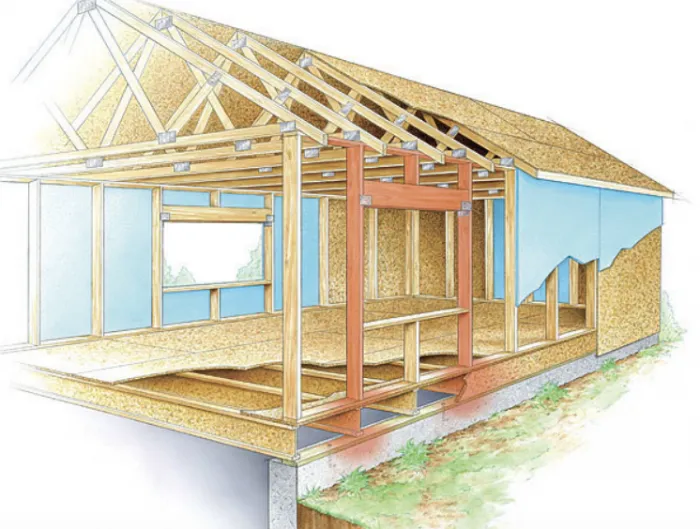
In his 2005 Fine Homebuilding article “The Future of Framing is Here,” Building Science Corporation principal, Joe Lstiburek, as a representative of the U.S. Department of Energy’s Building America program, shared an ambitious goal. “Our target is an affordable ‘net-zero’ house (one that produces as much energy as it consumes) built by production builders at no extra cost,” he wrote. The key to reaching that goal was in the building envelope, Lstiburek continued, and the “future” had been a long time coming.
Lstiburek’s article describes advanced framing, or optimum value engineering (OVE), a concept that was being developed and promoted as early as the 1970s by the National Association of Home Builder’s Research Center, (today, the Home Innovations Research Lab). Advanced framing techniques reduce the amount of lumber in building assemblies to achieve three goals: less resource consumption, lower costs, and more room for insulation.
The article was my introduction to advanced framing and I can remember thinking, “What’s not to like?” With Lstiburek’s article in the rear view, and as Fine Homebuilding and GBA went on to feature articles on alternative framing techniques—some of which seemed to use more lumber and cost more money—as well as houses that simply overlooked advanced framing altogether, that question kept coming to back to me. So, I recently asked it of some regular contributors who responded collectively: “Not much!” I was happy to learn that many of them, mostly custom builders, are using advanced framing techniques to the degree that it makes sense in a given project. I’ll share what I learned in those interviews, but first, let’s review how advanced framing works.
Advanced framing means less lumber
At the heart of advanced framing, and the detail that seems to be most commonly used…
Weekly Newsletter
Get building science and energy efficiency advice, plus special offers, in your inbox.
This article is only available to GBA Prime Members
Sign up for a free trial and get instant access to this article as well as GBA’s complete library of premium articles and construction details.
Start Free TrialAlready a member? Log in
7 Comments
Thanks for this Brian. It's an excellent overview, and it is really useful to hear the differing and nuanced ways in which various builders have approached the subject.
I'm somewhere in the middle too. I don't think it ever makes sense to alter the architecture for more efficient framing. I can't imagine having a conversation where I explained the odd location of a window, or size of a room, by saying it saved a few studs.
Another aspect of this was brought home to me recently. One of the benefits of conventional platform framing is its redundancy. If you engineer the structure to maximize its efficiency, this can disappear. Last week I found out that two log posts on a duplex I built 30 years ago had become rotten, and that rather than replace them, the owner simply took them out. Those posts hold up one end of a beam, which in turn has three roof trusses bearing on it. The structure was able to redistribute the load paths through the framing and sheathing - so far without apparent ill effect.
That's a useful attribute to have, not only in situations when someone does something stupid like that, but also when parts of a building experience decay over time. We have all seen old wood frame buildings that stay together when all the parts you would expect to hold them up have rotted away. There is something to be said for a bit of redundancy in any structure.
Thanks Malcolm.
While I think a lot of this makes sense, I'm curious about the design aspect and wonder how many projects start with the idea of building on 2 ft. modules and located windows and doors on layout, but abandon that aspect of OVE because of design complications. It would be good to find some successful projects that were designed and built that way and see how they handled the compromises.
I read your article today, Brian, and I like it very much. Excellent work. Reading Malcolm's comment, I will disagree--if your aim is more affordable construction, you must modify the architecture. A slightly off-center window, designed to line up with the framing module, looks terrible. But a completely off-center window, near one or the other corner, looks fine. It's the principle of thirds. The window near a corner also washes two walls with daylight and reflects more light into the room. It will afford long diagonal views, too. As in the example with Josh, I have done the same in a kitchen--reducing the number of cabinets while creating a more appealing kitchen. At least one that people liked more at first sight. Architectural constraints -- like poetic ones -- always lead to better solutions, and OVE framing provides an efficient constraint worth submitting to creative architectural solutions. Use wood, not too much, adding mostly insualtion.
Fernando,
"if your aim is more affordable construction, you must modify the architecture"
As a general proposition that may be true, but I'm not sure the numbers support moving windows to use less studs.
Given that the construction costs of a new house here are about 600K, and the savings of moving the openings is maybe $150, the difference is in the weeds.
What may well affect the longevity of the house is whether it is seen as desirable, and functioning well - which will in turn motivate the occupants to maintain it.
I agree entirely that constraints cans spur creativity. Every good designer imposes them on themselves, as do difficult sites, climate, and of course the quest for efficiencies. But I think it's important not to add constraints where the outcome may outweigh the benefits.
Of course, your points are well taken, Malcolm. Loveable buildings last longer because people preserve them. They are also easier to sell. And $150 may not be a significant saving if that's all you save on a $600,000 house. However, only some line items provide enough savings to justify themselves when considered individually. There are so many line items in a house -- close to 10,000 -- that you can build considerable savings when considering small savings on every single one. It's easy enough to save 10% on building a house--any house. I act as a cost-cutting consultant and this I can almost guarantee. The good news for you is that this would amount to $60,000, and that's good money in anybody's pocket. I read in the article above that Josh considers a $1,500 savings trivial. I don't. Building affordable housing requires a cost-cutting mindset in every decision made. After the cost-cutting is done, then you can add back in the architectural values. In other words, instead of thinking that $150 is too little to cut, cut everything you can (while building a good quality house) and then add back in the small increments -- such as, "Well, $150 is not a big splurge to get the window in the perfect location." I am sure you get my drift. To achieve a $60,000 savings on your construction, you will not find huge line items you can do without. But you can find 1,000 $60 cost cuts by thinking like a miserly grocer or coupon-clipping housewife A dime out of a dollar, a dollar out of ten. This thinking has value if you aim for affordability or to carve out higher profits. Otherwise, it's just a lot of mind-numbing minutia that makes no sense. Most builders won't mess with it. I don't blame them. This is what I do.
Fernando,
I agree entirely with your approach. It's too easy to do the opposite and say another $150 for X is small potatoes - and not do as you suggest and realize up what all those $150s add up to.
I'm definitely in favour of looking at framing with a functional eye to eliminate what is redundant. Moving windows is one of the few things I don't think merits doing.
One other practice of some AF I wonder about is carrying the 2 ft load path up through all the framing. Is there any real savings in materials or costs if that necessitates deeper floor members or a thicker sub-floor?
The load stack would not require a thicker subfloor, although wider joist spacing may. I have yet to find the single top plate a money saver due to the increased difficulty in lining up walls, joining them to the interior partitions, and having to rip drywall if you use studs.
Log in or become a member to post a comment.
Sign up Log in