Window installations

Its good practice to create a sill pan flashing prior to installation of a window?
After contacting most all major peal stick membrane suppliers I find none of their products are to be used with “standing water” or are warrantied at all with this application! They tell me water must shed. Its difficult to impossible to shed water off a flat sill surface.
Shimming the sill to slope places the window out of plumb and jeopardizes the warranty.
Am I looking to use sheet metal of some kind or?
Cheers
GBA Detail Library
A collection of one thousand construction details organized by climate and house part
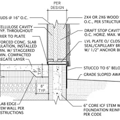
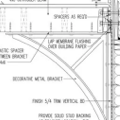
Replies
Homeflash,
It's not only good practice, here it is required by code.
Sill pans need to be installed on a sloped sill so any moisture can drain to the exterior. To provide a flat base for the windows use sloped shims.
Who makes sloped sill pans or are they fabricated on-site? If so, how much slope is needed?
Thx!
BrunoF,
You make them yourself out of peel & stick membranes. The slope is typically 6 degrees. Rather than slope the whole sill, I prefer to run the 2"x6" through my table saw so only the portion under the window frame gets sloped.
This shows one installation method with a sloped sill: https://www.youtube.com/watch?v=JhXx__AMzTo
So you are basically limiting the depth of the sloped portion by your table saw’s max blade height?
I use fiberglass, aluminum or vinyl flanged windows. The portion of the window frame inside the flange that sits on the sill is typically max 2". So well within the depth of cut on table saw.
I don't like sloping the whole sill because it makes casing the interior harder. And because the reason for the sloped sill is to shed any moisture that comes from the window itself leaking at some point. That can only occur in that same 2" depth, so there isn't anything to gain in detailing the opening inside the inner-face of the window frame to shed water.
Do you account for the slope in your rough opening sizing or is the interior side of the rough opening as per the window requirements?
If you only slope the outer part of the sill, you can frame the opening to the manufacturer's suggested RO.
Malcom, thx! This method may be the way to go!
BrunoF,
While you have your table saw out and are sloping the sills, move your fence out the width of your blade and cut a pice of scrap at the same 6 degrees you can use as shims.
How do you prep door rough openings?
What do you use to make the back dam once your windows are installed?
BrunoF,
The interior face of the window frame gets caulked for air-sealing. If the sill is sloped there is no need for a separate back-dam.
A piece of framing lumber ripped on a table saw.
Thx!
Another method is to use a piece of beveled cedar siding tacked to the rough sill and then the flashing membrane would go over the cedar. This is particularly useful if you're installing a new window in an old rough opening.
Hi Homeflash.
I think most high-performance builders install both a back dam and a sloped sill. You can see how to do that in this article: Installing Flangless Windows.
Keep in mind that this flangeless window is different than a flanged window install, though. Though the sill is prepped the same, once the window is set, in most flanged window installs, the bottom flange is not taped to the sheathing. That way, water than runs down the sloped sill has a way out.
All of our windows come with a subsill to allow the water to drain away, the last thing you want is water in the building structure
Ya, lots of manufactures say a lot of things. If you're concerned about the longevity and waterproof capability, perhaps look into a liquid based flashing.
Your window gets plumed by the installers with a level. It's not reliant on the thing that it's sitting on. Sloped sill or not, you're still adding shims at the bottom anyway to level the window (and leave a gap for drainage). So you might as well slope the sill and not have to worry about standing water issues. If you're still worried about the plumbness then use wedge shims like Malcolm suggested, the same degree your sloped your will you can counteract that degree with the opposing shim on top of the sill.
Jamie
I've seen some cool tricks with liquid flashing, like attaching narrow opposing shims to the sloped sill before flashing, which ends up looking like a wide-spaced dentil molding.
Also having an integral backdam, which is easy enough if the sill slope is ripped on a table saw. Can also make a backdam with a rip of 1X nailed to the sill, which works nicely if you're nailing a piece of cedar lap to the sill. Not really sure how many builders are actually making sills with backdams, but it doesn't sound particularly common.
You can rip the sill edges at an angle (parallel to each other) and cut an angle on the jacks, to frame the entire sill at an angle. I think that's a really elegant solution, but arguably the most effort.
Liquid flashing or ZIP stretch tape make really easy sill pans, if they are compatible with your WRB.
Chris,
"You can rip the sill edges at an angle (parallel to each other) and cut an angle on the jacks, to frame the entire sill at an angle."
I don't see what you gain by having the sill inside the window sloped. You have to start with a 2"x8", have to shim for the stool, and it's a lot harder to figure out the right RO height.
I understand, I'm just stating it as a method people use.
I've only seen people do it with the same nominal framing as they're already using, so just clearancing one/both edges of the same 2x6 so there isn't an out-of-plane bumpout at the sheathing or drywall. It's not a big cut to compensate for 6 degrees. You aren't removing any sill height thickness, unlike ripping the sill at a slope.
Just different methods, with different amounts of effort.
Thx! I will be using Benjamin Obdyke hydrogap and zip tape…thx for reminding me to check on their compatibility.