Will mold grow between foam panels in the wall?

Hi, I am planning a new house in Wisconsin with 2″ x 12″ wood framing. The wall will be: drywall, 6″ thick faced fiberglass batt, 3 foam panels 2″ thick each, plywood sheating, house wrap, tar paper, corrugated stucco wrap, stucco. I am wondering if there is a problem with condensation between the foam panels causing mold. I am planning on making the drywall and plywood be air barriers. Also, instead of 2″ x 12″ wall studs, I am planning on two 2″ x 4″ studs with a 4″ space between them for insulation.
The foam panels will be placed against each other but there may be a tiny space between them which will condensate when it is cold outside. The wall should be able to dry to the inside and the outside.
Thank you,
Dennis Vogt
GBA Detail Library
A collection of one thousand construction details organized by climate and house part
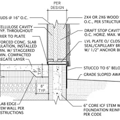
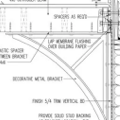
Replies
Dennis,
Whenever I hear that someone has bought a big pile of rigid foam, and plans to cut up all of the foam into narrow strips and insert the foam between their studs or rafters, I want to cry.
Please don't cut up your foam. If you want to install rigid foam, the right place to install it is on the exterior side of your wall sheathing. It should be installed in a continuous layer rather than cut up into strips.
Dennis,
Why are you using the two different types of insulation?
The reason for a combination of foam panels and fiberglass batts is to accomplish R51 versus R38 for 12" fiberglass.
The reason for placing the foam panels inside the wall cavity instead of outside the plywood sheathing is that both a framer and a mason told me that they wouldn't be comfortable with using 2" thick or greater of foam panels below stucco and thin-set stone. They both said that the foam wouldn't support the nails and the weight of the masonry would cause the masonry to droop over the years as the nails bent. The mason also told me that the foam isn't as rigid as plywood and so I will have a higher risk of cracking.
Thank you,
Dennis Vogt
When I say that the nails will bend, I am talking about the nails holding the metal lattice that the stucco and thin-set stone is cemented to.
Martin, many people spray foam the wall cavity. I won't, in part because it is too expensive but I don't see what is wrong with placing foam panels in the wall cavity. Yes the plywood sheathing will be frozen in the winter but not wet if I use the air-tight drywall approach, correct?. However, it is more likely to get wet from heat vapor in the summer, my way but I will have the air gap of the corrugated stucco wrap, correct?
What do you think?
Dennis Vogt
Dennis,
With the double stud 12" wall, you will have 5" between the edges of each pair of studs. Will you insulate inside of that 1 1/2" X 5" space between the studs?
Since you are going to the effort of building a relatively thick wall with double studs, I suggest using fiberglass for the whole thing. I think you could get it to R-50 by using high density batts and/or compressing low density batts. Take a look at page 2 of the Q&A question "Why Is There Such a Bias Against Fiberglass?"
It seems to me that it gets overly complicated to use two different types of insulation just to achieve an R-value that could be achieved with one type. And this is especially true, considering that you are going to revert to a wall system design that basically allows unlimited thickness.
In any case, I would not worry about moisture condensing between the foam board. If you stop the outward vapor movement at the interior wall, it will not be able to get into the wall, and thus will not condense in the wall.
I understand your point about supporting the stucco being difficult if you have a thick layer of foam between the stucco and the framing. I agree with Martin's point about placing the foam outside of the frame so it can run continuous rather than be interruped by each stud. The advantage is that it helps break the thermal bridge of the studs. But you already have broken the thermal bridge with the 5" space between the double studs.
Moreover, I see the main objectdive of applying an inch or two of foam board outside of the frame as a way to bolster the effect of the interior air barrier by keeping the whole cavity above the dew point. However, what you are proposing is the majority of your R-value produced by the foam in a 6" layer. Since you are building a 12" wall, it would not make sense to me to hang 6" of foam outside of the frame. And you will not need foam on the exterior to keep the cavity above the dew point if you stop the vapor before it gets into the cavity.
But, as I say, I would use fiberglass throughout the cavity and dispense with the foam sheet.
I would say dense pack with fiberglass or cellulose. Look up larson truss for exterior framing
Dennis,
I'm not a fan of either stucco or stone-veneer claddings over a wood-framed building. These cladding types have a high rate of failure because they allow very little drying to the exterior and they tend to hold moisture. If you want to use one of these risky claddings, be sure that you come up with a way to include an air gap between the cladding and the sheathing.
By far the safest sheathing to use with these risky claddings -- safer than plywood -- is rigid foam. For more information, see To Install Stucco Right, Include an Air Gap.
Thank you Martin and Ron for your much needed opinions.
I am planning on a ventilated air gap because of a system that uses a corrugated stucco wrap with a weep screed at the foundation.
Ron, thank you for addressing my original question. Yes I will insulate the 5" air gap between each stud of the 2" x 4" stud pairs. And I am also leaning toward using fiberglass batts only but I don't yet see a way of obtaining more than R-38 that way. I will review what happens to the R-value as you compress the batts to see if I can use thicker than 12" batts and compress them to 11 1/4" to increase the R-value above 40. This would also reduce air movement through the batts.
Martin, I apologize for making you cry and causing further annoyance for you as I realize that you are trying to get us to move the insulation outside the framing.
Thank you,
Dennis Vogt
With 2x 12 framing and 2 sets of 2x4 studs you'd have 4-1/4" between the studs (assuming you didn't stagger them) not 5". Staggering the ranks of studs gives a better thermal break. But trying to insulate that snugly with batts is a real PITA, and prone to voids & thermal bypasses.
With fiberglass batts or cellulose as cavity fill the thermal bridging of ranks of 2x4s with 2x12 plates treduces the whole-wall R to about R30. Even if you stacked it tight with polyiso or sprayed 2lb foam in there at full depth you'd be in R35+ provided you can make it tight enough. The weak point is the lack of thermal break at the 2x12 plates and subfloor. See the writeup and details for case 10 in this document:
http://www.buildingscience.com/documents/reports/rr-0903-building-america-special-research-project-high-r-walls
Alternatively...
A 2x6 16" o.c. studwall with 3" of exterior rigid poly iso comes in at ~R30 for far less money, and puts enough R value outside the structural sheathing that you won't need an interior vapor retarder. If you bumped that to 4" you'd be at R35, with a thinner wall than 2x12 double-stud framing. If you used your 2" stock on the sheathing and a layer foil-faced polyiso at the outer layer you'd also have a vapor barrier protecting the sheathing from the stucco cladding too.
Stucco contractors aren't that keen on exterior foam thicker than 1" though, and going thicker may cost you a premium if you stick with stucco siding.
Or, you could take the Larsen Truss approach which has a lot of flexibility. (See the discussion on case 11 in that document.)
Thank you for the information, Dana. I agree with your actual stud space dimension. The wall plates and the sill plate won't have insulation but a 11.25" wall plate board should have an R-value of 14. The R-value for the wall studs should be R-4.4 (2" x 4") + R-21.25 (4.25" foam) + R-4.4 (2" x 4") = R-30. As you said, I can't have a stucco/stone exterior and exterior foam insulation at the same time.
Dennis Vogt
Why use 2 X 12s for the wall plates, as opposed to 2 X 4 plates and plywood across the two plates for firestop at the top?
Good thinking, Ron.
That way, I can put insulation between the wall plates.
I'll discuss that with the framer.
Dennis Vogt
Dennis,
Are you planning on any connections between the outer and inner studs besides the connections at the top plate and floor?
Ron,
The framer wants to use solid 2 x 12 studs at the door frames and he would prefer to use them at the window frames. What are you thinking?
Dennis Vogt
Dennis,
I can understand the attraction of building a 12” nominal wall that would enable the use of 2 X 12s for top plates, and window and door rough openings. But there can be a lot of shrinkage across a 2 X 12, and they do contribute to thermal bridging.
I am working on designs for superinsulated houses that use ¾” plywood as a firestop capping across the two top plates of the double stud wall, as I mentioned earlier. I will also use ¾” plywood to pre-fabricate box-like tunnels for the windows and doors. These will be assembled with glued joints pulled together with nails or screws. I believe this is a rather common approach that I have seen detailed by others. I used it for one superinsulated house I built. Both that house and my new design have walls thicker than 12”. The target for the new design is 14” for the insulation layer in the walls.
The walls for my approach are framed with rough openings in the double stud walls to accommodate doors and windows. Then the plywood tunnels are installed into the rough openings. Finally, the doors and windows are installed into the tunnels. So the plywood tunnels are really a sort of high integrity, transitional element between the doors / windows, and the rough openings of the framing.
I am planning this design for a Minnesota climate, and will thus use a polyethylene vapor barrier on the warm side of the wall. The plywood tunnel structures lend themselves to extending that vapor barrier effect from the inner side of the wall to the outer side of the wall where the windows and doors are located.
Ron,
It looks like your going more wild than me. I'm going to ask my framer for ideas on how be can reduce the thermal bridging. Thank you for the ideas. I found a web page from Certainteed that publishes the R-value of compressed fiberglass batts. I'm a bit concerned that you are planning on using a poly sheet (class 1 vapor barrier) behind the drywall because that will cut off one direction for drying. Certainteed makes a poly sheet that they claim changes the permeability as the humidity changes, kind of like the paper facing on batts.
Dennis vogt
Dennis, Dana and Martin are tops in posting advice here. And best to even get with a production builder of double walls. So much will be learned (good and not good) if you do this one off and use tidbits of advice from the net and armchair one off DIY chat.
Know this, you will be conducting a one off DIY experiment with your home and a large chunk of your finances. Be willing to take that risk and to deal with improving all in the aftermath...
Dennis,
I have pondered the vapor barrier issues. I understand the point of allowing for drying to the inside, but I don’t want any drying to the inside. I plan to keep moisture out of the wall in the first place, so there is no need to dry to the inside. And besides, if any moisture does get into the wall, it can dry to the outside by passing through a vapor-permeable air barrier that I would place on the exterior.
I know that not everyone agrees with my rationale on this matter. But to explain further, it seems to me that a vapor-permeable air barrier on the inside that would let vaporizing wall moisture diffuse (dry) to the inside would also let vapor diffuse from the living space into the wall during the heating season when living space vapor pressure is higher than outdoor vapor pressure.
If you assume that diffusion does not play a role (as is widely assumed), then a warm-side, poly vapor diffusion barrier would not be needed, but an air barrier would be. And that way, any internal wall moisture would not be prevented from drying back to the living space by a poly vapor diffusion barrier.
However, if you believe that diffusion does not play a role, how can you rely on it for the drying function? If you have a warm-side air barrier you will be blocking the only mechanism for drying available, which is diffusion. So I don’t see how one can believe diffusion does not play a role in the wetting, but does play a role in the drying.
I believe that diffusion plays both roles since they are really the same role. Therefore, I would use a diffusion barrier on the warm side to prevent condensation within the wall. The fact that the diffusion barrier prevents drying back to the living space will not be a problem because there will be no moisture in the wall. This is because the diffusion barrier will not let vapor into the wall in the first place.
I know that there is also a possibility of moisture entering the wall as vapor from the outside. Certainly ambient outside vapor will enter the wall because there is only an air barrier at the exterior. If the vapor pressure of that outside air is high enough, and the interior air temperature is low enough, outside vapor will condense on the insulation-facing side of the interior vapor barrier. I know this occurs in warmer climates where summer humidity is high and air conditioning is heavily used to cool the living space.
However, in Minnesota or similar climates, I do not believe this so-called inward vapor drive will pose an issue of wetting the wall interior. It is on the edge of posing an issue, depending on how much air conditioning you prefer. We do often get 70 degree dewpoints during the summer. They can occasionally rise to 75-80 degrees. If the dewpoint does get that high, and the interior is at 70 degrees, for instance, then condensation on the outside of the vapor barrier is possible.
But this condition will be infrequent and short-lived. Moreover, my preference is to limit air conditioning overall. There is no time that I would want the interior cooled below 75-80 degrees. Therefore, I do not anticipate an issue of wall wetting due to inward vapor drive. Furthermore, if any sporadic wall wetting does occur, the ability to dry to the exterior will certainly be sufficient to mitigate the problem.
Some say that the ability for the wall to dry in both directions is necessary in case of direct water intrusion such as would result from defective flashing details. I would solve that problem by avoiding defective flashing details. I would also avoid siding that constitutes reservoir cladding, which can lead to inward vapor drive. I would use a wide roof overhang to further limit wall wetting from rain.
I know that one way to address the limiting of outward vapor flow in the winter while permitting inward drying in the summer is the so-called smart vapor retarder. But again, I don’t think that will be a problem that needs solving for the coldest U.S. climates. And I am not convinced that such a vapor barrier will do what is claimed or how long it will continue doing it. I am always leery of marketing promises at a molecular level.
So, overall, the second-to-the-last thing that I want to occur is having a house developing wet insulation cavities. And the LAST thing that I want to occur is having a house with wet insulation cavities drying to the living space.
Blog to peruse, also go to Lucas Durand's blog
https://www.greenbuildingadvisor.com/blogs/dept/green-building-blog/regional-variations-pretty-good-house
Hi Ron,
I agree that moisture diffusion will happen but I also think that the much greater condensation threat is from air movement. Also, if water does some how get into your wall, the plastic will be a drying barrier. However, you said that you don't want any drying to the interior any ways. I also am going to make it a top priority to stop air flow.
I also don't trust that Certainteed claim. Certainteed appears to be in big trouble with cement board siding that didn't cure correctly.
From your description, it appears to me that the weather in Minnesota is similar to Wisconsin.
I am planning on a 2 feet overhang.
Dennis Vogt
Dennis,
I agree that stopping vapor from being transported as a component of airflow is more important than stopping vapor from migrating by diffusion. But why not do both? A well-executed warm-side vapor barrier will also be a perfect air barrier. Some say vapor diffusion it is not a significant issue. But I don’t want to walk such a fine line after going to the effort and cost of building a superinsulated house. Furthermore, I see absolutely no downside to the fully impermeable vapor barrier on the warm side.
But this is for Minnesota-like climates. And yes, I would say that what applies to Minnesota applies to Wisconsin. I am not sure what I would build in warmer climates.
Thanks for the Info, AJ.
I'm going to be the builder. I haven't played builder before and most people think that I am crazy and wasting my money on this high-efficiency house. Part of my homework is seeing what you guys think of my wall idea.
Dennis Vogt
Thanks for the Info, AJ.
I'm going to be the builder. I haven't played builder before and most people think that I am crazy and wasting my money on this high-efficiency house. Part of my homework is seeing what you guys think of my wall idea.
Dennis Vogt
Ron,
I'm thinking that the kraft paper facing on the fiberglass batts will stop the vapor diffusion as well as the plastic sheet will but the paper also has the benefit of increasing vapor diffusion as the humidity increases. But as you say, you don't want drying to the interior. I can live with drying to the interior when it is needed.
Dennis Vogt
Dennis,
Regarding your comment, “I can live with drying to the interior when it is needed.”
I am not sure if it ever will be needed. Even with no drying to the interior possible, you will have free drying to the exterior. So if a super humid day in the summer happens to condense a little water in the wall, it will dry back out as soon as the humidity drops. Wintertime outward vapor drive will not be an issue if you prevent it with a vapor barrier, or maybe just an air barrier. So I don’t see any pressing need to provide for drying to the interior in addition to the exterior.
The problem with drying to the interior is that the moisture that needs to dry is moisture that will first accumulate in the insulation. Slow drying, wet insulation is ideal for growing mold. On one hand, drying that moisture out of the wall is a good thing because a dry wall will not grow mold.
But on the other hand, moisture may be charged into the wall faster than it can dry out, so it may dwell in the wall, and that might give it time to grow mold. Then, when it dries to the interior, it carries the mold with it into the living space. So I see it as leading right back into the toxic mold problem that everybody has spent the last 25 years trying to get away from.
Moisture gets in by any number of methods, the primary method being bulk water intrusion, followed by air-transport & condensation mechanisms, then a distant third 3-4 orders of magnitude down comes vapor diffusion.
But in a reasonably tight fiber-stuffed wall cavity the primary method by which it LEAVES is by vapor diffusion, and that's why you very much DO want to have at least some capacity to dry toward the interior- it adds resiliance to the assembly when you do.
The model where summertime moisture drives self-purge is just wrong for air conditioned buildings. Very often the extreme sun-driven moisture drives from masonry or stucco siding raises the dew point in wall cavities well above the temperature of the interior wall surfaces, and copious quantities of moisture can soak in, potentially rotting the subfloor and inner studwall plates if that moisture is completely blocked at the interior gypsum and creating a mold-habitat. Without the vapor barrier that moisture would pass harmlessly into the interior, a latent load to be handled by the air conditioning rather than building up inside the wall cavity.
Inside a fiber insulation layer water vapor quickly migrates to the colder regions, and in fact won't condense in the fiber until the moisture levels are pretty extreme, but instead condenses on the coldest surface first (the poly vapor barrier, or gypsum board if there is no vapor barrier.) In the process of condensing water is being removed from the air in the cavity, bringing the dew point below that of any portion of the fiber. But if that liquid water isn't allowed to re-evaporate on the conditioned space side it accumulates to visible levels, which is exactly what happens with interior side poly vapor retarders.
Water vapor can't carry mold with it- water vapor molecules (a pair of protons tucked into the outer shell of a oxygen atom) are smaller than the average size of AIR molecules (di-atomic nitrogen and di-atomic oxygen), and MANY orders of magnitude smaller than mold spores.
If the fiber is made of cellulosic materials (cotton batting, paper, etc) rather than spun glass or slag (fiberglass, rock wool) the fiber structure is hollow and it will wick liquid water away from structural materials under condensing conditions, and release it when vapor pressures reverse direction. The capacity for harmlessly buffering moisture this way is significant (but not infinite) and will protect the structural wood absorbing moisture during peak condensing conditions, which is another reason to use cellulose in a double-wall assembly rather than fiberglass or rock wool.
Poly sheeting has cause more mold problems in the lower 48 of the US than it has ever solved. Since it's possible to design & build climate-specific assemblies to be more resiliant to these issues without vapor barriers such that they dry in both directions without accumulating mold-inducing levels of moisture during any season, they SHOULD be designed & built that way (yes, even in MN/WI, and the MI-UP.) Rainscreen/backvented siding is one huge step in that direction, as is the use of somewhat vapor permeable exterior foam/rigid-fiber insulation to raise the average temperature of the sheathing. If you lived in Yukon or the interior of AK, there would be a better argument for interior poly, but even the universal Canadian national code prescription fpr interior poly is an error, IMHO, and creates as many problems as it fixes. (They have it dead-right on the 10mm rainscreen prescription though.)
If you're really stuck on the plastic membrane as air & vapor retarder concept, if it's on the interior side use Certainteed MemBrain, which is about 1 perm when the proximate air body is 25-35% relative humidity (across a temperature range), but rises to 10 perms or more when the proximate air is 70% RH or higher. So it'll open up (and rapidly) during bursty high-drive events, and will stay fairly vapor-open all summer, but hits class-II levels of vapor retardency during the drier winter months (unless you're actively adding moisture to the conditioned space air to above 30%RH average in winter.)
Dana, very well said. There is another batt product called Denim Ultra Touch, which is made of cotton and doesn't require any personal wear protection during the Install.
Dennis Vogt
Danna,
I understand all the points you made above in post #27, and agree with many of them. Generally, they seem to add up to a specific formula of construction details. However, there are many points comprising this rationale, and any of them can be altered in a way that affects the outcome. And if you alter several of them, it can have a large effect on the outcome. So I am not completely sold on the premise that threading this needle with this one complex series of cause and effect factors is the only way to reach a workable result.
You say that moisture gets in by any number of methods, the primary method being bulk water intrusion, followed by air-transport & condensation mechanisms, then a distant third 3-4 orders of magnitude down comes vapor diffusion. I have no reason to doubt that analysis, although I assume that it is based on average building performance. But I have ruled out building to average practices. I won’t have bulk water intrusion, for example. I also won’t have reservoir cladding, prolonged air conditioning to below 78 degrees. I will incorporate a large roof overhang that will keep much of the siding free from rain.
If I omit the vapor barrier, I get more drying potential, but I also get more wetting potential to the extent that outward diffusion occurs. By taking steps to avoid massive inward vapor drive, and building in a climate that produces little of that, I don’t think I will need much drying potential. So I would choose to forego the inward drying in exchange for a further reduction of wetting potential by using a vapor barrier that will absolutely block the outward vapor diffusion, though little it may be. And that vapor barrier, by default, will be a 100% effective air barrier.
I have heard several reasons why drying to the inside is necessary, and I think I can address those issues without drying to the inside. I don’t anticipate any water inside of the walls due to either direct penetration or vapor condensation. I don’t anticipate any mold inside of the walls. But, in the off chance that some mold does occur; I don’t want it entering the living space.
In my concern about mold entering the living space with inward drying, I did not mean to suggest that the mold would be transported by the vapor movement in the drying process. I was only considering that an air barrier permeable enough to permit the drying diffusion would be porous enough to permit the passage of mold. I do not know whether it would be or not, but my guess is that mold could move easily through some air barriers.
So, considering this same issue, I don’t want a smart vapor retarder that opens up and permits inward drying because I don’t want inward drying, and because I don’t believe I will need it.
I just don’t like the idea of building a super-tight, superinsulated house that relies of inward drying of wet wall insulation because of there being a forgone conclusion that such wetting will occur in such abundance that it needs all the drying potential possible. Why not push back against that extreme wetting potential and make it less likely rather than to take it as a given?
Generally, I see the value of redundancy in systems of insulation and vapor control. But I do not like the idea of systems intended to work together to accomplish one function under the assumption that no one system will be executed well enough to completely do the job by itself. That mindset often leads to situations where neither one of two cooperating systems does enough to satisfy the total requirement. So, for example, I don’t want to put foam board on the exterior to keep the wall temperature above the dewpoint because of the assumption that a 100% effective air barrier is impossible. Nor do I want to use cellulose for the purpose of soaking up water that condenses due to vapor getting past barriers that are assumed to be only partially capable of doing their job, or because flashings may be faulty.
These are some things I am skeptical about:
I am not convinced that a poly vapor barrier can only be justified once you get as far north as Alaska. Although I can see how the whole vapor model changes from outward-driven to inward-driven as you go further south.
I am also not convinced of the case against poly vapor barriers made by anecdotal evidence of failures. Just like the case against fiberglass, I am sure that the case against poly includes sloppy workmanship and installation damage. Moldy fiberglass resulting from bulk water intrusion caused by improper flashing is bound to be blamed on the fiberglass. And if there is poly involved, that will be blamed as well.
One other thing that I am skeptical of is the assumed benefit of the ability of cellulose to buffer moisture by soaking up water and preventing it from directly wetting the framing. Perhaps if there were enough water to leak out of the cavity and damage the drywall, sponging it up into the cellulose instead could be a benefit. But wouldn’t the cellulose action of sponging up the water slow down the drying out process? And if that is the case, is it really better to have a prolonged period of a large mass of damp cellulose than it is to have a little liquid lying on the floor plates and subfloor inside of the wall? It seems to me that the mass of damp cellulose would be an incubator for mold.
I also wonder why diffusion would be an important mechanism for vapor leaving a wall, but not a significant mechanism for vapor entering a wall.
Ron, this stuff is well understood and well measured & modeled by people who actually measure stuff rather than theorize about it in front of their PC. Download the WUFI tool and learn how use it without too much garbage-in-garbage out, and without a reliance on perfect-assemblies:
http://www.ornl.gov/sci/btc/apps/moisture/
Latex paint on gypsum is a pretty good vapor retarder- the wetting potential from diffusion drives are still pretty small, even in US climate zone 6, but air-transported moisture from the interior can be significant. Yes, it IS possible to build either with or without poly in your climate by how you do the stackup, but if you design it so that it doesn't need the poly it'll be far more resiliant to minor air leaks from the interior.
The reason vapor diffusion is more important for getting the moisture out is that a trickle air-leaks or vapor diffusion that deposits moisture over the winter months when it's too cold for fungus & mold to grow needs to be able to dry quickly when temps rise to where mold-growth can explode rather than slowly over 3-4 months. Bulk moisture that gets blown through the siding in a windy rainstorm isn't going to magically blow itself back out at the same rate, and accumulated moisture from air leaks won't dry into the same air leakage path quickly enough on its own unless you have a HUGE air leak, big enough to take a dramatic hit on thermal performance.
Cellulose does slow the drying process, but most of the moisture is distributed in the cellulose, not the wood. (WUFI models this pretty well.) It's the structural wood that you're trying to protect, and the cellulose can "take it", and isn't damaged or take a performance hit from the moisture cycling unless it's a HUGE moisture drive (like mis-lapped or absent window flashing), which would be a problem no matter what insulation was used. That puddle on the studwall plate soaks in and takes a VERY long time to get out since there's very little cross section for vapor diffusion. The same amount of moisture distributed in the insulation has both sides of the wall to dry toward, orders of magnitude more cross section than the saturated piece of subfloor & plate with the mushrooms growing out of it.
And yes, it IS a forgone conclusion that at least some of the building assemblies in any real world house will eventually experience moisture events, no matter how perfectly you think you can build something. The questions become how resiliant will it be in the face of these eventualities, and how to build in as much resiliance as possible. Poly is a two edged sword that works much better on paper than it does in the real world.
Dana,
I have no intention of developing theories in a vacuum simply as an end purpose.
I understand most of what you are saying, but I am curious as to what you mean when you refer to poly working better on paper than in the real world. What’s not to work?
I realize that poly prevents inward drying, but it also prevents outward diffusion. I don’t regard the prevention of inward drying as being a failure of poly to work. It would be working the way I want it to work. This is because I believe that stopping diffusion as much as possible is more important than providing as much drying as possible by allowing drying to the interior. You and others believe the opposite. So what is the scientific answer to this dispute?
All that I have been told here is that diffusion is not very significant. I asked Martin for the science supporting the contention that diffusion is not very significant, and he told me that there was no scientific support, but rather, only anecdotal evidence in taking apart buildings and finding little evidence of diffusion wetting in the walls.
I have also been told that maximum drying is needed because of construction defects, unfavorable architecture, and extreme weather events. I am told that these moisture producing conditions are forgone conclusions, and therefore, I must build to counteract them, even if it means accepting a little more outward diffusion. On first glance, this strikes me as an arbitrary conclusion because it based on several assumptions, generalizations, and value judgments.
Ron,
You wrote, "I asked Martin for the science supporting the contention that diffusion is not very significant, and he told me that there was no scientific support, but rather, only anecdotal evidence in taking apart buildings and finding little evidence of diffusion wetting in the walls."
You are not accurately reporting my statements. Diffusion is well understood by building science researchers, and programs like WUFI have been validated with laboratory measurements and monitoring of full-scale wall assemblies. Outward vapor diffusion in winter plays a much smaller role in moisture transport for wood-framed walls than air leakage; these values have been measured.
Martin,
Okay, fair enough. I do recall reading many times here that outward diffusion in winter plays a much smaller role in moisture transport than air leakage does. I have no doubt about that, however, that comparision still does not quantify the role of diffusion alone.
I expect that the actual measure of diffusion levels would need to be qualified with the many variables that would come into play. Is there a reference to a comprehensive listing of the rate of diffusion through a variety of materials, including painted drywall, and various vapor retarder films; under a variety of temperature and vapor pressure differentials?
Ron,
Most engineers use WUFI to determine the values you are seeking. WUFI allows you to tweak a wide variety of inputs.
Martin,
Actually, what I want to see is the scientific case that determines that providing inward drying results in lower overall average internal wall moisture than stopping outward diffusion. So, the amount of vapor moving by diffusion would also need to be factored against the amount of drying potential through the same route by diffusion in the opposite diffusion. It would have to account for the time periods of outward diffusion versus that of the drying diffusion. It would have to also account for the amount of drying needed to mitigate moisture condensation from all diffusion, inward vapor drive, air leaks, etc.
Ultimately, it has to answer this question: In terms of moisture affecting structure, growing mold, or affecting thermal performance, is it better to allow inward and outward diffusion by omitting a vapor barrier; or to include a vapor barrier, thus stopping diffusion in both directions?
It seems like it would require an incredibly complex calculation to provide a definitive answer to that question.
Ron,
Again, you are asking precisely the type of question that WUFI was designed to answer.
You're correct that the calculations are complicated, and the number of variables is very large.