Why keep attic air away from the roof deck?

Throughout the several discussions comparing/contrasting vented and unvented roofs and attics, the importance of keeping attic air from making contact with the roof deck underside is stressed. What I’ve not seen addressed is the situation where the ceiling (be it sloped or horizontal) is truly airtight. As in NO penetrations of any kind whatsoever, uninterrupted drywall, lotsa mud and tape, and all joints firmly backed up with deadwood and acoustic sealant. In short, whatever it takes to make it hermetically sealed. So: Where’s the assumed moist air coming from, ready to deposit its dreaded load on the cold roof underside? The IRC seems to ignore this possibility (of an airtight ceiling). Dr. Joe didn’t address it in his great FHB article either, which surprised me, what with him being THE principle exponent of ADA and all.
My intended roof system is to be primarily vented but what about roof sections above valleys? Is this another IRC no-man’s land? Also any particular issues with my using steel panels on 2X4 purlins (c/c 24″) on 12″ deep I-joist rafters? Judging from Joe L.’s piece, there won’t be enough channel over the purlins—through the panel profile “humps”— or under them and over the top of the batt insulation to afford plenty of ventilation. But if there’s no moisture to ventilate, so what? This arrangement will probably de-pressurize the mini-attic over the narrow area of horizontal ceiling just below the ridge, but again, so what?
Correct me if I’m wrong, but doesn’t it make more sense to expend extra time, effort and $$$ on getting the ceilings truly air tight rather than sealing off the deck with closed cell foams, etc. or building or buying under-deck channels all of which presume moisture laden air from the conditioned space?
Eagerly awaiting any and all feedback,
Charlie Berg
GBA Detail Library
A collection of one thousand construction details organized by climate and house part
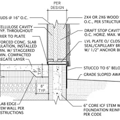
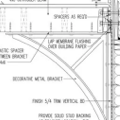
Replies
Charlie: I am not a pro, but I think your "hermetically sealed" is a dream, which is why it is not addressed in the literature/codes. Besides being impossible, IMO, to air seal perfectly, you'd still have vapor diffusion. How are you planning on stopping that?
Charles, it sounds like you're proposing to build a ventilated attic with a highly airtight ceiling and insulation over that. Good idea.
I'm not sure what you are saying about ventilating the space below a valley, unless you mean there's not much open area below that inside the attic. As long as you've got air flowing generally through the attic it should be fine (and the placement and number of vents has been discussed recently, as you've probably followed).
As for the 2x4 purlins, what about shear bracing for the rafters? You need a strategy for that. If you can brace with diagonal steel straps then the purlins may be part of the ventilated attic space, and air can flow all around.
First thing I would ask is where you are at and what's the weather? In eastern Washington state, it's about 35% humidity and moisture tends to be less of a problem.
As far as sealing the attic, we are using raised heel trusses and installing the baffles correctly for starters. I have learned not to put much faith in a signature on a building permit when it comes to insulation, baffles and air sealing so I am telling my builders that they had better know what a good job looks like if they want to have a chance of getting one.
What I like about raise heel trusses besides the extra insulation at the exterior wall is the added space to seal the attic from the top after the sheetrock is up. The last house we just finished had all electrical boxes caulked with 181 fibered mastic which is sold for ducts but also comes in tubes. The entire house costs about $25 over the cost o cheep painter's caulk and should last forever. This particular house is ICF and had 850 CFM for 3,700 sq ft before we sealed the attic. We decided to try the Knauf Ecoseal and had the blower door running as the insulators sealed the seams along the top plates and sheetrock from inside the attic and also over the electrical boxes, etc. We dropped the CFM@ 50 down to around 529 by the time we were done. While the blower door was running we also noted about a 15/26 Pa drop over the pressure pan we were using when placed over the electrical boxes in the ceiling and by recording the drop in leakage at the blower door we were able to determine that it translated into about the same amount of drop in CFM@50 for this home. Also, all boots and boxes were caulked to the ceiling after paint.
From my experience inspecting over 120 attics in our part of the state, I don't expect any moisture related problems.
The home we are currently working on we are doing different. It is 1,560 sq ft with cantilever trusses and sips exterior walls. I started to caulk the heck out of everything but got bored and called my insulator instead. When I found out he would flash coat the entire attic (over the sheetrock, bottom chord of the trusses, etc) for $1 per square foot, I just decide it was cheaper to get a good job by paying him and getting the extra insulation before blowing the R-49 in over the top. I am thinking this is the better way to seal the attic if $1 per square foot for the home doesn't blow your budget.
Charlie,
I agree with your priorities: air seal the ceiling and install deep insulation. After that, the ventilation is provided not so much to remove moisture (because your attic should be dry) but to reduce the chance of ice dams.
I thought a roof was ventilated to protect the shingles. Is this a misnomer?
Shane,
Researchers proved long ago that shingle color affects temperature far more than venting. So if shingle durability matters to you, and if you are convinced that lower temperatures increase durability -- the data are mixed on that point -- then you should choose white shingles.
John, Thomas, Tyson and Martin:
Thank you for your answers! The quick— virtually immediate— response is a very pleasant surprise. First, I used "hermetic" more in a figurative sense than literal; a perhaps unattainable goal to strive toward more than to arrive at. Still, judging from Tyson's undeniable results, maybe not all that unattainable after all.
Opps. The c.z. is 4a. The Southern Appalachian highlands vary A LOT. Sorry about the omission. And about the lack of clarity re venting "above" the valleys. I meant the stretches of roof running between a valley (as opposed to an eave/soffit) and the, small "attic" areas over the narrow, horizontal portions of ceiling up near the ridges. So here's the crux of the problem: If a gable-and-valley roof plan consists mainly of short wings forming a very stubby cross shape, say, then the combined length of eave/soffit relative to total ridge length is rather short, obviously. Now, if upwards of 3/4ths the space immediately under the rafters is conditioned (ceiling attached directly to the rafter undersides) and a large portion of those rafters are valleys or jack rafters, how can such a roof comply with the IRC's insistence that the between-rafter insulation be vented from eave to ridge in those areas where there simply aren't any eaves, just valleys??
Sure, one could make some sort of Herculean and/or Rube Goldbergian effort at valley ventilation but that would run completely contrary to my over-arching goal of achieving maximum aesthetic, and green, and livability bang for the $$ buck. Which generally means KISSing at every opportunity. Therefore, if the ceilings are real-world, and practically speaking air-and-moisture tight, is valley-to-ridge ventilation necessary at all? If so, can it be gotten in a reasonable, elegantly simple fashion? Disregarding —just for the moment that is— that bothersome business of the IRC.
About shear and racking stresses, Thomas: The steel roofing panels are 3' wide and well screwed to the purlins which are well nailed FLAT to the I-rafter tops. The valley I-rafters (about 15" deep) themselves also provide diagonal bracing. The pitches are 20:12 and supported at the intersecting ridges by unusually deep (48" and 32") ridge I-beams built in-place, gable-to-gable, using doubled up 1/2" OSB and paired 2X4 chords. The whole assembly is to be lavishly glued (gallons) and screwed together with plenty of cleats and seats (to receive the rafter ends and provide vertical stiffening every 16"). In addition, the valleys transfer their down-and-out thrusts from the ridges to the intersecting block walls they rest on, thus providing mid-span support. In short, (hah!) I'm relying primarily on gross roof geometry for strength and stiffness, secondarily on component dimensions, shapes and attachment/joint integrity. (i.e. the glue-and-screw thing). Lastly, the 2nd floor partitions, which go up ONLY after the ceiling and knee wall drywall is hung and finished, do their redundant part in supplying strength and stiffness to the whole roof/2nd floor combination. Suggestions, anyone, about how the partition top plates might be decently attached to the ceiling without popping fasteners through said air barrier?
Tyson, I'm making a note to myself to research flash coating. A dollah/ sq. ft., you say? Sounds to me like a good bang for the buck. Thanks.
If anyone feels i might be missing something PLEASE, BY ALL MEANS POINT IT OUT! Like John, I'm an amateur, not a professional (yet) but I do try to be as good a student as possible. Which, BTW, obviously goes for all of you otherwise you wouldn't even be here. I fervently hope that all of you are also amateurs (Latin: amo—to love) in the sense that you love what you're doing.
Thanks again to you all for your help, input and patience. Amazing grace, for sure.
Charlie
Charles,
If I follow this right, you've got a very steep pitch and a cruciform plan, like the image. It's not a vented attic except for a small area at the top (25% of the footprint). There's a cathedral ceiling around the perimeter and just the peak gets flattened out at the ceiling plane. The section is designed this way because otherwise there would be a ludicrously high attic space. Your question is about the joists that land in valleys, because they do not have eaves for letting ventilation air in. There is plenty of perimeter for eave vents, but they can't be aligned with each rafter bay.
Here's my opinion based on the above: for this to be a vented roof, you need to allow ventilation laterally between the rafter bays in order to address the valley issue. It's possible that open 2x4 purlins would do the trick to allow lateral airflow, given open space both between the rafters (between the insulation and the purlins) and above the rafters (between the purlins).
How were you planning to insulate? It's possible you could install baffle panels (e.g. 1/4" plywood) between I-joists, nailed to the underside of the upper flanges, and then dense-pack from below. Then your vent space would be as deep as the I-joist flange plus the purlin thickness (about 3").
Thomas—
Thanks for the image. Oh, how I wish I had the capability just now to post images !Working on it.
Yours is almost there: no hips, but gables instead. The 2nd floor is up in the roof, in other words. It's the gables as well as the valleys that limit the total eave/soffit run. With the insulation mainly between the rafters, Dr. Joe and others are saying that vent air "washing" the insulation from eave to ridge is the way to go, but are you saying that cross-rafter ventilation (via the 1 1/2" channels created by the purlins) is an alternative?
Summing up, the proposed ventilation pathway is: vent air enters the abbreviated soffits, makes its way up-slope over and under the purlins (aided perhaps by some stack effect due to the steep pitch), with some of it traveling along the purlins across to the jack rafters, then once again up-slope to the attic-as-vent-plenum and finally out. A circuitous path and somewhat throttled, to be sure. Your good idea of not letting the insulation push out beyond the underside of the I-rafters' top flanges would certainly alleviate the throttling affect. The loss of batt loft could be offset by the higher R per inch of an appropriate rigid foam board cut into panels snugly fitting between the rafter webs and up against the flanges.
Nevertheless, the original question still dangles out there; namely, is the reduction in overall ventilation, as a result of the roof geometry, a real concern (as opposed to a theoretical concern) considering the very small amounts of moisture that could/would make its way through the air barrier ceiling?
Thanks for your suggestion
Charles,
Here's a revised image. I agree the steep pitch should help move the air. Consider that rainscreen vent cavities are normally much less than 3". Your climate zone and the pitch should mean there's minimal risk of ice dams anyway.
You can use rigid foam as an insulation baffle, and this has been discussed in other threads here. I think your understanding of "batt loft" is off though. Fluffy batts perform poorly because of how air flows through them, and higher density batts perform better, inch for inch. Dense packed fiber performs much better than batts, and cellulose is the top recommendation based on cost, performance characteristics and resource use.
Charlie, I suggest you reread the posting rules. Gratuitous insults based on gender prejudice are neither nice nor polite. If you are coming here for free advice please be respectful of all readers of this open and inclusive forum whatever their occupation or gender.
Thomas— Bingo! ya got it. Now it's just a matter of checking out overall labor+material costs per R of the options you've laid out with respect to my specific steep roof application and covering material (steel). Like I'm wondering if it'd be possible to lay down the insulation and screw down the metal in one rolling operation.
For the IRC issue— with regard to my county, and most around here, it's mainly a matter of just spreading before the inspector well before hand what you want to do and most likely he'll say "Looks OK ta me". At most he'd like a stamp, which is no big deal either. 99%+ of building professionals in the region are blissfully unaware of the niceties of building science— which dovetails pleasantly with their generally laid-back ways. It's when ignorance combines with authoritarianism that nightmares ensue. Ever run into that?
Thanks again for your invaluable help.
Charlie
James—
Thanks for the check. I just corrected my stupidity.
Charlie
To all - There are lots of moving parts to this discussion, including some code history. The attic ventilation provisions in the IRC predate today's emphasis on energy conservation, and were intended to protect building components from various forms of water damage. The building science is clear enough now, that these requirements should be climate-specific, and further, that they should take into account energy conservation goals. It's time for some building science-based proposals to amend the code, probably by moving these provisions out of IRC Chapter 8 (Roof-Ceiling Construction) and into Chapter 11 (Energy Conservation). The direction the Energy Conservation Code is going is pretty clear: 1)tight air barriers, and 2)get the ducts and HVAC out of the attic. Changes to the attic vent rules should parallel these priorities.
Forrest Fielder, CBO
Phoenix, AZ