Wine room insulation

I am currently in the process of converting an existing “mud” room at the back of my Philadelphia brick row home into a conditioned wine room and have a few questions regarding insulation and vapor barrier installation.
Description of the existing space:
Room is built as an addition onto the back of my brick row home. The room is about 14ft wide x 9ft deep x 9ft tall. The existing wall stack up is: brick/R13 batt within 2×4 wall cavity/sheetrock. I will be removing the R13 batt insulation. The room sits above an unconditioned enclosed crawl space. I will be using half of this space for the wine room, so will be building a new interior wall also.
From my research, most sources say that the wine room must be enclosed with vapor barrier on all sides, floor, and ceiling to maintain humidity levels. The vapor barrier is supposed to be installed on the hot side of the wall. For insulation, I was planning to remove the existing R13 batts and use 3 inches of salvaged polyiso insulation in walls, 4 inches in the floor, and R30 batt in the ceiling. My concern here is with the floor. The stack up of the floor would be (from bottom to top): 3/4″ subfloor/6mil vapor barrier/4″ polyiso rigid insulation between sleepers/subfloor/tile. Since the floor is over an unconditioned crawlspace, I am worried about trapping moisture in the subfloor by putting vapor barrier/polyiso over it. Is this an issue, or will the insulation be sufficient to keep the subfloor from getting cold and building condensation that becomes trapped by the vapor barrier? Would going to 5 inches of ployiso in the floor help? The underside of the floor is not easily accessible, and would be difficult to try to install vapor barrier down there.
Also, another question regarding the polyiso: is it ok to stack it? as an example, if I were to purchase 2″ think panels and stack them for 4″ of total thickness, is that ok? Would I need to peel off the foil facing on the inner sheet if I did this?
GBA Detail Library
A collection of one thousand construction details organized by climate and house part
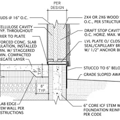
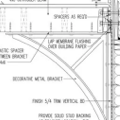
Replies
Stacking polyiso is fine. It's done all the time on commercial roofs.
What is the target temperature & humidity?
If there is no ground vapor barrier in the crawlspace even insulation over the floor (let alone a vapor barrier) puts the flooring & floor joists at risk unless actively controlling the humidity in the crawlspace.
The target temperature inside the wine room will be 55F. The space will be actively cooled during the summer by a wine room cooler that doesn't dry out the air. During winter, the space will not be conditioned. The house has zoned hydronic heating and the mud room is its own zone with its own thermostat. In winter it is kept at 57F.
If I had to, I could lift up the 3/4 subfloor and put down vapor barrier in the crawl space. The crawl space is full of gravel and there is about a foot of space between the gravel and the joists so I'd have to work from above. If lifting up the subfloor, I'd probably want to put insulation between the joists before putting the plywood back down. Could I use polyiso here, or would fiberglass batt be better? I'd still be putting sleepers and 4" of polyiso down on top of the subfloor.
Your subsoil temps in Philadelphia are pretty close to your target wine room temperatures:
https://www.builditsolar.com/Projects/Cooling/US-ground-temps.gif
Given that fact, you will be better off earth-coupling the whole thing to the deep subsoil temperatures by air sealing and insulating the foundation walls with EPS or closed cell spray polyurethane when you pop the subfloor to install the vapor barrier (which you really do need to install to mitigate the risk of rotted joists & subfloor.) The high thermal mass of the subsoil helps stablize the wine room temperatures, reducing the amount of active heating or cooling it would need.
Hmmm... So you're saying don't insulate the floor of the wine room, but instead insulate the crawl space, right? This would involve getting vapor barrier on the gravel and up the crawl space walls, and then putting insulation on the walls over the vapor barrier, correct?
I have some follow up question as I finalize my plan after now completing the gut of the existing space.
1. The ceiling turned out to have a lower 2x4 frame, supported by 2x4 framing around the perimeter. I am thinking about removing all of the 2x4 framing (its only a 6x8 space) and doing the following:
Ceiling - attach 8" worth of polyiso board, attached directly to underside of 2x12 rafters (flat roof). Is it an issue to put 6 mil vapor barrier between the polyiso and the underside of the rafters?
Walls(brick) - attach 2" polyiso to interior of brick walls, than build 2x3 frame over the 2" polyiso, and fill the cavities with another 2" of polyiso, with sheetrock to finish. Is it a problem to put 6mil vapor barrier between the polyiso and the brick?
Interior wall - frame 2x6 wall with 4" of polyiso in the cavities and sheetrock on both sides.
Floor - as discussed above, plan is to put vapor barrier in crawlspace below the space and insulate crawl space walls to leverage thermal mass of ground to support cooling the wine room.
You'll get more performance out of the walls with 4" of polyiso strapped to the brick with 1x4 furring & 6" masonry screws.
What is the purpose of the 6 mil polyethylene vapor barriers on the walls & ceiling?
The short answer to #4 is right, insulate the exterior walls of the foundation down to the floor of the crawlspace, but leave the floor of the crawlspace uninsulated, since it's natural temperature is very close to your target temperature. If flooding is even a remote possiblity, use EPS rather than polyiso on the crawlspace walls.
The idea of putting the 6mil poly on the hot side of the insulation (that is, the side facing out of the room since the room is cold) is to help maintain a more stable humidity level in the room. Perhaps the poly is not worth the effort since I'd expect the polyiso board to help in that regard some. It will be tedious, but I plan to seal all seams with foam and tape to get as close to air tight as possible.