Why are roofs insulated more than walls?

I see roofs insulated to R-100, walls to R-50 and basements insulated to R-10 or even R-0. Why not all the same?
I know that heat rises, but what’s the thinking behind this? Is it because the thermal difference between the top of a room and the outside is that much greater than 2 feet off the floor? Is there a stack effect going on?
Thanks
GBA Detail Library
A collection of one thousand construction details organized by climate and house part
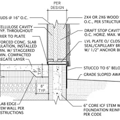
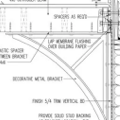
Replies
Technically heat doesn't rise, it "goes to where there isn't any," in the words of my junior-high science teacher. Or from warm to cold, in the words of most building scientists. But warm, moist air is more buoyant than cooler, drier air so it tends to rise.
I am aware of three reasons for putting more insulation in the roof than other locations:
1. The stack effect and the tendency for warm air to rise result in higher temperatures (and temperature differential with the cold outdoors) than other locations in the building.
2. It's usually easier to get more insulation into a roof because they typically have open attics, or when they have vaulted ceilings, the depth of framing allows for more insulation.
3. Night sky radiation on clear nights cools the surface of the roof below the ambient air temperature, resulting in higher temperature differential with the interior, and the associated increased heat flow/loss.
ETA: Oops, DC has a good point below--roofs get hot! The greater the temperature difference on each side of an assembly, the more heat flows through it.
Awesome insight!
This means that ceiling fans are useless for moving heat down once your house has reached its desired temp?
Not entirely, as you can still have some stratification with warmer air higher in the space, in which case "stirring" the air with a fan can help even things out temperature wise. In a well sealed structure though, and the size of spaces typically found in a home (not usually more than two stories high), the comfort gained with the fan is pretty minimal. You're usually able to achieve the same thing by locating a return air intake (assuming a ducted HVAC system) up high in such a space.
Bill
I’m thinking about not putting fans in my house because the ones in my parents house are never used and I don’t like them, plus my nose always seems to get stuffy when a fan is on
Although the height of my living room is 24 feet to the peak
I also sent you a pic of my plans in my post about insulation bill, thanks
Ceiling fans do push air down, but the warm air just rises up again around the edges of the room and you end up feeling a draft which usually makes you feel colder than if the temperature were slightly cooler but without a breeze.
I go back and forth on wether I should put ceiling fans in my house or not, the first floor is only 8 foot ceilings but the upstairs is 15 feet and the living room is 24
I don’t like them but everyone seems to think they offer these huge benefits so I can’t decide. Idk if it would hurt either if i ever sold it
I saw a study that 60% of people or some number like that don’t even use their fans
I’m currently debating a fan for our new construction (14’ ceiling room). This study suggests it’s worth it, to minimize the temperature differential. Has me strongly considering it.
Seems like you need to have the fan speed variability to push the air down, but not enough to create a breeze, that would result in a cool feeling. Note I did note the study was paid for by a fan company.
https://dash.harvard.edu/bitstream/handle/1/29312101/Residential_Fans-Destratification.pdf?sequence=1
markmac,
I'm not sure that study really makes the case for a ceiling fan in a new build. The primary purpose was to show whether they worked better in reverse or simply left running on forward, and presupposed the spaces would have a fair amount of temperature stratification that needed mixing.
It has been my experience with airtight buildings (1 ach50 or less) and with high insulation levels including foundation and sub slab insulation, stratification is minimal in open floor plans. I have placed thermometers on the floor and near the ceiling in such structures and the temperatures are nearly the same. The "envelope' homes of yesteryear relied on a very slow convective loop within the building to keep temperatures even throughout.
Malcom,
Understood the study was about the reverse direction, but the results suggest a ceiling fan would allow for destratification. The part I’m left questioning is how much the temperature differential would be in a well insulated new home. I’ve not found any technical papers or results showing temperature differential in newer or passive homes.
The real tangible benefit of ceiling fans is in the summer. I can be comfortable with at least +5F degrees with a quiet fan on low speed. That saves quite a bit on AC energy.
It's not that heat rises. Hot air rises, but with good air sealing that shouldn't matter. And more insulation doesn't mean more air-tight if it's batts or blow-in.
I think it's two reasons:
1. Roofs get hot. In the summer at least. Heat flow is going to be proportional to temperature delta, if the roof is a lot hotter than the walls you would want more insulation there.
2. Roofs are generally easier to insulate than walls. The standards in the IRC are designed with a lot of regard for practicality. When you're doing insulation it's pretty much the same cost to fill to the thickness of the framing. Framing in walls is rarely more than 6" and in roofs it's usually at least 10".
There's two aspects to look at it from, heat gain and heat loss.
In the heat gain situation, the sun is providing incident energy to the surfaces of the home. How much power is absorbed depends on the incident energy, the angle at which it is received, and the emissivity of the surface. A roof has (1) A lot of area, and (2) much of the time it's normal to the incoming light, and (3) it's almost a perfect black body (shingles) for most all roofs.
That is to say that in warm months, nearly all energy is radiative and not conductive or convective. that in turn radiates down on to the insulation, and makes its way into your home. That's why it makes sense to insulate the attic to a higher degree than the walls.
In the cooling seasons, where the incident energy on the structure is low, all heat loss is some form of convective, conductive, and then radiative. Now we're talking about mostly area, material, and air flow. In a ranch floor plan, the roof typically has about as much area as the rest of the walls, and if it were 100% air sealed, I'd say that equal amounts of insulation would be fine.
As DC Mentioned above, there's a structural and economical aspect that practically limits insulation thicknesses. Structurally, a 2x4 wall is sufficient for 99% of platform framed residential homes. Space is expensive, and having thick walls means less usable space. We insulate walls as an afterthought in most places, shoving it where it will fit after all other trades are finished with their work. The roof however is fair game. Not much going on above the ceiling, and cellulose is cheap. Let'R rip boys!
I've often thought that we shouldn't even bother with cavity insulation. It performs so badly by the time the framing, blocking, plumbing, electrical, and finishing are done, that we might as well forgo it on the interior, and put it continuously on the exterior where a lesser amount will do a superior job, and just make the rest of the process easier for everyone in the future. That's the PERSIST method, and I think it's the best for any climate really.
https://www.alberta.ca/assets/documents/tr/tr-dtseries01persist2016.pdf
I’m hoping to piggyback on the above question that asks something I have been wondering for awhile now. The R value recommendations for basement / slab insulation has interested me in that I would think more should be recommended. It seems to me that more heat would be transferred by conduction to the ground than some give credit to.
I have no data to back this up, I only know that I get a lot colder a lot faster when I lie on the ground, as compared to when I stand around in an air temperature that is comparable to the ground.
Thanks for the great discussion,
Ben
I agree with the other posters, but while ease of installation was mentioned, cost wasn't (although they're related). It tends to be a lot cheaper to "blow in some more!" when insulating the attic floor, so it's not a big deal to go from R49 to R60 -- probably just more material cost, and that's not even all that much. Going for more insulation in walls is a bigger deal, since you have more material, but also sometimes that "more material" is also a more expensive material (such as polyiso compared to fiberglass batts), and a whole lot more labor to put more R value in the walls (staggered stud walls, fancy details with thick exterior rigid foam, etc.). Adding more R value in a typical attic doesn't usually involve much more than keeping the blowing maching running for another hour on the job, and some more material to feed it.
The cost/benefit ratio for extra insulation looks a whole lot better when the cost part is small, so it's easier to justify higher R values in areas where the cost to install is low. If you're going with something like loose fill cellulose, which is essentially an "inherently green" insulating material (typically made from recycled paper, and it doesn't have to be bleached), there isn't a downside on the green end of things, either.
Basements are a different story though. The reason extra R value in basements doesn't make as much sense is because the average thermal delta across a basement wall is less compared to a roof or above grade wall. The subsoil temperature is usually close to 50F or so in many/most areas, so if you keep the interior at 70F, there is only a 20F delta. If it's 0F out, you have a 70F delta across the walls and roof, so it makes more sense to insulate those areas with the higher thermal delta, since those areas are where most of the energy loss is taking place. The lower thermal delta makes higher amounts of insulation more difficult to justify, since it won't be saving as much energy, and won't make as big of a contribution to interior comfort, either. Basements commonly use rigid foam insulation too, which also makes that insulation higher dollars per unit R value, so you now have the opposite of the "attic" area mentioned earlier: in the basement, you have a high cost and low benefit, so it doesn't make sense to go with high levels of insulation in this area. You'd gain more for your money spending extra on the walls or attic/roof than you would spending the same amount of money to increase the insulation levels on the basement walls or floor (and the floor is even worse in this regard compared to the walls).
Bill
I think you're right about basements. I'll add that for the most part basements are much better air-sealed than exterior walls so infiltration isn't as big of a concern. I'll also add that in almost all of the US soil temperatures are lower than room temperature, if you live in a place with summer cooling needs the basement actually contributes to cooling the house in the summer. So energy loss in the winter has to be balanced against reduced energy use in the summer.
A pet peeve of mine is that the IRC refers to such basement walls as "mass walls" in the section where it allows them to have lower insulation levels than other exterior walls. The reason that these walls don't need as much insulation has nothing to do with how massive they are or how much they weigh, it's because they're underground. The reason this annoys me is that there is a pervasive belief in the magical properties of "thermal mass" to do anything the heart can dream. By using that language they just reinforce that belief.
Thank you both for your replies. If I am understanding things correctly, even if the heat is being lost at a faster rate due to underground conduction, the small delta of 20 degrees below the frost line means this heat loss is not a big deal. I was planning on putting a lot of insulation under the slab, perhaps I will not do so now, though I can still see the value of insulation along the exposed part of the stem wall.
I must admit that I have not yet priced out what this is going to cost me, and your points about return on investment are well taken. At the very least I have spoken with a distributor of recycled foam, which I plan on using. Also interested in Glavel. Time will tell.
Thanks again,
Ben
You may very well still want to insulate more than just the exposed walls. Not sure of your climate zone, but you need some depth before the temperatures get annually steady.
To answer your question:
"even if the heat is being lost at a faster rate due to underground conduction, the small delta of 20 degrees below the frost line means this heat loss is not a big deal"
The rate is NOT faster, despite ground conductivity. If the rate was faster, you would be losing more heat. That's what rate means. The reason the ground feels colder to your body than air is because it is a better conductor (air a better imsulator). But the air around a building is not really 'insulating' it because it is the ambient temp. In other words, the relevant delta t occurs from the interior of the wall to the exterior, where temperatures are ambient and the insulating properties of air provide no benefit (no temperature gradient to insulate against).
With the ground, it is more complicated because one could model the relevant delta T across a much larger area-- into the earth-- which has both temperature gradients and varying conductivity/insulating values. But ultimately there is actually MORE insulating material between the interior temp and ambient outdoor temps (even conductive material like the ground is also an insulator compared to a short circuit). So while the ground is more conductive than air, there is a MUCH LONGER path the heat must travel to reach ambient air temps, so there is effectively MORE insulating material between the equivalent delta T.
Sub slab insulation is still in the works, likely using more than most. If I had provided background info you would have learned that I was considering 8” - 12” of recycled foam, which I will likely be scaling back.
Definitely putting a lot of insulation along the exposed part of the stem wall. I have heard that this small area can be responsible for a significant percentage of a buildings heat loss, so this might be an area where a little more expense pays off.
Thanks again,
Ben
Thermal mass is wildly over rated unless you are designing from scratch a passive house and can locate the mass strategically inside the house and exploit solar.
Even then it's wildly over-rated. If you're actually engineering a house -- modeling its energy usage -- as opposed to designing it -- drawing pretty picture -- you'll see that there's no benefit to adding additional heat capacity beyond what's provided by conventional construction.
I second DC’s point here. “Mass” really just means slow-changing, but slow-changing does NOT mean thermal resistance. Those are two very different things. A perfect assembly has both light mass and high thermal resistance (think vacuum chamber). Two things concrete will never be.
Ok I'll bite:
Why does the perfect assembly require 'light mass'?
You were on the right path with "slow-changing": Newton defined mass as the property matter has that causes it to resist acceleration -- change in velocity -- when force is applied. But the word "mass," when used properly, applies only to that property, the resistance to change in velocity. There is an intuitive -- and incorrect -- notion that resistance to other changes -- such as in temperature -- is the same property. This is why I resist the usage of the term "thermal mass," it makes no more sense than talking about the "thermal height" of a house or the "thermal depth" of a house. This is not a purely semantic point, because misunderstanding leads to people making poor choices in the choice of construction of their homes.
Now, mass is useful in houses -- without a fair bit of it you have to go to extraordinary lengths to keep them from being blown away by the wind. Fortunately for the most part conventional construction provides enough mass that a few fasteners is all you need to keep a house on the ground.
The property of matter that causes it to resist changes in temperature when heat is applied is called heat capacity. And just like mass, houses need heat capacity, otherwise they'd roast when the sun came out and the furnace would cycle endlessly when it was cold. Fortunately, just as with mass, conventional construction gives adequate heat capacity and almost always no steps need to be taken to add more heat capacity to a house.
While we're on the subject of semantics, I'll add that "thermal" is problematic too.
One of the concepts in introductory physics is that heat and temperature are distinct -- the filament in an incandescent bulb has a high temperature but not a lot of heat, the water in a swimming pool has a lot of heat but isn't hot. Confusingly, in science and engineering "thermal" is used to refer to both temperature and heat, almost mostly it is used to refer to temperature effects -- thermal expansion, thermal gradient, thermal stress are all temperature effects.
If you use "heat" instead of "thermal" -- and "heat capacity" instead of "thermal mass" -- it makes it clear that you're talking about a property of heat and not of temperature.
The primary reason for differential insulation thickness between wall and roof/ceiling insulation is cost difference. For a home in central Illinois with a heat pump with 10 HSPF and 20 SEER (optimal insulation depends on several factors such as heat pump efficiency, utility rates, climate, etc), assuming wall and ceiling insulation costs are the same (eg, $5/cubic ft for R3.5 per inch cellulose), optimal insulation thickness (defining "optimal" as the lowest lifetime cost) would be 15" for wall and ceiling. If ceiling insulation costs $1/cubic ft (what we paid for to have 18in thick cellulose blown in the attic of Build Equinox 4500sqft building), and wall insulation stays at $5/cuft, optimal ceiling insulation thickness is 34" while optimal wall insulation stays at 15" thickness. Homes using same cost insulation for walls and roof (eg, spray foam), would find that optimal thickness is the same if the cost per insulation is the same. Other building elements (eg, windows) may also impact optimal wall and ceiling insulation thickness, but not too much if reasonable design parameters are being used (eg, keeping window to floor area ratio about 10%). Our Feb 2020 article discusses optimal wall and roof insulation and links to an ASHRAE article describing in more detail (https://buildequinox.com/news/?article=featured-article-walls-and-roof-ashrae-solar-zeb-article-3).
TyNewall,
Am I getting this right: You are suggesting a house in Illinois would be optimized by using R-52 in the walls, and R-120 in the attic?
Yeah, those numbers are in the "way high" range. You need to look at the cost of energy saved vs the cost of the insulation, and you have to do a present (or future, depending on perspective) calculation too. The optimum spot for R value is also based on a starting point, which is usually taken as code minimum. So now what you calculate is the savings in energy over the life of the home (30-50 years or so), and then figure out how much energy you could buy TODAY (the "present worth" of the energy involves allowing for interest rates over time, basically) to save AT LEAST enough money on energy to pay for that insulation you bought.
BTW, when I do these kinds of cost/benefit calculations at work, it's common to use the savings over the financing period. For a residential example, that means you'd look at energy savings over the life of the MORTGAGE, not the life of the STRUCTURE. For a 30 year mortgage, you'd look at the savings over 30 years, for example. This has been discussed on GBA before. My own personal opionion though is that energy costs are likely to rise in the future, so you're likely to save more money than predicted by going with a little extra insulation now.
I think we've discussed this kind of thing in these forums before, and usually the "sweet spot" for an attic is R49-60, and for walls is probably around R25-30 or so. You can certainly go over those amounts, but the payoff gets to be a long time. As soon as the payoff period is longer than the expected life of the structure, you are "wasting money" in financial terms.
Bill
https://www.greenbuildingadvisor.com/question/r-values-of-ceiling-and-walls
Check out this oldie.
Also happens to mention the % efficiency of R value brought up in the other recent thread here on diminishing returns. What a coincidence.
Boxfactory,
Much of the discussion so far regarding roof/attic insulation covers it pretty thoroughly. Your largest delta T profile is generated on the roof due to exposure time and typical materials choices. The "whole ceiling" insulation value will be higher than most "whole wall" insulation values for good reason. The ceiling in a typical home is not punctuated with windows or doors, both noted for degrading the effectiveness of added insulation in walls. Window and door losses can easily be a third of total wall losses or higher. Individual walls with a large glass percentage can make additional insulation on the remainder of wall quite pointless. Higher ceiling insulation levels is an easy win for heat savings in the winter and a good way to deal with the high delta Ts in attics for the summers.
As you and others have noted the insulation code for basements is not well considered. Very little of the code addresses the condensation effects at the foundation/framing intersect that have been, and remain, a frequent topic in the Q&A section. My following comments of course reflects the bias of cold climate thinking because I live in CZ6A. So here is some extra piggy backing on the original question.
IMHO, encapsulating a foundation on the outside with insulation will result in better envelope performance for CZ 6-7 and when termites are not a major issue, CZ 5. By most code requirements, the soil surface must be 6-8" below top of foundation. A house with a brick ledge effectively has a foot or so of foundation directly subject to winter temperatures. Concrete has an R value of .1 to .2, so heat flow through an 8" foundation is roughly equivalent to single pane glass. Try calculating heat loss for just the directly exposed area of your foundation and marvel at the heat loss. That very cold concrete will also pose further problems .
Consider that the thermal conductivity of (some) concrete mixes is similar to single pane glass and think about how much heat flow there will be vertically in the foundation wall. The top foot being at 0F will be quite the heat wick. While ground temperature increases with depth, the local frost depth should be used when considering actual delta T values across the wall. Ice has four times the thermal conductivity of water, so wet frozen soil will accentuate heat loss. Another reason to keep soils adjacent to the foundation freely drainable. The soil temperature just below frost line will not suddenly be 50F. The variable delta T from top of wall to bottom will be complex in most instances . The seasonal balance point for a given locality is sometimes described as the median between summer and winter peaks. Unfortunately, I have seen references that suggest the stable point occurs at about 12' of depth, depending on soil types. Most basement floor slabs are never that far down, so calculate accordingly.
On GBA there is a great deal of discussion about how to insulate rim boards and joist pockets. The nature of construction makes thermally matching the main walls above very tricky. This is especially true with double wall construction. As an extra aggravation, for non-exterior insulated foundations, the sill plate - firmly attached to the foundation top - becomes thermally equivalent to an exterior surface area. In heating dominate climates, preventing condensation becomes a primary concern for these at risk elements. Chronically wetted sills and rim boards are to be avoided. How to insulate this part of the envelope is the problem.
The parallel problem of preventing condensation on the exterior wall sheathing's interior surface is handled through application of assorted air and moisture barriers. The products and methods used do not readily transfer to the complicated framing situation under the floor deck. Discussion of thermal bridging and potential air leak risks dominate most of the suggestions and counter suggestions on GBA for both areas. Specifically, condensation risk is the foremost concern. Spray foam as a "go to" answer for joist pockets, ignores the fact that the sill plate does not have sufficient seasonal drying surface area like sheathing. A sill becomes effectively encapsulated by foam on top, sill sealer on the bottom, with one edge somewhat close to the exterior and the other edge presenting to the interior during winter at a very cold temperature thanks to the uninsulated foundation top it sits upon. This can make for a very poor prognosis for long term future health.
Placing full height R-15 insulation on the exterior of the foundation has some useful side effects for the building envelope. Your wall R value is still R-17 when the insulation is on the exterior, however, this allows the concrete to settle during winter at a temperature above ambient air or soil temps. The foundation, though still only R2, is now on the warm side of the gradient to outside. Depending on how warm you keep your basement or whether it is occupied will guide wall finishing decisions. At least your battle won't be against a wall that is potentially well below 40F over a large area and maybe 10F at the top during the winter. Insulation on the exterior will also reduce the chilling of your sill plate though not enough to completely escape condensation risk, as the short path to outside still exists. The real boost to overall envelope performance happens when you combine an exterior insulated foundation with exterior insulation for above ground wall areas. I did this with my own build.
For my CZ6A and a design temp of -16F, I went with exterior insulation of 4.5" of EPS topped with the 2" low density foam used under my modified EIFS coating. The nature of my EPS application does not result in myriad long screws. The rim boards are protected by close to R-24. My joist pockets are uninsulated and open to my ambient basement air. Condensation is not easily possible as the sill plate and pockets average about 58F. The walls above are 2x6 with batts, vapor open to the inside. The wall sheathing was deliberatley dropped past the sill plate line 2" to provide a better seal. A pair of generous sealant beads, one on the sill/foundation intersect and one an inch below sealed the foundation and sheathing tight. I did not place batts in the joist pockets mostly because I got lazy. I accept that I have greater loss than the wall above and the observed warmth is driven by my first floor to basement heat "loss". But I will never need to worry about my rim boards or sill plates.
The foundation wall temperatures this winter, range from 56F next to the floor slab to 58F a foot below the sill plate. These are oddly consistent regardless of my varying exterior exposure. The lot slopes so I have exposures from 6" to 48" above soil line. My floor slab sits on R-15 recycled XPS over washed rock, which has (unused) radon piping pre-installed. It holds pretty consistently at 62F year round. I have pre-embedded pex tubing for floor heat, but so far don't feel it is necessary for my work shop.
If you are planning to heat your slab, then going a bit further to R-20 would decrease the downward rate of loss when heating. You create a higher delta T by heating the slab so don't use ambient room temperature to calculate the loss downward. The heat input will inherently "leak" to the uninsulated side of the slab (floor) faster than the insulated side (ground), which is exactly what you want to happen. Be sure to include edge insulation at the perimeter. Ground losses are 24/7-365, so be mindful of that when determining heating and cooling loads.
Onslow- lots of good thoughts here - what is your tackle on insulating the entire slab , and not just perimeter ? Using your Same logic , I’ve been thinking a walk out basement arguably could use perimeter 10 feet insulated, TAPERING back to nothing on the front of the house where you have eight feet min of soil insulation. Ie 24 inches at walk out section is inadequate, yet overkill where basement is fully underground I am dealing with man of same issues you discuss; im in climate zone 4 so ignoring termites takes on a bit More risk (tho I might add Formosa termite distribution is larger- and growing with climate change- than most people realize )
You're going to really complicate your construction process doing that. I would just stick with the same thickness insulation under the entire slab. I would probably just go with 2" here.
Bill
Bill with a foundation perimeter of 200 feet and a slab of ~2300, 2” solid foam along entire perimeter cost plus ; 2” OC formular rigid foam at $1.50 /sq foot, doing perimeter 2 feet is $500 materials; doing entire slab. Is $3450.what I am considering gets me an effective reasonably even r10 below entire foundation for $600 in materials . To be sure there is value in doing entire perimeter with some rigid to isolate the slab from the Foot/walls and not confuse concrete guys, in which c ase figure $700. I could also do 4 feet at walk out side tapering to 2 feet at front of house (fully underground ) for $1400. Does center of slab. Insulation make real sense ?it’s editing on very stable 50 degree soil and isolated from outside tempo swings by ~;25 feet of soil. I’m not sure condensation concerns even justify full slab insulation in zone 4.
Insulation R values don't average out that way, you have have to add inverses. As an example, insulating half a slab to R10 and the other half to R20 doesn't give you the equivalent of R15 everywhere, it gives you the equivalent of about R13 over the entire slab. You could do it the way you propose, just keep in mind you'll end up with an "average" that is lower than you might expect.
You will get more benefit from insulating the foundation walls compared with insulating the slab. Just remember that it's very difficult to change the insulation under the slab if you decide later that you wish you put more in. A good way to save some money here would be to look for some reclaimed XPS instead of buying new (reclaimed is also a greener way to go). Slightly damaged panels aren’t a big deal in an application like this, so this is a great place to use reclaimed materials to save money.
Bill
Onslow,
These are all great points. If I were planning on using exterior insulation I would do everything you just described.
We are likely to copy figure 3 from the link below - and use thicker vertical insulation as I think this is an area where it’s worth investing a little more, due to the conductive nature of the concrete stem wall. Using double stud walls should (hopefully) make installation of the thicker insulation straightforward. Thanks to the discussion on this thread, I will no longer be going overboard with sub slab insulation.
https://www.buildingscience.com/documents/building-science-insights-newsletters/bsi-118-concrete-solutions
I appreciate your concern for moisture build up on the sill plate. I hope to tape from the sill plate, to the vapor barrier, to the stem wall. Considering also taping from the sheathing to the stem wall as well. For those who haven’t seen it I will link to David Pos’s video where he takes apart his very well air sealed double stud wall to look at the framing. His test does not seem as sophisticated as the moisture measurement you describe on your build, but I think it will work for me.
https://m.youtube.com/watch?v=uqiee2yi_6I
Thanks!
Hope all is well,
Ben
Deleted
onslow,
How did you manage to install 4.5" of EPS insualtion on the exterior of your shething without using a myraid of long screws? Please share your method. Thanks!
"I went with exterior insulation of 4.5" of EPS topped with the 2" low density foam used under my modified EIFS coating. The nature of my EPS application does not result in myriad long screws."
P.S. I'm in CZ5 and subterranean termites are a major issue here. They may not cause their destruction as quickly as the formosan termites of the south, but when hidden, they can do some real damage over time. I was thinking that exterior rockwool might be a bette choice due to the termites. We also have carpenter ants, carpenter bees and powder post beetles.
" Individual walls with a large glass percentage can make additional insulation on the remainder of wall quite pointless."
Perhaps I am misinterpreting your point here, but it seems to me that is not how it works. The glass will be the primary heat loss, yes, but whether you added additional insulation to those walls or to the ceiling doesn't really matter (other than for the reasons outlined here in this thread) but not due to the presence of the windows.
Perhaps you mean because the area of the wall is less than the area of the ceiling?
maine-tyler,
Each major surface of the envelope needs independent analysis. I was attempting to make a point about whole wall values. Once you exceed a certain ratio of window to wall area, the window value will dominate the final whole wall value excessively. I suppose it could be possible to design a home that made ceiling/roof insulation levels moot. I think I know of one example in my area. The Farnsworth House in Illinois would certainly be an excellent example, if it has any insulation at all. Ceiling area is the least interrupted surface and often of greater area than the walls. Adding insulation there is pretty straightforward when calculating for heat loss. Walls and windows need balance and basements can be better than most are ever done
For one plan, I had an east facing living room wall that was close to 50% window. The general scheduled insulation treatment for exterior walls using R-7 windows in all locations gave me a whole wall value of R-32 for the whole house. Whole roof value of R-49. However, individual whole wall values varied on a per wall analysis with the east living room wall being hands down the poorest performer. The price one pays to make a view wall.
Attempting to balance that one wall closer to the R-32 mean value would require adding an insane amount of insulation to the wall portion or increasing the window R sharply. Both options didn't make sense. The wall insulation would need to be quadruple in depth or the windows would need to be super custom to get R-12 to make a meaningful change. The total design load for the three walls and roof over a 550 sf living dining area at -16F was still only 5460 btu/hr. Most of the year the sun load would be the main problem, not heat loss. The overall house was calculated to have a total design load of roughly 32,000 btu/hr at -16F. Total conditioned space was 5800 sf (including a large basement). Making extraordinary changes for that one east wall didn't pencil out. The view won.
A similar question was raised in another post about a cabin with two large sliding units in one wall. No amount of additional insulation on the meager wall area left on that one side could compensate in a meaningful way for the the modest R value of the sliding units. Adding insulation to the remaining walls would help the overall numbers, but that one wall would still be the main loss point in the design. Maybe lots of ceiling/roof insulation could help the total designed load, but that was not the question posed.
"Each major surface of the envelope needs independent analysis. I was attempting to make a point about whole wall values."
Why? Such an independent analysis is arbitrary. Heat doesn't care if it's exiting through a wall or ceiling. I either still don't understand your point, or you have a mistaken belief about how heat flow works.
I think maybe your point is about available area to insulate, but it should be stated in those terms if so.
maine_tyler,
I think onslow is referring to the discussion DC and I had in this thread: https://www.greenbuildingadvisor.com/question/sliding-doors-increase-wall-r-value-anyway
Thanks Malcolm, I did see that thread. And I agree with what appears to be its conclusion. To me, Onslows words are in conflict with its conclusion.
Perhaps this is just a language thing, but Onslow's phrasing is inaccurate to my ears. S/he may perfectly understand the topic, but the wording is not sound (or the understanding, I don't know which).
From a practical standpoint, I agree there are lots of reasons one would pile on the R in a ceiling vs a wall, but the presence of windows in a wall doesn't 'undermine' the rest of the wall anymore than those same windows 'undermine' the ceiling. The only caveat I can think of would be 3d heat flows around windows undermining the wall to some buffer extent around the windows.
Perhaps I'm being a bit unfair and onslow is making a mere practical point and I'm stuck on the theory.
I always think it's worth defining the theory behind the practical.
Or, the point is that it is simply a matter of available area, but when I brought that up, it didn't seem to jive..
You don't generally try to cancel out heat loss through a window by beefing up the insulation in a wall. Heat doesn't have "pressure" the way water does, so it's not as if having one leaky spot reduces the load on the other areas of the wall. If you insulate the wall to some given R value, that section of wall will perform the same, and lose the same amount of energy, regardless of the R value of the window. In terms of the overall system, the window will typically lose a lot more energy than the wall does, but that doesn't mean the wall's insulation performs any differently BECAUSE OF the window.
Bill
Wow, guess I must be giving a master class on how not to write clearly. I am quite aware of heat flow properties and how insulation works. I am a bit mystified at how anything I wrote can be understood to infer that I believe wall insulation behaves differently in the presence of windows. Or that heat has pressure. If my presentation was clumsy to some, so be it. Ceilings generally make for simple adds to insulation, walls can get more complicated, and basements get ignored in general.
The original two questions in play at the moment are "why do you insulate attics more?" and "will adding insulation to a wall help balance window losses?" I guess it would be more to the point to answer, "because it is easy and can save more energy " and second, "depends". Boxfactory raised another question about basement losses, so I jumped in. The three questions allow for exploration of some of the reasoning behind certain choices to be made when designing a full envelope. Certainly not an exhaustive discussion by any means.
Clearly, people new to the process of trying to build better homes do think things like "can I reduce window losses by adding insulation to the wall". If speaking about one particular wall area, like the cabin example, the answer is usually no, that's not how it works. The energy cost in dollars per wall area is one way to show why that is not a good plan. BTU losses per wall area of different materials in equally valid. Then there are misunderstandings about how to calculate for two different but adjacent R values, why stud wall don't give a final R value equal to the batts or why different levels in a house even exist.
I tend to work on the premise that while calculating total envelope heat load guides the heating system requirements, individual room load analysis guides the distribution requirements. This can be critical to comfort levels. Not doing wall/window/ceiling analysis on a room by room basis is much akin to the HVAC contractors that just install X tons per 500 sf or whatever rule of thumb they were taught. Not a good approach if the many posters on GBA are any guide. How many times have posters questioned HVAC plans calling for individual cassette heads in every bedroom.
To answer deucevantage's question about slab condensation is difficult because CZ4 is a lot more variable than some might think. For example, in Kentucky (CZ4) the 99% design temp ranges from 7F to 18F. I have only visited Kentucky once a long time ago, so my perception of it being humid in the summer may not be true over the entire state. Just the same, for ambient air of 70F and 45% humidity the dew point is under 48F. An uninsulated slab is unlikely to fall that low, but more to the point would be the foundation portion above ground during winter. The top part of the foundation could fall to 20-25F for many days. An interior humidity of 25% is a bit low, but not unheard of during winter. The dew point for 70F ambient air at 25% humidity is 32.6F.
The heat losses to ground for a 2300 sf slab do add up even if one accepts a ground temp of 50F. For 2" or R10 (nominal) under the slab, the loss per hour is 2300 sf x U 0.1 x delta T 20 or 4600 btu/hr. Seems small at first. The 1 day loss is 110,400 - 1 week loss is 772,800 - 1 month 3,091,200 - 1 year 37,094,400. Roughly 371 therms of natural gas at 100% energy value. Not a realistic way to look at your slab loss as you won't mind a cool basement in the summer. However, we haven't discussed wall losses during winter..or comfort.
For the discussion, granting a generous R2 to an uninsulated slab means all values are five times higher. Natural gas fluctuates between 1-2 dollars per therm in most markets, some much higher and this is excluding other charges associated with gas bills. If you are building for the long haul it may be worth reviewing your local conditions and insulation plans.
Onslow,
The reason for the scrutiny is that:
1) I don't know you or what you know, so all I have to go off are your (many) words, as is the case for most here.
2) Many people erroneously believe that resistance to heat flow through one building component is affected by another, such as windows undermining the effectiveness of nearby wall (which to some small degree it may due to 3d flows, but generally speaking and in a 2d sense, it doesn't).
3) Your words read as though you beleived the fallacy of point 2. If you don't see how, I'm not sure what to tell you other than to look at what you wrote from the perspective of someone who doesn't know whether you understand this point. Knowing now that you do, I think I generally get what you're saying (again, it has to do with available area, a point of clarity I'm not sure why you weren't willing to give a nod to-- more reason for me to be doubtful of agreement), but before knowing, it easily read the other way.
maine-tyler,
After re-reading post #20, I can see the semantic problem, for that is all it really is. GBA 's Q&A section frequently sees posters wanting to use spray foam in stud walls because they have been told the R per inch is so much better than batts, cellulose or whatever. Equally often, the replies point out the folly (economic, environmental, safety) of foam in stud walls because the studs "degrade" the value of the foam or assembly - (a word choice left to responder). Obviously the foam's properties are unaffected just as the studs properties are unaffected. What is affected, degraded, altered, etc., is the whole wall performance, the aggregate of all thermal pathways.
It is a common misunderstanding that putting "extra" insulation in the bays means the same increase of wall performance. Even energy.gov blithely states a 2x6 wall can hold R-19 or R-21, which somewhat tacitly supports the notion. I am sure you know that the effective whole R value is less to much less, depending on the framing factor. Some posters will request reviews of proposed wall sections showing good practice and then announce they don't want to spend the extra dollars on better windows. The low R windows ostensibly "degrade" the rest of the wall area in a way not readily perceived until one completes a "whole wall" analysis. Mr. Wichers pointed out a similar problem with thinking that R10 and R20 insulation areas averaged together as R-15 when it actually is R-13 overall.
If I were presenting a paper to physicists I would take care with my word choices knowing that the audience would demand precision definitions and quantification of results. GBA is a bit less demanding in order to remain accessible. Just the same I will endeavor to be a bit more precise.
Here's the thing: the only time "whole wall" performance matters is when you can't meet code requirements using a prescriptive method and you're trying to meet them using a performance-based calculation. Because otherwise, every section of wall acts independently of every other section of wall. Presuming that you're economically rational, you will add insulation to a section of wall until the expected value of the energy savings of that section of wall meets the cost of adding additional insulation. That calculation is made independently for each section of wall, the wall doesn't care what's beside it. The U-factor of a window has no bearing on what the optimal thickness of fiberglass is in the wall next to it.
Thanks Onslow,
My issue is actually less with the notion of thermal bridges (windows in our discussion) being a disproportionate source of heat loss, and more with your apparent differentiation between the wall the windows are in and the ceiling.
The usual prescription for fixing large thermal holes is to cover those holes-- not to say other insulation surrounding the holes is pointless. So in the case of your spray foam example, no one says don't bother insulate the bays due to the studs, they say cover the studs. Windows are different in that we can't cover them, so other than buying good windows or reducing window area, our goal may be to 'beef up' other areas of insulation even if the gains are disproportionately small. Your assertion appeared to be that beefing up the wall was pointless DUE TO the windows, so instead why don't we beef up the ceiling. I'm saying that statement needs qualification. Thermodynamically it doesn't matter if it's the ceiling or the wall. But for practical reasons the ceiling probably makes sense. Those reasons are the ones discussed here, and because there is likely more ceiling area than remaining wall area.
What I find helpful in discussions like these is to clarify what specific points there is agreement on, and what points there is still disagreement or confusion on. You seem unwilling to offer any agreement on small points of clarity, instead choosing to fill the page with unrelated and meandering side tracks. In my experience, it is difficult to get on the same page when there isn't a more direct and succinct acknowledgment of the specific points at hand.
But no one is required to engage in conversation in any specific way, so sometimes this is just the way of it.
The main point on my answer is the method that drives insulation thickness in one direction or another (whether through analysis or experience) is economics. Insulation thickness is a balance between lifetime energy cost and energy cost. The lifetime used is for sure important. As a society if we want the lowest cost, we would view over the expected (hoped) lifetime. If someone is building as a business opportunity, and they know from experience that they will not be paid more for a building with extra insulation and they don’t suffer the cost of utility bills, this economic balance drives them to very thin (none if codes still allowed it) insulation, resulting in the many poorly insulated and ventilated multi-family buildings over 10 decades that are making us pay the price today to renovate. Economic factors (see ZEROs analyses…see BuildEquinox.com/zeros….free-to-use, online, US DOE Besttest and field validated software) are in there, for replacement costs for windows, water heaters, heat pumps, solar collectors with their varying lifetimes. Time value of money can be included but when you play with fuel escalation, inflation and discount factors, you can tell any story you want. If you’re for renewables, escalate fuel at a slightly higher rate than inflation and interest. If you’re a fossil fuel advocate, escalate fuel at a lower rate, resulting the opposite result. As someone doing these analyses since the ‘70’s, no one knows these values 6 months let alone years in time. What we do know is that roughly the same amount of our hard earned pay gets divvied up in roughly equal fractions over the years (with declining discretionary funds per family), meaning things have all been escalating similarly (Piketty is a good historical reference), so I think a less distorted view without using these factors is a good place to start. (but for sure check them to see “sensitivity” to any of the variables)
TyNewell
I have been following the company you work for since I toured a Vermod house several years ago ( https://vermodhomes.com/ ). Since then I have been looking to copy their assembly with our upcoming build, i.e. double stud walls with dense pack cellulose, and a CERV.
As I am sure you are aware, a number of the Vermod homes have the geoloop. I think is fantastic in that there is an option for the people who are considering a mobile home, that is very energy efficient, and likely comfortable.
As your above post concerns return on investment for what we put into our homes, it occurs to ask if you have any rough info about the geoloop and how it performs in single family high performance homes? Basically I am at the point where I am planning the build with my general contractor, and I am trying to balance how many new things I am asking him to do.
Thanks!
Ben
Ben, geoloops work really well to temper air, and in the case of how a CERV2 operates, turns it into a hybrid air-source/geo-source heat pump as the controls automatically determine whether running the geoloop is beneficial (eg, in swing season, air may be warmer or cooler than ground temperature, and more beneficial than ground depending on heating or cooling). For new construction, dropping 1" plastic in the outside of a footer trench eliminates the need for additional trenching. The amount of heat per footer trench pulled out in the winter is at a rate that does not pull the footer to freezing. This article describes the loop at our lab in Illinois with a year of test data, https://buildequinox.com/news/?id=3736
As far as geoloop payback, this is difficult because house occupants are the dominant load in high performance homes such as Vermod (and these days, every new home in Vermont which is doing an incredible job building high performance homes). Our two year study (https://buildequinox.com/files/CERV/VermodCERVReport06262016.pdf) with Efficiency Vermont of 13 "identical" Vermod homes (we collected hourly CO2/VOC/temperature/humidity data and all electric circuit data) shows how non-identical humans impact house energy. Someone who is 24/7 gluing model airplanes together or conducting another fumy activity requires a lot more fresh air ventilation than a home with 3 or 4 occupants who are out of the house for 12 hours a day and careful about their pollutant generation....this is a significant impact on house energy.
This article (https://buildequinox.com/news/?id=4613) on geoboosting performance will let you estimate it's performance on energy performance relative to operation in recirculation (filtration) and fresh air ventilation modes. For "average" people (average people do not exist, just like average weather never occurs), CERV2 is in fresh air mode ~20% of the time and in recirculation mode for ~80% of the time. With good winter (summer) temperatures, roughly 500W benefit occurs....maybe for 3-4 winter months and similar for locations with hot summers. This should let you estimate its energy benefit relative to the cost to install. In this case, assuming a component lifetime 20years would be reasonable. These are "thermal" watts, so they should be discounted by heat pump COP for electric watts (divide by ~3). It doesn't sound like much, by over 20 years adds up and during extreme weather is very significant.
One last note on geoloops is to watch for a future newsletter on our site that expands how geoloops are significant thermal batteries that provide significant backup heating/cooling capacity during extreme weather (think of the Texas grid failing when everyone switched on a heater during "extreme" Texas winter weather). Long, boring experiments that take a year are required....we're in the middle of that data collection for this winter.
Somehow I missed your reply. Thank you for all the information, you have given me a lot to think about.
Ben