.
One thing to watch is that it does add a lot of weight to a wall, tipping up a wall without jacks is one person per 10'.
A benefit of the higher prices is that OSB and plywood are much closer in price. Much easier to justify the extra cost for plywood.
What's interesting is that only sheathing-grade plywood seems to be affected, the price of hardwood plywood is about where it's always been. Which means that oak, birch or maple is about the same price as CDX or Zip.
There is a futures market in lumber, you can read about it here: https://www.marketwatch.com/investing/future/lb00
The standard measure is 1000 board feet of 2x4. (An 8' 2x4 is about 10 board feet). Right now it's trading at $857. On February 22 it was over $1000. Futures prices are $772 for July delivery and $674 for March 2022 delivery. So the market seems to think prices will come down, but not that much. In March 2020 it was $264.
I talked to a friend of mine today's who's an engineer, he said he's heard from a few clients who are delaying projects for a few months in the hope that prices come down. But locally I'm seeing what Malcolm is seeing, the construction boom continues unabated.
maybe a minor point, but a board foot is 144 sq inches one inch thick or the equivalent. A 10' 2x6 is 10 board feet. An 8' 2x4 is roughly 5.3 board feet. ((2x4)/12)*8.
Right you are.
Interesting to hear this, DC; thanks for posting that link. I just had to delay a small addition until this time next year, and seeing that prices might maybe go down a bit is encouraging.
Just looked at futures, today's price is $964. March 2022 is $726.
With my current project, I considered the ICE panels from GSBP.ca out of Manitoba. I know that it is completely foam and metal, but the people I have spoken with are very knowledgeable about their product and support the low energy completed structure.
Just like a SIP panel, they can build wall and roof panels, but they can also do Foundation, Slab and floor replacements.
If my project was larger and not retaining a hillside, I believe we would have made the choice to use this product. It can save on the labour costs of the ICF and is quickly approaching the material costs of a complete stud wall assembly with foam sheathing. Once the walls are up, you are most of the way to completing the wall assembly.
I would be very interested in a technical review of their product or any further ICE brands and recognition of this type of system.
That's an interesting concept given the current high lumber prices. But there are few things that concern me in they way they are advertising it:
1. They talk about "effective R-values". That's usually a tip-off that they are selling them based on some fictional concept because they can't compete on real R-value. I see no details on that are their site.
2. They talk about "carbon neutral" but there's no explanation of how they make carbon-neutral steel or plastic. Steelmaking in particular has high carbon emissions.
>"2. They talk about "carbon neutral" but there's no explanation of how they make carbon-neutral steel or plastic. Steelmaking in particular has high carbon emissions."
Some 47+ percent of steel in North America is recycled, made from scrap, basically. That might be factored into their thinking.
I agree with you that somewhat sneaky marketing terms are something to be suspicious of though.
Bill
I have always thought it was kind of crazy that you needed two skins for a residential building-an outer layer of siding and sheathing. It seemed better to try to combine these into one. But I have always read here that sheathing is essential not only for structural rigidity and strength, but also to make a structure air tight and that it is very difficult to do this without plywood or OSB sheathing. Those of you who are eliminating the sheathing, how are you detailing the airtightness?
For those of you who think you can look to the futures market as an accurate predictor of where spot prices will be in the future, I suggest that if that were true many of us would be so rich now, we would not have to work for a living. There are too many factors involved, including whether the Biden Admin wants to roll back the trade spat with Canada, and the direction of interest rates, to be confident as to where prices will go.
I omitted structural sheathing (substituting with diagonal bracing) and meticulously detailed my recalimed xps sheathing for airtightness: the xps is caulked at at the point of contact to all framing members, at seams, and again at inside studbays. The seams are all taped at the exterior and interior.
T1-11 can be both the decorative and structural sheathing at the same time. This can be true even over a thin layer of rigid foam, but you're limited how thick the foam can go due to shear forces on the nails. You can detail plywood or OSB as an air barrier, and the same goes for T1-11. The big downside using T1-11 is that when it eventually comes time to reside, it's a lot more work and you have to be careful to do things in sections so that you don't compromise the structural integrity of the wall.
Using plywood or OSB as structural sheathing with a decorative siding over that makes a strong wall assembly that also has flexibility in terms of architectural design. If you put vinyl siding over a wall with no structural sheathing, you don't have a very strong wall assembly, especially for punch through types of failures (this is a big issue in hurricane zones). You'll also find that wall won't block sound as well as something with structural sheathing.
Bill
I kind of wonder if things like Thermo-Ply sheathing are going to see renewed popularity, because it's cheeeeeap. It's still being used in some areas of the country on tract homes, from what I understand (Texas?).
My house in NC is sheathed with it (with cedar lap siding), but it was done in 1989 and I've already found huge unsealed holes around exterior penetrations, so it's not functioning as an air barrier. Detailed well (taped seams, etc) it should work very well as an air barrier though.
It does need blocking in multiple areas though, as it doesn't function at all as a nail base for mounting exterior details.
I actually hate the stuff as sheathing, but it's an interesting material that has uses in the right situations. Like attic knee walls.
Has anyone priced out board sheathing in combination with a peel-and-stick air and water barrier (Henry Blueskin, for example)? Locally milled 1"x8"x12' pine boards are available in my area for $6.80 each.
But I know another pain-point for builders is the lack of competent labor. So maybe this approach would be too labor-intensive to make it worthwhile.
Cost of the peel and stick is more per sqft than plywood in my area. Even with the high cost of lumber, OSB/CDX+housewrap is still the lower cost option.
Does it need to be peel and stick? Taped housewrap can serve as the air barrier too. If I move forward with an addition this year, I will likely use local hemlock 1x6 planed on 3 sides wrapped with Tyvek, secured with strapping for a rainscreen. The hemlock comes out to $29 per "sheet" which is less that 50% of the cost of 1/2" CDX.
Taped housewrap is hard to detail as an air barrier. If you take a bit of care, use one of the stronger ones like commercial Tyvek and tie it in properly to the foundation and roof air barrier, use only cap staples, it should work.
Keep in mind that house wrap is pretty good at reducing infiltration since the house wrap is pushed against the sheathing. It does a pretty poor job though when the pressure is in the other direction. This can create some pretty large 3d air flow paths that will always find the weak points.
For the bit of extra cost and simplicity, peel and stick or taped rigid foam is simpler with board sheathing.
I'm gathering materials for my son's house, a new build. We have similar sheathing prices in our area to those described above. I just purchased enough fiber cement lap siding to do the entire house for pennies on the dollar. Included with the Hardie Plank was LP Smartside siding which is 3/8" thick in 16' lengths. The widths vary from range from 7 3/4" to 16". I plan on covering the sheathing with roofing felt then adding 3" of EPS with staggered seams. I was thinking that if I installed the Smartside on a diagonal that possibly that could replicate the traditional method of using boards to sheath a house. Any thoughts? I would have enough Smartside to cover the equivalent of 23 sheets of OSB, so it's a tempting solution. The one downside is that I don't think I would be able to do advanced framing with the studs 24 o.c.
Hi John,
If you want to frame 24 o.c., you will need to use the 7/16 LP SmartSide.
Thank you,
Arnold
Hi John,
How did you get the Hardie so cheaply?
Thanks
Deleted
I ran into Home Depot today and sheet goods aisle was fully stocked, piled up to the ceiling. This was a welcome change from earlier in the year when the lumber racks were empty. Prices haven't budged, still ~$40 for OSB and $50+ for plywood. But it may be a harbinger that the supply crunch is easing.
I did hear over the weekend that our local building supply is only selling lumber to commercial buyers with established accounts.
The concern I've been hearing from my suppliers is that they're worried about supply shortfalls sometime this summer. My electrical supply house (I deal with them the most) is concerned with copper wire availability this summer. My lumberyard thinks pressure treated lumber will be in short supply again as everyone spends stimulus money to build decks again.
My recommendation from what I've heard so far is that if you have a project you must do, it's a good idea to buy the materials now so that you're ready, provided that your project start is sometime in the near term. If you can hold off, you'll probably be able to save some money IF you can wait long enough -- and "long enough" is probably around the end of this year or possible later.
Obviously this is educated (hopefully :-) guesswork on the part of myself and my suppliers, so no guarantees. I can tell you that my electrical fabricator is telling me they are having a difficult time sourcing all kinds of parts, and that their steel suppliers won't hold prices for even 24 hours on quotes -- and these are big commerical accounts with decades of history. My primary generator supplier quote me a 15 week leadtime for a 150kw unit about two weeks ago, and as of yesterday that is now a 20 week leadtime. Many residential generators are back ordered through this fall.
Crazy times we're in, and it's likely to be a while yet before we see stuff hopefully start returning more to normal.
Bill
Just wait until (if) the new infrastructure package passes. If supply chains are overwhelmed now, I wonder how they will fare with $3 trillion of new spending moving into the economy. (Admittedly, this will be phased in over years, but markets are irrational and who knows how they will respond to this pile of money.)
I don't see how that will even be possible. Supply chains are super tight, and labor is super tight too. There just isn't enough capacity to do projects like that in such a short timeframe. That combination is likely to cause a lot of wonky economic impacts, I agree with you there!
Bill
Wanted to bump this. The WSJ ran an article on a new carbon market which is evolving in the SE US. Basically large companies are paying southern pine growers not to cut. This market will add additional price pressures as more supply is taken offline.
1/2" cdx plywood is around $65 a sheet in parts of Canada now.
My understanding is there's no shortage of timber, landowners aren't getting any more for the wood than before. The shortage is in processing capacity at the mills. When the stock market crashed a year ago, at the start of the pandemic, the mill owners cut way back on capacity, figuring that an economic downturn was at hand and construction follows the general economy. They guessed wrong. Then they had to close the mills due to COVID. Production still hasn't caught up.
So much of the modern supply chain has been optimized to the point where there isn't much resiliency. But I'm not sure manufacturers really lose out on this situation when entire industries operate in lockstep and everyone can raise prices when demand suddenly perks up and outmatches what they can ship.
Myself and several of my vendors are thinking that many suppliers have been looking to raise prices for some time, and now they can say "sorry, it's because of COVID", and their customers don't get mad at them. That means at least a little of what we're seeing is inflation. How much prices recover when things start getting back to normal remains to be seen.
Bill
I wonder if this mill bottleneck isn't more like the Enron debacle from 20 years ago. Power plants all going down for maintenance at the same time to drive up rates.
The mill consolidation of recent years makes me suspicious.
Personally, after insulation, my bonus room is going on hold. I simply will not pay 4x what products are worth. I put back a 20-amp breaker yesterday because it was 7 bucks. 6 months ago, I bought the same breaker for $2.15.
50 dollars per sheet of 23/32 OSB? 80 dollars a sheet for Advantech products? Screw that, I'll let the "I'm not going without" folks gobble it up...
You can use a $7 breaker? I wish I could. Our code is pretty much all circuits have to be on $45 CAFCI breakers. I have an empty panel waiting for payday before I can fill it.
Life experiences have taught me that most controversial issues are somewhere in between the extremes. I believe Covid has been a factor in lumber price increases, but I also believe that the lumber industry and others, have taken advantage of the situation to make a extra revenue.
All the homes around here are using steel bracing and eliminating almost all OSB except in maybe corners.
Price wise. It's actually less money to build concrete ICF walls vs wood frame. How crazy is that?
On lowes website regular 7/16 is going for $53, while 7/16 ZIP panel is going for $42? Crazy. It appears it's currently out of stock, but the other day lowes had ZR9 ZIPR panels in stock online for $58 per 4x8 sheet. That's about $.15/sqft over regular osb for a WRB and 1.5" of foam!
I think some of what you're seeing is that they might be trying to be honest with their prices and only update the prices when they restock. If a vendor constantly updates prices on their EXISTING INVENTORY, that's technically profiteering, since they already bought that material, so their cost is fixed at whatever the material was priced at when they bought it. If their pricing increases when they get a new shipment, then the new price is based on whatever they bought the new batch for.
BTW, I think Home Depot has been trying to do this (be honest) with copper wire. They are no longer advertising some things that I know they have in stock, and I think it's because people have been cleaning them out and they are trying to keep things in stock for "regular" customers and not only bulk buyers. I've seen Home Depot being consistently lower with their wire prices compared to some of the other box stores in my area, and it seems like their price updates when they get a new shipment and not before. I was surprised to see that, but that's what appears to be going on. I've seen other box stores with daily price increases...
Many vendors aren't holding prices right now, so it's entirely possible that you'll see a good price, but you won't be able to order at that price because it was an "old price". It's crazy time in the building materials world, so you have to be careful.
Bill
Should I be hoarding whatever wire I can find at this point? The doomsday scenario is that building stages get held back halfway through the build because materials can't be sourced .
I think at least some of the shortages we're currently seeing is from hoarding, but it's worth buying your materials early to keep your own project on track. Basically estimate what you actually need, and buy that now. My vendors are all telling me that they expect shortages sometime this summer, and the price trends have all been upwards. That means if you buy now, you're likely to both save some money AND protect yourself from possible future shortages.
Keep in mind though that this is all crystal ball gazing, so accuracy is not guaranteed :-)
Bill
Add joint compound to your hoarding list...
Not sheathing, but framing material related. I'm getting ready to finish a basement for a client. I have salvaged some of the old 2x4 framing for reuse. I'm also considering switching to metal studs as an alternative for the framing as it is about half the cost of wood studs right now. I'll have 2" of EPS between the framing and basement wall to help minimize thermal bridging losses.
The lumber market closed at $0.97/BF today and the price for March 2022 deliver is $0.66/BF.
https://www.marketwatch.com/investing/future/lb00
It's average around $0.50 over the past three years so that's still a little high but it looks like the crisis is ending.
I recently read that the lumber market is supposed to get MUCH better (cheaper) around the end of this year and/or into early next year. The expectation is that prices will probably never return to what they once were, but they should be far lower than they are today. Copper is supposed to go down too, although I haven't heard as much detail as to what and when might happen there -- which is very dissapointing since I'm more affected by copper prices than lumber prices in my usual commercial work!
Bill
Lumber closed at 53 cents on Friday. It hit a high of $1.67 in May. It's now within what was considered a normal range until a year ago.
A sheet of Advantech is still $105 though. And 7/16 Zip is still $75.
The distributers all bought their current stock at the high prices, so unless they want to take a bath on it they need to sell it on high. I don't think we will see much in the way of reduction at the retail level for a while yet. And then there are the fires...
The supply chain has to clear out the old, high-priced material before you're going to start seeing prices adjust. Futures contracts are just that -- prices against FUTURE contract purchases. It takes a little while before the prices on the shelf reflect that. My old economics professor used to like to say "prices are flexible upwards, but sticky downwards", which basically means vendors are often reluctant to lower prices until they really have to.
The big issue I've been seeing isn't even the high prices, it's materials availability in general. Generators (commercial units) are out well over 20 weeks now, residential ones longer than that. My telecom cable supplier is telling me a lot of fiber optic cable is on a 54 week leadtime now -- over a year! They're also having difficulty getting copper cabling in for stock.
I doubt things will start getting back to pre-pandemic levels of normalcy until at least the end of the year, and from what I've been hearing, sometime mid-2022 is probably more likely.
Bill
Yeah, I just had a roof put on and the roofer said he's waiting 30 days for materials.
A 2x4x8 is 4,79 CAD right now here in Quebec down from 10$ :-) Lower prices are coming. OSB and plywood prices are still through the roof though.
I actually just bought a few 8 foot pressure treated 4x4s and 2x4s yesterday for a "foundation" for my daughter's play structure (I have to build it into a slight hill, and I don't want the cedar pieces in the ground). I think the 4x4s were around $7 and the 2x4s a little less than that. Definetely less than a few months ago.
Fingers crossed prices drop sooner than many (including myself) have predicted :-)
Bill
What have people seen Huber zip r12 going for?
Vermont home depot sheet good prices dropped today or yesterday. 1/2" plywood sheathing is $45 instead of $75 or something earlier this week. 7/16" OSB down to $37 from $45 last week.
Advantech is still $106 per sheet. $3.30 per square foot. More than budget tile or hardwood flooring.
Advantech is $138 at my local yard still. That's $100 more than pre pandemic.
PNW - HD and Lowes ply is in the $40s all of a sudden. Been looking periodically because I have a project in the planning stages. Things will certainly be less expensive by the time my walls would be going up. Good sign.