Rigid Foam Between Top of Internal Footings and Slab

We are building g a custom home in the Salt Lake City area. Our footings & foundations are poured. We are currently grading out the area under the slab with gravel.
We (the owners) would like to put a complete XPS envelope under the slab (thermally decoupling beneath the slab & up the sides up the external footings). Our question is about the internal footings… the ones in the middle of the basement that support load bearing walls.
The city engineer, inspector, and structural engineer are all “uncomfortable” with putting XPS rigid foam between the top of the internal footings and the slab. They cannot explain why or point to a specific code this violates. But I also can’t find an article/video/explanation that’s explicitly says it’s ok.
If this is a terrible idea, can someone explain why. If it is not a terrible idea, how do I convince the skeptics in charge?
(Areas of concern circled in green in attached image.)
Cheers,
Travis
GBA Detail Library
A collection of one thousand construction details organized by climate and house part
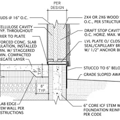
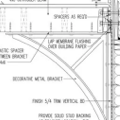
Replies
While I'm unable to say if it's a terrible idea, the city engineer and structural engineer should have no problem with making that determination, but they'd prefer the liability rest elsewhere."Uncomfortable" is a response the engineers should be be able to better clarify and offer hard data on, but that wohld require them to do the engineering work on plans that aren't their responsibility to work on. They just want to see the stamp, review them, and that's it.
It sounds like the placement of the foam on the footings wasn't detailed in your building plans. Maybe consider bringing the plans to a private structural engineer to have your idea reviewed and approved. The city employees don't want to put the effort into your plans, and if you present them with the changes accompanying a stamp their discomfort should go away.
Travis, that's my standard detail and the only reason they're uncomfortable with it is because they haven't seen it before. There is nothing in the IRC code that prohibits it.
I would encourage you to use EPS and not XPS, as the latter has blowing agents that are far worse for the environment. Even the new, so-called environmentally friendly XPS is far worse than EPS and has no performance advantages over EPS.
Michael,
What about point loading from the framed walls above? Do you spec. higher psi foam to compensate?
That's what the engineers I work with do at high load areas.
A recent project had Type VIII EPS as the typical sub slab EPS, but had to use Type XIV EPS in one location at the end of a shear wall where there was a particularly high point load.
For various reasons, this project ended up with some footings that have the foam between the slab and the footing, and some footings where the foam goes under the footing. The engineer was comfortable with engineering both situations, although it took a bit of back and forth to get it all sorted out to everyone's satisfaction. For what it's worth, the foam under the footing caused less grumbling that the foam between slab and footing, but both were achievable in the end.
Initially the engineer was more comfortable using geofoam specs (EPS-19 and EPS-39), because those specs list the PSI at 1% deformation, while conventional EPS only lists the psi at 10% deformation in the cut sheets.
We were able to work with the product rep from the manufacturer to find the equivalent conventional eps specs since the client (acting as GC) wanted to use a product that was only available as conventional. We concluded that for the purposes of this project Type VIII EPS could be substituted for EPS-19 Geofoam and Type XIV EPS could be substituted for EPS-39 Geofoam.
tg_johnson: you might try asking the engineer to determine what strength (in terms of "psi at 10% deformation") would be required to put the insulation where you want to put it. Then you are changing the question from "are you comfortable with this thing you've never seen before" to "please engineer this for me", which they might be more willing to do, being engineers and all :)
I would also love to know what you do here Michael. Do you upgrade to something that's like 600psi underneath the load bearing walls? Or will regular 250psi stuff do ok? Mine will only be bearing the first floor above.
It depends on the load. I've found that 25 psi foam is usually enough, sometimes 40 psi is needed, and I think I recall one time an engineer required 60 psi but don't quote me on that. Foam is rated for the load that results in 10% deformation, and for long-term loads that rating should be reduced to 1/3. Once you know the actual load and the acceptable deformation, you can determine the required foam PSI rating. Foam deformation under load is roughly linear so half the load results in about half the deformation.
These are not prescriptive values or calculations, so you may need to involve a licensed engineer, as I do regularly when required (and sometimes for my own peace of mind). Engineers vary in their experience and approach; the more conservative ones still aren't comfortable with "structural foam" but if you ask around you should be able to find a more progressive engineer.
Yes. I am haveing a hard time selling this detail to my contractors too. Their final reason for not doing sub slab insullation foam is, "Well, your gonna loose 2" of head space!" 8' 6" with less potential for mold vs 8' 8" with more potential for mold... not a hard decision. Also I like the idea of have the whole slab incapsulated by foam on the bottom and sides.
Tell them to dig down two inches deeper. Problem solved. Not a big deal to do, either, unless everything has already been poured. If things have already been poured, put a double sill plate on top of the foundation wall and your "2" less head space" is now "1/2" less head space", and you'll never notice the difference. That's another easy solution to show your contractors.
In the end, it's your project, make them build it the way you want. There are plenty of detail drawings available that show subslab rigid foam, so it's not a particularly new idea that might bring surprises down the road.
Bill
If they dig 2" deeper, then the foam wouldn't rest on the footer. Isn't that an important detail?
Yes, it would have. So we should have asked for 2” higher poured concrete walls. If we cared about the 2” head space. Which we don’t (cause 9’ basement walls). The only weird thing is we had to double up our bottom treated 2x6 plate on the walkout. And the second 2x6 is just a little under 1” above the finished concrete floor. Which is a little odd.